Table of Contents
- Introduction to PCB Footprints
- Types of PCB Footprints
- Creating a PCB Footprint
- PCB Footprint Libraries
- Best Practices for PCB Footprint Design
- Common PCB Footprint Challenges
- PCB Footprint Verification and Testing
- Future Trends in PCB Footprint Design
- Frequently Asked Questions (FAQ)
- Conclusion
1. Introduction to PCB Footprints
A PCB footprint is a critical aspect of PCB design, as it determines how a component is mounted on the board. It includes the following elements:
- Pads: The conductive areas where the component leads or pins are soldered
- Holes: Drilled holes for through-hole components or vias
- Silkscreen: Text and symbols printed on the PCB for component identification and orientation
- Keepout areas: Regions where other components or traces should not be placed
Proper PCB footprint design ensures that components fit correctly, have adequate soldering points, and maintain the necessary clearances to avoid interference with other components or traces.
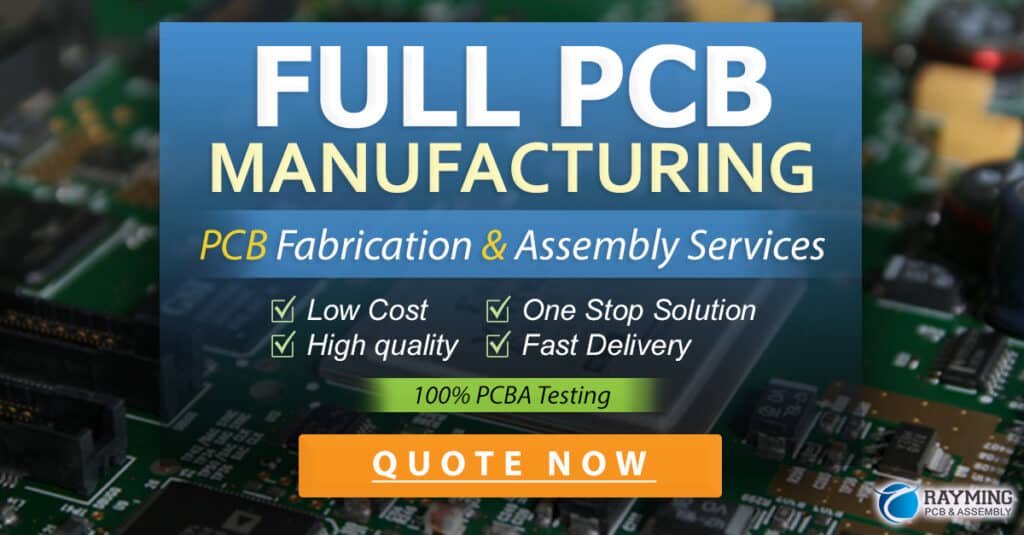
2. Types of PCB Footprints
There are several types of PCB footprints, each designed for specific component packages or mounting styles. Some common types include:
Footprint Type | Description |
---|---|
Surface Mount (SMD) | Components are mounted directly on the PCB surface, with pads for soldering. Examples include resistors, capacitors, and ICs in packages like 0402, 0603, SOIC, and QFP. |
Through-Hole (THT) | Components have leads that are inserted through drilled holes in the PCB and soldered on the opposite side. Examples include DIP ICs, connectors, and large capacitors. |
Ball Grid Array (BGA) | ICs with an array of solder balls underneath for high-density connections. Requires precise alignment and specialized soldering techniques. |
Quad Flat Package (QFP) | Surface mount ICs with leads on all four sides, providing a high pin count in a compact package. |
Land Grid Array (LGA) | Similar to BGA, but with flat pads instead of solder balls. Often used for high-frequency applications. |
Choosing the appropriate footprint type depends on factors such as component availability, PCB space constraints, manufacturing capabilities, and performance requirements.
3. Creating a PCB Footprint
Creating a PCB footprint involves the following steps:
- Obtain component dimensions and specifications from the manufacturer’s datasheet.
- Choose the appropriate CAD software for PCB design, such as Altium Designer, KiCad, or Eagle.
- Set up the CAD software with the correct units and grid settings.
- Draw the pads, holes, and outline of the component based on the datasheet dimensions.
- Add silkscreen markings for component identification and orientation.
- Define keepout areas, if necessary, to avoid interference with other components or traces.
- Verify the footprint dimensions and ensure compliance with the manufacturer’s recommendations and IPC standards.
When creating a PCB footprint, it’s essential to consider factors such as pad size, spacing, and shape, as well as the component’s tolerance and manufacturing variability. Proper footprint design helps ensure reliable soldering, reduces assembly errors, and minimizes the risk of component failure.
4. PCB Footprint Libraries
PCB footprint libraries are collections of pre-designed footprints for common components, which can save time and effort in the PCB design process. Many CAD software packages include built-in footprint libraries, and there are also online resources and community-created libraries available.
When using a footprint library, it’s important to:
- Verify the accuracy and compatibility of the footprint with your specific component and PCB manufacturing process.
- Check the footprint’s dimensions, pad sizes, and spacing against the manufacturer’s datasheet.
- Ensure that the footprint follows the appropriate IPC standards for your industry and application.
Creating and maintaining a custom footprint library can be beneficial for companies or individuals working on multiple projects with similar components, as it ensures consistency and reduces the risk of errors.
5. Best Practices for PCB Footprint Design
To ensure optimal PCB footprint design, consider the following best practices:
- Always refer to the manufacturer’s datasheet for component dimensions and recommended footprint layout.
- Follow IPC standards for pad size, spacing, and hole diameter to ensure manufacturing compatibility and reliability.
- Use appropriate pad shapes and sizes for the component’s pins or leads, considering factors such as solderability, mechanical stability, and current carrying capacity.
- Provide adequate clearance between pads and other components or traces to avoid short circuits and signal interference.
- Include clear silkscreen markings for component identification, orientation, and polarity.
- Consider the component’s thermal requirements and provide sufficient pad area for heat dissipation, if necessary.
- Verify the footprint design through visual inspection, CAD software checks, and prototype testing before finalizing the PCB layout.
By following these best practices, designers can create PCB footprints that are reliable, manufacturable, and compatible with the intended components and assembly processes.
6. Common PCB Footprint Challenges
Designing PCB footprints can present several challenges, particularly for complex or high-density designs. Some common challenges include:
- Accommodating component variations: Manufacturers may update component packages or dimensions, requiring footprint adjustments.
- Ensuring proper pad size and spacing: Insufficient pad size or spacing can lead to soldering difficulties or signal integrity issues.
- Dealing with high pin count components: Complex ICs like BGAs or QFPs require precise footprint design and specialized manufacturing processes.
- Managing thermal requirements: High-power components may require larger pads or thermal vias for effective heat dissipation.
- Accommodating mechanical constraints: Footprints must consider the component’s height, weight, and mounting requirements to ensure mechanical stability.
To overcome these challenges, designers should stay up-to-date with component specifications, collaborate with manufacturers and assembly partners, and use simulation tools to validate footprint performance before finalizing the PCB layout.
7. PCB Footprint Verification and Testing
Verifying and testing PCB footprints is essential to ensure proper component fitment, solderability, and overall PCB functionality. Some methods for footprint verification and testing include:
- Visual inspection: Carefully review the footprint dimensions, pad sizes, and spacing against the component datasheet and IPC standards.
- CAD software checks: Use the design rule check (DRC) and other verification tools in your CAD software to identify potential errors or violations.
- 3D modeling: Create a 3D model of the component and footprint to visually verify the fitment and identify any mechanical interferences.
- Prototype testing: Manufacture a prototype PCB with the designed footprints and physically test the component fitment, solderability, and functionality.
- X-ray inspection: Use X-ray imaging to verify the soldering quality and identify any hidden defects or voids in the solder joints.
By incorporating these verification and testing methods into the PCB design process, designers can identify and correct footprint issues early, reducing the risk of costly manufacturing defects or component failures.
8. Future Trends in PCB Footprint Design
As electronic components and PCB manufacturing technologies continue to evolve, PCB footprint design must adapt to new challenges and opportunities. Some future trends in PCB footprint design include:
- Miniaturization: As components become smaller and more compact, footprints must be designed to accommodate tighter spaces and higher densities.
- Advanced packaging: New component packaging technologies, such as wafer-level packaging (WLP) and system-in-package (SiP), require specialized footprint designs and manufacturing processes.
- High-speed design: With increasing signal frequencies and data rates, footprints must be designed to minimize signal integrity issues and maintain controlled impedance.
- Flexible and stretchable electronics: Footprints for flexible and stretchable PCBs must account for material properties and mechanical stresses.
- Additive manufacturing: 3D printing technologies may enable new footprint designs and manufacturing methods, such as embedded components and conformal circuits.
By staying informed about these trends and adapting footprint design practices accordingly, designers can create PCBs that are compatible with the latest components and manufacturing technologies.
9. Frequently Asked Questions (FAQ)
-
What is the difference between a PCB footprint and a schematic symbol?
A: A PCB footprint represents the physical layout and dimensions of a component on the PCB, while a schematic symbol represents the electrical connections and functionality of the component in the circuit diagram. -
Can I use the same PCB footprint for different components?
A: Generally, each component requires a specific footprint that matches its package dimensions and pin configuration. Using the wrong footprint can lead to fitment issues, soldering defects, or functional failures. -
How do I choose the appropriate pad size for a component?
A: Pad size is determined by factors such as the component’s pin size, soldering requirements, and current carrying capacity. Refer to the component datasheet and IPC standards for recommended pad sizes and tolerances. -
What is the purpose of silkscreen markings in a PCB footprint?
A: Silkscreen markings provide visual information about the component’s identification, orientation, and polarity, which aids in PCB assembly and troubleshooting. -
How can I verify the accuracy of a PCB footprint?
A: Verify the footprint by comparing its dimensions and layout against the component datasheet, using CAD software checks, and conducting prototype testing to ensure proper fitment and functionality.
10. Conclusion
PCB footprints play a crucial role in the design and manufacturing of electronic circuits. By understanding the types, creation process, best practices, and challenges associated with PCB footprints, designers can create reliable and manufacturable PCBs that meet the requirements of modern electronic devices.
As component technologies and PCB manufacturing methods continue to evolve, staying informed about the latest trends and adapting footprint design practices accordingly will be essential for success in the electronics industry.
By following the guidelines and best practices outlined in this article, designers can create PCB footprints that ensure proper component fitment, solderability, and overall PCB functionality, leading to more efficient and cost-effective electronic products.