What is a PCB?
A printed circuit board (PCB) is a flat board made of insulating material, such as fiberglass or plastic, with conductive copper traces printed onto its surface. These traces connect electronic components, such as resistors, capacitors, and integrated circuits, to form a complete electronic circuit. PCBs are used in virtually all electronic devices, from smartphones and computers to industrial equipment and medical devices.
Why make your own PCBs?
There are several reasons why you might want to make your own PCBs:
- Customization: By making your own PCBs, you can create circuits that are tailored to your specific needs and requirements.
- Cost savings: For small-scale projects, making your own PCBs can be more cost-effective than ordering them from a manufacturer.
- Learning experience: Making PCBs is a great way to learn about electronics and gain hands-on experience with circuit design and fabrication.
- Prototyping: If you’re developing a new electronic product, making your own PCBs allows you to quickly prototype and test your designs.
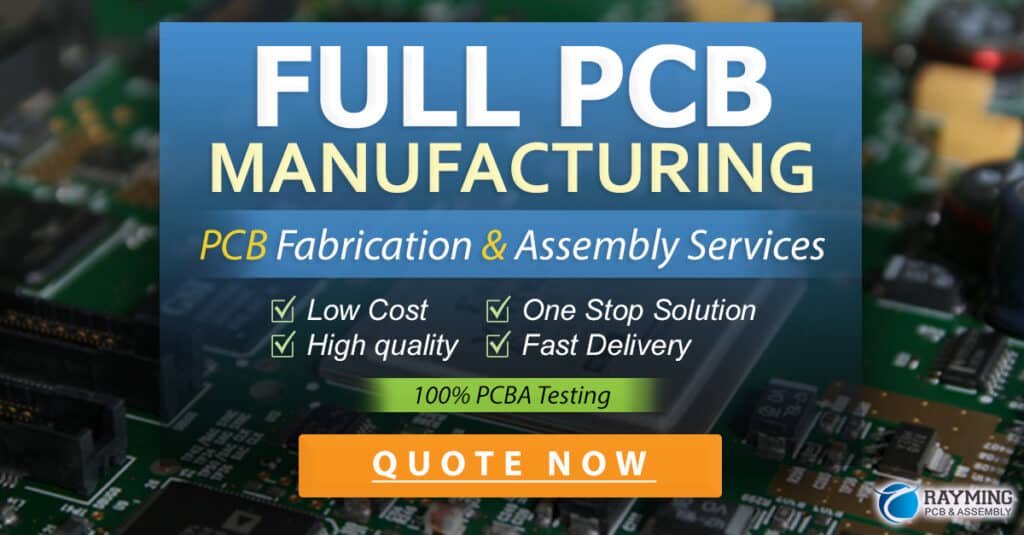
Tools and materials needed
Before you start making your own PCBs, you’ll need to gather the following tools and materials:
Tool/Material | Description |
---|---|
Computer with PCB design software | You’ll need a computer with PCB design software installed, such as KiCad, Eagle, or Altium Designer. |
Laser printer | A laser printer is used to print your circuit designs onto transfer paper. |
Transfer paper | Transfer paper is a special type of paper that allows you to transfer your printed circuit design onto the copper-clad board. |
Copper-clad board | A copper-clad board is a blank PCB with a layer of copper on one or both sides. |
Etching solution | An etching solution, such as ferric chloride, is used to remove the unwanted copper from the board, leaving only your circuit traces. |
Protective gear | When working with etching solution, it’s important to wear protective gear, such as gloves and safety glasses. |
Drill or drill press | A drill or drill press is used to create holes in your PCB for mounting components. |
Soldering iron and solder | A soldering iron and solder are used to attach components to your PCB. |
Step 1: Design your circuit
The first step in making a PCB is to design your circuit using PCB design software. There are several popular software options available, including:
- KiCad (free and open-source)
- Eagle (free for non-commercial use)
- Altium Designer (paid)
When designing your circuit, keep the following tips in mind:
- Start with a schematic: Before laying out your PCB, create a schematic diagram of your circuit. This will help you visualize how the components are connected and ensure that your design is correct.
- Consider component placement: When laying out your PCB, think carefully about where you place your components. Try to minimize the distance between connected components to reduce the length of your traces.
- Use appropriate trace widths: The width of your traces will depend on the amount of current they need to carry. Use wider traces for high-current paths and narrower traces for low-current paths.
- Add ground and power planes: To reduce noise and improve signal integrity, consider adding ground and power planes to your PCB.
- Include mounting holes: Don’t forget to include mounting holes in your PCB design to make it easier to install your board in an enclosure.
Step 2: Print your circuit design
Once you’ve finished designing your circuit, the next step is to print it onto transfer paper using a laser printer. Make sure to print your design at 100% scale and use the highest quality settings available.
If your design includes multiple layers, you’ll need to print each layer separately onto its own sheet of transfer paper. Make sure to align the layers carefully when printing to ensure that they line up correctly when transferred onto the copper-clad board.
Step 3: Transfer your design onto the copper-clad board
To transfer your printed circuit design onto the copper-clad board, follow these steps:
- Clean the copper-clad board with steel wool or a scouring pad to remove any oxidation or dirt.
- Place the transfer paper with your printed circuit design face-down onto the copper-clad board.
- Use a clothes iron set to its highest temperature (without steam) to heat the transfer paper for several minutes, pressing down firmly and evenly.
- Allow the board to cool for a few minutes, then carefully peel off the transfer paper. Your circuit design should now be transferred onto the copper-clad board.
Step 4: Etch your PCB
To remove the unwanted copper from your board, you’ll need to etch it using an etching solution, such as ferric chloride. Follow these steps to etch your PCB:
- Put on your protective gear, including gloves and safety glasses.
- Place your PCB into a container filled with etching solution.
- Agitate the container gently to ensure that the etching solution is evenly distributed over the board.
- Check the board periodically to see how the etching is progressing. Depending on the strength of your etching solution and the size of your board, the etching process can take anywhere from a few minutes to an hour or more.
- Once all of the unwanted copper has been removed, rinse the board thoroughly with water to remove any remaining etching solution.
Step 5: Drill holes and solder components
After etching your PCB, you’ll need to drill holes for mounting your components. Use a drill or drill press to carefully drill holes at the locations indicated in your PCB design.
Once you’ve drilled all of the necessary holes, you can begin soldering your components onto the board. Follow these tips for successful soldering:
- Use a soldering iron with a fine tip and set it to the appropriate temperature for your solder (usually around 600-700°F).
- Apply a small amount of solder to the tip of the iron to help transfer heat to the joint.
- Place the component lead through the hole in the PCB and press the tip of the soldering iron against the lead and the pad simultaneously.
- Apply solder to the joint, allowing it to flow around the lead and the pad.
- Remove the soldering iron and allow the joint to cool for a few seconds before moving on to the next one.
Frequently Asked Questions (FAQ)
- What is the best PCB design software for beginners?
-
For beginners, KiCad and Eagle are both excellent choices. They are free (KiCad is open-source, while Eagle offers a free version for non-commercial use) and have extensive libraries of components and tutorials available online.
-
Can I make double-sided PCBs at home?
-
Yes, it is possible to make double-sided PCBs at home, but it requires more advanced techniques, such as using alignment pins to ensure that the layers are properly aligned during the transfer process.
-
How do I choose the right etching solution?
-
Ferric chloride is the most commonly used etching solution for home PCB fabrication. It is relatively inexpensive and easy to use, but it can be messy and requires careful handling. Other options include ammonium persulfate and sodium persulfate, which are less messy but may be more expensive.
-
Can I reuse my etching solution?
-
Etching solution can be reused multiple times, but it will become less effective over time as it becomes saturated with copper. When your etching solution starts to take significantly longer to etch your boards, it’s time to replace it.
-
How can I make my PCBs look more professional?
- To give your PCBs a more professional look, you can apply a solder mask and silkscreen layer. A solder mask is a layer of polymer that covers the copper traces on your board, leaving only the pads exposed for soldering. A silkscreen layer is used to add text and graphics to your board, such as component labels and logos. These layers can be applied using special transfer papers and techniques similar to those used for transferring your circuit design.
Conclusion
Making your own PCBs can be a fun and rewarding hobby for electronics enthusiasts. By following the steps outlined in this guide, you can create custom circuits that are tailored to your specific needs and requirements. While the process may seem daunting at first, with practice and patience, you’ll be able to produce high-quality PCBs that rival those made by professional manufacturers.
Remember to always prioritize safety when working with etching solutions and other chemicals, and don’t be discouraged if your first few attempts don’t turn out perfectly. With time and experience, you’ll be able to refine your techniques and produce PCBs that you can be proud of.