What is a Surface-Mount PCB?
A surface-mount PCB is a printed circuit board designed to accommodate surface-mount devices (SMDs) – electronic components that are mounted directly onto the surface of the board, rather than through holes as in traditional through-hole technology. SMDs are smaller, lighter, and have shorter leads, allowing for higher component density and improved performance.
Advantages of Surface-Mount PCBs
-
Miniaturization: SMDs are significantly smaller than their through-hole counterparts, enabling the creation of more compact and lightweight electronic devices.
-
Increased component density: With SMDs, more components can be placed on a single PCB, allowing for more complex circuits and enhanced functionality.
-
Improved performance: Shorter lead lengths in SMDs reduce parasitic capacitance and inductance, resulting in better signal integrity and higher-frequency operation.
-
Cost-effectiveness: SMT enables faster and more automated assembly processes, reducing labor costs and increasing production efficiency.
-
Enhanced reliability: SMDs have a stronger mechanical bond to the PCB, making them more resistant to vibration and thermal stress.
Surface-Mount PCB Manufacturing Process
The manufacturing process for surface-mount PCBs involves several key steps:
1. PCB Design and Layout
The first step in creating a surface-mount PCB is designing the circuit and laying out the components using electronic design automation (EDA) software. The layout must adhere to SMT design guidelines, ensuring proper spacing, trace widths, and component placement.
2. PCB Fabrication
Once the design is finalized, the PCB is fabricated using a multi-step process:
a. Substrate preparation: The PCB substrate, typically made of FR-4 material, is cleaned and inspected for defects.
b. Copper cladding: A thin layer of copper is laminated onto the substrate.
c. Photoresist application: A light-sensitive polymer, called photoresist, is applied to the copper layer.
d. Exposure and development: The photoresist is exposed to UV light through a photomask, which contains the PCB pattern. The exposed areas are then removed during the development process.
e. Etching: The exposed copper is etched away using a chemical solution, leaving behind the desired conductive traces.
f. Soldermask and silkscreen: A soldermask layer is applied to protect the copper traces, while a silkscreen layer is added for component labeling and identification.
3. Solder Paste Application
Solder paste, a mixture of tiny solder particles and flux, is precisely applied to the PCB’s SMD pads using a stencil or screen printing process. The stencil ensures that the correct amount of solder paste is deposited on each pad.
4. Component Placement
SMDs are placed onto the solder paste-covered pads using automated pick-and-place machines. These machines use computer vision and precise positioning systems to accurately place components at high speeds.
5. Reflow Soldering
The PCB with placed components undergoes a reflow soldering process in a reflow oven. The board is heated gradually, allowing the solder paste to melt and form a strong electrical and mechanical bond between the components and the PCB pads.
6. Inspection and Testing
After reflow soldering, the PCB undergoes visual inspection and automated optical inspection (AOI) to detect any manufacturing defects, such as misaligned components, solder bridges, or insufficient solder joints. Functional testing is also performed to ensure that the assembled PCB operates as intended.
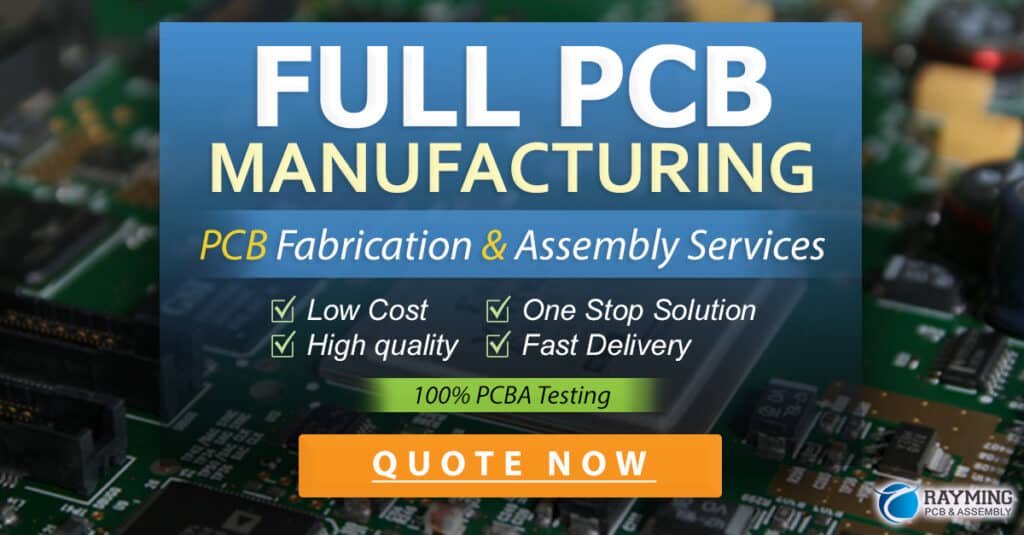
Surface-Mount PCB Applications
Surface-mount PCBs find applications across a wide range of industries and products:
-
Consumer electronics: Smartphones, tablets, laptops, and wearable devices extensively use surface-mount PCBs to achieve compact form factors and advanced functionality.
-
Automotive electronics: Modern vehicles incorporate numerous surface-mount PCBs for engine control, infotainment systems, and advanced driver assistance systems (ADAS).
-
Medical devices: Miniaturized and highly reliable surface-mount PCBs are essential for medical devices such as pacemakers, insulin pumps, and patient monitoring systems.
-
Industrial automation: Surface-mount PCBs play a crucial role in industrial control systems, sensors, and communication devices, enabling efficient and reliable automation.
-
Aerospace and defense: High-performance surface-mount PCBs are used in avionics, satellite communications, and military equipment, where reliability and space constraints are critical.
Surface-Mount PCB Design Considerations
When designing a surface-mount PCB, several key factors must be considered to ensure optimal performance and manufacturability:
-
Component selection: Choose SMDs that are compatible with the PCB’s electrical and mechanical requirements, considering factors such as package size, pin count, and thermal characteristics.
-
Pad design: Ensure that SMD pads are appropriately sized and spaced to accommodate the selected components and facilitate reliable solder connections.
-
Trace routing: Route traces efficiently to minimize signal interference and maintain proper impedance control, especially for high-frequency circuits.
-
Thermal management: Consider the thermal dissipation requirements of SMDs and design the PCB layout accordingly, incorporating features such as thermal vias and heatsinks when necessary.
-
Manufacturing constraints: Adhere to the manufacturing capabilities and guidelines of the chosen PCB fabrication and assembly partner to avoid design issues and ensure successful production.
Frequently Asked Questions (FAQ)
-
What is the difference between surface-mount and through-hole technology?
Surface-mount technology involves mounting components directly onto the surface of a PCB, while through-hole technology requires components to be inserted into drilled holes and soldered on the opposite side of the board. -
Can surface-mount and through-hole components be used together on the same PCB?
Yes, it is possible to use both surface-mount and through-hole components on the same PCB, creating a hybrid design. However, this may increase manufacturing complexity and cost. -
What are the most common SMD package types?
Some of the most common SMD package types include: - Chip resistors and capacitors (0402, 0603, 0805, etc.)
- Small Outline Integrated Circuit (SOIC)
- Quad Flat Pack (QFP)
- Ball Grid Array (BGA)
-
Quad Flat No-lead (QFN)
-
How does the solder paste application process work in SMT?
Solder paste is applied to the PCB’s SMD pads using a stencil or screen printing process. The stencil, which has apertures corresponding to the pad locations, is placed over the PCB, and solder paste is spread across the stencil using a squeegee. The stencil ensures that the correct amount of solder paste is deposited on each pad. -
What are the challenges associated with surface-mount PCB rework?
Surface-mount PCB rework can be challenging due to the small size and close proximity of SMDs. Common challenges include: - Localized heating to avoid damaging nearby components
- Precise component alignment during replacement
- Ensuring proper solder joint formation without bridging or insufficient solder
- Cleaning residual solder and flux from the rework area
In conclusion, surface-mount PCBs have become the dominant technology in the electronics industry, offering numerous advantages over traditional through-hole designs. By understanding the manufacturing process, design considerations, and applications of surface-mount PCBs, engineers and manufacturers can create more efficient, reliable, and compact electronic devices that meet the ever-increasing demands of modern technology.