Introduction
Flexible printed circuit boards (flex PCBs) are a vital component in many of today’s electronic devices. Choosing the right flex PCB manufacturer is key to getting high quality, reliable flexible circuits boards delivered on time and within budget. This guide covers the capabilities to look for when selecting a flex PCB production partner.
Flex PCB Manufacturing Capabilities
The ideal flex circuit vendor will have expertise across the full range of specialized manufacturing processes involved:
Circuit Printing
The manufacturer should utilize advanced printing methods to pattern fine line traces and spaces on flexible substrates. Common techniques include:
- Photolithography: Light sensitive photoresists and masks to transfer circuit patterns onto substrates. Allows very high resolution patterning.
- Screen Printing: Squeegee pushes conductive ink through a stencil onto the substrate. Lower resolution but simple and low cost.
- Inkjet Printing: Conductive inks directly printed to precise locations without masks. Lower initial investment than photolithography.
Metal Plating
Copper traces are often plated to achieve desired thickness, coatings and connectivity:
- Copper Plating: Electrolytic copper builds up trace thickness.
- Tin-Lead Plating: Provides solderability for component terminals.
- Gold Plating: Improves conductivity and corrosion resistance.
- Nickel Plating: Undercoating to provide adhesion and barrier properties.
Process | Description |
---|---|
Photolithography | High resolution printing using photoresists and masks |
Screen Printing | Conductive ink forced through stencil |
Inkjet Printing | Direct printing of traces without masks |
Copper Plating | Electrolytic copper plating of traces |
Tin-Lead Plating | Coating for solderability |
Gold Plating | Corrosion resistance and conductivity |
Nickel Plating | Adhesion layer and diffusion barrier |
Layer Lamination
Combining multiple circuit layers expands possibilities and requires reliable adhesive bonding:
- Adhesive Lamination: Bonds layers with heat activated adhesive films.
- Thermal Bonding: Layers fused together under heat and pressure.
Circuit Singulation
Individual circuits must be precision cut from panel substrates:
- Die Cutting: Steel rule or rotary dies slice circuits apart.
- Laser Cutting: Precise, narrow cut lines.
- Punching: Mechanical punches penetrate substrate.
Testing and QC
- Visual Inspection: Microscope examination of circuits.
- Dimensional Analysis: Confirmation of trace sizes, distances and features.
- Electrical Testing: Validating proper connectivity and function.
- Environmental Testing: Exposing circuits to stress factors like temperature, humidity and vibration.
A capable manufacturer will leverage these processes to fabricate high quality flex circuits targeted to the customer’s application.
Provider Sourcing and Locations
There are quality flex PCB producers located across the global electronics supply chain:
United States
The US is home to a number of specialized, domestic flex PCB manufacturers including large corporations and smaller shops. Benefits include close proximity, direct communication and access to ITAR military and defense contracts.
China
Many flex circuit producers have manufacturing sites located in China. These offshore facilities offer competitive pricing attractive to high volume consumer electronics production. Quality levels vary significantly among Chinese suppliers.
Other Asian Countries
Taiwan, Japan and South Korea also have reputable flex PCB manufacturers with capabilities on par with American firms. These can provide regional options.
Selecting flex circuit vendors across multiple geographic regions gives flexibility in the supply chain. However, customers should directly audit and qualify any offshore manufacturers to ensure their capabilities and quality levels meet expectations.
Volume Production Capabilities
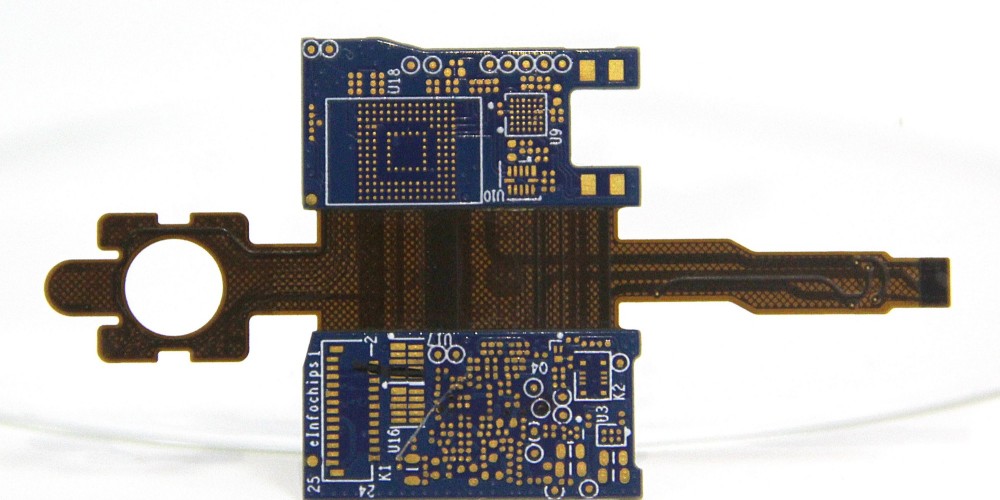
Another vital aspect is the ability to scale up for volume production. Manufacturing large quantities efficiently requires optimized processes. Considerations include:
- Facilities: The supplier’s factories and cleanrooms should support mass production.
- Panel Size: Manufacturing from larger panel substrates improves panel utilization and efficiency.
- Automation: Production machinery should be automated for speed, precision and repeatability.
- Changeovers: Procedures must allow quick changeovers between different circuit designs.
- Yields: Manufacturing processes should consistently produce high functioning yield rates.
- Testing: Electrical, functional and quality control testing capacity must keep pace with output volumes.
- Personnel: Sufficient staffing of qualified operators, technicians and engineers.
Mature flex PCB companies will invest in the above capabilities to facilitate profitable high volume manufacturing.
Design Support Services
The earliest engagement between your engineering team and the manufacturer during design and prototyping will pay significant dividends later in avoiding errors and delays. Consider needs like:
Design Reviews
Experienced engineers can review circuit designs and provide feedback before layouts are finalized. This allows catching issues that could impact manufacturability early on.
DFM Guidance
Many specialized design rules and layout tricks apply for optimal flexible PCB fabrication. Manufacturers can provide design for manufacturing (DFM) assistance so circuits are designed for quality and yield.
Prototyping
Rapid prototyping services validate designs prior to full production. This avoids costly revisions later on.
Testing
Testing and validation of prototypes under temperature, dynamic flexing and other environmental conditions.
Data Formats
Compatibility with your design software outputs (Gerber, DXF, IPC-2581, etc) ensures smooth data handoff.
Choose a manufacturer that offers detailed design assistance and reviews throughout development, not just manufacturing.
Ordering, Delivery and Logistics
For smooth ongoing production, assess capabilities like:
- Ordering: Convenient ways to place and track orders (online, EDI, etc).
- Lead Times: Typical turnaround times from order receipt to delivery.
- Inventory: Some manufacturers stock common flex layer types for faster turnaround.
- Lot Tracking: System to trace each delivered lot back to specific production batches.
- Change Management: Handling of mid-production design change orders or feature adds.
- Shipping: Familiarity with international shipping, regulations, customs etc.
Quality and Certifications
For reliable, defect-free flex circuits, partner with manufacturers that demonstrate a commitment to quality:
- QC focus: A culture that makes quality assurance a priority at every step.
- Process controls: Statistical process control to minimize process variations.
- Inspection: Comprehensive inspection procedures to catch flaws.
- Testing: Rigorous testing regimens before, during and after production.
- ISO Certification: Compliance with international quality standards like ISO 9001 reflects disciplined quality systems.
- Industry Approvals: Specific certifications may be required by markets like automotive, aerospace, medical, consumer electronics etc.
Reputable flex PCB companies will have the certifications required by your industry. Customer audits of facilities can offer further validation of capabilities.
Additional Services
Look for manufacturers that provide additional value-added services beyond just bare flex boards:
- Assembly: Component placement, soldering and testing.
- Box Build: Fully packaged, completed electronic modules.
- Overmolding: Plastic molding of components onto circuits.
- Cables: Attached flex cabling for interconnects.
- Coatings: Protective coverlays, encapsulants and conformal coats.
These services enable delivery of turnkey circuit sub-assemblies ready for integration into the final product.
Summary Checklist for Selecting a Flex PCB Manufacturer
When qualifying flexible printed circuit board production partners, make sure to evaluate:
- Breadth of specialized flex PCB manufacturing processes
- Locations and proximity to your team
- Volume production capabilities and scalability
- Early-stage design support and reviews
- Ordering convenience and logistics
- Quality certifications and process control maturity
- Value-added services like assembly and overmolding
- Overall responsiveness and ease of communication
Using the criteria above will help identify the ideal flex circuit company to manufacture your next generation of products.
Frequently Asked Questions About Flex PCB Manufacturers
What are some of the largest flex PCB companies?
Some of the leading global flex PCB producers include Flex Ltd, Multi-Fineline Electronix (MFLEX), Zhen Ding Tech, and Flexium Interconnect. Many other smaller companies also specialize in flex manufacturing.
What is the typical lead time for flex PCB production?
Lead times vary based on flex board complexity and order volumes. Simple single or double layer boards may ship in 5-7 days. Complex multilayer circuits may take 15 days or longer. Discuss expectations with your manufacturer.
How long does it take to go from design to production?
The full cycle from initial design to volume production may take several months. Allow 2-4 weeks for prototyping to finalize the design. Once released, expect about 4+ weeks for first article then pilot builds before full ramp up.
What file formats do flex PCB manufacturers accept?
Gerber and DXF formats are universally supported. Many also accept newer standards like ODB++ and IPC-2581 which incorporate more design details. Discuss preferred formats with your provider.
How much does it cost to manufacture flex PCBs?
Pricing varies based on board complexity, material types, order quantities and other factors. As a rough estimate, expect $100 – $500 prototyping cost and $0.20 to $5 production cost per square inch of flex circuit.