Introduction
Printed circuit boards (PCBs) are essential components in almost all modern electronics. They provide the foundation on which components are mounted and connected together with conductive tracks. While rigid PCBs are commonly used, flex PCBs provide unique advantages, especially as electronics become smaller, lighter and more portable.
Advanced Circuits is a leading PCB manufacturer providing custom flex PCB solutions. This article will examine what makes their flex PCBs advanced, the key benefits, and typical applications.
What Makes Advanced Circuits Flex PCBs Advanced?
Advanced Circuits utilizes the latest flex PCB technology and manufacturing processes to create high-quality flex circuits. Here are some of their key advantages:
Precision Manufacturing
Flex PCBs require specialized machinery and processes. Advanced Circuits uses advanced photolithographic processes to produce fine line traces and spaces down to 2 mils. This allows for higher circuit density in a smaller space.
Tight Tolerances
With flex PCBs, dimensional stability is critical. Advanced Circuits holds extremely tight tolerances of ±0.10mm ensuring reliable connectivity and layer-to-layer registration.
High Layer Count
Advanced Circuits can produce flex PCBs with up to 12 conductive layers. Having more layers allows for increased circuit complexity and component density.
Fine Line Traces
With trace and space capabilities down to 2 mils, Advanced Circuits can produce very fine line flex PCBs for high density interconnections.
Advanced Materials
From flexible polyimide to rigid FR4 substrates, Advanced Circuits uses advanced materials engineered for optimal mechanical, electrical and thermal performance.
Design Support
Their engineering team provides design-for-manufacturing support and guidelines tailored to flex PCBs throughout the design and development process.
Testing and Certification
They conduct complete electrical testing and quality assurance inspections on all flex PCB orders. Their facilities are ISO 9001:2015 certified.
Key Benefits of Using Advanced Circuits Flex PCBs
There are several important benefits to using flex PCBs from Advanced Circuits:
Flexibility and Motion
Flex circuits can bend, fold and flex repeatedly. This makes them ideal for dynamically moving applications like wearables, robotics and automotive.
Lightweight and Compact
With very thin dielectric layers, flex PCBs are lightweight and take up less space versus rigid boards. This helps minimize the overall product weight and footprint.
Reliability
The flexible material absorbs vibration and shock that can damage solder joints. This improves reliability in motion applications.
Complex and 3D Assembly
Flex circuits can be folded and formed into complex 3D configurations not possible with rigid boards.
High Density
Thin, flexible boards with fine features allow for increased component density and miniaturization.
Lower Assembly Costs
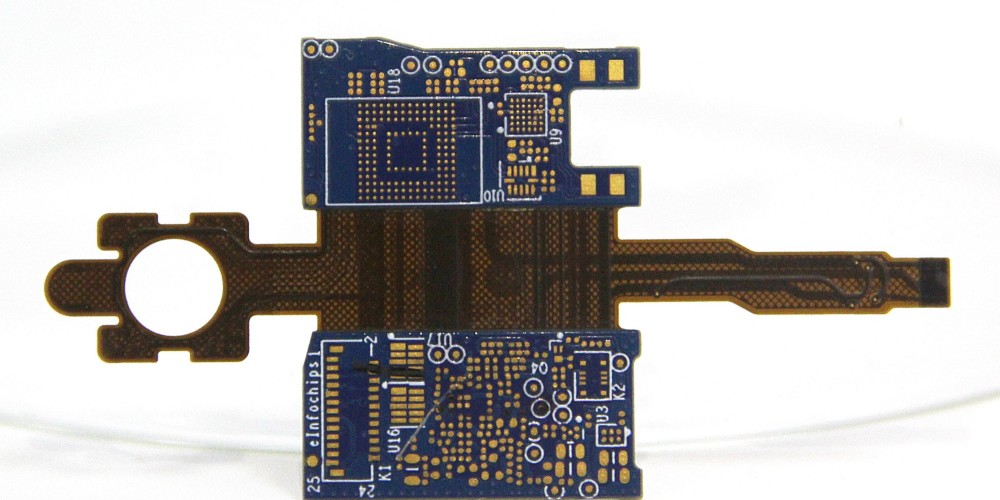
Fewer connectors and simpler assembly steps reduce overall assembly time and costs.
Typical Applications for Advanced Circuits Flex PCBs
Here are some common applications that benefit from using Advanced Circuits flex PCB technology:
Wearable Electronics
For smart watches, fitness trackers, smart glasses and VR headsets. The compact design and flexibility are ideal for conforming to the human body.
Medical Devices
For ultrasound transducers, insulin pumps, digital imaging sensors and implantable devices. Flex circuits provide reliability and size benefits.
Consumer Electronics
Miniaturized consumer products like cameras, mobile phones and display screens utilize flex PCBs.
Automotive Electronics
Accelerometer sensors, engine control modules and in-vehicle entertainment rely on flex circuits to withstand vibration, shock and extreme temperatures.
Robotics and UAVs
The tight folds, dynamic flexibility and high density help maximize functionality in the limited space of robots and UAVs.
Aerospace and Military
Rugged flex circuits withstand G forces and thermal stresses in guidance systems, radars and avionics.
Flex PCB Design Considerations
Designing and specifying flex PCBs comes with some important considerations:
- Flexibility – Avoid sharp folds and tear drops. Maximize dynamic bending capabilities with large bend radii.
- Layer Stackup – Use thicker dielectric layers towards the center, thinner dielectrics to the outer layers. Include stiffeners if needed.
- Component Placement – Strategically place components for optimal flexibility, weight distribution and density.
- Trace Routing – Route traces to direct motion along or perpendicular to traces to reduce stress. Avoid traces over folds.
- Board Stiffness – Reinforce areas with cover layers, bondplies or stiffeners to provide sufficient support.
- ESD Protection – Use proper grounding, shielding and insulation to protect from electrostatic discharge.
- Thermal Management – Ensure heat generating components are properly vented or cooled.
Addressing these considerations early in the design process helps ensure reliable, high-performing flex PCBs.
Ordering Advanced Circuits Flex PCBs
Ordering flex PCBs from Advanced Circuits is fast and simple:
- Design File – Submit Gerber files, schematics, drawings, bill of materials and assembly instructions.
- Engineering Review – Their engineering team reviews the design for DFM and makes recommendations.
- Instant Online Quote – Upload the design to get an instant online quote for flex PCB manufacturing.
- Flexible Order Options – Choose standard lead times from 2 to 10 days or expedited shipping.
- Manufacturing and Testing – They precisely manufacture your design using the latest flex PCB technology and test thoroughly.
- Delivery – Orders ship directly to you with standard or expedited delivery options.
With over 30 years of experience, Advanced Circuits has the technical expertise and capabilities to manufacture high quality, advanced flex PCB solutions.
Frequently Asked Questions
Here are some common questions about Advanced Circuits flex PCB technology:
Q: What types of substrates do they offer?
A: They can manufacture on polyimide, polyester, LCP and rigid FR4 substrates. Polyimide is most common providing excellent flexibility and temperature resistance.
Q: What design software do they support?
A: They accept Gerber files from all leading PCB design software packages including Altium, Cadence, Eagle, and OrCAD.
Q: How small of traces and spaces can they produce?
A: Their capabilities range down to 2 mil lines and spaces. Ultra-fine line flex PCBs are used for high density interconnections.
Q: Can both rigid and flex layers be combined?
A: Yes, rigid-flex PCBs utilize both flexible substrates and rigid FR4 substrates allowing components to be mounted across both sections.
Q: Do they only produce simple 2 layer flex boards?
A: No, they can manufacture complex multilayer boards with up to 12 conductive layers, involving multiple flex and rigid sections.
Conclusion
Advanced Circuits leverages 30+ years of flex PCB manufacturing expertise and advanced technology to produce high-quality flex circuits with tight tolerances, fine features and complex designs. Their flex PCBs offer unique advantages of flexibility, lightweight, reliability and miniaturization that open new possibilities in electronic product design. With quick-turn prototyping and cost-effective production, Advanced Circuits helps take innovative products from concept to reality.