Introduction to SMT PCB Assembly
Surface Mount Technology (SMT) is a modern method of assembling printed circuit boards (PCBs) that has revolutionized the electronics manufacturing industry. SMT PCB assembly involves placing and soldering electronic components directly onto the surface of a PCB, as opposed to the traditional through-hole method where components are inserted into drilled holes and soldered on the opposite side of the board.
SMT PCB assembly offers numerous advantages over through-hole assembly, including:
- Smaller component sizes
- Higher component density
- Faster assembly process
- Lower production costs
- Improved reliability and performance
In this comprehensive article, we will delve into the details of SMT PCB assembly, covering its history, the assembly process, equipment used, benefits, and challenges.
The History of SMT PCB Assembly
The concept of surface mount technology dates back to the 1960s when IBM introduced the first surface mount package for their System/360 mainframe computer. However, it wasn’t until the 1980s that SMT gained widespread adoption in the electronics industry.
The transition from through-hole to SMT assembly was driven by several factors:
- The increasing demand for smaller, more compact electronic devices
- The need for faster assembly processes to meet growing production volumes
- The desire to reduce manufacturing costs
As SMT technology advanced, component sizes continued to shrink, allowing for even higher component densities on PCBs. Today, SMT is the primary method used for assembling the vast majority of electronic devices, from smartphones and laptops to medical devices and automotive electronics.
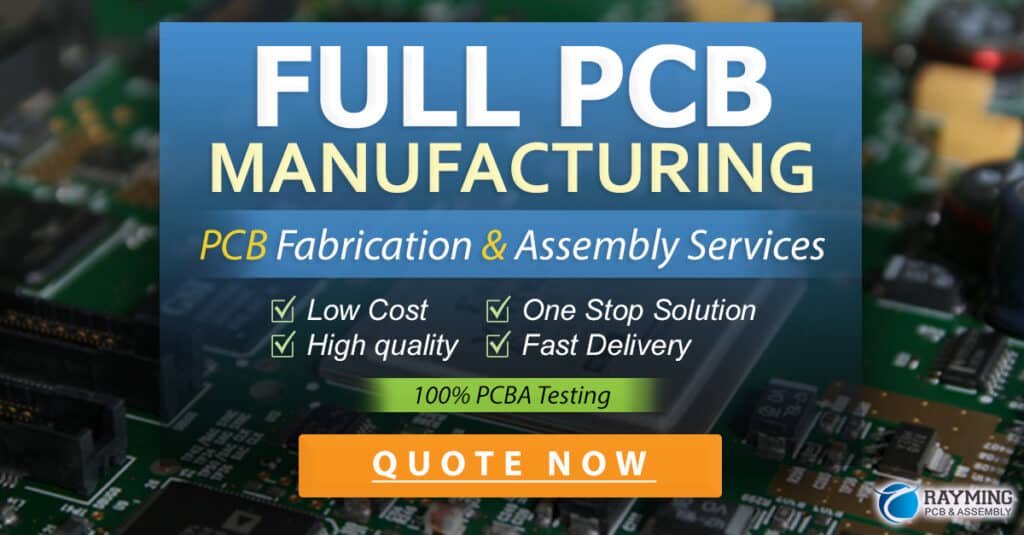
The SMT PCB Assembly Process
The SMT PCB assembly process consists of several key steps:
- Solder Paste Application
- Component Placement
- Reflow Soldering
- Inspection and Testing
1. Solder Paste Application
The first step in the SMT PCB assembly process is applying solder paste to the PCB. Solder paste is a mixture of tiny solder particles suspended in a flux medium. The paste is applied to the PCB using a stencil printing process, where a thin metal stencil with apertures corresponding to the component pads is placed over the PCB. Solder paste is then spread across the stencil, filling the apertures and depositing the paste onto the pads.
2. Component Placement
Once the solder paste has been applied, the next step is to place the surface mount components onto the PCB. This is typically done using a pick-and-place machine, which uses vacuum nozzles to pick up components from tape reels or trays and place them precisely onto the solder paste-covered pads.
Modern pick-and-place machines are highly automated and can place thousands of components per hour with incredible accuracy. They are equipped with vision systems that allow them to locate and align components correctly, even when dealing with extremely small or oddly shaped parts.
3. Reflow Soldering
After the components have been placed, the PCB is ready for reflow soldering. In this process, the PCB is passed through a reflow oven, which heats the board to a specific temperature profile. As the temperature increases, the solder paste melts, forming a metallurgical bond between the component leads and the PCB pads.
Reflow soldering is a carefully controlled process, with the temperature profile being critical to ensuring a reliable solder joint. The profile typically consists of several stages:
- Preheat: The PCB is gradually heated to activate the flux and remove any moisture.
- Soak: The temperature is maintained to allow the components and PCB to reach a uniform temperature.
- Reflow: The temperature is increased to above the melting point of the solder, allowing it to flow and form a connection between the component leads and PCB pads.
- Cooling: The PCB is cooled, allowing the solder to solidify and form a strong, reliable joint.
4. Inspection and Testing
The final step in the SMT PCB assembly process is inspection and testing. Visual inspection is performed to check for any obvious defects, such as misaligned components, solder bridges, or insufficient solder joints. Automated optical inspection (AOI) systems are often used to quickly scan the PCB for defects, comparing the assembled board to a known good reference.
In addition to visual inspection, functional testing may also be performed to ensure that the assembled PCB operates as intended. This can include in-circuit testing (ICT), where a bed of nails fixture is used to test individual components and circuits, or functional testing, where the complete PCB is tested in its final operating configuration.
Equipment Used in SMT PCB Assembly
The success of SMT PCB assembly relies on a range of specialized equipment:
- Stencil Printer: Used to apply solder paste to the PCB pads.
- Pick-and-Place Machine: Automatically places components onto the PCB with high speed and accuracy.
- Reflow Oven: Heats the PCB to melt the solder paste and form a connection between components and pads.
- Inspection Systems: Automated optical inspection (AOI) and X-ray inspection systems are used to detect defects and ensure the quality of the assembled PCB.
Equipment | Function |
---|---|
Stencil Printer | Applies solder paste to PCB pads |
Pick-and-Place Machine | Places components onto the PCB |
Reflow Oven | Melts solder paste to form connections |
Inspection Systems | Detects defects and ensures quality |
Benefits of SMT PCB Assembly
SMT PCB assembly offers numerous benefits over traditional through-hole assembly:
- Smaller Component Sizes: SMT components are much smaller than their through-hole counterparts, allowing for more compact PCB designs.
- Higher Component Density: With smaller components, more parts can be placed on a single PCB, enabling more complex and powerful electronic devices.
- Faster Assembly Process: Pick-and-place machines and reflow soldering allow for much faster assembly times compared to manual through-hole assembly.
- Lower Production Costs: The automated nature of SMT assembly and the ability to process multiple PCBs simultaneously results in lower overall production costs.
- Improved Reliability and Performance: SMT components have shorter lead lengths, which reduces parasitic inductance and capacitance, leading to improved signal integrity and overall performance.
Challenges in SMT PCB Assembly
Despite its many advantages, SMT PCB assembly also presents some challenges:
- Component Miniaturization: As components continue to shrink in size, the placement and soldering process becomes more challenging, requiring more precise equipment and process control.
- Thermal Management: With higher component densities, thermal management becomes a concern, as heat dissipation can be more difficult in compact PCB designs.
- Rework and Repair: Removing and replacing SMT components can be more difficult than through-hole components, often requiring specialized equipment and skills.
- Moisture Sensitivity: Some SMT components are sensitive to moisture and require careful handling and storage to prevent damage during the reflow soldering process.
Frequently Asked Questions (FAQ)
1. What is the difference between SMT and through-hole assembly?
SMT components are placed and soldered directly onto the surface of the PCB, while through-hole components are inserted into drilled holes and soldered on the opposite side of the board.
2. Can SMT and through-hole components be used on the same PCB?
Yes, it is possible to use both SMT and through-hole components on the same PCB. This is known as a mixed assembly process.
3. What are the most common SMT component packages?
Some of the most common SMT component packages include:
– Chip resistors and capacitors
– Small Outline Integrated Circuit (SOIC)
– Quad Flat Pack (QFP)
– Ball Grid Array (BGA)
4. How does the size of an SMT component affect the assembly process?
Smaller SMT components require more precise placement and soldering equipment, as well as tighter process control to ensure reliable assembly.
5. What is the role of flux in the SMT assembly process?
Flux serves several important functions in SMT assembly:
– Removing oxides from the metal surfaces to promote solder wetting
– Protecting the metal surfaces from oxidation during the soldering process
– Improving the flow and spread of molten solder to create reliable joints
Conclusion
SMT PCB assembly has revolutionized the electronics manufacturing industry, enabling the production of smaller, more complex, and more reliable electronic devices. By placing and soldering components directly onto the surface of the PCB, SMT assembly offers numerous advantages over traditional through-hole methods, including smaller component sizes, higher component density, faster assembly processes, lower production costs, and improved performance.
As electronic devices continue to evolve and become more sophisticated, SMT technology will undoubtedly play a crucial role in meeting the demands of the industry. While challenges such as component miniaturization and thermal management remain, ongoing advancements in equipment, materials, and processes will help manufacturers overcome these hurdles and push the boundaries of what is possible in electronic packaging and assembly.