Why is PCB Depaneling Necessary?
PCBs are typically manufactured in large panels containing multiple copies of the same board design. This approach offers several advantages:
-
Cost-effectiveness: Producing multiple boards on a single panel reduces material waste and optimizes the use of manufacturing equipment, resulting in lower production costs.
-
Efficiency: Handling a single large panel rather than numerous individual boards streamlines the manufacturing process, saving time and resources.
-
Consistency: Manufacturing boards in a panel ensures consistent quality across all boards, as they undergo the same processes simultaneously.
However, to use the individual boards in electronic devices or for further assembly, they must be separated from the panel. This is where PCB depaneling comes into play.
PCB Depaneling Methods
There are several methods used for PCB depaneling, each with its own advantages and limitations. The choice of method depends on factors such as the board material, thickness, design complexity, and the required level of precision. The most common PCB depaneling methods include:
1. V-Scoring
V-scoring is a popular depaneling method that involves creating V-shaped grooves along the board edges during the PCB manufacturing process. These grooves are cut partially through the board, leaving a thin layer of material that holds the individual boards together in the panel.
Advantages:
– Cost-effective and simple process
– Suitable for both rigid and flexible PCBs
– Allows for easy manual separation of boards
Limitations:
– Not suitable for thick or high-density boards
– May cause stress on the board during separation
– Requires additional space on the panel for the V-grooves
2. Routing
Routing, also known as milling, uses a computer-controlled router with a spinning blade to cut along the board edges, separating the individual boards from the panel. This method offers high precision and can handle complex board shapes.
Advantages:
– High precision and accuracy
– Can handle complex board shapes and designs
– Suitable for thick and high-density boards
Limitations:
– More expensive than V-scoring
– Slower process compared to other methods
– May cause dust and debris during the cutting process
3. Punching
Punching involves using a custom-made die to punch out the individual boards from the panel. This method is fast and efficient, making it suitable for high-volume production.
Advantages:
– Fast and efficient process
– Suitable for high-volume production
– Consistent and precise results
Limitations:
– Requires custom-made dies, which can be expensive
– Limited flexibility for design changes
– May cause stress on the board during separation
4. Laser Cutting
Laser cutting uses a high-powered laser beam to cut along the board edges, separating the individual boards from the panel. This method offers high precision and minimal stress on the board.
Advantages:
– High precision and accuracy
– Minimal stress on the board during separation
– Suitable for complex board shapes and designs
Limitations:
– More expensive than other methods
– Slower process compared to punching
– May cause discoloration or burning along the cut edges
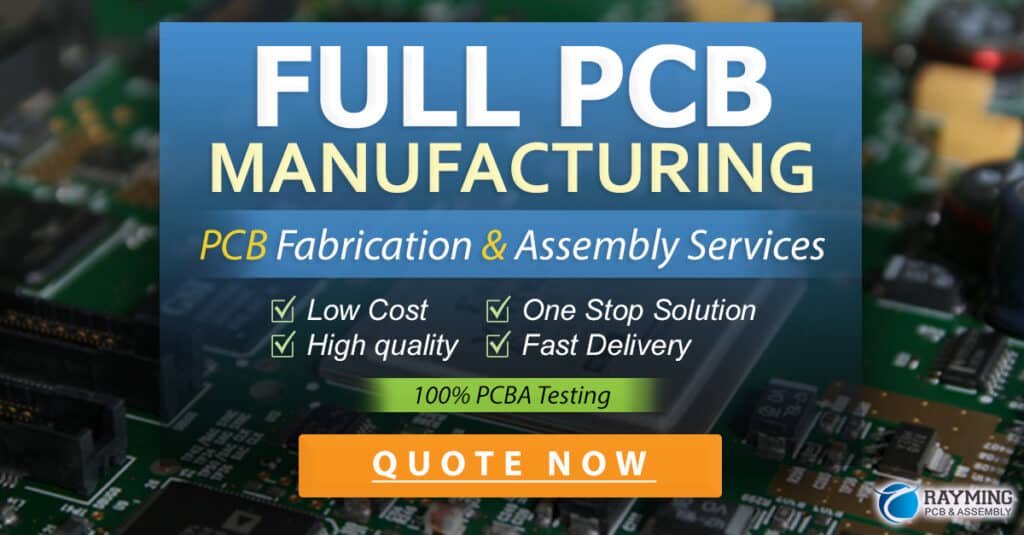
Factors to Consider When Choosing a PCB Depaneling Method
When selecting a PCB depaneling method, consider the following factors:
-
Board material and thickness: Some methods may not be suitable for thick or rigid boards, while others can handle a wide range of materials and thicknesses.
-
Board design complexity: Complex board shapes or designs may require more precise depaneling methods, such as routing or laser cutting.
-
Production volume: High-volume production may benefit from faster methods like punching, while low-volume or prototyping projects may opt for more flexible methods like V-scoring or routing.
-
Cost: Consider the cost of the depaneling process, including equipment, tooling, and labor costs, and balance it against your project budget and requirements.
-
Quality and precision requirements: Some applications may demand higher precision and cleaner cut edges, in which case laser cutting or routing may be preferred over V-scoring or punching.
Best Practices for PCB Depaneling
To ensure successful PCB depaneling, consider the following best practices:
-
Design for depaneling: When designing your PCB, consider the depaneling method you will use and incorporate necessary features, such as V-grooves or tab routes, to facilitate the process.
-
Allow for adequate spacing: Provide sufficient spacing between individual boards on the panel to accommodate the chosen depaneling method and avoid damaging the boards during separation.
-
Choose the right depaneling equipment: Select depaneling equipment that is compatible with your chosen method and can handle your specific board requirements, such as material, thickness, and design complexity.
-
Perform regular maintenance: Regularly maintain and calibrate your depaneling equipment to ensure consistent performance and minimize the risk of damage to the boards.
-
Implement quality control measures: Establish quality control procedures to inspect the depaneled boards for any signs of damage, stress, or contamination, and address any issues promptly.
Frequently Asked Questions (FAQ)
- What is the most cost-effective PCB depaneling method for low-volume production?
-
For low-volume production, V-scoring is often the most cost-effective depaneling method. It is simple to implement and does not require expensive tooling or equipment.
-
Can PCB depaneling cause damage to the boards?
-
Yes, improper depaneling techniques or equipment can cause damage to the boards, such as stress, cracking, or delamination. It is essential to choose the right method and follow best practices to minimize the risk of damage.
-
How do I choose the right PCB depaneling method for my project?
-
When choosing a PCB depaneling method, consider factors such as the board material, thickness, design complexity, production volume, cost, and quality requirements. Consult with your PCB manufacturer or a depaneling expert to determine the best method for your specific project.
-
Can I use multiple depaneling methods on the same PCB panel?
-
Yes, it is possible to use multiple depaneling methods on the same panel, depending on the board requirements and design. For example, you may use V-scoring for some boards and routing for others based on their complexity or thickness.
-
How can I ensure consistent quality when depaneling PCBs?
- To ensure consistent quality, implement best practices such as designing for depaneling, allowing for adequate spacing, choosing the right equipment, performing regular maintenance, and implementing quality control measures. Additionally, work with experienced PCB manufacturers and depaneling service providers who follow industry standards and best practices.
Depaneling Method | Advantages | Limitations |
---|---|---|
V-Scoring | – Cost-effective and simple – Suitable for rigid and flexible PCBs – Allows for easy manual separation |
– Not suitable for thick or high-density boards – May cause stress on the board – Requires additional space for V-grooves |
Routing | – High precision and accuracy – Can handle complex board shapes – Suitable for thick and high-density boards |
– More expensive than V-scoring – Slower process – May cause dust and debris |
Punching | – Fast and efficient – Suitable for high-volume production – Consistent and precise results |
– Requires custom-made dies – Limited flexibility for design changes – May cause stress on the board |
Laser Cutting | – High precision and accuracy – Minimal stress on the board – Suitable for complex board shapes |
– More expensive than other methods – Slower process – May cause discoloration or burning |
In conclusion, PCB depaneling is a critical step in the PCB manufacturing process, ensuring that individual boards are separated from larger panels efficiently and accurately. By understanding the various depaneling methods, their advantages and limitations, and the factors to consider when choosing a method, you can ensure that your PCBs are depaneled successfully, ready for the next stages of assembly or packaging. Implementing best practices and working with experienced professionals can help you achieve consistent quality and minimize the risk of damage to your boards during the depaneling process.