Printed Circuit Board (PCB) manufacturing is a complex process that requires precision and attention to detail. One of the most critical aspects of PCB design and manufacturing is understanding and specifying tolerances. Tolerances define the acceptable limits of variation in physical dimensions, electrical properties, and material characteristics of a PCB. Properly defining these tolerances ensures that the final product meets design requirements and functions as intended. This article provides a comprehensive guide to PCB manufacturing tolerances, focusing on how to add fabrication tolerance options to your manufacturer deliverables.
1. Understanding PCB Manufacturing Tolerances
1.1 What are PCB Tolerances?
PCB tolerances refer to the allowable deviations from specified dimensions, properties, or characteristics during the manufacturing process. These tolerances are necessary because no manufacturing process is perfect, and slight variations are inevitable. Tolerances ensure that the PCB remains functional and reliable despite these variations.
1.2 Importance of Tolerances
- Functionality: Tolerances ensure that components fit correctly and that electrical connections are reliable.
- Manufacturability: Realistic tolerances make the PCB easier and more cost-effective to manufacture.
- Quality Control: Tolerances provide a benchmark for quality control, helping manufacturers identify and address defects.
1.3 Types of PCB Tolerances
PCB tolerances can be categorized into several types, including:
- Dimensional Tolerances: Variations in physical dimensions such as board thickness, trace width, and hole size.
- Electrical Tolerances: Variations in electrical properties such as impedance and resistance.
- Material Tolerances: Variations in material properties such as dielectric constant and thermal conductivity.
2. Key Dimensional Tolerances in PCB Manufacturing
2.1 Board Thickness Tolerance
The thickness of a PCB is critical for mechanical stability and compatibility with connectors and enclosures. Typical board thickness tolerances range from ±10% to ±5%, depending on the material and manufacturing process.
2.2 Trace Width and Spacing Tolerance
Trace width and spacing affect the electrical performance and manufacturability of the PCB. Typical tolerances for trace width and spacing are ±10% to ±20%, depending on the PCB manufacturer’s capabilities.
2.3 Hole Size and Position Tolerance
Holes, including vias and through-holes, must be accurately sized and positioned to ensure proper component placement and electrical connections. Typical hole size tolerances are ±0.05 mm to ±0.10 mm, while hole position tolerances are ±0.075 mm to ±0.15 mm.
2.4 Copper Thickness Tolerance
Copper thickness affects the current-carrying capacity and thermal performance of the PCB. Typical copper thickness tolerances are ±10% to ±20%, depending on the copper weight and manufacturing process.
2.5 Solder Mask and Silkscreen Tolerance
Solder mask and silkscreen tolerances affect the accuracy of component placement and the appearance of the PCB. Typical solder mask tolerances are ±0.05 mm to ±0.10 mm, while silkscreen tolerances are ±0.10 mm to ±0.20 mm.
3. Electrical and Material Tolerances
3.1 Impedance Tolerance
Impedance control is critical for high-speed and RF designs. Typical impedance tolerances are ±10% to ±5%, depending on the PCB manufacturer’s capabilities and the complexity of the design.
3.2 Dielectric Constant Tolerance
The dielectric constant of the PCB material affects signal propagation and impedance. Typical dielectric constant tolerances are ±5% to ±10%, depending on the material and manufacturing process.
3.3 Thermal Conductivity Tolerance
Thermal conductivity is important for heat dissipation in high-power designs. Typical thermal conductivity tolerances are ±10% to ±20%, depending on the material and manufacturing process.
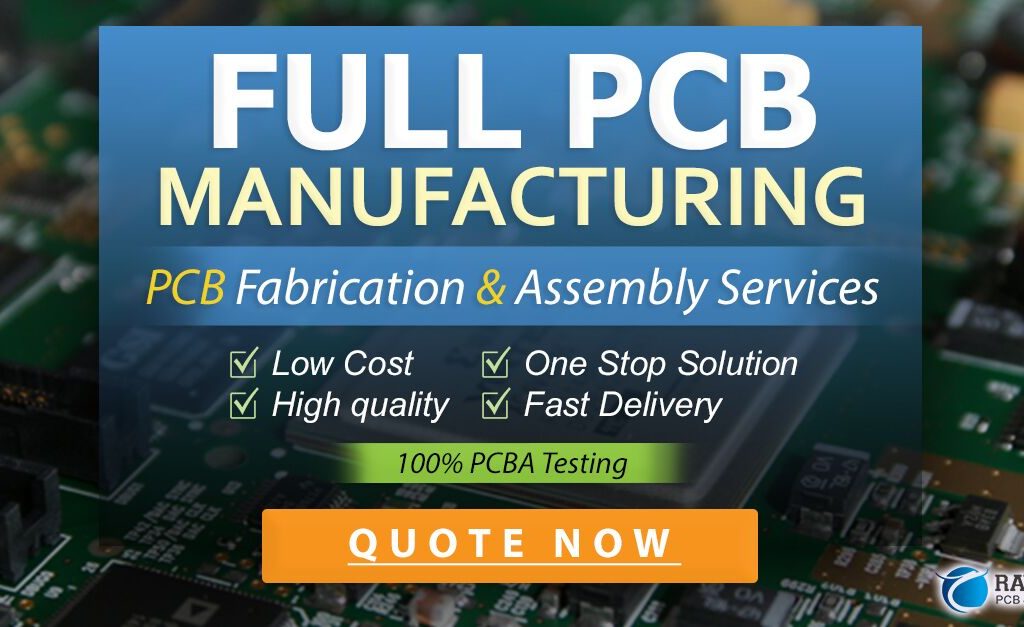
4. Adding Fabrication Tolerance Options to Manufacturer Deliverables
4.1 Communicating Tolerances to Manufacturers
To ensure that your PCB is manufactured to the required tolerances, it is essential to communicate these tolerances clearly to the manufacturer. This can be done through:
- Gerber Files: Include tolerance information in the Gerber files, which are used to define the PCB layout.
- Manufacturing Drawings: Provide detailed manufacturing drawings that specify tolerances for critical dimensions and features.
- Design Specifications: Include a design specification document that outlines all relevant tolerances and requirements.
4.2 Using Design for Manufacturability (DFM) Guidelines
DFM guidelines help ensure that your design is manufacturable and meets tolerance requirements. Key DFM considerations include:
- Standard Tolerances: Use standard tolerances whenever possible to reduce manufacturing complexity and cost.
- Tight Tolerances: Specify tight tolerances only for critical features, as they can increase manufacturing cost and lead time.
- Material Selection: Choose materials with consistent properties to minimize variations in electrical and thermal performance.
4.3 Collaborating with Manufacturers
Collaborate closely with your PCB manufacturer to understand their capabilities and limitations. This collaboration can help you:
- Optimize Tolerances: Adjust tolerances based on the manufacturer’s capabilities to balance performance and cost.
- Identify Potential Issues: Address potential manufacturing issues early in the design process to avoid costly revisions.
5. Best Practices for Specifying Tolerances
5.1 Define Critical and Non-Critical Tolerances
Identify which tolerances are critical for the functionality and reliability of the PCB, and which are less critical. Focus on specifying tight tolerances for critical features and use standard tolerances for non-critical features.
5.2 Use Industry Standards
Refer to industry standards such as IPC-6012 and IPC-A-600 for guidance on PCB tolerances. These standards provide detailed specifications for various types of PCBs and can help ensure that your design meets industry requirements.
5.3 Perform Tolerance Analysis
Use tolerance analysis tools to evaluate the impact of variations on the PCB’s performance. This analysis can help you identify potential issues and adjust tolerances accordingly.
5.4 Document Tolerances Clearly
Ensure that all tolerances are clearly documented in your design files and manufacturing deliverables. This documentation should include:
- Dimensional Tolerances: Specify tolerances for board thickness, trace width, hole size, and other critical dimensions.
- Electrical Tolerances: Specify tolerances for impedance, resistance, and other electrical properties.
- Material Tolerances: Specify tolerances for dielectric constant, thermal conductivity, and other material properties.
6. Case Study: Specifying Tolerances for a High-Density PCB
To illustrate the importance of specifying tolerances, let’s examine a case study involving a high-density PCB used in a telecommunications application.
6.1 Design Requirements
- Board Thickness: 1.6 mm ±10%
- Trace Width and Spacing: 0.1 mm ±20%
- Hole Size: 0.2 mm ±0.05 mm
- Impedance: 50 Ω ±5%
- Dielectric Constant: 4.5 ±5%
6.2 Tolerance Challenges
- High-Density Layout: The high-density layout required tight tolerances for trace width and spacing.
- Impedance Control: The impedance tolerance was critical for signal integrity in the high-speed design.
- Material Consistency: Variations in the dielectric constant could affect impedance and signal propagation.
6.3 Tolerance Solutions
- Collaboration with Manufacturer: The design team collaborated closely with the manufacturer to understand their capabilities and optimize tolerances.
- Tolerance Analysis: Tolerance analysis tools were used to evaluate the impact of variations on the PCB’s performance.
- Clear Documentation: All tolerances were clearly documented in the design files and manufacturing deliverables.
6.4 Results
The final design met all performance requirements, with the PCB manufactured to the specified tolerances. The collaboration between the design team and the manufacturer ensured that the high-density layout was manufacturable and reliable.
7. Conclusion
PCB manufacturing tolerances are a critical aspect of PCB design and manufacturing. By understanding and specifying tolerances accurately, you can ensure that your PCB meets design requirements and functions as intended. Adding fabrication tolerance options to your manufacturer deliverables involves clear communication, collaboration, and adherence to industry standards. By following the best practices outlined in this guide, you can achieve high-quality, reliable PCBs that meet the demands of modern electronics applications.
This guide provides a comprehensive overview of PCB manufacturing tolerances and how to add fabrication tolerance options to your manufacturer deliverables. By understanding the principles and best practices outlined here, you can ensure that your PCB designs are manufacturable, reliable, and meet performance requirements.