Introduction to Ceramic PCB
A ceramic printed circuit board (PCB) is a specialized type of PCB that uses a ceramic substrate material instead of the more common FR-4 fiberglass. Ceramic PCBs offer several advantages over traditional PCBs, making them ideal for certain high-performance applications.
The key benefits of ceramic PCBs include:
- High thermal conductivity
- Low dielectric constant and loss tangent
- Excellent dimensional stability
- Superior mechanical strength
- Resistance to harsh environments
These properties allow ceramic PCBs to operate reliably in demanding conditions such as high temperatures, high frequencies, and extreme environments. As a result, ceramic PCBs find use in various industries and applications where conventional PCBs may not be suitable.
Manufacturing Process of Ceramic PCBs
The manufacturing process of ceramic PCBs differs from that of standard PCBs due to the unique properties of the ceramic substrate. The basic steps involved in creating a ceramic PCB are:
-
Substrate preparation: The ceramic substrate, typically alumina (Al2O3) or aluminum nitride (AlN), is cleaned and inspected for defects.
-
Via drilling: Holes are drilled into the substrate to accommodate vias, which are used for interconnections between layers.
-
Metallization: A thin layer of metal, usually copper or gold, is deposited onto the substrate and into the via holes using techniques such as screen printing, sputtering, or plating.
-
Patterning: The desired circuit pattern is created on the metallized substrate using photolithography and etching processes.
-
Lamination: For multi-layer ceramic PCBs, individual layers are stacked and laminated together under high pressure and temperature.
-
Sintering: The laminated board is fired in a kiln at temperatures ranging from 850°C to 1600°C, depending on the ceramic material used. This process fuses the ceramic and metallic layers together.
-
Surface finishing: Additional surface treatments, such as nickel/gold plating or solder mask application, may be applied to improve solderability and protect the circuit.
The choice of ceramic material and manufacturing techniques employed depends on the specific requirements of the application, such as the desired electrical, thermal, and mechanical properties.
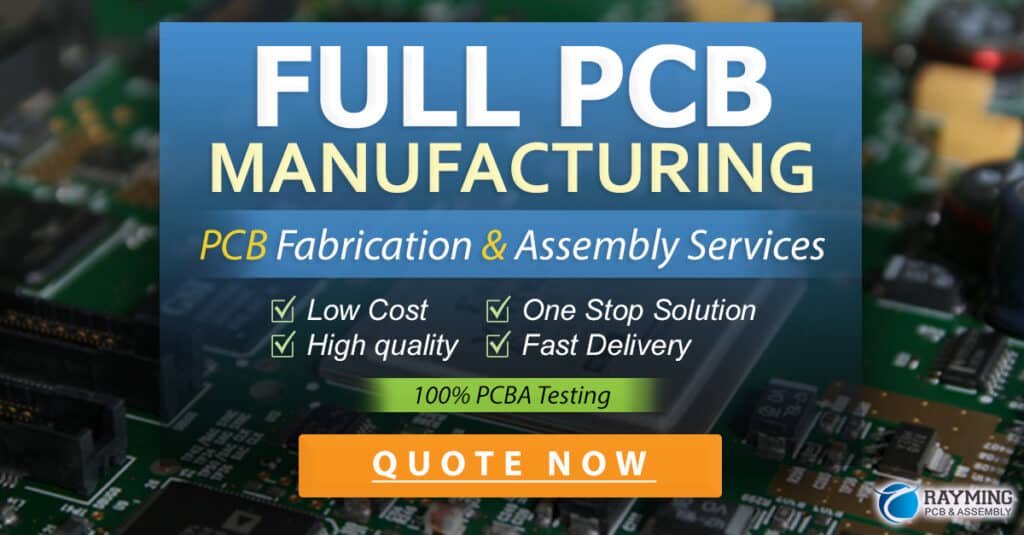
Advantages of Ceramic PCBs
High Thermal Conductivity
One of the primary advantages of ceramic PCBs is their high thermal conductivity compared to traditional FR-4 PCBs. This property allows ceramic PCBs to efficiently dissipate heat generated by electronic components, preventing overheating and ensuring reliable operation in high-temperature environments.
The thermal conductivity of common ceramic PCB materials is as follows:
Material | Thermal Conductivity (W/mK) |
---|---|
Alumina (Al2O3) | 20-30 |
Aluminum Nitride (AlN) | 170-200 |
Beryllium Oxide (BeO) | 260-300 |
In contrast, the thermal conductivity of FR-4 is only around 0.3 W/mK. The superior thermal management capabilities of ceramic PCBs make them suitable for applications such as power electronics, high-power LEDs, and aerospace systems.
Low Dielectric Constant and Loss Tangent
Ceramic PCBs offer low dielectric constant (Dk) and loss tangent (Df) values, which are crucial for high-frequency applications. A low Dk value minimizes signal propagation delay, while a low Df value reduces signal attenuation and power loss.
Typical Dk and Df values for common ceramic PCB materials are:
Material | Dielectric Constant (Dk) | Loss Tangent (Df) |
---|---|---|
Alumina (Al2O3) | 9.8-10.1 | 0.0001-0.0004 |
Aluminum Nitride (AlN) | 8.6-8.9 | 0.0005-0.0010 |
Beryllium Oxide (BeO) | 6.5-6.7 | 0.0001-0.0004 |
These properties make ceramic PCBs ideal for high-frequency applications such as RF and microwave circuits, radar systems, and wireless communications equipment.
Excellent Dimensional Stability
Ceramic PCBs exhibit excellent dimensional stability over a wide temperature range due to their low coefficient of thermal expansion (CTE). This stability is essential for maintaining the integrity of circuit traces and preventing warpage or delamination during thermal cycling.
The CTE values for common ceramic PCB materials are:
Material | CTE (ppm/°C) |
---|---|
Alumina (Al2O3) | 6.5-7.5 |
Aluminum Nitride (AlN) | 4.5-5.5 |
Beryllium Oxide (BeO) | 6.5-7.5 |
The low CTE of ceramic PCBs closely matches that of common electronic components, such as silicon (2.6 ppm/°C), minimizing stress on solder joints and improving long-term reliability.
Superior Mechanical Strength
Ceramic PCBs possess superior mechanical strength compared to traditional PCBs, making them more resistant to vibration, shock, and physical damage. This strength is due to the inherent properties of ceramic materials, which are harder and more rigid than the reinforced fiberglass used in FR-4 PCBs.
The flexural strength of common ceramic PCB materials is:
Material | Flexural Strength (MPa) |
---|---|
Alumina (Al2O3) | 300-400 |
Aluminum Nitride (AlN) | 300-350 |
Beryllium Oxide (BeO) | 200-250 |
The high mechanical strength of ceramic PCBs makes them suitable for applications that experience harsh mechanical stresses, such as aerospace, automotive, and industrial systems.
Resistance to Harsh Environments
Ceramic PCBs are highly resistant to harsh environmental conditions, including extreme temperatures, humidity, and corrosive substances. This resistance is due to the chemical stability and inert nature of ceramic materials.
Alumina and aluminum nitride ceramic PCBs can operate in temperatures ranging from -55°C to +400°C, while beryllium oxide PCBs can withstand temperatures up to +500°C. In contrast, FR-4 PCBs are typically limited to a maximum operating temperature of +130°C.
Ceramic PCBs are also resistant to moisture absorption, which can cause delamination and deterioration of electrical properties in traditional PCBs. Additionally, ceramic materials are chemically inert and resistant to most acids, bases, and solvents, making them suitable for use in corrosive environments.
Applications of Ceramic PCBs
Power Electronics
Ceramic PCBs are widely used in power electronics applications due to their high thermal conductivity and excellent electrical insulation properties. They are used in the following:
- Power modules for electric vehicles and renewable energy systems
- Motor drives and inverters
- High-power LED lighting
- Switching mode power supplies
The efficient heat dissipation and high dielectric strength of ceramic PCBs enable the design of compact, high-power electronic systems with improved reliability and performance.
High-Frequency and RF Applications
The low dielectric constant and loss tangent of ceramic PCBs make them ideal for high-frequency and RF applications, including:
- 5G wireless communications equipment
- Radar systems
- Satellite communications
- Microwave circuits
- Antennas and waveguides
Ceramic PCBs minimize signal distortion and power loss in these applications, ensuring optimal signal integrity and system performance.
Aerospace and Defense
Ceramic PCBs are used in various aerospace and defense applications due to their ability to withstand extreme temperatures, mechanical stresses, and harsh environments. Some examples include:
- Avionics systems
- Satellite components
- Missile guidance systems
- Radar and electronic warfare equipment
The high reliability and durability of ceramic PCBs make them essential for mission-critical systems in the aerospace and defense industries.
Automotive Electronics
Ceramic PCBs are increasingly used in automotive electronics, particularly in high-temperature and high-power applications such as:
- Engine control units
- Transmission control units
- Electric vehicle power electronics
- Hybrid vehicle battery management systems
The thermal stability and mechanical strength of ceramic PCBs ensure reliable operation in the demanding automotive environment, where vibration, shock, and temperature extremes are common.
Medical Devices
Ceramic PCBs are used in various medical devices, especially those that require high-frequency performance or resistance to sterilization processes. Some applications include:
- Imaging equipment (e.g., MRI, CT scanners)
- Surgical instruments
- Implantable devices
- Diagnostic equipment
The biocompatibility and chemical resistance of ceramic materials make them suitable for use in medical devices that come into contact with the human body or are exposed to sterilization agents.
Frequently Asked Questions (FAQ)
1. What is the difference between a ceramic PCB and a standard FR-4 PCB?
Ceramic PCBs use a ceramic substrate material, such as alumina or aluminum nitride, instead of the reinforced fiberglass used in FR-4 PCBs. This difference in substrate material gives ceramic PCBs superior thermal conductivity, low dielectric constant and loss tangent, excellent dimensional stability, and resistance to harsh environments compared to FR-4 PCBs.
2. What are the main advantages of using ceramic PCBs?
The main advantages of using ceramic PCBs include:
– High thermal conductivity for efficient heat dissipation
– Low dielectric constant and loss tangent for high-frequency applications
– Excellent dimensional stability over a wide temperature range
– Superior mechanical strength and resistance to vibration and shock
– Resistance to harsh environments, including extreme temperatures, humidity, and corrosive substances
3. What industries commonly use ceramic PCBs?
Ceramic PCBs are commonly used in industries and applications that require high performance, reliability, and durability, such as:
– Power electronics
– High-frequency and RF applications
– Aerospace and defense
– Automotive electronics
– Medical devices
4. Can ceramic PCBs be used for multilayer designs?
Yes, ceramic PCBs can be used for multilayer designs. The individual layers are stacked and laminated together under high pressure and temperature during the manufacturing process. Multilayer ceramic PCBs offer increased circuit density and functionality compared to single-layer designs.
5. Are ceramic PCBs more expensive than traditional PCBs?
Yes, ceramic PCBs are generally more expensive than traditional FR-4 PCBs due to the higher cost of ceramic materials and the specialized manufacturing processes involved. However, the superior performance and reliability of ceramic PCBs often justify the higher cost in demanding applications where traditional PCBs may not be suitable.
Conclusion
Ceramic PCBs offer a range of advantages over traditional PCBs, including high thermal conductivity, low dielectric constant and loss tangent, excellent dimensional stability, superior mechanical strength, and resistance to harsh environments. These properties make ceramic PCBs ideal for various high-performance applications in industries such as power electronics, high-frequency and RF systems, aerospace and defense, automotive electronics, and medical devices.
While ceramic PCBs may have a higher initial cost compared to FR-4 PCBs, their superior performance and reliability often justify the investment in demanding applications. As technology continues to advance and the need for high-performance electronics grows, the use of ceramic PCBs is likely to expand further, enabling the development of more advanced and reliable systems across various industries.