Structure of a 4 Layer PCB
A 4 layer PCB is composed of the following layers:
- Top Layer (Signal Layer)
- Ground Layer
- Power Layer
- Bottom Layer (Signal Layer)
The top and bottom layers are typically used for routing signals, while the inner layers (ground and power) provide a stable reference plane and power distribution, respectively. The insulating material, usually FR-4, separates the conductive layers and provides mechanical support.
Layer | Function |
---|---|
Top | Signal routing, component placement |
Ground | Provides a stable reference plane, reduces EMI |
Power | Distributes power to components |
Bottom | Signal routing, component placement |
Top and Bottom Layers
The top and bottom layers of a 4 layer PCB are primarily used for routing signals and placing components. These layers are typically designed with a combination of traces, pads, and vias to connect components and route signals efficiently. The top layer often accommodates the majority of components, while the bottom layer is used for additional routing and component placement when necessary.
Ground Layer
The ground layer in a 4 layer PCB serves as a stable reference plane for the signal layers. By providing a low-impedance return path for signals, the ground layer helps to reduce EMI and improve signal integrity. This layer is usually a solid plane of copper, with vias connecting it to the ground pins of components on the top and bottom layers.
Power Layer
The power layer in a 4 layer PCB is responsible for distributing power to components on the board. This layer is typically divided into multiple power planes, each supplying a specific voltage level required by different components. The power layer is connected to the power pins of components through vias, ensuring a stable and reliable power supply.
Benefits of 4 Layer PCBs
Improved Signal Integrity
One of the primary benefits of using a 4 layer PCB is improved signal integrity. By having dedicated ground and power planes, the signal layers are shielded from interference, reducing crosstalk and signal distortion. This is particularly important for high-speed designs, where maintaining signal integrity is critical for proper functioning.
Reduced Electromagnetic Interference (EMI)
The ground layer in a 4 layer PCB acts as a shield against EMI, both from external sources and between different sections of the board. By providing a low-impedance return path for signals, the ground layer minimizes the loop area of current flow, reducing the amount of electromagnetic radiation emitted by the board. This is crucial for meeting EMC (Electromagnetic Compatibility) regulations and ensuring the reliability of the device.
Better Power Distribution
The dedicated power layer in a 4 layer PCB allows for better power distribution compared to 2 layer boards. By having a separate layer for power distribution, the voltage drop across the board is minimized, ensuring that all components receive a stable and consistent power supply. This is especially important for boards with high-power components or those requiring multiple voltage levels.
Increased Component Density
With four layers available for routing and component placement, 4 layer PCBs enable higher component density compared to 2 layer boards. This is because the additional layers provide more space for traces and vias, allowing for tighter component placement and more efficient use of board space. As a result, 4 layer PCBs are often used in applications where space is limited, such as mobile devices and wearables.
Enhanced Mechanical Strength
The additional layers in a 4 layer PCB contribute to increased mechanical strength and rigidity compared to 2 layer boards. This is due to the extra insulating material and copper layers, which provide more support and reduce the likelihood of board warpage or damage during handling and assembly. Enhanced mechanical strength is particularly important for applications subjected to vibration, shock, or extreme temperatures.
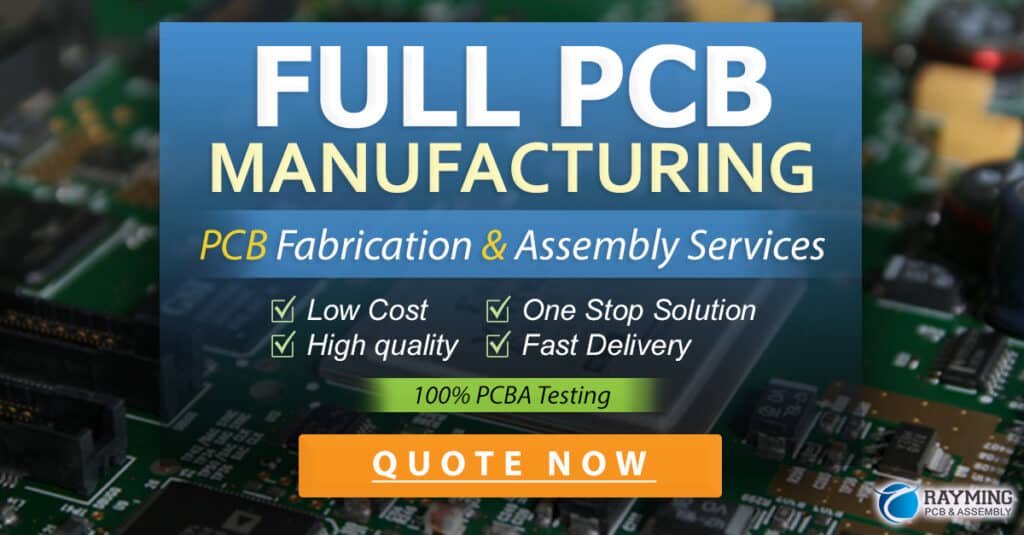
Applications of 4 Layer PCBs
4 layer PCBs are used in a wide range of applications, including:
- Consumer Electronics (smartphones, tablets, laptops)
- Automotive Electronics (infotainment systems, engine control units)
- Medical Devices (patient monitors, diagnostic equipment)
- Industrial Automation (PLCs, sensors, control systems)
- Aerospace and Defense (avionics, communication systems)
- Internet of Things (IoT) Devices (smart home appliances, wearables)
In each of these applications, 4 layer PCBs offer the necessary signal integrity, EMI reduction, power distribution, and component density to meet the specific requirements of the device.
Designing 4 Layer PCBs
When designing a 4 layer PCB, several key considerations must be taken into account to ensure optimal performance and manufacturability. These include:
Stack-up Planning
The stack-up of a 4 layer PCB refers to the arrangement of the layers and the materials used. Proper stack-up planning involves selecting the appropriate layer thicknesses, dielectric materials, and copper weights to meet the electrical and mechanical requirements of the design. The stack-up also influences the impedance of the traces, which is critical for high-speed designs.
Signal Routing
Signal routing on a 4 layer PCB involves carefully planning the placement of traces and vias to minimize signal integrity issues, such as crosstalk and reflections. This includes following best practices for trace width and spacing, avoiding sharp bends or long parallel runs, and properly terminating signals. It is also important to consider the routing of high-speed signals, which may require specific techniques like differential pairs or controlled impedance traces.
Power and Ground Distribution
Designing the power and ground layers of a 4 layer PCB involves creating an efficient distribution network that provides a stable and low-impedance supply to all components. This includes properly sizing the power and ground planes, placing decoupling capacitors close to power pins, and using vias to connect the planes to the top and bottom layers. It is also important to consider the current carrying capacity of the traces and planes to ensure adequate power delivery.
EMI Reduction Techniques
To further reduce EMI in a 4 layer PCB, designers can employ various techniques, such as:
- Proper grounding and shielding
- Use of ground planes and power planes
- Minimizing loop areas
- Filtering and decoupling
- Proper component placement and orientation
By implementing these techniques, designers can ensure that the 4 layer PCB meets EMC regulations and functions reliably in its intended environment.
Design for Manufacturing (DFM)
Designing a 4 layer PCB with manufacturability in mind is essential for ensuring a smooth and cost-effective production process. This involves adhering to the manufacturer’s design guidelines, such as minimum trace widths and spacings, hole sizes, and clearances. It is also important to consider the assembly process, including component placement, solderability, and testability. By following DFM principles, designers can minimize the risk of manufacturing defects and delays.
Frequently Asked Questions (FAQ)
-
What is the difference between a 2 layer and a 4 layer PCB?
A 4 layer PCB has two additional inner layers compared to a 2 layer pcb, which allows for better signal integrity, reduced EMI, and improved power distribution. 4 layer PCBs also offer higher component density and mechanical strength. -
When should I use a 4 layer PCB instead of a 2 layer PCB?
You should consider using a 4 layer PCB when your design requires high signal integrity, reduced EMI, efficient power distribution, or high component density. This is often the case for high-speed designs, devices with strict EMC requirements, or applications where space is limited. -
Are 4 layer PCBs more expensive than 2 layer PCBs?
Yes, 4 layer PCBs are generally more expensive than 2 layer PCBs due to the additional materials and manufacturing steps involved. However, the benefits of using a 4 layer PCB, such as improved performance and reliability, often outweigh the increased cost for many applications. -
How do I ensure proper signal integrity in a 4 layer PCB design?
To ensure proper signal integrity in a 4 layer PCB, follow best practices for signal routing, such as minimizing crosstalk and reflections, using appropriate trace widths and spacings, and properly terminating signals. It is also important to have a well-designed stack-up and to use techniques like ground planes and power planes to provide a stable reference and reduce EMI. -
Can I mix different signal types (e.g., analog and digital) on the same 4 layer PCB?
Yes, you can mix different signal types on a 4 layer PCB, but it is important to follow proper design guidelines to minimize interference between them. This includes separating analog and digital sections of the board, using proper grounding and shielding techniques, and routing sensitive signals away from noisy ones. In some cases, it may be necessary to use additional layers or split planes to further isolate different signal types.
Conclusion
4 layer PCBs offer numerous benefits over traditional 2 layer boards, including improved signal integrity, reduced EMI, better power distribution, and increased component density. These advantages make 4 layer PCBs an ideal choice for a wide range of applications, from consumer electronics to aerospace and defense.
When designing a 4 layer PCB, it is essential to consider factors such as stack-up planning, signal routing, power and ground distribution, EMI reduction, and design for manufacturing. By following best practices and guidelines in each of these areas, designers can create 4 layer PCBs that meet the specific requirements of their applications and perform reliably in their intended environments.
As technology continues to advance and the demand for high-performance, compact electronic devices grows, the use of 4 layer PCBs is likely to become increasingly common. By understanding the structure, benefits, and design considerations of these boards, engineers and manufacturers can leverage the capabilities of 4 layer PCBs to create innovative and reliable products that meet the needs of today’s market.