Rigid flex PCBs, also known as rigid flexible printed circuit boards, are circuit boards that consist of rigid and flexible substrates laminated together. They provide solutions for applications that require dynamic flexing, bending or folding while maintaining electronic interconnections. As the name suggests, rigid flex PCBs provide the benefits of having both rigid and flexible PCBs in one design.
When evaluating PCB solutions, cost is often a primary concern. Rigid flex PCBs provide unique advantages, but can come at a higher initial cost compared to alternatives. This article will examine the key factors that influence the cost of rigid flex PCBs to provide a better understanding of what drives pricing.
What is a Rigid Flex PCB?
A rigid flex PCB combines rigid FR-4 boards with flexible polyimide films bonded together with acrylic adhesives. The rigid sections provide mechanical support and mounting platforms, while the flexible sections allow dynamic movement and three-dimensional configuration.
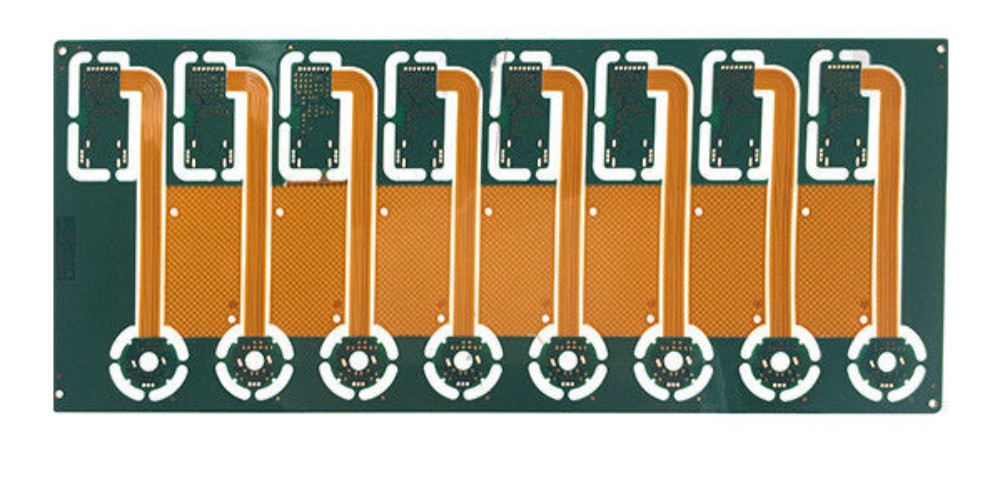
Rigid flex PCB combining rigid FR-4 and flexible polyimide
Rigid flex PCBs open new possibilities in electronic device design by:
- Allowing flexible couplings between different rigid circuit board areas
- Enabling devices to conform to unique mechanical housings
- Supporting dynamic flexing motions in use
- Providing shock absorption and vibration resistance
Common applications include aerospace systems, medical devices, wearables, robotics, folding displays, and more.
Cost Factors for Rigid Flex PCBs
The costs of rigid flex PCBs are driven by a number of factors that must be considered when budgeting for a new design. Key factors include:
1. Board Complexity
As with any PCB, design complexity impacts cost. Complexity factors include:
- Number of layers
- Board thickness
- Component density
- Trace routing complexity
- High frequency considerations
- Impedance control requirements
- Stackup configuration
- Fine features/tolerances
More complex rigid flex designs require additional fabrication processing steps and more advanced materials, driving up costs.
2. Board Size/Area
Larger rigid flex PCB sizes have higher material costs. Flexible materials in particular can become expensive for very large designs.
3. Bend Radii
Smaller bend radii require special flexible materials and processing, increasing cost. The flex sections must be properly designed with suitable bend radii to avoid overstressing.
4. Layer Count
Rigid flex PCB costs are impacted by total layer count, which includes both rigid and flex layers. More layers require additional materials, processing, and lamination steps.
5. Stiffener Requirements
Stiffeners may be required for certain designs. Stiffeners and support inserts add cost for the additional materials and integration.
6. Special Materials
Unique material requirements drive cost upward. This includes high frequency materials, non-standard flex films, adhesives, and laminates.
7. Advanced Finishes
Special finishes like gold plating or coatings add cost compared to standard finishes.
8. High Density Interconnects (HDI)
Dense designs using microvias and other HDI features often necessitate additional process steps, increasing fabrication complexity and cost.
9. Tooling and NRE Costs
Non-recurring engineering (NRE) costs include any upfront design, prototyping, or tooling charges by the PCB manufacturer.
10. Order Quantity
As with any PCB, increased order quantities drive down overall per unit costs due to efficiencies in manufacturing.
Cost Saving Tips for Rigid Flex
Here are some tips to help reduce rigid flex PCB costs for your next design:
- Optimize layer count – Minimize layers whenever possible. Balance layer needs with via costs.
- Design panels efficiently – Panelize boards to maximize material usage and reduce waste.
- Standardize materials – When possible, use standard materials versus exotic flex films or laminates.
- Relax tolerances – Open tolerances as much as allowed by the design to leverage standard fab processes.
- Simplify layer stackup – Minimize lamination cycles by optimizing the construction sequence.
- Consider flex-rigid-flex – Can potentially reduce cost compared to full rigid-flex construction.
- Scale flex areas judiciously – Size flex areas to requirements – larger flex drives costs.
- Standardize on finish – Avoid special finishes whenever standard finishes will suffice.
- Evaluate crew vs. laser cutting – Crew cutting can potentially lower cost in some cases.
- Leverage design guidelines – Follow manufacturer design rules to avoid unnecessary cost additions.
- Evaluate partial flex – Weigh tradeoffs of partial flex versus full rigid-flex construction.
- Consult with your PCB partner – Work with your fabricator to identify opportunities to optimize cost.
Estimating Rigid Flex PCB Costs
With many variables at play, it can be challenging to estimate rigid flex PCB costs. In general:
- Rigid flex will carry a cost premium over rigid PCBs due to additional materials and processes.
- The cost premium depends greatly on the design complexity and requirements.
- For simpler rigid flex designs, the cost may be 2X-3X the price of an equivalent rigid PCB.
- For highly complex rigid flex, the multiplier can be 5X or greater compared to rigid.
- NRE/tooling costs typically range from $1500 to $5000 for rigid flex.
To get accurate pricing, it’s best to work directly with a rigid flex PCB manufacturer. They can provide detailed quotes tailored to your specific design’s parameters and expected order volumes. Be sure to communicate all of your requirements upfront.
Many fabricators offer free rigid flex PCB quoting services, enabling you to get budgetary estimates before fully committing to a design. Take advantage of these services early in your design process to inform cost-driven decisions.
Cost Comparison: Rigid Flex PCB vs. Alternatives
While rigid flex PCB technology provides unique benefits, it’s not the only solution for every application requiring flexibility and dynamics. Lower-cost alternatives exist.
Here is a brief comparison against some other approaches:
Method | Pros | Cons | Relative Cost |
---|---|---|---|
Rigid Flex PCB | High reliability, excellent performance, layout flexibility | Higher cost, longer lead times | 2X-5X+ vs. rigid PCB |
Flexible Printed Circuits (FPC) | Very low cost, unlimited flexibility | Limited features, challenging component mounting | 20-50% of rigid flex cost |
Traditional Cabling | Simple, unlimited flexibility | Bulky, prone to failure, impedance issues | Lower cost than PCBs |
Rigid PCB + Connectors | Well-established, moderate cost | Bulky, lower reliability than rigid flex | 1.5X rigid PCB cost |
For many applications, the benefits of rigid flex PCB technology justify the higher initial price over these alternatives. But for simpler use cases where flexibility is not as demanding, lower-cost solutions may suffice.
Factors That May Increase Rigid Flex PCB Costs
Here are some application requirements that could potentially drive rigid flex PCB costs higher:
- Very high layer counts (>12-18 layers)
- Numerous small bend radii (under 3mm)
- Dense HDI interconnects (microvias, etc.)
- High layer-to-layer registration accuracy demands
- Extreme environment use requirements
- Maximum frequency demands (50+ GHz)
- Impedance tolerances under +/- 5%
- Gold or other exotic finishing
- Small production volumes (<100 units)
- Very large panel sizes
- Extremely tight lead time requirements
Designs incorporating multiple of these factors will likely fall on the higher end of the cost spectrum. Carefully evaluate where you can make tradeoffs to help control overall expenditures.
Optimizing Cost Through Design Choices
To recap, here are some ways to optimize rigid flex PCB cost through smart design choices:
- Simplify layer stackup construction
- Standardize materials whenever possible
- Scale rigid sections and flex areas appropriately
- Reduce layer count by consolidating plane layers
- Relax tolerances and use thicker trace/space rules
- Minimize the number of bends
- Increase bend radii to reduce special flex materials
- Avoid any unnecessary finishes
- Panelize efficiently to maximize material usage
- Standardize on cost-effective flex laminates
- Reduce stiffener requirements where possible
Your PCB design partner can provide guidance to help implement these cost optimization measures without sacrificing required performance.
Long-Term Cost Savings of Rigid Flex PCBs
While rigid flex PCB fabrication carries higher initial cost, there are ways it can reduce total long-term expenses and provide value:
Space/Weight Savings
Consolidating rigid and flex PCBs into one integrated design minimizes weight and saves internal space compared to connectors and cables. This is especially impactful in aerospace, defense, and portables.
Reliability Improvements
Rigid flex PCB construction enhances reliability and product longevity compared to cabling or connectors. The design is less prone to cracking or detachment during use.
Assembly Cost Reduction
Combining the rigid and flex PCBs eliminates interconnect components, reducing overall assembly costs and streamlining manufacturing.
Single Supplier
Procuring the complete rigid flex PCB from one manufacturer simplifies procurement andavoids multi-sourcing complexities.
Design Optimization
Rigid flex PCBs enable performance benefits and design optimization unachievable through other means. This added value may justify the cost premium for many applications.
While cost is key, be sure to analyze total system cost savings enabled by rigid flex PCB technology when making design decisions. The value over the product lifecycle often offsets the higher initial fabrication costs.
Conclusion
Rigid flex PCBs provide an advanced solution to integrate rigid boards and dynamic flex circuits, but come at a cost premium versus traditional rigid PCBs. Cost is driven by design complexity factors such as layer count, features/tolerances, special materials needs, and order quantities.
By optimizing the design, standardizing materials, scaling requirements judiciously, and leveraging cost-reduction tips, you can help minimize overall rigid flex PCB expenses. Rigid flex technology also enables long-term value through space/weight savings, improved reliability, easier assembly, and performance benefits.
To determine accurate pricing for your particular rigid flex PCB application and order quantity, obtain quotes from a rigid flex fabrication partner early in your design process. This enables properly budgeting for your project, and identifying opportunities to control costs while meeting design requirements.
Rigid Flex PCB Costs FQA
Q: Is rigid flex PCB technology worth the additional cost?
A: Rigid flex PCBs justify their typically higher cost through space/weight savings, improved reliability, design optimization, and other benefits. For applications not requiring maximum flexibility and dynamics, lower-cost alternatives may be suitable. Evaluate tradeoffs between technology cost vs. benefits.
Q: Can costs be estimated before the design is finished?
A: Yes, experienced rigid flex PCB manufacturers can provide budgetary estimates based on your initial design requirements, flex circuit areas, and order quantities. These early estimations help guide cost considerations.
Q: What are key ways to reduce layer count?
A: Careful stackup planning to consolidate plane layers, balancing layer needs with via costs, and minimizing crossovers through good routing practices.
Q: How much does designing with HDI features increase rigid flex PCB cost?
A: Depends on extent of use, but implementing dense interconnects with microvias can potentially double the fabrication cost over standard density designs.
Q: Is panelization less important for cost savings with rigid flex PCBs?
A: No, effective panel design is still critical for material utilization and cost reduction. Rigid flex panelization does have unique considerations.