Why is PCBA Inspection Important?
PCBA inspection plays a vital role in ensuring the reliability and functionality of electronic devices. Here are some key reasons why PCBA inspection is essential:
-
Quality Assurance: PCBA inspection helps identify and eliminate defects or irregularities in the assembly process, ensuring that the final product meets the desired quality standards.
-
Cost Reduction: By detecting defects early in the manufacturing process, PCBA inspection helps reduce the cost associated with rework, repairs, and product returns.
-
Reliability: Thorough PCBA inspection ensures that the assembled boards are reliable and perform as intended, minimizing the risk of device failures and customer dissatisfaction.
-
Compliance: PCBA inspection helps manufacturers comply with industry standards and regulations, such as IPC (Association Connecting Electronics Industries) standards, ensuring consistency and adherence to best practices.
Methods of PCBA Inspection
There are several methods used for PCBA inspection, each with its own advantages and limitations. Let’s explore some of the most common methods:
Visual Inspection
Visual inspection is the most basic and commonly used method for PCBA inspection. It involves visually examining the assembled boards for defects such as:
- Solder bridges or shorts
- Misaligned or missing components
- Incorrect component orientation
- Damaged or lifted pads
- Flux residue or contamination
Visual inspection can be performed manually by trained operators using magnifying lenses or microscopes. However, this method is time-consuming and subject to human error.
Automated Optical Inspection (AOI)
Automated Optical Inspection (AOI) is a more advanced method that uses high-resolution cameras and image processing algorithms to inspect PCBAs. AOI systems can detect a wide range of defects, including:
- Solder defects (bridges, insufficient solder, tombstoning)
- Component placement errors
- Missing or incorrect components
- Polarity issues
- Marking or labeling errors
AOI systems can inspect PCBAs at high speeds and with high accuracy, making them suitable for high-volume production. However, they may have limitations in detecting certain types of defects, such as hidden solder joints or under-component defects.
X-Ray Inspection
X-ray inspection is a non-destructive method that uses X-rays to examine the internal structure of PCBAs. It is particularly useful for inspecting:
- Ball Grid Array (BGA) and Quad Flat Package (QFP) solder joints
- Voids or cracks in solder joints
- Misaligned or missing components
- Counterfeit components
X-ray inspection systems can provide detailed images of the internal structure of PCBAs, allowing for the detection of defects that may not be visible through other methods. However, X-ray inspection equipment can be expensive and may require specialized training to operate.
In-Circuit Testing (ICT)
In-Circuit Testing (ICT) is a method that involves using a bed-of-nails fixture to make electrical contact with specific points on the PCBA. ICT systems can perform various tests, including:
- Continuity testing
- Resistance measurement
- Capacitance and inductance measurement
- Diode and transistor testing
ICT is effective in detecting manufacturing defects and ensuring the electrical functionality of the PCBA. However, it requires the development of specific test fixtures for each PCBA design, which can be time-consuming and costly.
Functional Testing
Functional testing involves testing the PCBA under actual operating conditions to ensure it performs as intended. This method can detect defects that may not be apparent during other inspection methods, such as:
- Incorrect component values
- Timing issues
- Signal integrity problems
- Firmware or software bugs
Functional testing can be performed using specialized test equipment or by integrating the PCBA into the final product for testing. It is an essential step in ensuring the overall quality and reliability of the electronic device.
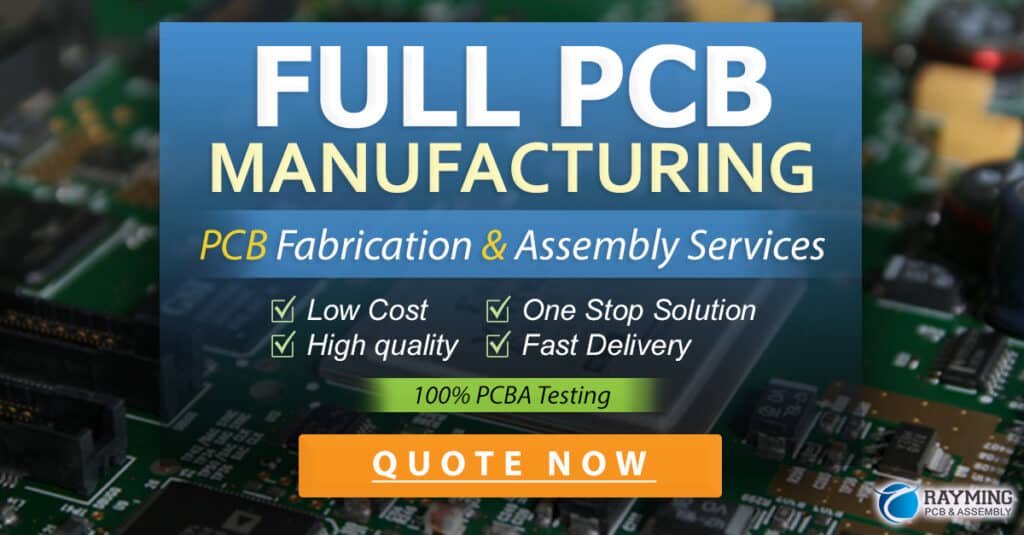
Best Practices for PCBA Inspection
To ensure effective and efficient PCBA inspection, manufacturers should follow these best practices:
-
Establish Inspection Criteria: Define clear and measurable inspection criteria based on industry standards, customer requirements, and product specifications.
-
Implement Multiple Inspection Methods: Use a combination of inspection methods, such as visual inspection, AOI, X-ray, ICT, and functional testing, to detect a wide range of defects and ensure comprehensive coverage.
-
Maintain Proper Documentation: Document inspection procedures, criteria, and results to ensure traceability and facilitate continuous improvement.
-
Train and Certify Operators: Provide adequate training and certification for inspection operators to ensure consistency and adherence to best practices.
-
Regularly Calibrate and Maintain Equipment: Ensure that inspection equipment is regularly calibrated and maintained to ensure accurate and reliable results.
-
Implement Statistical Process Control (SPC): Use SPC techniques to monitor and control the inspection process, identifying trends and taking corrective actions as needed.
-
Conduct Root Cause Analysis: Investigate the root causes of defects identified during inspection and implement corrective and preventive actions to eliminate them.
PCBA Inspection Standards and Guidelines
Several industry standards and guidelines provide a framework for PCBA inspection and quality assurance. Some of the most widely recognized standards include:
Standard | Description |
---|---|
IPC-A-610 | Acceptability of Electronic Assemblies |
IPC-6012 | Qualification and Performance Specification for Rigid Printed Boards |
IPC-J-STD-001 | Requirements for Soldered Electrical and Electronic Assemblies |
IPC-7711/7721 | Rework, Modification, and Repair of Electronic Assemblies |
These standards provide detailed guidelines on workmanship, acceptability criteria, and inspection methods, helping manufacturers ensure consistency and quality in their PCBA inspection processes.
Frequently Asked Questions (FAQ)
-
What are the most common defects found during PCBA inspection?
The most common defects found during PCBA inspection include solder defects (bridges, insufficient solder, tombstoning), component placement errors, missing or incorrect components, and damaged or lifted pads. -
How does AOI differ from visual inspection?
AOI uses high-resolution cameras and image processing algorithms to inspect PCBAs automatically, while visual inspection relies on human operators to visually examine the boards. AOI is faster, more accurate, and less prone to human error compared to visual inspection. -
What are the advantages of X-ray inspection?
X-ray inspection allows for the examination of the internal structure of PCBAs, making it particularly useful for inspecting BGAs, QFPs, and hidden solder joints. It can detect defects such as voids, cracks, and counterfeit components that may not be visible through other methods. -
How often should PCBA inspection equipment be calibrated?
The frequency of calibration depends on the specific equipment and manufacturer’s recommendations. However, it is generally recommended to calibrate inspection equipment at least annually or as per the manufacturer’s guidelines to ensure accurate and reliable results. -
What is the role of Statistical Process Control (SPC) in PCBA inspection?
SPC is a quality control technique that involves monitoring and controlling the inspection process using statistical methods. It helps identify trends, variations, and out-of-control conditions, allowing manufacturers to take corrective actions and continuously improve their inspection processes.
Conclusion
PCBA inspection is a critical process in the manufacturing of electronic devices, ensuring the quality, reliability, and functionality of the assembled boards. By employing various inspection methods, such as visual inspection, AOI, X-ray, ICT, and functional testing, manufacturers can detect and eliminate a wide range of defects, reducing costs and improving customer satisfaction.
To achieve effective PCBA inspection, manufacturers should establish clear inspection criteria, implement multiple inspection methods, maintain proper documentation, train and certify operators, regularly calibrate and maintain equipment, implement SPC techniques, and conduct root cause analysis.
By adhering to industry standards and best practices, manufacturers can ensure consistent and high-quality PCBA inspection processes, ultimately delivering reliable and high-performing electronic devices to their customers.