Introduction to Stacked PCBs
In the world of electronic design and manufacturing, printed circuit boards (PCBs) play a crucial role in connecting and supporting various components. As technology advances and devices become more compact and complex, the demand for efficient PCB design techniques increases. One such technique is PCB stacking, also known as stacked PCB. In this article, we will delve into the concept of stacking in PCB, its benefits, applications, and design considerations.
What is a Stacked PCB?
A stacked PCB, also referred to as a multi-layer PCB or 3D PCB, is a printed circuit board that consists of multiple layers of conductive material and insulating substrate stacked on top of each other. Unlike traditional single-layer or double-layer PCBs, stacked PCBs allow for a higher density of components and interconnections within a limited space.
How Stacked PCBs are Manufactured
The manufacturing process of stacked PCBs involves several steps:
-
Layer Fabrication: Each layer of the stacked PCB is fabricated separately, similar to a standard single-layer PCB. The conductive patterns are etched onto the copper-clad laminate using photolithography and chemical etching processes.
-
Layer Alignment: The fabricated layers are precisely aligned using registration holes or fiducial markers to ensure proper positioning.
-
Lamination: The aligned layers are bonded together using heat and pressure in a lamination process. Insulating material, such as prepreg (pre-impregnated) or bonding sheets, is placed between the layers to provide electrical isolation and structural integrity.
-
Drilling: After lamination, holes are drilled through the stacked layers to create vias, which are conductive pathways that connect different layers of the PCB.
-
Plating: The drilled holes are plated with a conductive material, typically copper, to establish electrical connections between the layers.
-
Surface Finishing: The outer layers of the stacked PCB undergo surface finishing processes, such as solder mask application and silkscreen printing, to protect the copper traces and provide labeling for component placement.
Types of Stacked PCBs
Stacked PCBs can be categorized based on the number of layers and the arrangement of the stacked boards:
-
Multi-Layer PCBs: These are the most common type of stacked PCBs, where multiple layers of conductive material and insulating substrate are laminated together. The number of layers can vary from four to over thirty, depending on the complexity of the design.
-
Rigid-Flex PCBs: Rigid-flex PCBs combine rigid PCB layers with flexible PCB layers. The flexible layers allow for bending and folding of the PCB, enabling 3D packaging and improved connectivity between different sections of the board.
-
Package-on-Package (PoP): PoP is a stacking technique where one packaged chip, such as a memory chip, is mounted on top of another packaged chip, such as a processor. This arrangement saves space and reduces the overall footprint of the PCB.
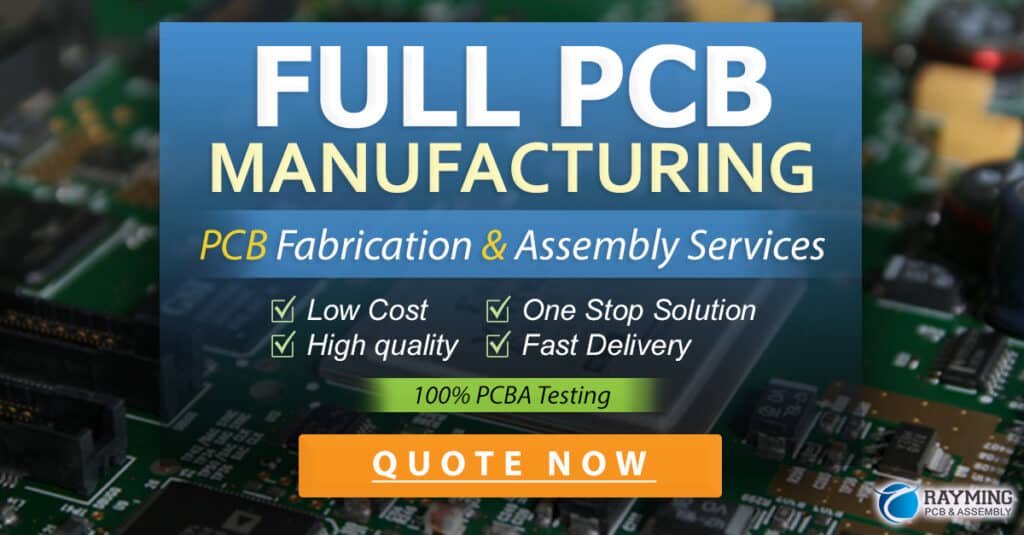
Benefits of Stacked PCBs
Stacked PCBs offer several advantages over traditional single-layer or double-layer PCBs:
-
Space Savings: By stacking multiple layers, stacked PCBs can accommodate a higher density of components and interconnections within a smaller footprint. This is particularly beneficial for miniaturized devices and space-constrained applications.
-
Improved Signal Integrity: With shorter interconnections between layers, stacked PCBs can minimize signal distortion and cross-talk. The reduced path length also leads to improved signal speed and reduced noise.
-
Enhanced Functionality: Stacked PCBs enable the integration of multiple functions and subsystems within a single board. Different layers can be dedicated to specific functions, such as power distribution, signal routing, or shielding.
-
Reduced Assembly Costs: By consolidating multiple single-layer PCBs into a single stacked PCB, the overall assembly costs can be reduced. Fewer boards need to be manufactured and assembled, leading to cost savings.
-
Increased Reliability: Stacked PCBs offer improved mechanical stability and protection against environmental factors. The laminated structure provides better resistance to vibration, shock, and thermal stress.
Applications of Stacked PCBs
Stacked PCBs find applications in various industries and products where space optimization, high functionality, and reliability are critical:
-
Consumer Electronics: Smartphones, tablets, wearable devices, and IoT gadgets often utilize stacked PCBs to achieve compact designs without compromising functionality.
-
Aerospace and Defense: Stacked PCBs are used in avionics systems, satellites, and military equipment, where high-density packaging and robust performance are essential.
-
Medical Devices: Implantable medical devices, such as pacemakers and hearing aids, rely on stacked PCBs to minimize size while maintaining reliability and functionality.
-
Automotive Electronics: Advanced driver assistance systems (ADAS), infotainment systems, and engine control units (ECUs) in modern vehicles employ stacked PCBs for space efficiency and enhanced capabilities.
-
High-Performance Computing: Stacked PCBs are used in servers, data centers, and supercomputers to achieve high-speed interconnections and optimize system performance.
Design Considerations for Stacked PCBs
Designing stacked PCBs requires careful consideration of various factors to ensure optimal performance and manufacturability:
-
Layer Stack-up: The arrangement of conductive layers, insulating layers, and their thicknesses should be carefully planned to achieve the desired electrical and mechanical properties. Factors such as signal integrity, impedance control, and thermal management should be taken into account.
-
Via Design: The placement and sizing of vias are critical in stacked PCBs. Proper via design ensures reliable connections between layers while minimizing signal degradation and manufacturing challenges.
-
Thermal Management: Stacked PCBs generate more heat due to the high density of components and interconnections. Adequate thermal management techniques, such as the use of thermal vias, heat sinks, or cooling solutions, should be incorporated into the design.
-
Signal Integrity: Proper signal routing, impedance matching, and shielding techniques should be employed to minimize crosstalk, signal reflections, and electromagnetic interference (EMI) in stacked PCBs.
-
Manufacturing Constraints: The design of stacked PCBs should adhere to the manufacturing capabilities and limitations of the chosen fabrication process. Factors such as minimum feature sizes, layer registration accuracy, and drilling tolerances should be considered.
-
Testing and Inspection: Stacked PCBs require specialized testing and inspection techniques to ensure the integrity of interconnections and the overall functionality of the board. Methods such as X-ray inspection, boundary scan testing, and electrical testing are commonly used.
Challenges and Limitations of Stacked PCBs
While stacked PCBs offer numerous benefits, they also present certain challenges and limitations:
-
Design Complexity: Designing stacked PCBs is more complex compared to single-layer or double-layer PCBs. The increased number of layers and interconnections requires careful planning and analysis to ensure signal integrity and manufacturability.
-
Manufacturing Cost: The fabrication and assembly of stacked PCBs are generally more expensive than traditional PCBs due to the additional materials, processes, and equipment required.
-
Repair and Rework: Repairing or reworking stacked PCBs can be challenging due to the multiple layers and interconnections. Accessing and replacing components on inner layers may require specialized techniques or may not be feasible in some cases.
-
Thermal Management: The high density of components and interconnections in stacked PCBs can lead to increased heat generation. Effective thermal management strategies are essential to prevent overheating and ensure reliable operation.
-
Mechanical Stress: The lamination process and the different thermal expansion coefficients of the materials used in stacked PCBs can introduce mechanical stress. Proper material selection and design techniques are necessary to mitigate stress-related issues.
Future Trends in Stacked PCB Technology
As technology continues to advance, stacked PCB technology is evolving to meet the growing demands for miniaturization, high performance, and multi-functionality:
-
3D Packaging: The integration of stacked PCBs with 3D packaging techniques, such as through-silicon vias (TSVs) and chip stacking, is gaining traction. This approach enables even higher density and performance by combining multiple chips and PCB layers into a single package.
-
Embedded Components: The embedding of passive components, such as resistors and capacitors, within the PCB substrate is becoming more common. Embedded components save space on the surface of the PCB and improve signal integrity by reducing the distance between components.
-
High-Speed Materials: The development of advanced materials, such as low-loss dielectrics and high-speed laminates, is enabling faster signal transmission and improved signal integrity in stacked PCBs.
-
Flexible and Stretchable PCBs: The integration of flexible and stretchable materials into stacked PCBs is opening up new possibilities for wearable electronics, medical devices, and other applications that require conformable and bendable circuits.
Frequently Asked Questions (FAQ)
-
What is the difference between a stacked PCB and a multi-layer PCB?
A stacked PCB and a multi-layer PCB are often used interchangeably. Both refer to a PCB that consists of multiple layers of conductive material and insulating substrate stacked on top of each other. The term “stacked PCB” emphasizes the vertical stacking of layers, while “multi-layer PCB” highlights the presence of multiple layers. -
How many layers can a stacked PCB have?
The number of layers in a stacked PCB can vary depending on the complexity of the design and the manufacturing capabilities. Stacked PCBs can have as few as four layers or as many as thirty or more layers. The most common layer counts are four, six, eight, ten, and twelve layers. -
Are stacked PCBs more expensive than single-layer or double-layer PCBs?
Yes, stacked PCBs are generally more expensive to manufacture compared to single-layer or double-layer PCBs. The additional materials, processes, and equipment required for fabricating and assembling stacked PCBs contribute to the higher cost. However, the cost per unit can be offset by the space savings, improved functionality, and reduced assembly costs in the overall product. -
What are the challenges in repairing or reworking stacked PCBs?
Repairing or reworking stacked PCBs can be challenging due to the multiple layers and interconnections. Accessing components on inner layers may require specialized techniques, such as micro-sectioning or layer-by-layer removal. In some cases, rework may not be feasible, and the entire board may need to be replaced. -
What are the future trends in stacked PCB technology?
The future trends in stacked PCB technology include the integration of 3D packaging techniques, such as through-silicon vias (TSVs) and chip stacking, the embedding of passive components within the PCB substrate, the use of high-speed materials for improved signal integrity, and the development of flexible and stretchable PCBs for wearable electronics and medical devices.
Conclusion
Stacking in PCB is a powerful technique that enables the creation of high-density, multi-functional, and space-efficient printed circuit boards. By leveraging multiple layers of conductive material and insulating substrate, stacked PCBs offer numerous benefits, including space savings, improved signal integrity, enhanced functionality, reduced assembly costs, and increased reliability.
However, designing and manufacturing stacked PCBs also presents challenges, such as increased complexity, higher manufacturing costs, and difficulties in repair and rework. Careful consideration of design factors, such as layer stack-up, via design, thermal management, and signal integrity, is essential for achieving optimal performance and manufacturability.
As technology advances, stacked PCB technology continues to evolve, with trends such as 3D packaging, embedded components, high-speed materials, and flexible and stretchable PCBs shaping the future of electronic design and manufacturing.
By understanding the concepts, benefits, applications, and design considerations of stacked PCBs, engineers and designers can leverage this technology to create innovative and efficient electronic products that meet the ever-increasing demands of the modern world.
Layer Count | Typical Applications |
---|---|
4 | Simple digital circuits, low-density analog circuits |
6 | Digital circuits, mixed-signal circuits |
8 | Complex digital circuits, high-speed designs |
10 | High-density digital circuits, advanced analog designs |
12+ | High-performance computing, aerospace, and defense |