Introduction
In the realm of product development, engineering, and manufacturing, the management of component revisions is a critical aspect that ensures the integrity, reliability, and efficiency of the final product. Components, which are the building blocks of any product, undergo numerous changes throughout their lifecycle. These changes can be due to design improvements, material substitutions, regulatory compliance, or corrective actions to address defects. Validating and updating component revisions is a meticulous process that requires a structured approach to ensure that all changes are accurately documented, tested, and implemented. This article delves into the intricacies of validating and updating component revisions, highlighting best practices, methodologies, and the importance of this process in maintaining product quality and compliance.
Understanding Component Revisions
What are Component Revisions?
Component revisions refer to the modifications made to a component’s design, specifications, or materials after its initial release. These revisions are typically documented in a revision history, which tracks all changes made to the component over time. Each revision is assigned a unique identifier, such as a revision number or letter, to distinguish it from previous versions.
Why are Component Revisions Necessary?
Component revisions are necessary for several reasons:
- Design Improvements: As products evolve, components may need to be redesigned to enhance performance, reduce costs, or incorporate new technologies.
- Material Substitutions: Changes in material availability, cost, or regulatory requirements may necessitate the substitution of materials used in a component.
- Corrective Actions: If a component is found to be defective or non-compliant, revisions may be required to address the issue.
- Regulatory Compliance: Changes in industry standards or regulations may require updates to components to ensure compliance.
- Manufacturing Optimization: Revisions may be made to improve manufacturability, reduce production time, or enhance quality control.
The Importance of Validating Component Revisions
Ensuring Product Quality
Validating component revisions is crucial to maintaining the quality of the final product. Each revision must be thoroughly tested to ensure that it meets the required specifications and performs as intended. Failure to validate revisions can lead to product failures, recalls, and damage to the brand’s reputation.
Compliance with Standards and Regulations
Many industries are subject to strict regulations and standards that govern the design, manufacturing, and testing of components. Validating revisions ensures that the component remains compliant with these requirements, reducing the risk of legal issues and penalties.
Risk Management
Validating revisions helps identify and mitigate potential risks associated with changes to a component. By thoroughly testing each revision, manufacturers can detect and address issues before they impact the product or end-users.
Cost Control
Unvalidated revisions can lead to costly rework, scrap, and warranty claims. By validating revisions, manufacturers can avoid these expenses and ensure that changes are implemented correctly the first time.
The Process of Validating Component Revisions
1. Change Request and Approval
The validation process begins with a change request, which documents the proposed revision and the rationale behind it. The request is reviewed by a cross-functional team, including design engineers, quality assurance, and manufacturing personnel, to assess the impact of the change. Once approved, the revision is assigned a unique identifier and added to the component’s revision history.
2. Design and Documentation Update
The next step is to update the component’s design and documentation to reflect the proposed changes. This may involve modifying CAD drawings, updating bill of materials (BOM), and revising technical specifications. All changes must be clearly documented and communicated to relevant stakeholders.
3. Prototyping and Testing
After the design and documentation have been updated, a prototype of the revised component is produced. The prototype undergoes rigorous testing to validate its performance, durability, and compliance with specifications. Testing may include:
- Functional Testing: Ensures that the component performs its intended function.
- Environmental Testing: Assesses the component’s performance under various environmental conditions, such as temperature, humidity, and vibration.
- Lifecycle Testing: Evaluates the component’s durability and longevity under normal operating conditions.
- Compliance Testing: Verifies that the component meets relevant industry standards and regulations.
4. Review and Approval of Test Results
Once testing is complete, the results are reviewed by the cross-functional team to determine if the revised component meets the required criteria. If the results are satisfactory, the revision is approved for implementation. If issues are identified, the component may need to be redesigned and retested.
5. Implementation and Documentation
After approval, the revised component is implemented into production. The revision history is updated to reflect the changes, and all relevant documentation, including BOMs, drawings, and specifications, is revised accordingly. The updated documentation is distributed to all stakeholders to ensure that everyone is working with the most current information.
6. Monitoring and Feedback
Once the revised component is in production, it is important to monitor its performance and gather feedback from end-users. This feedback can be used to identify any issues that may not have been detected during testing and to inform future revisions.
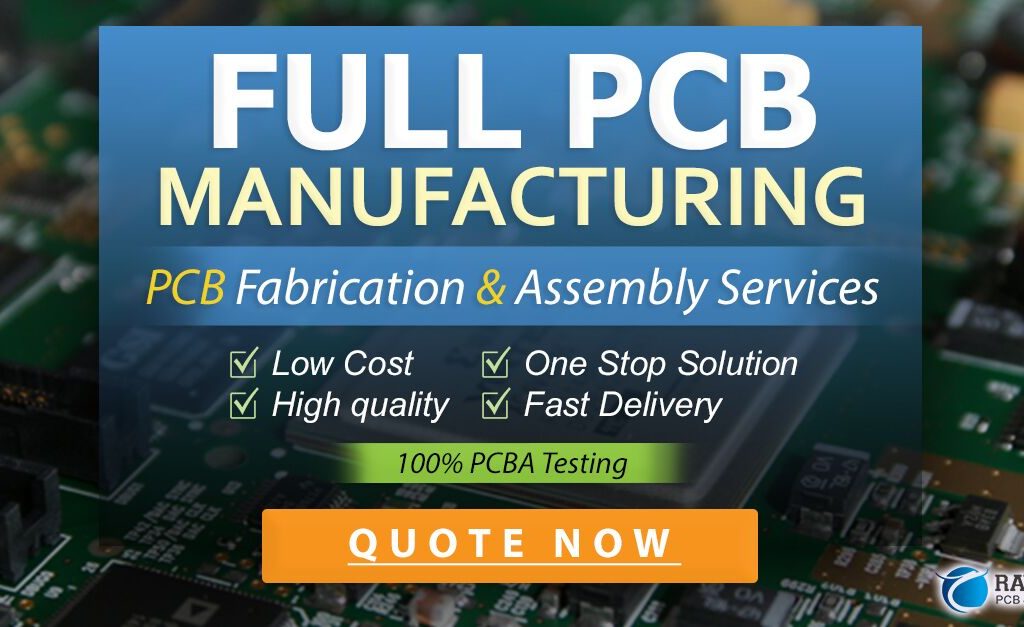
Best Practices for Validating and Updating Component Revisions
1. Establish a Robust Change Management Process
A well-defined change management process is essential for effectively managing component revisions. This process should include clear guidelines for submitting, reviewing, and approving change requests, as well as procedures for updating documentation and communicating changes to stakeholders.
2. Utilize a Cross-Functional Team
Validating component revisions requires input from various disciplines, including design, engineering, quality assurance, and manufacturing. A cross-functional team ensures that all aspects of the revision are thoroughly evaluated and that potential impacts on the product and production process are considered.
3. Implement a Comprehensive Testing Protocol
A comprehensive testing protocol is critical for validating component revisions. The protocol should include a variety of tests to assess the component’s performance, durability, and compliance with specifications. Testing should be conducted under conditions that simulate real-world use to ensure that the component will perform as expected in the field.
4. Maintain Accurate and Up-to-Date Documentation
Accurate and up-to-date documentation is essential for managing component revisions. All changes to the component’s design, specifications, and materials should be clearly documented and communicated to relevant stakeholders. This documentation serves as a reference for future revisions and helps ensure that everyone is working with the most current information.
5. Conduct Regular Audits and Reviews
Regular audits and reviews of the change management process can help identify areas for improvement and ensure that the process is being followed consistently. Audits should include a review of change requests, testing protocols, and documentation to ensure that all revisions are being properly validated and implemented.
6. Leverage Technology and Automation
Technology and automation can streamline the process of validating and updating component revisions. For example, product lifecycle management (PLM) software can be used to track changes, manage documentation, and facilitate communication among stakeholders. Automated testing equipment can also be used to conduct tests more efficiently and accurately.
7. Foster a Culture of Continuous Improvement
A culture of continuous improvement encourages employees to identify opportunities for enhancing the change management process and to suggest improvements to component designs. This culture can lead to more efficient and effective validation processes, as well as higher-quality components.
Challenges in Validating and Updating Component Revisions
1. Complexity of Components
As products become more complex, so do their components. Complex components may require more extensive testing and validation, which can increase the time and cost associated with revisions.
2. Regulatory Compliance
Navigating the regulatory landscape can be challenging, especially for products that are subject to multiple regulations and standards. Ensuring that component revisions comply with all relevant requirements can be a time-consuming and resource-intensive process.
3. Supply Chain Considerations
Changes to components can have a ripple effect throughout the supply chain. For example, a material substitution may require sourcing from a new supplier, which can impact lead times and costs. Coordinating with suppliers and ensuring that they are aware of and can accommodate changes is a critical aspect of managing component revisions.
4. Communication and Collaboration
Effective communication and collaboration among stakeholders are essential for successfully validating and updating component revisions. However, achieving this can be challenging, especially in large organizations with multiple departments and teams. Miscommunication or lack of collaboration can lead to delays, errors, and inconsistencies in the revision process.
5. Balancing Speed and Thoroughness
In today’s fast-paced market, there is often pressure to implement changes quickly to stay competitive. However, rushing the validation process can lead to oversights and errors that compromise product quality. Balancing the need for speed with the need for thoroughness is a key challenge in managing component revisions.
Case Study: Validating and Updating Component Revisions in the Automotive Industry
Background
The automotive industry is highly regulated and requires rigorous validation of component revisions to ensure safety, reliability, and compliance with standards. A leading automotive manufacturer faced a challenge when a critical component in one of its vehicles was found to be prone to failure under certain conditions. The manufacturer needed to revise the component and validate the changes to prevent future failures and maintain customer trust.
The Process
- Change Request and Approval: The issue was identified through customer feedback and internal testing. A change request was submitted, and a cross-functional team was assembled to assess the impact of the proposed revision.
- Design and Documentation Update: The design team modified the component to address the failure mode, and the documentation was updated to reflect the changes. The revised design was reviewed and approved by the cross-functional team.
- Prototyping and Testing: A prototype of the revised component was produced and subjected to a battery of tests, including functional testing, environmental testing, and lifecycle testing. The testing protocol was designed to simulate real-world conditions and ensure that the revised component would perform as expected.
- Review and Approval of Test Results: The test results were reviewed by the cross-functional team, and the revised component was found to meet all required criteria. The revision was approved for implementation.
- Implementation and Documentation: The revised component was implemented into production, and the revision history was updated. The updated documentation was distributed to all stakeholders, including suppliers and manufacturing partners.
- Monitoring and Feedback: The revised component was monitored in the field, and feedback was collected from customers and service technicians. The feedback was used to confirm that the revision had successfully addressed the issue and to identify any additional areas for improvement.
Outcome
The validation and update process resulted in a revised component that met all performance, durability, and compliance requirements. The manufacturer was able to address the issue quickly and effectively, minimizing the impact on customers and maintaining the quality and reliability of its vehicles.
Conclusion
Validating and updating component revisions is a critical process that ensures the quality, reliability, and compliance of products. By following a structured approach and adhering to best practices, manufacturers can effectively manage component revisions and minimize the risks associated with changes. A robust change management process, cross-functional collaboration, comprehensive testing, and accurate documentation are key to successfully validating and updating component revisions. Despite the challenges, the benefits of a well-executed revision process far outweigh the costs, leading to higher-quality products, satisfied customers, and a stronger competitive position in the market.