Introduction to Silkscreen on PCB
Silkscreen, also known as screen printing, is a crucial component of printed circuit board (PCB) design and manufacturing. It involves applying ink onto the PCB surface through a fine mesh screen, creating text, logos, and other visual elements. The silkscreen layer on a PCB serves multiple purposes, including component identification, branding, and providing essential information for assembly and maintenance.
In this comprehensive article, we will delve into the world of silkscreen on PCB, exploring its importance, the silkscreen printing process, design considerations, and best practices for achieving optimal results.
The Importance of Silkscreen on PCB
Component Identification
One of the primary functions of silkscreen on PCB is to facilitate component identification. The silkscreen layer typically includes component designators, such as R1 for a resistor or C2 for a capacitor, along with their respective values or ratings. This information is invaluable during the assembly process, as it guides the placement of components on the PCB.
Orientation and Polarity Markers
Silkscreen markings also indicate the orientation and polarity of components. For example, a small circle or dot may be used to denote the cathode end of a diode or the positive terminal of a capacitor. These markers ensure that components are installed correctly, preventing potential damage or malfunction.
Branding and Aesthetic Appeal
In addition to its functional aspects, silkscreen on PCB serves a branding and aesthetic purpose. Companies often include their logos, product names, or other branding elements on the silkscreen layer. This not only enhances the visual appeal of the PCB but also helps in product identification and marketing.
Assembly and Maintenance Instructions
Silkscreen can also provide essential information for assembly and maintenance. This may include warnings, handling instructions, or other relevant guidelines. For instance, a “Do Not Touch” warning near sensitive components or a “High Voltage” indication near power supply sections can prevent accidental damage or injury.
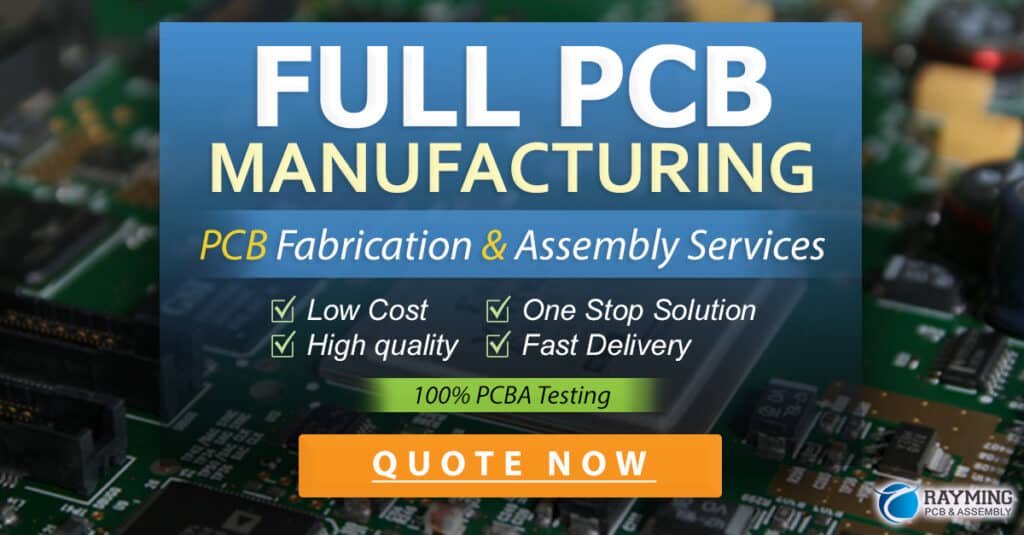
The Silkscreen Printing Process
Screen Preparation
The silkscreen printing process begins with the preparation of the screen. A fine mesh screen, typically made of polyester or stainless steel, is stretched tightly over a frame. The desired silkscreen design is then transferred onto the screen using a photosensitive emulsion or a stencil.
Ink Application
Once the screen is prepared, ink is applied to the surface of the PCB. The ink is typically a special type of epoxy or UV-curable ink that adheres well to the PCB material and offers excellent durability. The ink is pushed through the open areas of the screen onto the PCB surface using a squeegee.
Curing and Drying
After the ink is applied, the PCB undergoes a curing and drying process. This ensures that the ink adheres properly to the PCB surface and achieves its desired properties. Curing can be done using heat, UV light, or a combination of both, depending on the type of ink used.
Silkscreen Design Considerations
Legibility and Font Selection
When designing the silkscreen layer, legibility is of utmost importance. The chosen font should be clear, easy to read, and suitable for the specific PCB application. Sans-serif fonts, such as Arial or Helvetica, are commonly used due to their clarity and readability at small sizes.
Size and Spacing
The size and spacing of silkscreen elements should be carefully considered. Component designators and values should be large enough to be easily readable but not so large that they interfere with component placement or other PCB features. Adequate spacing between elements ensures clarity and prevents confusion.
Color and Contrast
The color and contrast of the silkscreen ink should be chosen to provide optimal visibility against the PCB substrate. White ink on a dark substrate or black ink on a light substrate are common choices for good contrast. However, other colors may be used for specific applications or to match branding requirements.
Placement and Clearance
When placing silkscreen elements, it is crucial to maintain appropriate clearance from components, pads, and other PCB features. Silkscreen should not overlap with component footprints or interfere with the soldering process. Industry standards, such as the IPC guidelines, provide recommended clearance distances for various PCB manufacturing processes.
Best Practices for Silkscreen on PCB
Consistent Naming Conventions
Using consistent naming conventions for component designators and other silkscreen elements helps maintain clarity and prevents confusion. For example, using “R” for resistors, “C” for capacitors, and “IC” for integrated circuits is a common practice.
Readable Font Size
To ensure readability, it is recommended to use a minimum font size of 0.8mm (0.032 inches) for silkscreen text. Smaller sizes may be used in certain cases but should be carefully evaluated for legibility.
Avoid Overcrowding
Overcrowding the silkscreen layer with too much information can lead to confusion and manufacturing difficulties. Strike a balance between providing necessary information and maintaining a clean, uncluttered layout.
Consider Manufacturing Limitations
When designing the silkscreen layer, it is essential to consider the limitations of the manufacturing process. Fine details, thin lines, or small gaps may not be reproducible consistently. Consulting with the PCB manufacturer and adhering to their guidelines can help ensure successful silkscreen printing.
Use Silkscreen for Essential Information
While silkscreen can be used for various purposes, it is best to reserve it for essential information. Overloading the silkscreen layer with unnecessary details can clutter the PCB and make it harder to read and understand.
Frequently Asked Questions (FAQ)
1. What is the purpose of silkscreen on PCB?
The purpose of silkscreen on PCB is to provide essential information for component identification, orientation, assembly, and maintenance. It includes component designators, values, polarity markers, and other relevant details.
2. What type of ink is used for silkscreen printing on PCBs?
Special epoxy or UV-curable inks are commonly used for silkscreen printing on PCBs. These inks offer excellent adhesion to the PCB surface and provide durability to withstand the manufacturing process and operational conditions.
3. What is the recommended minimum font size for silkscreen text?
The recommended minimum font size for silkscreen text is 0.8mm (0.032 inches) to ensure readability. However, smaller sizes may be used in certain cases, subject to careful evaluation for legibility.
4. Can silkscreen be used for branding purposes on PCBs?
Yes, silkscreen can be used for branding purposes on PCBs. Companies often include their logos, product names, or other branding elements on the silkscreen layer to enhance the visual appeal and aid in product identification.
5. What should be considered when placing silkscreen elements on a PCB?
When placing silkscreen elements on a PCB, it is important to maintain appropriate clearance from components, pads, and other features. Industry standards, such as the IPC guidelines, provide recommended clearance distances to ensure proper manufacturing and assembly.
Conclusion
Silkscreen on PCB plays a vital role in the design, manufacturing, and assembly of electronic devices. It provides essential information for component identification, orientation, and branding while enhancing the overall aesthetics of the PCB.
By understanding the importance of silkscreen, the printing process, design considerations, and best practices, PCB designers and manufacturers can create high-quality silkscreen layers that facilitate efficient assembly, maintenance, and product identification.
As PCB technology continues to advance, the role of silkscreen remains crucial in ensuring the functionality, reliability, and usability of electronic devices across various industries.
Aspect | Considerations |
---|---|
Legibility | Choose clear, easy-to-read fonts (e.g., Arial, Helvetica) |
Size and Spacing | Ensure adequate size and spacing for clarity and avoid interference |
Color and Contrast | Select colors that provide optimal visibility against the PCB substrate |
Placement and Clearance | Maintain appropriate clearance from components and other PCB features |
By adhering to these design considerations and best practices, PCB designers and manufacturers can create effective and informative silkscreen layers that enhance the overall quality and usability of their products.