Introduction to PCB Traces
Printed Circuit Board (PCB) traces are the copper paths that conduct electrical signals between components on a PCB. The traces act as wires to interconnect components like resistors, capacitors, integrated circuits, and connectors soldered to the board. Properly designed PCB traces are critical for the reliable operation and performance of electronic devices.
Key Characteristics of PCB Traces
- Made of copper foil laminated onto an insulating substrate
- Etched away areas of unwanted copper leaving behind conductive paths
- Typically covered by a solder mask layer with openings for component pads
- Can be on external or internal layers in multi-layer PCBs
- Trace width, thickness, and spacing impact electrical properties
PCB Trace Geometry and Dimensions
The geometry and dimensions of PCB traces determine their electrical characteristics like resistance, capacitance, and ability to carry current. The main parameters are:
Trace Width
Trace width is the side-to-side distance across a trace. Wider traces have lower resistance and can carry higher currents. Common trace widths range from 0.005″ to 0.025″ depending on the current requirements.
Trace Thickness
Copper thickness or weight refers to the thickness of the copper foil used for PCB traces. It’s specified in ounces per square foot, with 1 oz/ft² yielding a thickness of approximately 1.4 mils or 35 microns. Thicker copper allows higher current capacity.
Trace Spacing
The spacing between adjacent traces impacts crosstalk, electrical isolation, and PCB manufacturing capabilities. Smaller spacing allows denser routing at the cost of increased crosstalk. Typical trace spacing ranges from 0.003″ to 0.010″.
Here is a table summarizing common PCB trace width and copper thicknesses:
Copper Weight (oz/ft²) | Trace Thickness (mils / μm) | Typical Trace Width Range (mils) |
---|---|---|
0.5 | 0.7 / 17.5 | 4 – 8 |
1 | 1.4 / 35 | 5 – 25 |
2 | 2.8 / 70 | 25 – 100 |
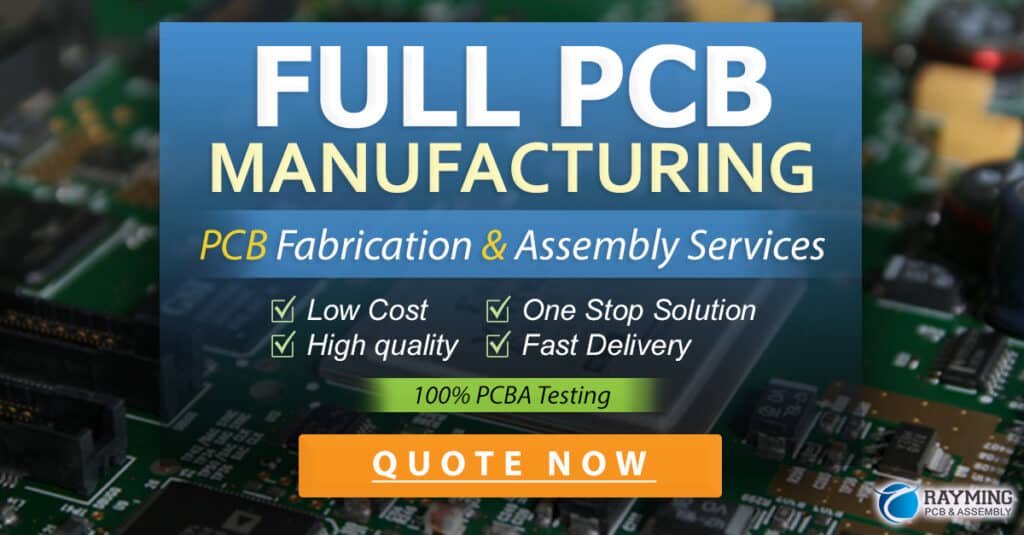
Calculating Trace Width for Current Capacity
To ensure PCB traces can safely carry the required current without overheating, designers must calculate the appropriate trace width. The maximum allowable current is a function of the trace cross-sectional area, copper thickness, and allowable temperature rise.
IPC-2221 Current Capacity Charts
The IPC-2221 generic standard on PCB design provides charts that relate trace width and thickness to current capacity for external and internal traces with different copper weights and temperature rises.
For example, for a 10°C rise on an external 1 oz copper trace:
Trace Width (mils) | Maximum Current (A) |
---|---|
10 | 0.5 |
50 | 2.2 |
100 | 3.9 |
Online Trace Width Calculators
Many free online tools allow easy calculation of PCB trace widths based on IPC-2221 formulas. The user enters parameters such as copper thickness, maximum current, allowable temperature rise, and trace length, and the tool outputs the required trace width.
Controlling PCB Trace Impedance
For high-speed digital and RF circuits, the impedance of PCB traces is critical for signal integrity and must be tightly controlled to match driver, receiver and interconnect impedances. The characteristic impedance of a trace is determined by its geometry and the properties of the PCB substrate.
Microstrip Traces
A microstrip is a trace on an outer layer, separated from a reference plane like a ground plane by the board substrate, which acts as the dielectric.
The characteristic impedance of a microstrip trace is approximately:
Z₀ = 87/√(ϵᵣ+1.41) ln[5.98H/(0.8W+T)]
Where:
– ϵᵣ is the dielectric constant of the substrate
– H is the substrate thickness
– W is the trace width
– T is the trace thickness
Stripline Traces
A stripline is a trace embedded between two reference planes inside a multi-layer board, with the substrate as dielectric on both sides.
The characteristic impedance of a stripline trace is approximately:
Z₀ = 60/√ϵᵣ ln[1.9H/(0.8W+T)]
Where the variables are the same as for microstrip traces.
Coplanar Waveguides
A coplanar waveguide (CPW) has the trace and reference planes on the same layer, with the trace surrounded by a dielectric and then ground planes on either side.
The characteristic impedance of a CPW is:
Z₀ = 30π/√ϵᵣ [K(k₁)/K(k₂)]
Where:
– K(k) is the complete elliptic integral of the first kind
– k₁ = W/(W+2G)
– k₂ = √(1-k₁²)
– W is the trace width
– G is the gap width between trace and grounds
Here is a table comparing typical geometries for 50 ohm impedance traces:
Trace Geometry | W | H | T | G |
---|---|---|---|---|
Microstrip | 20 mil | 8 mil | 1.4 mil | N/A |
Stripline | 10 mil | 10 mil | 1.4 mil | N/A |
CPW | 12 mil | 8 mil | 1.4 mil | 8 mil |
Transmission Lines and Reflections
At high frequencies or with fast rise/fall times, PCB traces act as transmission lines and can suffer from reflections and ringing if not properly terminated.
Critical Length
The critical length is the trace length at which transmission line effects become significant and reflections can occur. It’s determined by the signal rise time and propagation delay of the trace.
Lcritical = trise/(2√ϵᵣ)
Where:
– trise is the 10-90% rise time of the signal
– ϵᵣ is the dielectric constant of the substrate
Traces longer than the critical length should be treated as transmission lines.
Reflection Coefficient
When a signal encounters an impedance mismatch at the end of a trace, some of the energy is reflected back towards the source. The amount of reflection is given by the reflection coefficient:
Γ = (ZL – Z0)/(ZL + Z0)
Where:
– ZL is the load impedance
– Z0 is the characteristic impedance of the trace
The magnitude of the reflection coefficient should be minimized by matching the load impedance to the trace impedance.
Termination Strategies
To minimize reflections, PCB traces should be terminated by matching the load impedance to the trace characteristic impedance. Common termination strategies include:
Series Termination
A resistor in series with the driver output, with value equal to the driver impedance minus the trace impedance.
Parallel Termination
A resistor in parallel with the receiver input, with value equal to the trace characteristic impedance.
AC Termination
A resistor in series with a capacitor to ground at the receiver input, providing a high-frequency termination while consuming less DC current.
Termination | Schematic |
---|---|
Series | |
Parallel | |
AC |
Routing PCB Traces
Effective PCB layout and routing of traces is critical for good signal integrity, EMC, and manufacturability. Some key guidelines include:
Keep Traces Short
Shorter traces have lower resistance, inductance, and capacitance, reducing losses, crosstalk, and EMI. They also minimize the potential for transmission line effects and reflections.
Avoid 90° Corners
Sharp 90° corners in traces can cause impedance discontinuities and radiate EMI. Use 45° mitred or curved corners instead.
Route in Orthogonal Directions
On multi-layer boards, route traces in orthogonal directions on adjacent layers, e.g. horizontal on one layer and vertical on next. This minimizes crosstalk between layers.
Provide Ground Planes
Solid ground planes provide a low-impedance return path for currents, important for signal integrity and EMI reduction. They also help control trace impedance.
Minimize Loop Areas
The current flowing in a signal trace returns through the ground plane directly beneath it. This current loop acts as an antenna to radiate and pick up noise. Minimizing loop area by keeping signal and return close together reduces EMI.
Avoid Splitting Ground Planes
Splits in ground planes force return currents to divert around them, causing large loop areas and EMI. Avoid splitting ground planes under sensitive analog and high-speed digital circuits.
FAQ
What is a PCB trace?
A PCB trace is a copper path etched onto a PCB to electrically connect components. Traces act as wires carrying signals and power between components on the board.
How thin can PCB traces be?
The minimum PCB trace width is limited by the capabilities of the PCB manufacturer and the required current capacity. Typical minimum trace widths are around 0.005″ or 5 mils, but some advanced processes can produce traces as thin as 0.003″.
What is trace impedance and why does it matter?
The characteristic impedance of a PCB trace is its equivalent resistance to high-frequency AC signals. It is determined by the trace geometry and PCB materials. Matching the trace impedance to driver and receiver impedances is critical for good signal integrity and to avoid reflections, especially for high-speed digital and RF circuits.
How much current can a PCB trace handle?
The maximum current capacity of a PCB trace depends on its width, thickness, and allowable temperature rise. Charts in the IPC-2221 standard define the current limits for different trace geometries. As a rough guide, a 0.010″ wide 1 oz copper trace can safely carry about 0.5A.
What is a PCB transmission line?
A PCB trace acts as a transmission line when its length is greater than the critical length determined by the signal rise time and propagation velocity. Transmission lines require termination to avoid reflections and ringing. High-speed digital and RF traces are often transmission lines and must be carefully designed and routed.