The electronics industry is undergoing a transformative shift with the advent of additive manufacturing (AM), also known as 3D printing. This technology is revolutionizing the way complex multilayer circuits are designed and manufactured, enabling unprecedented levels of customization, rapid prototyping, and innovation. Unlike traditional subtractive methods, which involve etching away material to create circuits, additive manufacturing builds circuits layer by layer, offering greater design freedom and efficiency. This article explores the principles, benefits, challenges, and applications of additive manufacturing for complex multilayer circuits, providing a comprehensive guide for designers and manufacturers looking to embrace this cutting-edge technology.
1. What is Additive Manufacturing of Multilayer Circuits?
1.1 Definition
Additive manufacturing of multilayer circuits refers to the process of creating electronic circuits by depositing conductive, insulating, and other functional materials layer by layer using 3D printing technologies. This approach allows for the fabrication of complex, three-dimensional circuit structures that are difficult or impossible to achieve with traditional methods.
1.2 How It Works
The additive manufacturing process for multilayer circuits typically involves the following steps:
- Design: Create a 3D model of the circuit using computer-aided design (CAD) software.
- Material Deposition: Use a 3D printer to deposit conductive inks (e.g., silver, copper) and insulating materials (e.g., polymers) layer by layer.
- Curing: Solidify the deposited materials using heat, UV light, or other curing methods.
- Post-Processing: Perform additional steps such as sintering, polishing, or coating to enhance the circuit’s performance and durability.
1.3 Key Technologies
Several additive manufacturing technologies are used for creating multilayer circuits, including:
- Inkjet Printing: Deposits conductive and insulating inks with high precision.
- Aerosol Jet Printing: Uses a focused aerosol stream to deposit materials, enabling fine features and complex geometries.
- Fused Deposition Modeling (FDM): Extrudes thermoplastic materials to create insulating layers, with conductive traces added separately.
- Direct Ink Writing (DIW): Extrudes viscous inks to create 3D structures with high aspect ratios.
2. Benefits of Additive Manufacturing for Multilayer Circuits
2.1 Design Freedom
Additive manufacturing enables the creation of complex, three-dimensional circuit geometries that are not possible with traditional methods. This includes curved surfaces, embedded components, and intricate interconnects.
2.2 Rapid Prototyping
3D printing allows for quick iteration and testing of circuit designs, reducing development time and costs. Designers can easily modify and print new prototypes without the need for expensive tooling.
2.3 Customization
Additive manufacturing supports highly customized designs, making it ideal for niche applications and small-batch production. Each circuit can be tailored to specific requirements without significant additional cost.
2.4 Material Efficiency
Unlike subtractive methods, which waste material during etching, additive manufacturing uses only the material needed to build the circuit. This reduces material costs and environmental impact.
2.5 Integration of Functions
Additive manufacturing enables the integration of multiple functions, such as sensors, antennas, and energy storage devices, into a single printed structure. This simplifies assembly and reduces the overall size and weight of the device.
3. Challenges of Additive Manufacturing for Multilayer Circuits
3.1 Material Limitations
The range of conductive and insulating materials available for additive manufacturing is still limited compared to traditional methods. Developing materials with the required electrical, thermal, and mechanical properties remains a challenge.
3.2 Resolution and Precision
While additive manufacturing technologies have improved significantly, they still struggle to match the resolution and precision of traditional photolithography. This can limit the miniaturization of circuits.
3.3 Conductivity
The conductivity of printed conductive traces is often lower than that of bulk metals due to the presence of voids and impurities. Post-processing steps such as sintering can improve conductivity but add complexity to the process.
3.4 Scalability
Additive manufacturing is currently more suited for prototyping and small-batch production. Scaling up to high-volume manufacturing remains a challenge due to speed and cost limitations.
3.5 Reliability and Durability
Printed circuits may have lower reliability and durability compared to traditionally manufactured circuits, particularly in harsh environments. Ensuring long-term performance requires careful material selection and post-processing.
4. Applications of Additive Manufacturing for Multilayer Circuits
4.1 Wearable Electronics
Additive manufacturing is ideal for creating flexible, lightweight circuits that can be integrated into clothing, medical devices, and fitness trackers. The ability to print on flexible substrates and create conformal designs makes it well-suited for wearable applications.
4.2 Internet of Things (IoT)
The customization and rapid prototyping capabilities of additive manufacturing are valuable for developing IoT devices, which often require unique form factors and integrated functionalities.
4.3 Aerospace and Defense
Additive manufacturing enables the creation of lightweight, high-performance circuits for aerospace and defense applications. The ability to print complex geometries and integrate multiple functions is particularly advantageous in these industries.
4.4 Medical Devices
3D-printed circuits are used in medical devices such as implantable sensors, diagnostic tools, and prosthetics. The customization and biocompatibility of printed materials make additive manufacturing a promising technology for healthcare.
4.5 Automotive
Additive manufacturing is being explored for creating customized circuits for automotive applications, including sensors, control systems, and infotainment systems. The ability to print on curved surfaces and integrate functions is particularly useful in this sector.
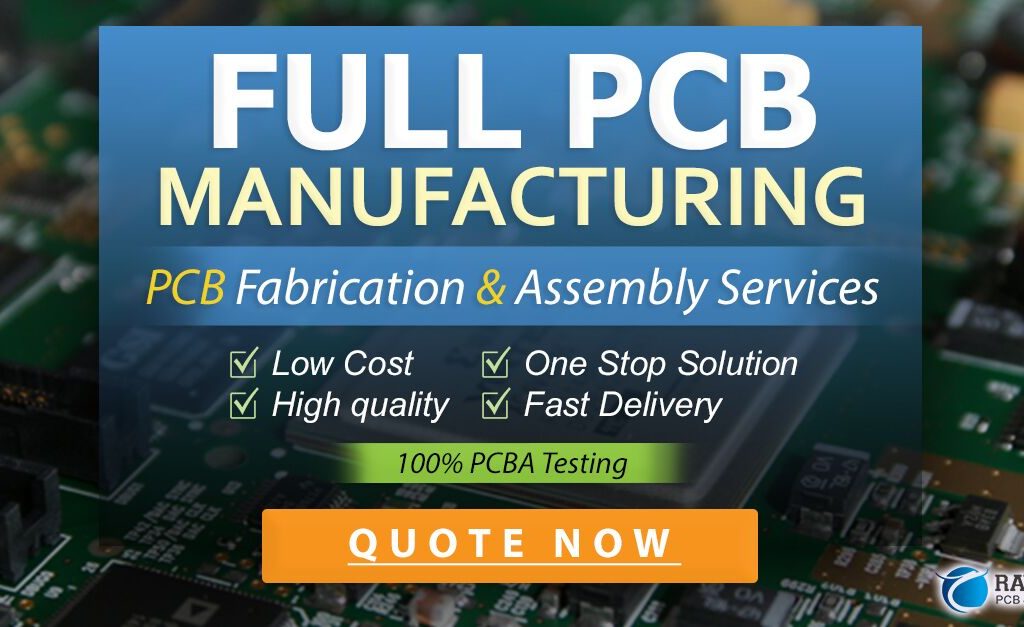
5. Design Considerations for Additive Manufacturing of Multilayer Circuits
5.1 Material Selection
Choose materials with the required electrical, thermal, and mechanical properties for your application. Consider the compatibility of conductive and insulating materials to ensure proper adhesion and performance.
5.2 Layer Thickness and Resolution
Optimize layer thickness and resolution based on the capabilities of your 3D printing technology. Thinner layers and higher resolution enable finer features but may increase printing time and complexity.
5.3 Interlayer Connectivity
Ensure proper connectivity between layers in multilayer circuits. This may require careful design of vias and interconnects, as well as post-processing steps such as sintering or plating.
5.4 Thermal Management
Consider thermal management in your design, particularly for high-power circuits. Additive manufacturing allows for the integration of thermal vias and heat sinks, but material limitations may require innovative solutions.
5.5 Mechanical Stability
Ensure that the printed circuit has sufficient mechanical stability for its intended application. This may involve reinforcing the structure with additional materials or optimizing the design for strength and durability.
6. Best Practices for Additive Manufacturing of Multilayer Circuits
6.1 Collaborate with Material Suppliers
Work closely with material suppliers to identify the best materials for your application. They can provide valuable insights into material properties, compatibility, and processing requirements.
6.2 Optimize Printing Parameters
Experiment with printing parameters such as nozzle size, deposition speed, and curing conditions to achieve the desired resolution, conductivity, and adhesion.
6.3 Perform Design for Manufacturability (DFM) Checks
Use DFM tools to ensure that your design is compatible with additive manufacturing processes. This includes checking for issues such as overhangs, unsupported structures, and material compatibility.
6.4 Test and Validate Prototypes
Thoroughly test and validate prototypes to ensure that they meet performance requirements. This may involve electrical testing, thermal analysis, and mechanical testing.
6.5 Iterate and Improve
Use the rapid prototyping capabilities of additive manufacturing to iterate and improve your design. Incorporate feedback from testing and validation to refine the design and optimize performance.
7. Future Trends in Additive Manufacturing of Multilayer Circuits
7.1 Advanced Materials
The development of new conductive and insulating materials with improved properties will expand the capabilities of additive manufacturing for multilayer circuits. This includes materials with higher conductivity, better thermal stability, and enhanced flexibility.
7.2 Hybrid Manufacturing
Combining additive manufacturing with traditional methods, such as subtractive etching or plating, can overcome some of the limitations of 3D printing. Hybrid approaches enable the creation of circuits with both high complexity and high performance.
7.3 Scalability Improvements
Advances in 3D printing technology, such as faster printing speeds and larger build volumes, will make additive manufacturing more viable for high-volume production.
7.4 Integration with AI and Machine Learning
The integration of artificial intelligence (AI) and machine learning into additive manufacturing processes can optimize printing parameters, improve quality control, and enable predictive maintenance.
8. Conclusion
Additive manufacturing is transforming the design and manufacture of complex multilayer circuits, offering unprecedented levels of customization, rapid prototyping, and innovation. While challenges remain, the benefits of this technology are driving its adoption across a wide range of industries, from wearable electronics to aerospace. By understanding the principles, benefits, and challenges of additive manufacturing, designers and manufacturers can unlock new possibilities and stay ahead in the rapidly evolving electronics industry.
This guide provides a comprehensive overview of additive manufacturing for complex multilayer circuits, covering everything from design considerations to future trends. By embracing this cutting-edge technology, you can push the boundaries of what’s possible in electronics design and manufacturing.