404 13:16:55
Types of PCBs: A Comprehensive Guide
Printed Circuit Boards (PCBs) are the backbone of modern electronics. They provide the mechanical support and electrical connections necessary for electronic components to function. PCBs are used in a wide range of applications, from simple consumer electronics to complex aerospace systems. Over the years, the technology behind PCBs has evolved significantly, leading to the development of various types of PCBs, each designed to meet specific requirements. In this article, we will explore the different types of PCBs, their characteristics, and their applications.
1. Single-Sided PCBs
Overview
Single-sided PCBs are the simplest and most basic type of printed circuit board. They consist of a single layer of substrate material, typically fiberglass, with a thin layer of conductive material, usually copper, on one side. The components are mounted on one side, and the conductive traces are etched onto the opposite side.
Characteristics
- Single Layer: Only one layer of conductive material.
- Simple Design: Easy to design and manufacture.
- Cost-Effective: Lower production costs due to simplicity.
- Limited Complexity: Suitable for simple circuits with fewer components.
Applications
Single-sided PCBs are commonly used in simple electronic devices where the circuit complexity is low. Examples include:
- Calculators
- Power supplies
- LED lighting
- Basic consumer electronics
2. Double-Sided PCBs
Overview
Double-sided PCBs have conductive layers on both sides of the substrate. The two layers are connected using through-hole vias, which allow electrical signals to pass from one side to the other. This type of PCB offers more flexibility in design compared to single-sided PCBs.
Characteristics
- Two Layers: Conductive material on both sides of the substrate.
- Increased Complexity: Allows for more complex circuits.
- Through-Hole Vias: Connections between layers are made using vias.
- Moderate Cost: More expensive than single-sided PCBs but still cost-effective.
Applications
Double-sided PCBs are used in a wide range of applications, including:
- Automotive electronics
- Industrial controls
- Power converters
- Consumer electronics with moderate complexity
3. Multi-Layer PCBs
Overview
Multi-layer PCBs consist of three or more layers of conductive material, separated by insulating layers. These layers are interconnected using vias, which can be through-hole, blind, or buried. Multi-layer PCBs are used in highly complex circuits where space and performance are critical.
Characteristics
- Multiple Layers: Three or more conductive layers.
- High Complexity: Suitable for complex circuits with many components.
- Enhanced Performance: Better signal integrity and reduced electromagnetic interference (EMI).
- Higher Cost: More expensive to design and manufacture due to increased complexity.
Applications
Multi-layer PCBs are used in advanced electronic systems, such as:
- Smartphones and tablets
- Computers and servers
- Medical devices
- Aerospace and defense systems
4. Rigid PCBs
Overview
Rigid PCBs are made from a solid, inflexible substrate material, typically fiberglass. They are the most common type of PCB and are used in applications where the board needs to maintain its shape and provide strong mechanical support.
Characteristics
- Inflexible: The board does not bend or flex.
- Durable: Provides strong mechanical support.
- High Density: Can accommodate a high number of components.
- Wide Range of Applications: Used in various industries.
Applications
Rigid PCBs are used in a wide range of applications, including:
- Consumer electronics
- Industrial equipment
- Automotive systems
- Medical devices
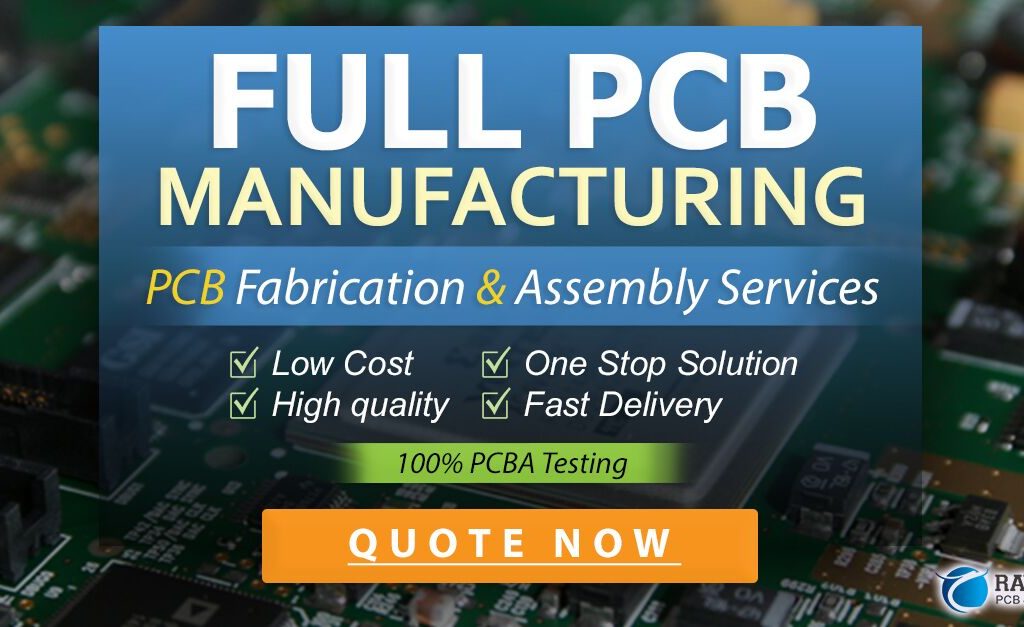
5. Flexible PCBs
Overview
Flexible PCBs, also known as flex circuits, are made from flexible substrate materials such as polyimide. They can bend and flex, making them ideal for applications where the board needs to conform to a specific shape or fit into tight spaces.
Characteristics
- Flexible: Can bend and flex without breaking.
- Lightweight: Lighter than rigid PCBs.
- Space-Saving: Can fit into tight spaces and conform to unique shapes.
- Durability: Resistant to vibration and shock.
Applications
Flexible PCBs are used in applications where space and weight are critical, such as:
- Wearable electronics
- Medical devices
- Aerospace systems
- Automotive electronics
6. Rigid-Flex PCBs
Overview
Rigid-flex PCBs combine the benefits of both rigid and flexible PCBs. They consist of multiple layers of rigid and flexible substrates, interconnected to form a single circuit board. This type of PCB offers the mechanical stability of rigid boards and the flexibility of flex circuits.
Characteristics
- Combination of Rigid and Flexible: Offers both rigidity and flexibility.
- High Density: Can accommodate a high number of components.
- Space-Saving: Can fit into tight spaces and conform to unique shapes.
- Complex Design: More complex to design and manufacture.
Applications
Rigid-flex PCBs are used in applications that require both mechanical stability and flexibility, such as:
- Military and aerospace systems
- Medical devices
- High-end consumer electronics
- Industrial equipment
7. High-Frequency PCBs
Overview
High-frequency PCBs are designed to operate at high frequencies, typically above 1 GHz. They are used in applications where signal integrity and low signal loss are critical. These PCBs are made from specialized materials that have low dielectric loss and high thermal stability.
Characteristics
- High-Frequency Operation: Designed for frequencies above 1 GHz.
- Low Signal Loss: Minimizes signal loss at high frequencies.
- Specialized Materials: Uses materials with low dielectric loss and high thermal stability.
- Complex Design: Requires careful design to maintain signal integrity.
Applications
High-frequency PCBs are used in applications that require high-speed signal transmission, such as:
- RF and microwave circuits
- Telecommunications
- Satellite systems
- Radar systems
8. Aluminum-Backed PCBs
Overview
Aluminum-backed PCBs, also known as metal-core PCBs, have a layer of aluminum as the base material. The aluminum layer provides excellent thermal conductivity, making these PCBs ideal for applications that generate a lot of heat.
Characteristics
- Thermal Conductivity: Excellent heat dissipation.
- Durability: Provides strong mechanical support.
- Lightweight: Lighter than traditional PCBs with heat sinks.
- Cost-Effective: Lower cost compared to other thermal management solutions.
Applications
Aluminum-backed PCBs are used in applications that require efficient heat dissipation, such as:
- LED lighting
- Power supplies
- Automotive electronics
- Industrial equipment
9. Ceramic PCBs
Overview
Ceramic PCBs are made from ceramic materials such as alumina, aluminum nitride, or beryllium oxide. These materials offer excellent thermal conductivity, electrical insulation, and mechanical strength. Ceramic PCBs are used in high-temperature and high-power applications.
Characteristics
- High Thermal Conductivity: Excellent heat dissipation.
- Electrical Insulation: Provides high electrical insulation.
- Mechanical Strength: Strong and durable.
- High-Temperature Resistance: Can withstand high temperatures.
Applications
Ceramic PCBs are used in high-temperature and high-power applications, such as:
- Power electronics
- Aerospace systems
- Medical devices
- High-power LED lighting
10. High-Density Interconnect (HDI) PCBs
Overview
High-Density Interconnect (HDI) PCBs are designed to accommodate a high number of components in a small area. They use advanced manufacturing techniques such as microvias, blind vias, and buried vias to achieve high circuit density. HDI PCBs are used in applications where space is limited, and high performance is required.
Characteristics
- High Circuit Density: Accommodates a high number of components in a small area.
- Advanced Manufacturing: Uses microvias, blind vias, and buried vias.
- Enhanced Performance: Improved signal integrity and reduced EMI.
- Complex Design: Requires advanced design and manufacturing techniques.
Applications
HDI PCBs are used in applications that require high performance and miniaturization, such as:
- Smartphones and tablets
- Wearable electronics
- Medical devices
- Aerospace and defense systems
11. Backplane PCBs
Overview
Backplane PCBs are used to connect multiple PCBs together in a system. They provide a backbone for the system, allowing different boards to communicate with each other. Backplane PCBs are typically used in large electronic systems such as servers, telecommunications equipment, and industrial control systems.
Characteristics
- High Connectivity: Connects multiple PCBs together.
- Robust Design: Designed to handle high data rates and power levels.
- Large Size: Typically larger than other types of PCBs.
- Complex Design: Requires careful design to ensure reliable connections.
Applications
Backplane PCBs are used in large electronic systems, such as:
- Servers and data centers
- Telecommunications equipment
- Industrial control systems
- Military and aerospace systems
12. LED PCBs
Overview
LED PCBs are specifically designed for LED applications. They provide the necessary thermal management and electrical connections for LED components. LED PCBs are typically made from materials with high thermal conductivity, such as aluminum or ceramic.
Characteristics
- Thermal Management: Excellent heat dissipation for LED components.
- High Conductivity: Provides efficient electrical connections.
- Durability: Designed to withstand the thermal stress of LED operation.
- Cost-Effective: Lower cost compared to other thermal management solutions.
Applications
LED PCBs are used in various LED applications, such as:
- LED lighting
- Automotive lighting
- Display panels
- Signage
Conclusion
PCBs are an essential component of modern electronics, and the type of PCB used can significantly impact the performance, reliability, and cost of an electronic device. From simple single-sided PCBs to complex multi-layer and HDI PCBs, each type has its own set of characteristics and applications. Understanding the different types of PCBs and their unique features is crucial for designing and manufacturing electronic systems that meet the specific requirements of various industries.
As technology continues to advance, we can expect to see further innovations in PCB design and manufacturing, leading to even more specialized types of PCBs that push the boundaries of what is possible in electronics. Whether you are designing a simple consumer device or a complex aerospace system, choosing the right type of PCB is essential for achieving the desired performance and reliability.