Introduction to OSP PCB
OSP, which stands for Organic Solderability Preservative, is a surface finish commonly used in printed circuit board (PCB) manufacturing. It is a clear, organic coating applied to the copper pads and through-holes of a PCB to protect them from oxidation and enhance solderability. OSP PCB has gained popularity in the electronics industry due to its cost-effectiveness, environmental friendliness, and excellent soldering performance.
What is a PCB Surface Finish?
A PCB surface finish is a protective layer applied to the exposed copper surfaces of a printed circuit board. Its primary functions are to:
- Prevent oxidation of the copper surfaces
- Enhance solderability during the assembly process
- Improve the shelf life of the PCB
- Provide a smooth, uniform surface for better electrical conductivity
There are several types of surface finishes used in PCB manufacturing, including:
- Hot Air Solder Leveling (HASL)
- Electroless Nickel Immersion Gold (ENIG)
- Immersion Silver (IAg)
- Immersion Tin (ISn)
- Organic Solderability Preservative (OSP)
Each surface finish has its advantages and disadvantages, and the choice depends on factors such as cost, application requirements, and environmental considerations.
How Does OSP PCB Work?
OSP is a clear, organic compound that is applied to the copper surfaces of a PCB through a simple dipping process. The OSP coating forms a thin, protective layer over the copper, preventing oxidation and ensuring excellent solderability.
The OSP Application Process
The OSP application process typically involves the following steps:
- Cleaning: The PCB is thoroughly cleaned to remove any contaminants or residues from the copper surfaces.
- Microetching: A mild etching solution is used to remove any remaining oxides and create a uniform surface for better OSP adhesion.
- OSP Application: The PCB is dipped into an OSP solution, which forms a thin, protective layer on the copper surfaces.
- Drying: The PCB is dried using hot air or infrared heating to evaporate any remaining solvents and ensure a uniform OSP coating.
The entire process is relatively simple and cost-effective compared to other surface finishes like ENIG or HASL.
Advantages of OSP PCB
OSP PCB offers several advantages over other surface finishes:
- Cost-effective: OSP is one of the most economical surface finishes available, making it an attractive option for budget-conscious projects.
- Environmentally friendly: OSP is a lead-free and RoHS-compliant surface finish, making it an eco-friendly choice.
- Excellent solderability: OSP provides excellent wetting and soldering performance, ensuring reliable connections during the assembly process.
- Flat surface: OSP creates a flat, uniform surface, which is ideal for fine-pitch components and high-density designs.
- Good shelf life: When stored properly, OSP PCBs can maintain their solderability for up to 12 months.
Disadvantages of OSP PCB
Despite its many benefits, OSP PCB also has some limitations:
- Limited shelf life: Compared to other surface finishes like ENIG, OSP has a shorter shelf life, typically up to 12 months when stored properly.
- Sensitivity to handling: OSP-coated PCBs are more susceptible to contamination from handling, requiring extra care during storage and assembly.
- Not suitable for multiple reflow cycles: OSP may degrade after multiple reflow cycles, making it less suitable for applications that require rework or multiple assembly stages.
- Incompatibility with some soldering methods: OSP may not be compatible with certain soldering methods, such as wave soldering, due to its organic nature.
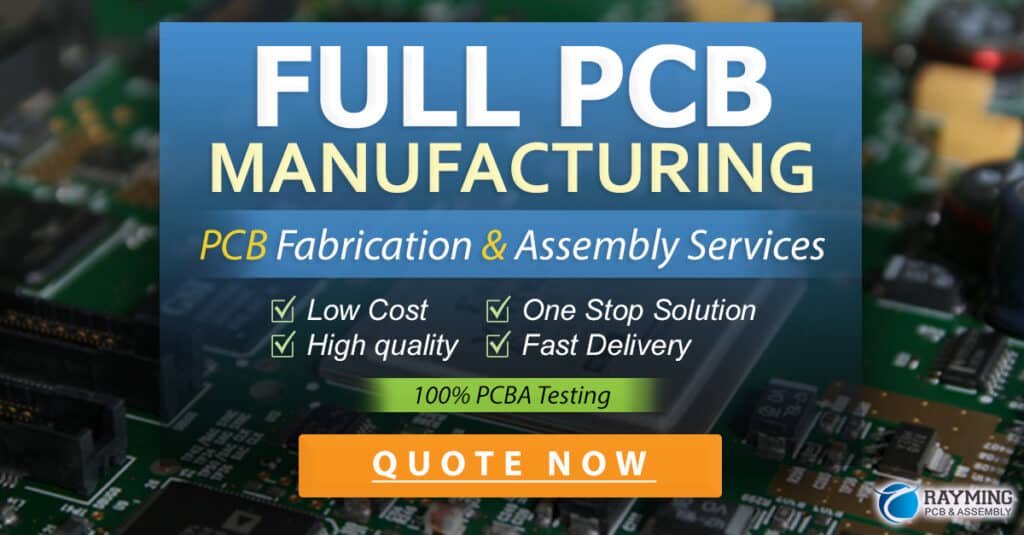
OSP PCB vs. Other Surface Finishes
To better understand the benefits and limitations of OSP PCB, it is essential to compare it with other common surface finishes.
OSP vs. HASL
Hot Air Solder Leveling (HASL) is a traditional surface finish that involves dipping the PCB in molten solder and then using hot air to level the surface. While HASL is cost-effective and provides good solderability, it has some drawbacks compared to OSP:
Feature | OSP | HASL |
---|---|---|
Surface Flatness | Flat, uniform surface | Uneven surface due to solder buildup |
Fine-Pitch Compatibility | Suitable for fine-pitch components | Limited due to uneven surface |
Environmental Impact | Lead-free and RoHS-compliant | May contain lead (Lead-free HASL available) |
Shelf Life | Up to 12 months | Longer shelf life due to solder protection |
OSP vs. ENIG
Electroless Nickel Immersion Gold (ENIG) is a high-end surface finish that offers excellent solderability, long shelf life, and compatibility with various soldering methods. However, it comes at a higher cost compared to OSP:
Feature | OSP | ENIG |
---|---|---|
Cost | Low cost | High cost |
Shelf Life | Up to 12 months | Longer shelf life (12+ months) |
Multiple Reflow Cycles | Limited compatibility | Suitable for multiple reflow cycles |
Solder Joint Appearance | Matte finish | Bright, shiny finish |
Aluminum Wire Bonding | Not recommended | Suitable for aluminum wire bonding |
OSP vs. Immersion Silver and Tin
Immersion Silver (IAg) and Immersion Tin (ISn) are other lead-free surface finishes that offer good solderability and flat surfaces. However, they have some limitations compared to OSP:
Feature | OSP | IAg | ISn |
---|---|---|---|
Cost | Low cost | Moderate cost | Moderate cost |
Shelf Life | Up to 12 months | Limited shelf life (6-12 months) | Limited shelf life (6-12 months) |
Solder Joint Appearance | Matte finish | Matte finish | Matte finish |
Copper Wire Bonding | Not recommended | Suitable for copper wire bonding | Not recommended |
Whisker Growth | No whisker growth | No whisker growth | Potential for whisker growth |
Designing for OSP PCB
When designing a PCB for OSP surface finish, there are several guidelines to follow to ensure optimal performance and reliability:
- Pad and Via Design: Ensure that the pad and via sizes are appropriate for OSP finish. Avoid overly small or large pads, as they may lead to solderability issues.
- Solder Mask Design: Use a solder mask to protect the OSP-coated copper from contamination and mechanical damage. Ensure adequate solder mask clearance around pads and vias.
- Copper Thickness: Maintain a minimum copper thickness of 1 oz (35 µm) to ensure good OSP adhesion and solderability.
- Solderable Area: Maximize the solderable area on the pads and vias to enhance solderability and reliability of the solder joints.
- Handling and Storage: Implement proper handling and storage procedures to minimize contamination and ensure the longevity of the OSP finish.
By following these design guidelines, you can optimize your PCB design for OSP surface finish and achieve reliable, high-quality results.
FAQs
-
Q: What is the shelf life of OSP PCB?
A: When stored properly, OSP PCBs can maintain their solderability for up to 12 months. -
Q: Is OSP suitable for multiple reflow cycles?
A: OSP may degrade after multiple reflow cycles, making it less suitable for applications that require rework or multiple assembly stages. -
Q: Can OSP be used with aluminum wire bonding?
A: OSP is not recommended for aluminum wire bonding. ENIG is a more suitable surface finish for this application. -
Q: Is OSP compatible with all soldering methods?
A: OSP may not be compatible with certain soldering methods, such as wave soldering, due to its organic nature. It is best suited for reflow soldering. -
Q: How does OSP compare to HASL in terms of cost?
A: OSP is generally more cost-effective than HASL, as it involves a simpler application process and does not require the use of molten solder.
Conclusion
OSP PCB is a popular and cost-effective surface finish that offers excellent solderability, environmental friendliness, and compatibility with fine-pitch components. By understanding the advantages, limitations, and design considerations of OSP, you can make an informed decision when choosing a surface finish for your PCB project.
While OSP may not be suitable for every application, it remains a reliable and economical choice for many electronics manufacturers. As with any surface finish, proper handling, storage, and assembly procedures are essential to ensure the best possible results.