Flexible printed circuit boards (flex PCBs) have become increasingly popular in modern electronics due to their ability to bend and flex. However, flex PCBs come at a higher cost compared to their rigid PCB counterparts. There are several factors that contribute to the higher prices of flex PCBs:
Raw Material Costs
Base Materials
The base materials used in flex PCBs are more expensive than those used in rigid PCBs. The most common base materials for flex PCBs are polyimide and polyester films.
Polyimide films like Kapton or Upilex are relatively expensive but have excellent thermal stability and flexural endurance. Polyester films are cheaper but cannot withstand high temperatures.
Copper Foil
Copper foil is laminated onto the flexible substrate to create the conductive traces. Flex PCBs typically use rolled annealed copper foil which is more expensive than electrodeposited foil used in rigid PCBs.
The thickness of the copper foil is also lower for flex PCBs, usually around 1 oz/ft2 versus 1-2 oz/ft2 for rigid PCBs. The thinner foil increases cost.
Coverlay/Coverfilm
Coverlay or coverfilm is a protective layer laminated over the copper traces. Polyimide coverlay provides the best protection but is more costly than acrylic or epoxy options.
Fabrication Process
Photolithography
The imaging and etching processes used to pattern copper traces on flex PCBs require more specialized equipment suited for flexible substrates.
Most rigid PCB fabricators use panel sizes of 18”x24” or 21”x24”. But flex PCB fabrication is done on smaller panels due to the challenges of handling thin flexible materials in larger formats.
Smaller panel sizes reduce fabrication efficiency and increase cost.
Registration
Precise registration (alignment) of layers is critical during the imaging process. Flexible substrates are more difficult to control and register compared to rigid laminates.
Advanced registration systems are needed to achieve the tight tolerances necessary for flex PCBs. This requires substantial capital investment, increasing costs.
Handling and Transportation
Flex materials need to be processed differently than rigid boards throughout the fabrication process. The thin, bendable substrates require more delicate handling, such as dedicated racks and carriers.
Automated material handling is more complex and expensive for flex PCBs. Manual labour costs are also higher for handling and inspection during production.
Shipping finished flex PCBs also requires specially designed carriers to prevent damage during transportation.
Testing and Inspection
Automated Optical Inspection (AOI)
AOI machines check for defects and quality issues. Flex PCBs often require special fixtures, lighting, and calibration procedures due to the unique properties of the substrates.
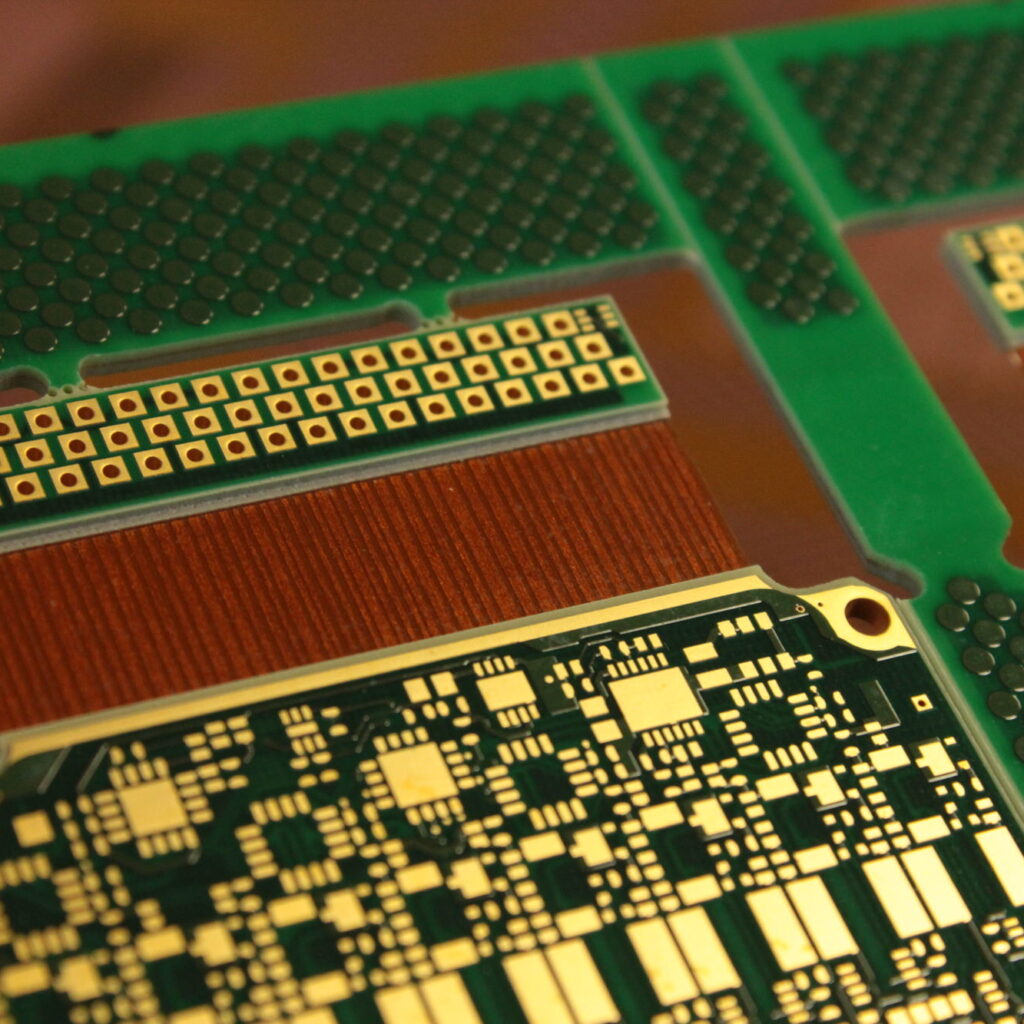
Upgrading AOI capabilities to support flex PCB production involves substantial expense.
Flying Probe Testing
Flying probe testers use movable probes to test electrical connectivity on bare boards. Standard flying probe machines designed for rigid boards usually cannot accommodate thin flex materials.
Specialized flying probe equipment is needed to reliably handle flex PCBs, driving up test costs.
Manual Inspection
The flexible nature of the boards means that manual visual inspection is more critical in flex PCB fabrication. However, manual inspection relies on operators with specialized training and expertise in flex PCB quality control.
Having dedicated and skilled staff for manual inspection increases labor costs.
Low Production Volumes
Flex PCB production volumes are typically much lower than rigid PCB volumes. It is not uncommon for prototyping volumes to be a few boards or even single digits.
The costs of production equipment, facilities, and staff are distributed over fewer boards, resulting in a higher cost per board.
Design Factors
Certain design decisions also impact flex PCB pricing:
- More layer counts increase costs due to additional imaging, lamination, and registration steps required.
- Tighter trace/space widths and smaller vias require more expensive fabrication capabilities.
- More bends in the design make fabrication more difficult and drive up cost.
- Multilayer flex with blind/buried vias involves additional processing complexity.
- Small outline shapes drive cost up due to material utilization.
- Thinner dielectrics require special handling during lamination.
- Plating holes, edges, stiffeners, and other secondary operations add steps and cost.
Summary of Cost Factors:
- Base materials – polyimide, polyester, thin copper foil
- Protective coverlay and stiffeners
- Specialized imaging and etching equipment
- Tight layer-to-layer registration
- Delicate handling requirements
- Custom fixtures for fabrication and inspection
- Low production volumes
- Complex designs with more layers, dense features
The combination of advanced materials, process challenges, low volume production, and complex designs results in flex PCBs having a higher cost compared to standard rigid PCBs. However, the benefits of flexibility and reliability make flex PCBs an indispensable technology where bending and contour-following connections are required.
Frequently Asked Questions
Why can’t flexible PCBs be made using the same process as rigid PCBs?
The thin, bendable materials used in flex PCBs require different fabrication techniques than the rigid, self-supporting boards used in standard PCBs. Flexible substrates need more delicate handling and processing to prevent damage. The imaging, plating, lamination, and testing processes must also be adapted for the flexible boards.
Are multilayer flex PCBs more expensive than 2-layer versions?
Yes, multilayer flex PCBs typically cost more than 2-layer versions. Each additional layer adds steps for imaging, lamination, and registration during fabrication. Multilayer flex with blind/buried vias is even more complex and expensive.
Is flex PCB production volume as high as rigid PCBs?
No. Flex PCB production volumes are usually much lower than standard rigid PCB volumes. It is common for prototype and low volume orders to be just a few boards. The costs of the fabrication equipment and facilities have to be distributed over a smaller number of boards, increasing the cost per board.
Can flex PCBs be tested using the same equipment as rigid PCBs?
Most standard testing equipment designed for rigid boards cannot be used directly with flex PCBs. For example, flying probe testers require special fixtures and calibration for thin flex materials. And automated optical inspection (AOI) machines often need custom lighting and setups.
Are there certain flex PCB design factors that increase cost?
Yes. Design choices like number of layers, trace density, bend radius, small outlines, and secondary operations will impact the fabrication difficulty and ultimately the cost. The more complex the flex PCB design, the higher the fabrication pricing.