What is PCB Printing?
PCB printing refers to the process of fabricating printed circuit boards. PCBs are flat boards made of insulating materials like fiberglass, with conductive copper traces printed on them to connect different electronic components. Nearly all modern electronic devices use PCBs to route signals and power between components.
There are several methods for printing PCBs, which we’ll cover in detail later in this article. The most common PCB printing processes are:
- Etching
- Milling
- Silk-screen printing
- Inkjet printing
- 3D printing
The choice of printing method depends on factors like the complexity of the board design, the required precision and conductivity of the traces, the production volume, and cost considerations.
Why Print Your Own PCBs?
There are several advantages to printing your own PCBs:
-
Rapid prototyping: Printing your own boards allows you to quickly test and iterate on designs without the lead time of sending them out for fabrication.
-
Customization: You have full control over the board specs and can tailor them exactly to your needs.
-
Cost savings: For low-volume production, it’s often cheaper to print the boards yourself versus paying for a fabrication service, especially for simple designs.
-
Educational value: Printing PCBs is a great way to learn about electronics manufacturing. It gives you hands-on experience with the entire process from design to assembly.
Of course, there are also some drawbacks to consider. Printing PCBs requires an initial investment in equipment and materials. It also takes time to master the process and produce reliable, high-quality boards. And complex, multilayer designs may be challenging or impractical to print at home.
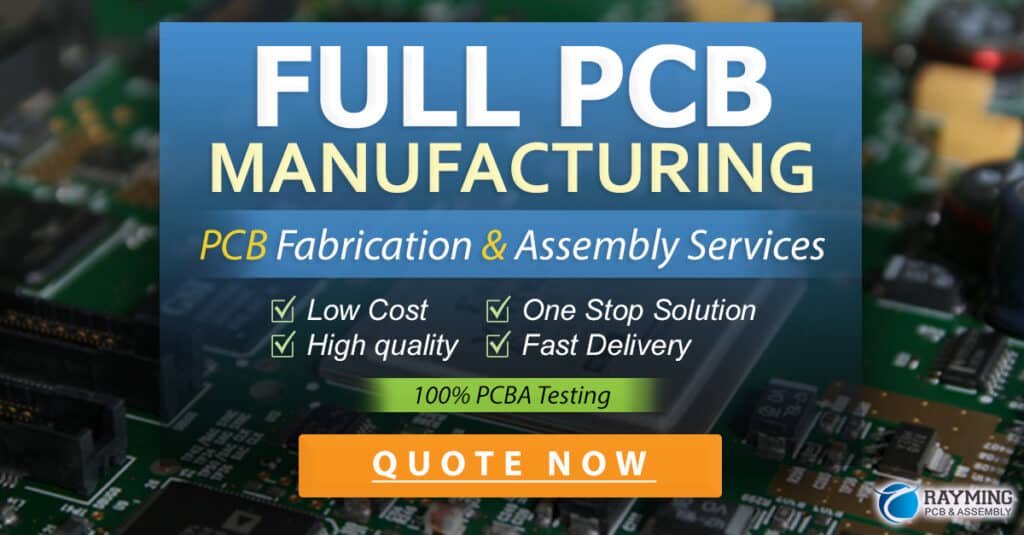
PCB Printing Methods
Let’s take a closer look at the different methods you can use to print PCBs and the pros and cons of each.
Etching
pcb etching is a subtractive method that starts with a copper-clad board and removes unwanted copper to leave behind the desired traces. The basic process is:
- Print the circuit pattern onto a transparent film to create a mask
- Apply a photoresist layer to the copper-clad board and expose it to UV light with the mask
- Develop the photoresist to harden the exposed areas
- Etch away the unwanted copper using a chemical solution like ferric chloride
- Remove the hardened photoresist with a solvent, leaving the final circuit traces
Etching produces professional-looking boards and works well for complex designs. However, it requires careful handling of chemicals and proper disposal of waste. The process is also relatively time-consuming.
Milling
pcb milling uses a CNC machine to mechanically remove copper from a blank board, leaving behind the circuit traces. This an additive process, as opposed to the subtractive etching process.
A conductive ink or paste is applied to the board through a screen or stencil with the circuit pattern. The most common materials are silver-based conductive inks. After screen printing, the ink is cured, typically with heat, to make it conductive.
Screen printing can quickly produce large batches of simple boards. The printed traces have lower resolution and conductivity compared to etched traces, but are sufficient for many applications. Materials and equipment for screen printing are relatively inexpensive.
Inkjet Printing
Inkjet printing deposits conductive ink directly onto the PCB substrate using a modified inkjet printer. Conductive inks containing silver nanoparticles or other metal particles are printed, then sintered to achieve conductivity.
Inkjet printing is an additive process with quick turnaround times. It has good resolution and allows printing on a variety of substrates. However, the conductivity of printed traces is lower than bulk metals. Inkjet printing is best suited for low-power, high-resistance circuits.
3D Printing
3D printing can be used to print PCBs, either by printing a substrate and then depositing conductive traces, or by directly printing with conductive filament. Fused deposition modeling (FDM) and stereolithography (SLA) are two common 3D printing methods that can be adapted for PCBs.
3D printing allows complex geometries and rapid iteration. Multimaterial 3D printers can print the substrate and conductors in a single process. However, 3D printed traces currently have much lower conductivity than etched or screen printed traces. The technology is still nascent but holds promise for the future.
Here’s a summary table comparing the different PCB printing methods:
Method | Type | Pros | Cons |
---|---|---|---|
Etching | Subtractive | High resolution and conductivity, works for complex designs | Requires chemicals, time-consuming |
Milling | Subtractive | No chemicals, good for prototypes and low volumes | Requires CNC machine, limited complexity |
Screen Printing | Additive | Fast, low-cost, good for simple designs and high volumes | Lower resolution and conductivity |
Inkjet Printing | Additive | High resolution, quick turnaround, prints on various substrates | Lower conductivity, best for low-power circuits |
3D Printing | Additive | Enables complex geometries, fast iteration | Very low conductivity, new technology |
Designing Your PCB
Before you can print a PCB, you need to design it. The PCB design process typically involves the following steps:
-
Schematic capture: Create a schematic diagram of your circuit showing how the components connect. You can use electronics design automation (EDA) software like KiCad, Eagle, or Altium for this.
-
Component placement: Arrange the components on the board and define the board shape and size. Consider factors like signal integrity, power distribution, heat dissipation, and mechanical constraints.
-
Routing: Route the connections between components, either manually or using the autorouter feature in your EDA tool. The routing stage defines the actual copper traces on the different layers of the board.
-
Design rule check: Verify that your design meets the manufacturing capabilities and design requirements. This includes checking trace widths and spacing, hole sizes, annular rings, etc.
-
Output generation: Generate the output files needed for manufacturing, such as Gerber files, drill files, and pick-and-place files.
Some tips for designing PCBs for printing:
- Keep the design single-sided if possible for simplicity
- Use larger traces and pad sizes to accommodate the lower resolution of printing vs etching
- Provide clear labels and markers for component placement and orientation
- Follow good practices for grounding, shielding, and signal routing to ensure proper functioning of the circuit
- Consider the specific design rules and limitations of your chosen printing method
Printing Your PCB
Once you have your PCB design ready, it’s time to print it. The exact printing process will depend on the specific method you’re using. However, there are some general steps and considerations that apply across methods.
Preparing the PCB Blanks
PCB blanks are the raw substrates you’ll print your circuits on. The most common material is FR-4, a glass-reinforced epoxy laminate. You can buy FR-4 blanks in various thicknesses and copper weights.
Copper weight refers to the thickness of the copper layer on the blank, typically measured in ounces per square foot (oz/ft²). Common copper weights are 0.5 oz/ft², 1 oz/ft², and 2 oz/ft². Thicker copper allows for higher current carrying capacity but may be more challenging to etch or mill.
Before printing, you’ll need to cut the PCB blank to the appropriate size for your design. You can use a shear, saw, or router to cut the blanks. Be sure to wear protective gear and follow safety precautions when cutting.
Clean the copper surface of the blank with a mild abrasive like steel wool or fine sandpaper to remove any oxidation and improve adhesion of the resist or ink.
Applying the Circuit Pattern
The method for applying the circuit pattern to the PCB blank depends on the printing process:
- For etching, you’ll need to print the circuit pattern onto a transparent film and use it to expose a photoresist layer on the blank.
- For milling, you’ll load the PCB design file into the CNC control software, which will guide the milling bit to remove copper according to the pattern.
- For screen printing, you’ll need to create a screen or stencil with the circuit pattern. Align the screen with the blank and apply the conductive ink.
- For inkjet printing, load the blank into the printer and print the circuit pattern using the conductive ink.
- For 3D printing, set up the printer with the appropriate filaments and substrates and initiate the print process according to your design.
Curing and Finishing
After applying the circuit pattern, the printed PCB typically needs to be cured to make the traces conductive and durable. The curing process depends on the specific ink or material used:
- Silver-based inks are usually cured with heat using an oven or hot plate.
- Some inks require UV curing using a UV lamp.
- Conductive filaments used in 3D printing may require sintering, which involves heating the material close to its melting point to fuse the conductive particles.
After curing, you may need to apply a protective coating like soldermask or silkscreen to the PCB. These coatings insulate the traces, prevent oxidation, and provide labels for assembly.
Finally, drill any holes needed for through-hole components or mounting using a drill press or handheld drill. Now your PCB is ready for assembly!
Tips for Successful PCB Printing
Here are some additional tips to help you succeed with PCB printing:
-
Start simple: If you’re new to PCB printing, start with simple single-sided designs to get a feel for the process before attempting more complex boards.
-
Use the right materials: Choose high-quality substrates, inks, and materials that are compatible with your printing method. Cheap materials may lead to poor results.
-
Calibrate your equipment: Regularly calibrate your printer, CNC machine, or other equipment to ensure consistent results. Check alignment, speed, and material dispense settings.
-
Control the environment: Factors like temperature, humidity, and dust can affect the printing process. Try to print in a controlled environment for the best results.
-
Test and verify: Always test your printed PCBs for continuity and shorts before assembling components. Use a multimeter or simple LED circuit to verify that traces are intact and isolated.
-
Practice good circuit design: Proper circuit design is critical for the functionality of your PCB. Follow best practices for component placement, signal routing, grounding, and heat management.
-
Iterate and refine: Don’t expect perfect results on the first try. PCB printing often requires some trial and error to dial in the process for a particular design. Keep iterating and refining your techniques.
FAQ
What equipment do I need to print PCBs?
The equipment needed depends on the printing method you choose:
- Etching: You’ll need a UV exposure unit, developing trays, etching tank, and drill press, along with consumables like photoresist, etchant solution, and copper-clad blanks.
- Milling: You’ll need a CNC mill or router, bits, and software to control the machine, along with copper-clad blanks.
- Screen printing: You’ll need screens or stencils, a squeegee, curing equipment (oven or UV lamp), and conductive ink.
- Inkjet printing: You’ll need an inkjet printer (either modified or purpose-built for PCBs), conductive ink, and curing equipment.
- 3D printing: You’ll need a 3D printer capable of printing conductive filament or multiple materials, along with the appropriate filaments and substrates.
You’ll also need basic tools like a multimeter, soldering iron, safety gear, and computer with PCB design software.
How much does it cost to print PCBs?
The cost to print PCBs varies widely depending on the printing method, the complexity of the design, and the materials used. Here are some rough estimates:
- Etching: $50-100 for equipment and $10-20 per board for materials
- Milling: $500-1000 for a CNC machine and $10-20 per board for materials
- Screen printing: $50-100 for screens and ink, $5-10 per board for materials
- Inkjet printing: $500-5000 for a printer and $10-50 per board for materials
- 3D printing: $500-5000 for a printer and $10-100 per board for materials
These are just ballpark figures – the actual costs can be higher or lower depending on your specific setup and requirements. In general, the upfront equipment costs are higher for methods like milling, inkjet, and 3D printing, while the per-board costs are lower for methods like etching and screen printing.
Can I print multi-layer PCBs?
Yes, it’s possible to print multi-layer PCBs, but it’s more challenging than single-layer boards. Etching and inkjet printing can produce double-sided boards by printing and aligning patterns on both sides of the substrate. Some 3D printing methods can print multi-layer boards in a single process.
However, multi-layer boards with more than two layers are difficult to produce with home printing methods. The alignment and insulation requirements are very precise. For complex multi-layer boards, it’s usually better to use a professional pcb fabrication service.
What resolution can I achieve with PCB printing?
The resolution of printed PCBs depends on the printing method:
- Etching can achieve trace widths and spacing down to about 0.1 mm (4 mil) with good equipment and technique.
- Milling is limited by the size of the milling bit, typically around 0.2-0.3 mm (8-12 mil).
- Screen printing has a practical resolution limit around 0.3-0.4 mm (12-16 mil) due to the mesh size of the screens.
- Inkjet printing can achieve high resolutions under 0.1 mm (4 mil), but the conductivity of the traces may be lower.
- 3D printing resolution depends on the printer and nozzle size, but is typically 0.3 mm (12 mil) or larger. Conductive 3D printed traces have very low conductivity.
Keep in mind that these are rough guidelines – the actual resolution achievable depends on the specific equipment, materials, and operator skill.
How do I choose the right PCB printing method?
Choosing the right PCB printing method depends on your specific needs and constraints. Consider factors like:
- The complexity and size of your PCB design
- The required resolution and conductivity of traces
- The number of boards you need to produce
- Your budget for equipment and materials
- Your skills and experience level
- The available space and facilities for printing
In general, etching is a good choice for complex designs and high conductivity. Milling works well for rapid prototyping. Screen printing is suitable for simple designs in high volumes. Inkjet printing offers high resolution but lower conductivity. 3D printing is a newer technology best for experimental designs.
I hope this guide has been helpful for learning about PCB printing! Let me know if you have any other questions.