Introduction to RF PCBs
A Radio Frequency Printed Circuit Board (RF PCB) is a specialized type of PCB designed to work with high-frequency signals in the radio frequency range. These PCBs are crucial components in various electronic devices that transmit or receive wireless signals, such as smartphones, tablets, Wi-Fi routers, and GPS systems.
RF PCBs are engineered to minimize signal loss, interference, and distortion, ensuring optimal performance in high-frequency applications. They require careful design considerations and manufacturing techniques to achieve the desired functionality and reliability.
Key Characteristics of RF PCBs
1. High-Frequency Operation
RF PCBs are designed to operate at high frequencies, typically in the range of 100 MHz to several GHz. At these frequencies, the behavior of electrical signals differs significantly from lower frequencies, requiring special design considerations.
2. Controlled Impedance
Maintaining a consistent impedance throughout the RF PCB is crucial for minimizing signal reflections and ensuring proper signal propagation. Controlled impedance is achieved through careful selection of materials, trace width and thickness, and dielectric properties.
3. Low Loss Materials
RF PCBs often employ low-loss substrates, such as PTFE (Polytetrafluoroethylene) or Rogers materials, to minimize dielectric losses and maintain signal integrity at high frequencies. These materials have lower dielectric constants and dissipation factors compared to standard FR-4 substrates.
4. Shielding and Grounding
Proper shielding and grounding techniques are essential in RF PCB design to minimize electromagnetic interference (EMI) and crosstalk between different sections of the board. This is achieved through the use of ground planes, shielding cans, and careful placement of components and traces.
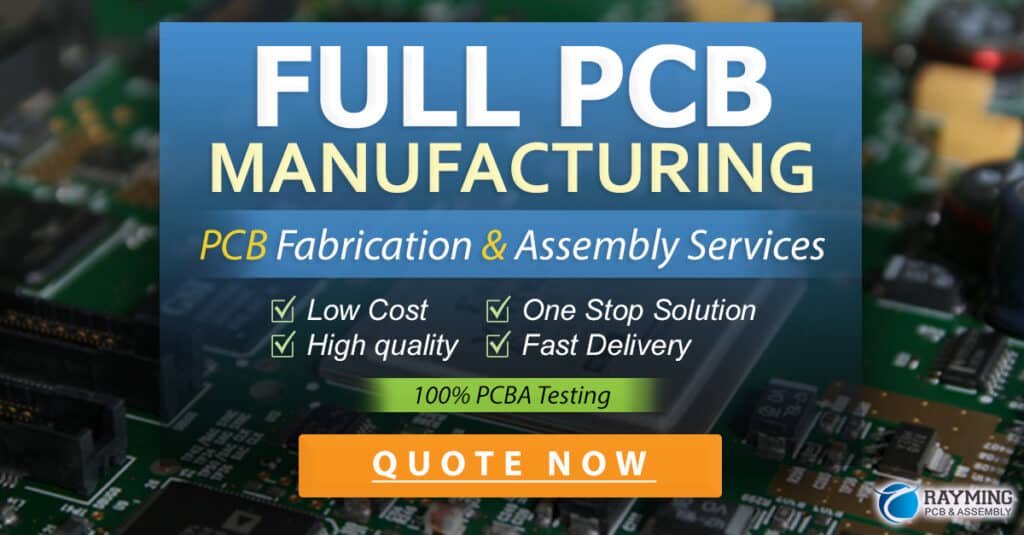
RF PCB Design Considerations
1. Transmission Lines
In RF PCBs, traces that carry high-frequency signals are treated as transmission lines. The two most common types of transmission lines used in RF PCBs are microstrip and stripline.
Microstrip
Microstrip transmission lines consist of a conductive trace on the top layer of the PCB, separated from a ground plane on the bottom layer by a dielectric substrate. Microstrip lines are easier to fabricate and provide better heat dissipation compared to striplines.
Stripline
Stripline transmission lines are embedded within the PCB, with conductive traces sandwiched between two ground planes. Striplines offer better shielding and lower radiation compared to microstrip lines but are more challenging to fabricate and have limited heat dissipation capabilities.
2. Impedance Matching
Impedance matching is critical in RF PCB design to ensure maximum power transfer and minimize signal reflections. This is achieved by designing transmission lines and components with matching impedances, typically 50 ohms in most RF systems.
3. Component Placement and Routing
The placement of components and routing of traces on an RF PCB play a significant role in its performance. Components should be placed close to each other to minimize trace lengths and reduce parasitic effects. Traces should be routed carefully to avoid sharp bends, maintain consistent impedance, and minimize crosstalk.
4. Multilayer Stackup
RF PCBs often employ multilayer stackups to accommodate complex circuitry and provide shielding between different sections of the board. A typical RF PCB stackup may include multiple signal layers, ground planes, and power planes, separated by dielectric layers.
Manufacturing Techniques for RF PCBs
1. High-Density Interconnect (HDI)
HDI technology enables the fabrication of RF PCBs with finer trace widths, smaller via sizes, and higher layer counts. This allows for more compact designs and improved signal integrity.
2. Microvia Technology
Microvias are small, laser-drilled holes that provide interconnections between layers in an RF PCB. They offer lower inductance and improved signal integrity compared to traditional mechanically-drilled vias.
3. Copper Plating
RF PCBs often require thicker copper plating to minimize resistive losses and improve heat dissipation. The thickness of the copper plating is typically expressed in ounces per square foot (oz/ft²), with common values ranging from 0.5 oz/ft² to 2 oz/ft².
4. Surface Finish
The choice of surface finish for an RF PCB can impact its performance and reliability. Common surface finishes for RF PCBs include Immersion Silver (IAg), Electroless Nickel Immersion Gold (ENIG), and Immersion Tin (ISn). Each surface finish has its own advantages and disadvantages in terms of cost, solderability, and high-frequency performance.
Applications of RF PCBs
RF PCBs find applications in a wide range of industries and devices, including:
- Telecommunications
- Cellular networks (4G, 5G)
- Wireless base stations
-
Satellite communication systems
-
Consumer Electronics
- Smartphones and tablets
- Wi-Fi routers and modems
- Bluetooth devices
-
GPS receivers
-
Automotive
- Vehicle-to-vehicle communication
- Radar sensors
-
Infotainment systems
-
Aerospace and Defense
- Radar systems
- Avionics
-
Military communication devices
-
Medical Devices
- Wireless patient monitoring
- Implantable devices
- Medical imaging equipment
Challenges in RF PCB Design and Manufacturing
Designing and manufacturing RF PCBs present several challenges due to the high-frequency nature of the signals and the stringent performance requirements. Some of the key challenges include:
-
Signal Integrity: Maintaining signal integrity in RF PCBs requires careful design and manufacturing practices to minimize signal distortion, reflections, and crosstalk.
-
Electromagnetic Compatibility (EMC): RF PCBs must be designed to minimize electromagnetic interference (EMI) and ensure compatibility with other electronic devices in their operating environment.
-
Thermal Management: High-frequency operation and dense component packaging in RF PCBs can lead to increased heat generation, requiring effective thermal management solutions.
-
Manufacturing Tolerances: RF PCBs require tighter manufacturing tolerances compared to standard PCBs, as even small deviations can significantly impact high-frequency performance.
-
Cost: The specialized materials, design considerations, and manufacturing techniques required for RF PCBs often result in higher costs compared to standard PCBs.
Future Trends in RF PCB Technology
As wireless technologies continue to evolve, RF PCB design and manufacturing must adapt to meet the increasing demands for higher data rates, lower latency, and improved reliability. Some of the future trends in RF PCB technology include:
-
5G and Beyond: The deployment of 5G networks and the development of future wireless standards will drive the need for advanced RF PCBs capable of operating at higher frequencies and supporting more complex modulation schemes.
-
Millimeter-Wave (mmWave) Technology: The use of mmWave frequencies (30 GHz to 300 GHz) for high-bandwidth applications, such as wireless backhaul and short-range communications, will require specialized RF PCB designs and manufacturing techniques.
-
Advanced Materials: The development of new, low-loss dielectric materials and conductive inks will enable the fabrication of RF PCBs with improved high-frequency performance and reduced losses.
-
Additive Manufacturing: The adoption of additive manufacturing techniques, such as 3D printing, for RF PCB fabrication may offer new design possibilities and faster prototyping.
-
Integration of Active Components: The integration of active components, such as amplifiers and filters, directly onto RF PCBs will lead to more compact and efficient designs.
Frequently Asked Questions (FAQ)
-
Q: What is the difference between an RF PCB and a standard PCB?
A: RF PCBs are designed to work with high-frequency signals in the radio frequency range, while standard PCBs are designed for lower-frequency applications. RF PCBs require specialized design considerations, materials, and manufacturing techniques to ensure optimal performance and signal integrity. -
Q: What are the most common materials used for RF PCB substrates?
A: The most common materials used for RF PCB substrates are PTFE (Polytetrafluoroethylene) and Rogers materials, such as RO4003C and RO4350B. These materials have low dielectric constants and dissipation factors, which help minimize signal losses at high frequencies. -
Q: What is the purpose of controlled impedance in RF PCBs?
A: Controlled impedance is essential in RF PCBs to ensure proper signal propagation and minimize reflections. By maintaining a consistent impedance throughout the PCB, signal integrity is preserved, and power transfer is optimized. -
Q: How does the surface finish affect the performance of an RF PCB?
A: The surface finish of an RF PCB can impact its high-frequency performance, solderability, and reliability. Different surface finishes, such as Immersion Silver (IAg), Electroless Nickel Immersion Gold (ENIG), and Immersion Tin (ISn), have their own advantages and disadvantages in terms of cost, signal integrity, and durability. -
Q: What are the key challenges in designing and manufacturing RF PCBs?
A: The key challenges in designing and manufacturing RF PCBs include maintaining signal integrity, ensuring electromagnetic compatibility, managing thermal issues, meeting tight manufacturing tolerances, and managing higher costs compared to standard PCBs.
Conclusion
RF PCBs are essential components in a wide range of electronic devices that rely on wireless communication and high-frequency signal processing. These specialized PCBs require careful design considerations, advanced materials, and precise manufacturing techniques to ensure optimal performance and reliability.
As wireless technologies continue to evolve and demand for high-frequency applications grows, RF PCB design and manufacturing will play a crucial role in enabling the next generation of wireless devices and systems. By understanding the key characteristics, design considerations, and manufacturing techniques associated with RF PCBs, engineers and designers can develop innovative solutions that push the boundaries of wireless communication and high-frequency electronics.
Characteristic | RF PCBs | Standard PCBs |
---|---|---|
Frequency Range | 100 MHz to several GHz | Typically below 100 MHz |
Materials | Low-loss substrates (PTFE, Rogers) | FR-4, CEM-3 |
Impedance Control | Critical for signal integrity | Less critical |
Transmission Lines | Microstrip, stripline | Not typically used |
Shielding and Grounding | Essential for EMI reduction | Less critical |
Manufacturing Techniques | HDI, microvias, thicker copper plating | Standard techniques |
Cost | Higher due to specialized materials and techniques | Lower |