The Importance of Prototype PCB Assembly
Prototype PCB assembly plays a crucial role in the product development process for several reasons:
-
Design Validation: Assembling a prototype PCB allows engineers to physically test and validate their circuit design. They can check if the circuit functions as intended, identify any design flaws, and make necessary modifications before proceeding to mass production.
-
Performance Evaluation: With a prototype PCB, engineers can evaluate the performance of their circuit under real-world conditions. They can measure parameters such as power consumption, signal integrity, and thermal behavior to ensure that the design meets the required specifications.
-
Compatibility Testing: Prototype PCB assembly enables engineers to test the compatibility of their circuit with other components or systems. They can verify if the PCB interfaces correctly with sensors, actuators, or communication modules and make any necessary adjustments.
-
Cost Optimization: Building a prototype PCB helps in identifying potential manufacturing challenges and optimizing the design for cost-effective production. Engineers can experiment with different component placements, routing strategies, and assembly techniques to minimize production costs.
-
Investor and Customer Demonstration: A functional prototype PCB serves as a tangible demonstration of the product concept to investors, customers, or stakeholders. It provides a visual representation of the product’s capabilities and helps in securing funding or gathering feedback for further improvements.
The Prototype PCB Assembly Process
The prototype PCB assembly process involves several steps, each requiring careful attention to detail and adherence to industry standards. Here’s an overview of the key stages involved:
1. PCB Design and Layout
The first step in prototype PCB assembly is designing the circuit schematic and creating the PCB layout. Engineers use electronic design automation (EDA) software to capture the schematic diagram, which represents the electrical connections between components. They then create the PCB layout, which determines the physical placement of components and routing of traces on the board.
During the PCB layout process, engineers consider factors such as component footprints, trace widths, clearances, and signal integrity. They follow design guidelines and industry standards to ensure manufacturability and reliability of the PCB.
2. PCB Fabrication
Once the PCB design is finalized, the next step is to fabricate the physical PCB. This involves the following sub-processes:
a. PCB Material Selection: The choice of PCB material depends on the specific requirements of the circuit, such as thermal conductivity, dielectric constant, and mechanical strength. Common PCB materials include FR-4, Rogers, and aluminum.
b. Copper Clad Laminate: The selected PCB material is coated with a thin layer of copper on one or both sides, forming the conductive layer for the traces and pads.
c. Photoresist Application: A photosensitive film called photoresist is applied to the copper surface of the PCB. This film will later be exposed to UV light to transfer the PCB layout pattern onto the copper layer.
d. Exposure and Development: The PCB is exposed to UV light through a photomask, which contains the PCB layout pattern. The exposed areas of the photoresist harden, while the unexposed areas remain soluble. The board is then developed, removing the soluble photoresist and revealing the copper traces.
e. Etching: The exposed copper areas are etched away using a chemical solution, leaving only the desired traces and pads on the PCB.
f. Drilling: Holes are drilled into the PCB to accommodate through-hole components and provide electrical connections between layers.
g. Surface Finish: A surface finish, such as
HASL (Hot Air Solder Leveling), ENIG (Electroless Nickel Immersion Gold), or OSP (Organic Solderability Preservative), is applied to the exposed copper surfaces to prevent oxidation and enhance solderability.
3. Component Sourcing and Preparation
While the PCB is being fabricated, engineers source the required electronic components for the assembly. This involves:
a. Bill of Materials (BOM) Creation: A BOM is a comprehensive list of all the components needed for the PCB assembly, including their quantities, part numbers, and specifications.
b. Component Procurement: Components are purchased from reliable suppliers, ensuring they meet the required specifications and have the necessary certifications.
c. Component Preparation: Some components may require pre-conditioning before assembly, such as baking moisture-sensitive devices (MSDs) to prevent damage during soldering.
4. PCB Assembly
With the fabricated PCB and sourced components ready, the actual assembly process begins. There are two primary methods of PCB assembly:
a. Through-Hole Assembly (THA): In THA, component leads are inserted through the drilled holes in the PCB and soldered on the opposite side. This method is suitable for larger components or those requiring higher mechanical strength.
b. Surface Mount Assembly (SMA): SMA involves placing components directly on the surface of the PCB and soldering them using reflow or wave soldering techniques. SMA allows for smaller component sizes and higher component density compared to THA.
The choice between THA and SMA depends on the specific requirements of the circuit, component availability, and manufacturing capabilities.
During the assembly process, the following steps are performed:
-
Solder Paste Application: For SMA, solder paste is applied to the pads on the PCB using a stencil or screen printing process. The solder paste consists of tiny solder particles suspended in a flux medium.
-
Component Placement: Components are placed on the PCB, either manually or using automated pick-and-place machines. Proper alignment and orientation of the components are crucial for ensuring reliable connections.
-
Soldering: The PCB with placed components is subjected to a controlled heating process, such as reflow soldering for SMA or wave soldering for THA. The solder paste melts, creating a permanent electrical and mechanical bond between the components and the PCB.
-
Inspection and Testing: After soldering, the assembled PCB undergoes visual inspection to check for any defects, such as bridging, cold solder joints, or misaligned components. Automated optical inspection (AOI) systems may be used for more precise and efficient inspection.
5. Prototype Testing and Debugging
Once the prototype PCB is assembled, it undergoes rigorous testing and debugging to ensure its functionality and performance. This stage involves:
a. Power-On Testing: The PCB is powered on, and basic functionality tests are performed to verify that the circuit is operating as intended.
b. Functional Testing: Specific test cases are executed to validate the functionality of individual components and the overall system. This may include testing input/output signals, communication interfaces, and sensor responses.
c. Debugging: If any issues or anomalies are identified during testing, engineers use debugging techniques such as probing, signal tracing, and software debugging to isolate and resolve the problems.
d. Performance Optimization: Based on the testing results, engineers may make minor modifications to the PCB design or component selection to optimize performance, power consumption, or signal integrity.
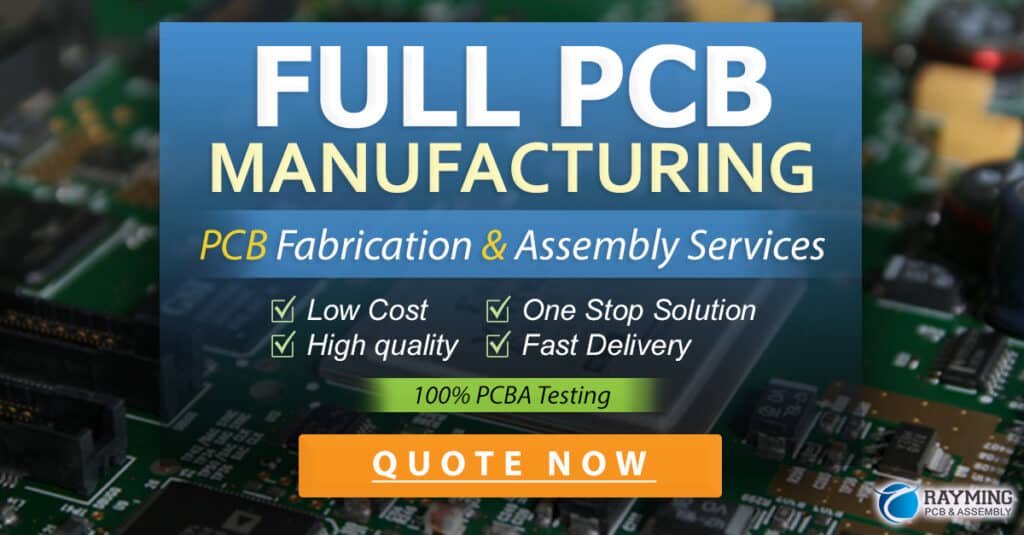
Advantages of Prototype PCB Assembly
Prototype PCB assembly offers several advantages in the product development process:
-
Early Design Validation: Assembling a prototype PCB allows for early validation of the circuit design, enabling engineers to identify and rectify design flaws before mass production. This reduces the risk of costly redesigns and delays later in the development cycle.
-
Iterative Refinement: Prototype PCB assembly enables iterative refinement of the design based on testing and feedback. Engineers can make incremental improvements to the PCB layout, component selection, and firmware until the desired performance and functionality are achieved.
-
Risk Mitigation: By thoroughly testing and debugging the prototype PCB, potential risks and issues can be identified and mitigated early in the development process. This reduces the likelihood of encountering critical problems during mass production or in the final product.
-
Accelerated Time-to-Market: Prototype PCB assembly allows for parallel development activities, such as firmware development, mechanical design, and software integration. By validating the PCB design early, other development tasks can proceed concurrently, accelerating the overall time-to-market for the product.
-
Cost Savings: Identifying and resolving design issues during the prototype stage helps avoid expensive rework and redesigns during mass production. Prototype PCB assembly enables cost optimization by allowing engineers to experiment with different component options and manufacturing processes to find the most cost-effective solution.
Challenges in Prototype PCB Assembly
While prototype PCB assembly offers numerous benefits, it also presents some challenges that need to be addressed:
-
Component Availability: Sourcing components for prototype PCBs can be challenging, especially for specialized or high-performance components with limited availability. Engineers may need to find alternative components or work with suppliers to secure the necessary parts.
-
Manual Assembly: Prototype PCBs are often assembled manually, which can be time-consuming and prone to human errors. Ensuring proper component placement, soldering quality, and handling of sensitive components requires skilled technicians and attention to detail.
-
Limited Test Coverage: Due to time and resource constraints, prototype testing may not cover all possible scenarios or edge cases. Engineers need to prioritize critical tests and develop efficient test strategies to maximize coverage within the available time and budget.
-
Design for Manufacturability (DFM): Prototype PCBs should be designed with manufacturability in mind to ensure smooth transition to mass production. Engineers need to consider factors such as component placement, trace routing, and assembly processes to minimize potential manufacturing challenges.
-
Regulatory Compliance: Depending on the target market and application, prototype PCBs may need to comply with various regulatory standards, such as electromagnetic compatibility (EMC), safety, and environmental regulations. Ensuring compliance during the prototype stage helps avoid delays and additional costs later in the development process.
Best Practices for Successful Prototype PCB Assembly
To ensure successful prototype PCB assembly and maximize its benefits, consider the following best practices:
-
Thorough Design Review: Conduct a comprehensive design review before starting the prototype assembly process. Verify the schematic, PCB layout, and component selections to catch any potential issues early.
-
Clear Documentation: Maintain clear and detailed documentation, including the schematic, PCB layout files, BOM, and assembly instructions. This ensures that all stakeholders have access to the necessary information and reduces the risk of errors during assembly.
-
Component Management: Implement a robust component management system to track component availability, lead times, and inventory levels. Establish reliable supplier relationships to ensure timely delivery of components for prototype assembly.
-
Skilled Assembly Team: Invest in training and development of the PCB assembly team to ensure they have the necessary skills and knowledge to handle prototype assembly. Encourage attention to detail, following best practices, and adherence to industry standards.
-
Comprehensive Testing Strategy: Develop a comprehensive testing strategy that covers all critical aspects of the prototype PCB. Define clear test cases, specify test equipment and procedures, and allocate sufficient time for thorough testing and debugging.
-
Design for Manufacturability (DFM) Considerations: Incorporate DFM principles into the PCB design process. Follow guidelines for component placement, trace routing, and clearances to ensure the prototype can be easily transitioned to mass production.
-
Iteration and Refinement: Embrace an iterative approach to prototype PCB assembly. Be prepared to make multiple iterations based on testing results and feedback. Continuously refine the design, component selections, and assembly processes to optimize performance and manufacturability.
-
Collaboration and Communication: Foster effective collaboration and communication among all stakeholders involved in the prototype PCB assembly process, including design engineers, assembly technicians, component suppliers, and testing teams. Regular meetings, progress updates, and clear communication channels help ensure everyone is aligned and working towards common goals.
-
Documentation and Version Control: Maintain comprehensive documentation throughout the prototype PCB assembly process, including design files, assembly instructions, test reports, and any modifications made. Implement a robust version control system to track changes and ensure everyone is working with the latest version of the design.
-
Continuous Improvement: Continuously assess and improve the prototype PCB assembly process based on lessons learned and feedback from stakeholders. Identify areas for optimization, streamline workflows, and adopt new technologies or techniques that can enhance efficiency and quality.
Frequently Asked Questions (FAQ)
-
What is the difference between prototype PCB assembly and mass production assembly?
Prototype PCB assembly focuses on assembling a small number of boards for testing and validation purposes, often involving manual assembly processes. Mass production assembly, on the other hand, involves assembling a large volume of boards using automated processes and optimized manufacturing techniques. -
How long does prototype PCB assembly typically take?
The duration of prototype PCB assembly varies depending on the complexity of the design, component availability, and assembly methods used. Simple prototypes can be assembled within a few days, while more complex designs may take several weeks. Effective planning, clear communication, and efficient workflows can help streamline the assembly process. -
What are the common challenges faced during prototype PCB assembly?
Common challenges in prototype PCB assembly include component availability, manual assembly errors, limited test coverage, design for manufacturability issues, and regulatory compliance requirements. Addressing these challenges requires careful planning, skilled technicians, comprehensive testing strategies, and adherence to best practices. -
How can I ensure the quality of my prototype PCB assembly?
To ensure the quality of prototype PCB assembly, follow best practices such as conducting thorough design reviews, maintaining clear documentation, investing in skilled assembly teams, implementing comprehensive testing strategies, and incorporating design for manufacturability principles. Continuously monitor and improve the assembly process based on feedback and lessons learned. -
What should I consider when selecting a prototype PCB assembly service provider?
When selecting a prototype PCB assembly service provider, consider factors such as their experience and expertise in handling similar projects, the range of services they offer (e.g., PCB fabrication, component sourcing, assembly, testing), their quality control processes, turnaround time, and customer support. Look for providers with a proven track record of delivering high-quality prototypes and who can provide valuable guidance and support throughout the assembly process.
Conclusion
Prototype PCB assembly is a critical step in the product development process, enabling engineers to validate their designs, evaluate performance, and optimize for mass production. By following best practices, addressing challenges, and leveraging the expertise of skilled assembly teams, companies can successfully navigate the prototype PCB assembly process and bring their electronic products to market faster and with higher quality.
Investing in prototype PCB assembly pays off in the long run by reducing design risks, accelerating time-to-market, and ensuring a smooth transition to mass production. As technology advances and consumer demands evolve, the ability to quickly and efficiently assemble prototype PCBs will continue to be a key differentiator for companies in the electronics industry.
Aspect | Prototype PCB Assembly | Mass Production Assembly |
---|---|---|
Volume | Low (a few units) | High (hundreds or thousands) |
Assembly Methods | Often manual | Highly automated |
Component Sourcing | Smaller quantities | Bulk quantities |
Testing and Validation | Focused on functionality and performance | Focused on process control and quality assurance |
Design Optimization | Iterative refinement based on testing results | Optimized for manufacturability and cost |
Turnaround Time | Days to weeks | Weeks to months |
Cost per Unit | Higher | Lower |
Purpose | Design validation and performance evaluation | Volume production for commercial release |
Table 1: Comparison between Prototype PCB Assembly and Mass Production Assembly
By embracing the power of prototype PCB assembly and following industry best practices, companies can drive innovation, mitigate risks, and deliver high-quality electronic products that meet the evolving needs of their customers.