What is the IPC-2221 Standard?
IPC-2221, titled “Generic Standard on Printed Board Design”, is a standard published by the IPC (Institute of Printed Circuits) that provides guidelines and requirements for the design of printed circuit boards (PCBs). One important aspect covered by IPC-2221 is determining the current carrying capacity and allowable temperature rise of PCB traces based on their width, thickness, and copper weight.
Properly sizing PCB traces is critical to ensure reliability and prevent issues like excessive heating, voltage drop, or even trace damage. The IPC-2221 standard provides equations and charts to calculate the maximum current a trace can safely handle given its cross-sectional area and allowable temperature rise.
PCB Trace Current Capacity Calculation
The current carrying capacity of a PCB trace depends on several factors:
– Trace width
– Trace thickness (copper weight)
– Allowable temperature rise above ambient
– PCB material properties
IPC-2221 provides two methods to determine the current capacity:
1. Equations
2. Charts
Current Capacity Equations
The equations for internal and external PCB traces are:
Internal traces:
I = 0.024 * dT^0.44 * A^0.725
External traces:
I = 0.048 * dT^0.44 * A^0.725
Where:
– I = maximum current in Amps
– dT = temperature rise above ambient in °C
– A = cross-sectional area in mils^2 (1 mil = 0.001 inch)
The cross-sectional area A is calculated from the trace width W (in mils) and thickness H (in oz/ft^2):
A = W * (1.378 * H)
For example, a 10 mil wide, 1 oz copper trace has a cross-sectional area of:
A = 10 * (1.378 * 1) = 13.78 mils^2
Allowing a 10°C temp rise, the maximum current for an internal trace is:
I = 0.024 * 10^0.44 * 13.78^0.725 = 0.61 A
And for an external trace:
I = 0.048 * 10^0.44 * 13.78^0.725 = 1.22 A
Current Capacity Charts
As an alternative to the equations, IPC-2221 provides charts that plot the current capacity versus cross-sectional area for various temperature rises. Here is an example chart for external PCB traces:
Cross-sectional Area (mils^2) | 10°C Rise | 20°C Rise | 30°C Rise |
---|---|---|---|
15 | 1.32 A | 1.86 A | 2.28 A |
25 | 1.78 A | 2.53 A | 3.09 A |
35 | 2.18 A | 3.08 A | 3.77 A |
50 | 2.69 A | 3.80 A | 4.65 A |
75 | 3.43 A | 4.84 A | 5.92 A |
100 | 4.06 A | 5.72 A | 7.00 A |
To use the chart, calculate the cross-sectional area and look up the current capacity for the desired temperature rise.
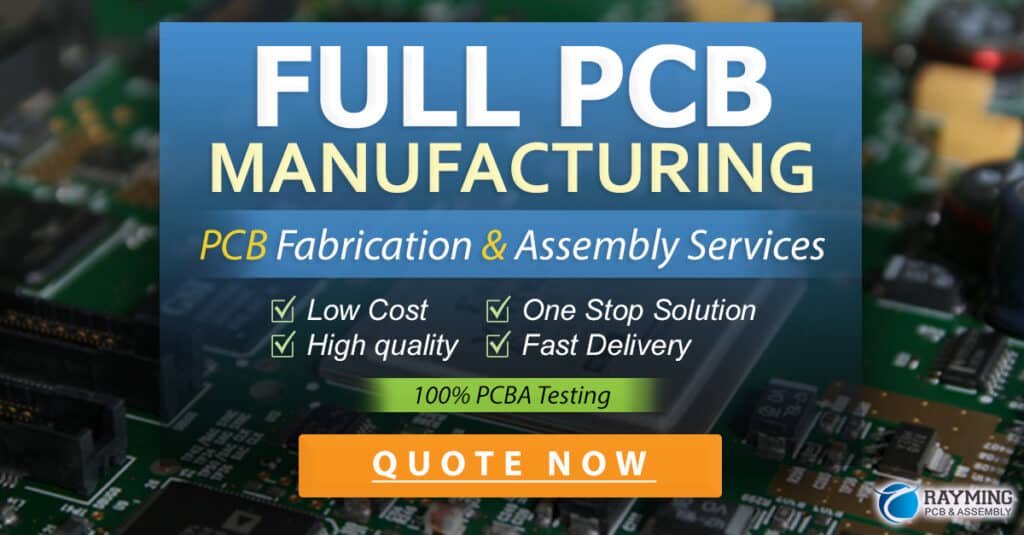
PCB Trace Heating Calculation
In addition to current capacity, it’s important to consider the heating of PCB traces due to power dissipation. IPC-2221 provides an equation to calculate the trace temperature rise:
dT = (I^2 * R * L) / (k * W * H)
Where:
– dT = trace temperature rise above ambient in °C
– I = RMS current in Amps
– R = trace resistance in Ohms/length
– L = trace length
– k = PCB thermal conductivity (typical 0.481 for FR4)
– W = trace width
– H = trace thickness
The trace resistance R in Ohms/mil can be calculated from the sheet resistance Rs in mOhms/sq and trace width W in mils:
R = Rs / W
Rs depends on the copper weight, here are some typical values:
Copper Weight (oz/ft^2) | Sheet Resistance Rs (mOhms/sq) |
---|---|
0.5 | 1.272 |
1 | 0.636 |
2 | 0.318 |
3 | 0.212 |
For example, consider a 1 oz copper trace with:
– 1 A RMS current
– 1000 mil length
– 10 mil width
The trace resistance is:
R = 0.636 / 10 = 0.0636 Ohms/mil
Assuming 1.378 mils thickness (1 oz cu) and FR4 PCB material (k = 0.481), the temperature rise is:
dT = (1^2 * 0.0636 * 1000) / (0.481 * 10 * 1.378) = 9.58 °C
This calculation determines if the trace heating is acceptable. If dT is too high, increasing the trace width or copper weight can help reduce the temperature rise.
FAQ
Q1: What is a mil?
A1: In PCB design, a mil is a unit equal to 0.001 inches or 25.4 microns. PCB dimensions like trace width and thickness are often specified in mils.
Q2: What copper weights are commonly used for PCBs?
A2: Standard copper weights for PCBs are 0.5 oz, 1 oz, 2 oz, and 3 oz per square foot. 1 oz/ft^2 is most common. Higher weights allow higher current capacity.
Q3: What is the best way to reduce PCB trace heating?
A3: To minimize trace heating, you can:
1. Increase the trace width to decrease resistance
2. Use heavier copper weight (2+ oz/ft^2) for high current traces
3. Use wider spacing to improve heat dissipation
4. Add thermal relief pads and vias to conduct heat to other layers
Q4: What is a PCB’s thermal conductivity?
A4: The thermal conductivity k measures a PCB material’s ability to conduct heat. It is in units of Watts per meter-Kelvin (W/mK). FR4, a common PCB material, has a thermal conductivity around 0.3 W/mK.
Q5: Where can I find IPC-2221?
A5: IPC-2221 is available for purchase from the IPC organization at their website (ipc.org). However, many key graphs and equations are available in electronics design references, application notes, and online calculators.
Conclusion
The IPC-2221 standard provides important guidelines for sizing PCB traces to achieve acceptable current capacity and heating. By using the equations and charts from the standard, designers can ensure traces are large enough to handle the required current without excessive temperature rise. This helps create reliable PCBs without undersized traces that could overheat or fail prematurely. When in doubt, it’s best to be conservative by oversizing traces, using heavy copper, and providing adequate cooling. Following the IPC-2221 guidelines is an essential part of good PCB design practices.