Introduction to PCB Panels
A PCB panel, also known as a printed circuit board panel, is a large board that contains multiple identical printed circuit boards (PCBs) arranged in a specific pattern. The purpose of using PCB panels is to maximize production efficiency and reduce manufacturing costs by producing multiple PCBs simultaneously.
What are PCBs?
Before diving into the details of PCB panels, it’s essential to understand what PCBs are. PCBs are the backbone of modern electronic devices, providing mechanical support and electrical connections for various components such as resistors, capacitors, and integrated circuits. They are made of a non-conductive substrate, typically fiberglass or plastic, with conductive copper traces etched onto the surface to form the desired circuit pattern.
The Need for PCB Panels
As the demand for electronic devices continues to grow, manufacturers are constantly seeking ways to optimize their production processes. One of the most effective methods is to use PCB panels, which allow for the simultaneous fabrication of multiple PCBs in a single production run. This approach offers several advantages, including:
- Reduced production time
- Lower manufacturing costs
- Improved consistency and quality control
- Easier handling and transportation of PCBs
PCB Panel Design Considerations
When designing a PCB panel, several factors must be taken into account to ensure optimal performance and manufacturability. These considerations include:
Panel Size and Layout
The size and layout of the PCB panel depend on the dimensions of the individual PCBs and the number of PCBs to be produced. The panel size should be compatible with the manufacturing equipment and allow for efficient utilization of the available space. The layout should also consider the placement of tooling holes, fiducial marks, and other necessary features.
Spacing and Clearance
Proper spacing and clearance between individual PCBs on the panel are crucial to prevent short circuits and ensure smooth separation of the boards after fabrication. The spacing should account for the width of the cutting tools used to separate the PCBs and any potential warping or shrinkage of the substrate during the manufacturing process.
Panelization Methods
There are several methods for arranging PCBs on a panel, each with its own advantages and limitations. Some common panelization methods include:
- Tab-routed panels: PCBs are connected by thin tabs that are easily broken off after fabrication.
- Scored panels: PCBs are separated by pre-cut grooves, allowing for easy separation.
- V-cut panels: PCBs are connected by V-shaped grooves, which provide a clean break when separated.
- Frame-based panels: PCBs are placed in a frame with breakaway tabs, ensuring stability during manufacturing.
The choice of panelization method depends on factors such as the PCB design, material, and the intended application.
Tooling Holes and Fiducial Marks
Tooling holes and fiducial marks are essential features in PCB panel design. Tooling holes are used to secure the panel during the manufacturing process, ensuring accurate positioning and preventing movement. Fiducial marks, on the other hand, serve as reference points for automated assembly equipment, enabling precise component placement on the individual PCBs.
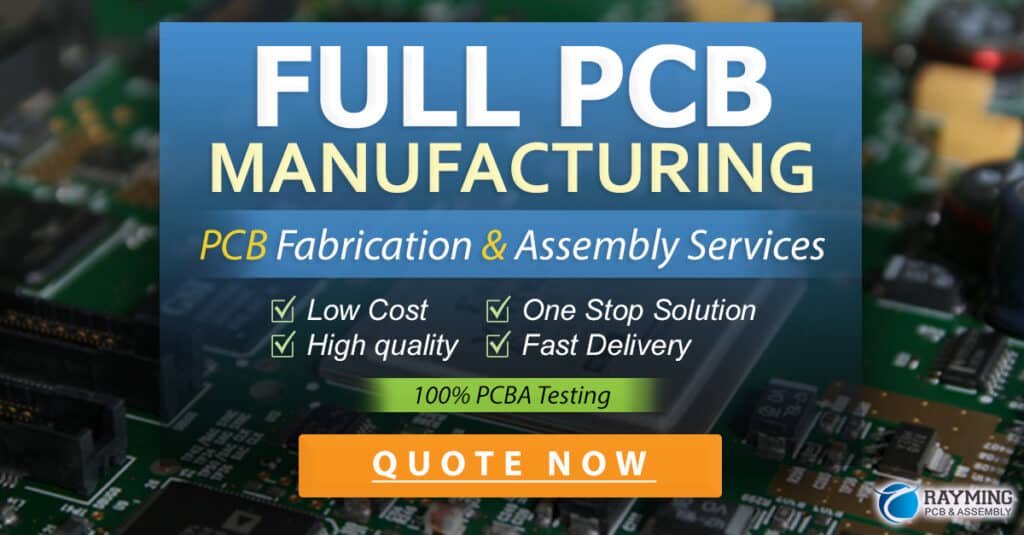
PCB Panel Fabrication Process
The PCB panel fabrication process involves several steps, each of which contributes to the final quality and functionality of the PCBs. The main stages of PCB panel fabrication are:
Substrate Preparation
The fabrication process begins with the preparation of the substrate material, usually a laminate of fiberglass and epoxy resin. The substrate is cut to the desired panel size and cleaned to remove any contaminants that could affect the subsequent steps.
Copper Deposition
A thin layer of copper is deposited onto the substrate using techniques such as electroless plating or electrodeposition. This layer will form the conductive traces of the PCBs.
Patterning and Etching
The desired circuit pattern is transferred onto the copper layer using a photolithographic process. A photoresist material is applied to the copper surface and exposed to UV light through a photomask containing the circuit design. The exposed areas of the photoresist are then removed, leaving the desired pattern. Finally, the unwanted copper is etched away using a chemical solution, revealing the final circuit layout.
Drilling and Plating
Holes are drilled through the PCB panel at the locations specified in the design. These holes are used for mounting components and creating electrical connections between layers in multi-layer PCBs. The holes are then plated with copper to ensure reliable electrical conductivity.
Solder Mask Application
A solder mask, typically a green or other colored polymer, is applied to the PCB panel. This mask covers the areas of the board that should not be exposed to solder during the assembly process, protecting the copper traces and preventing short circuits.
Surface Finishing
To enhance the solderability and protect the exposed copper, a surface finish is applied to the PCB panel. Common surface finishes include:
- Hot Air Solder Leveling (HASL)
- Immersion Silver (IAg)
- Immersion Tin (ISn)
- Electroless Nickel Immersion Gold (ENIG)
- Organic Solderability Preservative (OSP)
The choice of surface finish depends on the specific requirements of the PCB, such as the intended environment, shelf life, and compatibility with the assembly process.
Silkscreen Printing
A silkscreen layer is printed onto the PCB panel to provide text, logos, and other identifying markings. This layer helps with the assembly process and provides a professional appearance to the final product.
Profiling and Separating
Once the fabrication process is complete, the individual PCBs are separated from the panel using the chosen panelization method. This step, also known as depaneling or singulation, requires precision to ensure that the PCBs are not damaged during the separation process.
Advantages of Using PCB Panels
Using PCB panels in the manufacturing process offers several advantages, including:
-
Increased Production Efficiency: By producing multiple PCBs simultaneously, manufacturers can significantly reduce the time and resources required for fabrication. This leads to faster turnaround times and higher output volumes.
-
Cost Reduction: PCB panels allow for the sharing of manufacturing costs across multiple PCBs, resulting in lower per-unit costs. This is particularly beneficial for high-volume production runs.
-
Improved Quality Control: Producing PCBs in panels enables better control over the fabrication process, as the panels can be inspected and tested as a whole before separation. This helps identify and address any issues early on, reducing the risk of defective PCBs reaching the end-user.
-
Easier Handling and Transportation: PCB panels are easier to handle and transport compared to individual PCBs. They can be stacked and packaged more efficiently, reducing the risk of damage during shipping and storage.
Challenges and Considerations
While PCB panels offer numerous benefits, there are also some challenges and considerations to keep in mind:
-
Design Complexity: Designing a PCB panel requires careful planning and consideration of factors such as spacing, clearance, and panelization methods. Designers must ensure that the panel layout is optimized for manufacturability and that the individual PCBs will function as intended after separation.
-
Material Selection: The choice of substrate material and surface finish can impact the performance and reliability of the PCBs. Manufacturers must select materials that are compatible with the intended application and meet the required standards and specifications.
-
Depaneling Process: Separating the individual PCBs from the panel requires precision and care to avoid damaging the boards. The choice of depaneling method, such as manual breaking, routing, or laser cutting, depends on factors such as the PCB design, material, and volume.
-
Tooling and Equipment: Producing PCB panels requires specialized tooling and equipment, such as panel-sized etching and drilling machines. Manufacturers must invest in the necessary infrastructure to support panel-based production, which can be a significant upfront cost.
Frequently Asked Questions (FAQ)
-
What is the difference between a PCB and a PCB panel?
A PCB is an individual printed circuit board, while a PCB panel is a larger board containing multiple identical PCBs arranged in a specific pattern. PCB panels are used to maximize production efficiency and reduce manufacturing costs. -
What are the common panelization methods used for PCB panels?
The most common panelization methods include tab-routed panels, scored panels, V-cut panels, and frame-based panels. Each method has its own advantages and limitations, and the choice depends on factors such as the PCB design, material, and intended application. -
Why are tooling holes and fiducial marks important in PCB panel design?
Tooling holes are used to secure the panel during the manufacturing process, ensuring accurate positioning and preventing movement. Fiducial marks serve as reference points for automated assembly equipment, enabling precise component placement on the individual PCBs. -
What are the main stages of the PCB panel fabrication process?
The main stages of PCB panel fabrication include substrate preparation, copper deposition, patterning and etching, drilling and plating, solder mask application, surface finishing, silkscreen printing, and profiling and separating. -
What are the advantages of using PCB panels in the manufacturing process?
The advantages of using PCB panels include increased production efficiency, cost reduction, improved quality control, and easier handling and transportation. By producing multiple PCBs simultaneously, manufacturers can optimize their production processes and deliver high-quality products at a lower cost.
Conclusion
PCB panels play a crucial role in the electronics manufacturing industry, enabling the efficient and cost-effective production of printed circuit boards. By understanding the design considerations, fabrication process, and advantages of using PCB panels, manufacturers can optimize their production workflows and deliver high-quality PCBs that meet the ever-growing demands of the market.
As technology continues to advance, the importance of PCB panels in the manufacturing process will only continue to grow. By staying up-to-date with the latest techniques and best practices in PCB panel design and fabrication, manufacturers can remain competitive and deliver innovative solutions to their customers.