Understanding PCB Thickness
PCB thickness refers to the distance between the top and bottom surfaces of the board, excluding any additional layers such as solder mask or silkscreen. The thickness of a PCB is typically measured in either inches or millimeters.
Common PCB Thickness Units
- Inches (e.g., 0.031″, 0.062″)
- Millimeters (e.g., 0.8mm, 1.6mm)
It’s important to note that PCB thickness is often specified using the imperial unit of inches in the United States and Canada, while the metric unit of millimeters is more commonly used in other parts of the world.
PCB Thickness and Layer Count
PCB thickness is closely related to the number of layers in the board. As the number of layers increases, the overall thickness of the PCB also increases. However, the relationship between layer count and thickness is not always linear, as it depends on the specific manufacturing process and materials used.
Layer Count | Typical Thickness Range |
---|---|
1 | 0.4mm – 1.6mm |
2 | 0.8mm – 2.0mm |
4 | 1.0mm – 2.4mm |
6 | 1.2mm – 2.8mm |
8 | 1.6mm – 3.2mm |
Note: The thickness ranges provided are approximate and may vary depending on the manufacturer and specific requirements.
Standard PCB Thicknesses
There are several standard PCB thicknesses used in the industry, each with its own applications and benefits. Let’s explore some of the most common standard thicknesses.
0.8mm (0.031″)
- Lightweight and flexible
- Suitable for low-power and portable devices
- Commonly used in small handheld devices, wearables, and flexible circuits
1.0mm (0.039″)
- Offers a balance between thickness and durability
- Suitable for general-purpose applications
- Used in consumer electronics, automotive components, and industrial controls
1.2mm (0.047″)
- Provides increased mechanical strength and rigidity
- Suitable for applications with moderate power requirements
- Used in telecommunications equipment, medical devices, and aerospace systems
1.6mm (0.063″)
- Robust and sturdy construction
- Suitable for high-power and high-reliability applications
- Used in power electronics, industrial automation, and military equipment
2.0mm (0.079″)
- Extremely durable and resistant to mechanical stress
- Suitable for heavy-duty and harsh environmental conditions
- Used in industrial machinery, power distribution systems, and offshore installations
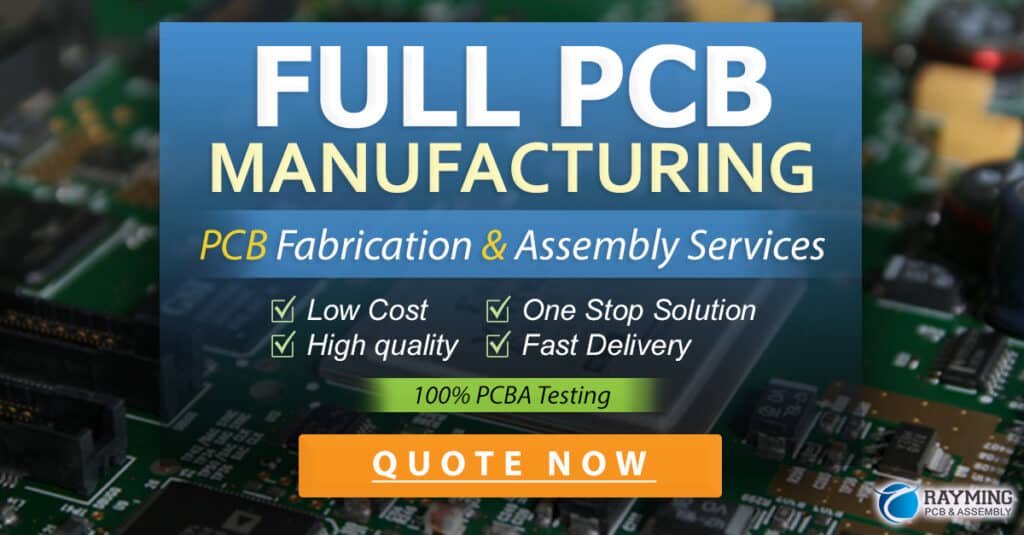
Factors Affecting PCB Thickness Selection
When choosing the appropriate PCB thickness for your project, several factors should be considered to ensure optimal performance and reliability.
Mechanical Strength and Durability
The thickness of a PCB directly impacts its mechanical strength and durability. Thicker PCBs are generally more resistant to bending, twisting, and vibration. If your application involves harsh environmental conditions or high mechanical stress, opting for a thicker PCB can provide increased durability and longevity.
Electrical Performance
PCB thickness can also influence the electrical performance of the board. Thinner PCBs may be more susceptible to signal integrity issues, such as crosstalk and electromagnetic interference (EMI). On the other hand, thicker PCBs can offer better power handling capabilities and improved thermal dissipation.
Component Mounting and Assembly
The thickness of a PCB should be compatible with the components that will be mounted on it. Certain components, such as heavy heatsinks or connectors, may require a thicker PCB for proper support and stability. Additionally, the assembly process, including soldering and reflow, should be considered when selecting the PCB thickness to ensure reliable and consistent results.
Cost and Manufacturing Considerations
PCB thickness can impact the cost and manufacturing process of the board. Thinner PCBs generally require less material and may be more cost-effective to produce. However, thicker PCBs may require specialized manufacturing techniques and equipment, which can increase production costs. It’s essential to find a balance between cost and performance when selecting the appropriate PCB thickness.
PCB Thickness Standards and Guidelines
Several industry standards and guidelines provide recommendations for PCB thickness based on specific applications and requirements.
IPC Standards
The IPC (Association Connecting Electronics Industries) is a global trade association that develops standards for the electronic manufacturing industry. IPC standards, such as IPC-2221 and IPC-6012, provide guidelines for PCB design and fabrication, including recommendations for PCB thickness based on layer count and application.
Mil-Spec Standards
Military and aerospace applications often require adherence to specific military specifications (Mil-Spec) for PCB design and manufacturing. Mil-Spec standards, such as MIL-PRF-31032 and MIL-PRF-55110, outline requirements for PCB thickness, material selection, and performance criteria to ensure reliability in harsh environments.
Manufacturer Guidelines
PCB manufacturers may provide their own guidelines and recommendations for PCB thickness based on their manufacturing capabilities and experience. It’s important to consult with your chosen manufacturer to ensure that your desired PCB thickness is feasible and compatible with their production processes.
Frequently Asked Questions (FAQ)
-
Q: What is the most common PCB thickness?
A: The most common PCB thickness is 1.6mm (0.063″). This thickness offers a good balance between mechanical strength and cost-effectiveness for a wide range of applications. -
Q: Can I use a thinner PCB to save cost?
A: While using a thinner PCB may result in cost savings due to reduced material usage, it’s important to consider the specific requirements of your application. Thinner PCBs may not provide sufficient mechanical strength or electrical performance for certain applications. -
Q: How does PCB thickness affect signal integrity?
A: PCB thickness can impact signal integrity in several ways. Thinner PCBs may be more susceptible to crosstalk and electromagnetic interference (EMI) due to closer proximity of traces. Thicker PCBs can provide better signal integrity by allowing for wider trace spacing and improved shielding. -
Q: Can I mix different PCB thicknesses in the same design?
A: Yes, it is possible to use different PCB thicknesses within the same design. This approach is known as a “rigid-flex” PCB, where flexible sections are combined with rigid sections of varying thicknesses. Rigid-flex PCBs offer unique advantages in terms of packaging and mechanical flexibility. -
Q: How do I determine the appropriate PCB thickness for my project?
A: To determine the appropriate PCB thickness, consider factors such as mechanical strength requirements, electrical performance needs, component mounting, and cost. Consult with your PCB manufacturer and refer to relevant industry standards and guidelines to make an informed decision based on your specific application.
Conclusion
PCB thickness is a critical aspect of PCB design and manufacturing, impacting the mechanical strength, electrical performance, and overall functionality of the board. Understanding the standard PCB thicknesses and their applications is essential for selecting the appropriate thickness for your project.
When choosing PCB thickness, consider factors such as mechanical durability, electrical requirements, component mounting, and cost. Refer to industry standards, such as IPC and Mil-Spec, and consult with your PCB manufacturer for guidance and recommendations.
By selecting the appropriate PCB thickness, you can ensure that your electronic device performs reliably, meets the necessary mechanical and electrical requirements, and achieves the desired level of durability and longevity.