Introduction
Flexible printed circuit boards (PCBs), also known as flex circuits or flex PCBs, are a vital component in modern electronics due to their ability to bend and flex. As devices get smaller and more compact, flexible PCBs allow circuitry to fit into tight spaces. They are commonly used in consumer devices like mobile phones and wearable tech. For device manufacturers, calculating flexible PCB costs is an important part of the design and production process. This guide will provide a comprehensive overview of the factors that influence flex PCB pricing.
What is a Flexible PCB?
A flexible PCB is a circuit built on a flexible plastic substrate like polyimide or polyester film. The circuits are made from conductive copper traces that are photo-etched or printed onto the substrate. The flex circuit can bend, twist and flex dynamically without damage to the copper traces. Some key advantages of flexible PCBs:
- Can be bent and folded to fit into tight spaces
- Dynamic flexing withstands vibration and impact
- Thin, lightweight and portable
- Can be twisted and contorted during assembly
- More reliable connections to moving components
- Allows for more compact and ergonomic designs
- Can be embedded into cables, displays and wearables
Flexible PCBs are commonly single, double or multilayer circuits. Rigid PCBs or components can be mounted onto them as well. Flexible PCB technology enables the production of slim, compact and portable modern electronics.
Flexible PCB Cost Considerations
The costs of a flex PCB can be broken down into materials, fabrication and testing expenses. Here are the key factors that influence pricing:
Flex Circuit Materials
- Base material – Polyimide and polyester films are commonly used. Thinner material is more expensive.
- Copper thickness – Varies from 1/4 oz to 2 oz typically. Thicker copper increases cost.
- Dielectric layers – Additional polyimide layers increase flex thickness and cost.
- Stiffeners – Rigid sections can be added for mounting components.
- Coverlay/Mask – Covers expose traces for protection. More expensive than solder mask.
- Adhesives – Bond flex layers together. Can be acrylic or epoxy based.
Fabrication Processes
- Number of layers – Costs increase with more layers. 2-6 layers are typical.
- Line width/spacing – Narrow width and spacing require tighter tolerances.
- Hole sizes – Smaller microvias and holes require advanced lasers.
- Tolerances – Tighter tolerances require more precision and cost.
- Bending zones – Flex-to-rigid transitions require special processing.
- Solder mask – LPI solder masks are smoother but more expensive.
- Surface finish – Immersion silver, gold or ENIG add cost for wear protection.
- Legend printing – Printed markings for labels, logos and assembly notes.
- Testing – Testing for continuity, shorts and opens ensures quality.
Order Size, Prototyping and Tooling
- Quantity – Unit price drops significantly at higher order volumes.
- Prototyping – Low volume or custom runs increase costs.
- Tooling – Reuse of existing tools reduces setup costs.
- NRE Costs – Design, engineering and testing expenses may apply.
Let’s take a closer look at how some of these factors influence overall flexible PCB pricing.
How Board Size Affects Cost
In general, larger boards will have a higher base cost. The fabrication facility charges by the square inch for processing panels. Larger boards take up more panel space. One 4″ x 6″ board will have a lower raw cost than five 2″ x 2″ boards of the same stackup.
However, as board size increases, quantity pricing achieves better economy of scale. The graph below shows an example of how size factors into quantity pricing per square inch:
Board Size (in²) | 5 pieces ($/in²) | 10 pieces ($/in² ) | 50 pieces ($/in²) | 100 pieces ($/in²) |
---|---|---|---|---|
4 x 6 = 24 in² | $25 | $20 | $12 | $8 |
2 x 2 = 4 in² | $45 | $40 | $18 | $15 |
6 x 6 = 36 in² | $22 | $18 | $10 | $6 |
So while the base cost is higher for larger boards, the cost per square inch drops dramatically at higher quantities due to efficiency gains in manufacturing.
Layer Count Pricing
Adding additional conductive layers to a flexible PCB increases costs in materials, lamination and processing. Each layer adds alignment accuracy challenges as well. Below is an approximate cost increase for each layer added to the stackup:
Layer Count | Cost Increase |
---|---|
Single Layer | Baseline |
Double Layer | 15-20% |
4 Layers | 50-60% |
6 Layers | 80-100% |
8 Layers | 130-150% |
As you can see, there are diminishing returns for adding layers, as complexity and processing requirements compound. 4 layer flex boards offer the best balance of cost versus layout capability for many applications.
Comparing Rigid-Flex PCB Costs
When rigid sections are combined with flex circuits into a rigid-flex PCB, additional processing steps are required. The rigid sections are typically standard FR4 PCB laminates that integrate with the flex layers. Here is a comparison of a 4 layer all-flex board to a 2 layer flex + 2 layer rigid stackup:
Parameter | 4 Layer Flex | 2 Layer Flex + 2 Layer Rigid |
---|---|---|
Layers | 4 Layer Polyimide | 2 Layer Polyimide + 2 Layer FR4 |
Fabrication | Flex PCB Only | Flex PCB + Rigid PCB |
Connections | Layer Alignment | Precision Flex-Rigid Transition |
Cost | Base Flex Cost | Base Flex Cost + $200-500+ |
The rigid sections add $200-500 typically to the base cost of the equivalent all-flex board. The additional cost covers attaching the rigid sections to the flex circuit and ensuring reliable connections.
Prototyping Versus Production Costs
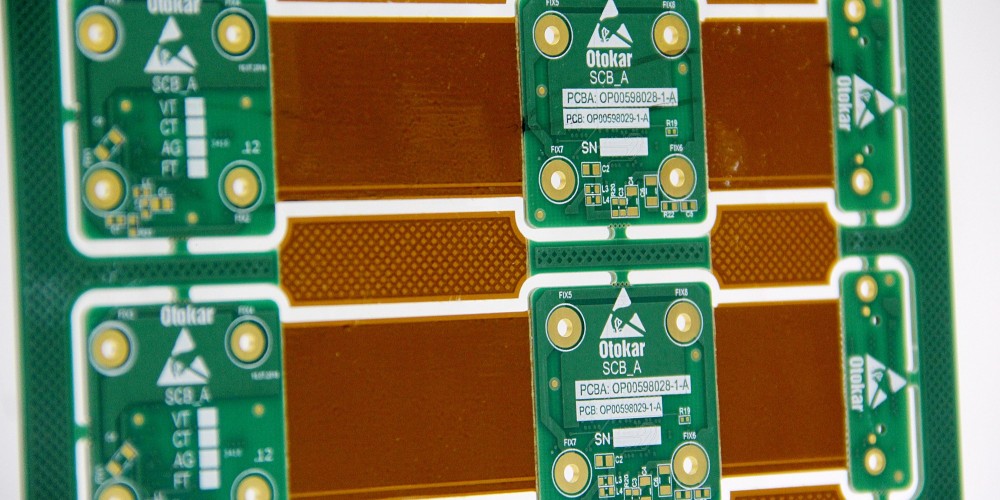
When calculating flexible PCB costs, keep in mind that prototype and low volume orders will be priced higher than production runs. Economies of scale apply as volume increases. Some typical volume thresholds:
Order Volume | Description | Cost Impact |
---|---|---|
1-25 units | Prototype Quantities | Highest per unit cost |
25-100 units | Low Volume | Moderate cost reduction |
100-500 units | Medium Volume | Significantly lower cost |
500+ units | High Volume Production | Maximum cost savings |
Prototype runs don’t benefit from production tooling, processing and material ordering efficiency. Allow for 3-4 week lead times on prototypes. Production orders achieve maximum efficiency at 5,000+ units when dedicated tooling is justified.
Flexible PCB Cost Estimator Tools
To get accurate flexible PCB pricing tailored to your design requirements, it is best to get quotes from potential vendors. Many flex PCB manufacturers provide online cost calculator tools on their websites. These let you input your board specs and quantity to get an estimated price and lead time.
When collecting cost estimates, be sure to get quotes from at least 2-3 vendors to compare pricing. Some things to consider are:
- Make sure all vendors are quoting based on the same specifications
- Confirm if tooling and NRE costs are included or additional
- Ask about lead times to match your development schedule
- Review each vendor’s capabilities and quality certifications
- Consider overall cost, not just board pricing
- Get references for vendors when possible
With a good process for quoting, you’ll be able to find the best value flexible PCB manufacturer for your particular design needs.
Tips for Optimizing Flexible PCB Costs
Here are some helpful tips for keeping flexible PCB costs down in your next project:
- Build prototypes with the simplest design that verifies functionality. Complexity can come later.
- Use spacing/widths at the high end of vendor capabilities when layout permits.
- Choose polyimide material in standard 1 mil, 2mil or 3mil thicknesses.
- Implement just enough layers for required connectivity (2-4 typical).
- Combine small boards into panel arrays for efficiency.
- Reuse existing specifications like thickness, copper weight, and tolerance from previous designs if possible.
- Partner with vendors early in design process for advice on optimization.
- Compare vendor quotes to find the best value flex PCB maker.
- Plan board layouts with ease of assembly and test in mind.
With careful design considerations and good communication with your flex PCB vendor, you can keep costs low without sacrificing quality and reliability.
Frequently Asked Questions
What are some typical base costs for simple flex boards?
For simple 2-4 layer flex boards sized at 4″x 6″ or smaller without special requirements, base costs typically range from $100-300 for 5-10 pieces, and $50-150 for volumes of 100. Actual pricing depends on the specs.
What design factors contribute most to increased costs?
The number one drivers of increased costs are additional layers and smaller line width/spacing. High layer counts increase complexity exponentially, as do advanced tolerances below 5 mil line and space.
How much does flex-to-rigid interface design add to cost?
Expect an additional $200-500 on base price for incorporating rigid sections into flex designs. Careful interface engineering is needed for reliability.
Can costs be estimated without getting direct vendor quotes?
It’s very difficult to estimate pricing accurately without engaging vendors directly. Every project has unique specifications that dramatically impact cost. Quotes from at least 2-3 vendors are recommended.
How can I reduce costs by optimizing the CAD layout?
Simplifying layer count, maximizing spacing/widths, optimizing board size, and using panelization can help reduce cost from the layout stage. Work with your vendor to identify optimization opportunities.
Conclusion
Flexible PCBs enable innovative and compact product designs, but also require careful cost planning due to their specialized materials and fabrication processes. By understanding the key factors that influence cost such as materials, layer count, order volume and interface complexity, designers can develop cost effective flex circuits for their products. Partnership and early collaboration with potential flex PCB vendors is crucial to optimizing design for functionality, quality and affordability. With the right design approach and vendor selection, the unique benefits of flex PCB technology can be leveraged without blowing budgets.