What is laser cutting?
Laser cutting is a process that uses a high-powered laser to cut materials with high precision. The laser beam is focused onto the material, and the intense heat generated by the laser vaporizes or melts the material along the cutting path. Laser cutting is widely used in various industries, including automotive, aerospace, and electronics, due to its accuracy, speed, and versatility.
Advantages of laser cutting
- Precision: Laser cutting offers high precision, with cutting accuracies of up to ±0.05 mm, depending on the material and laser system used.
- Speed: Laser cutting is a fast process, with cutting speeds ranging from a few millimeters per second to several meters per second, depending on the material and laser power.
- Versatility: Laser cutting can be used on a wide range of materials, including metals, plastics, wood, and composites.
- Minimal material waste: Laser cutting produces minimal material waste compared to traditional cutting methods, as the laser beam vaporizes the material along the cutting path.
- Environmentally friendly: Laser cutting does not require the use of chemicals or produce harmful fumes, making it a more environmentally friendly alternative to traditional manufacturing methods.
Laser cutting PCBs
Laser cutting PCBs is a relatively new technology that offers several advantages over traditional PCB manufacturing methods. The process involves using a high-powered laser to cut the copper traces and drill holes on the PCB substrate. This eliminates the need for chemical etching and mechanical drilling, resulting in a more precise and environmentally friendly manufacturing process.
Advantages of laser cutting PCBs
- High precision: Laser cutting offers high precision, with cutting accuracies of up to ±0.05 mm, enabling the creation of fine pitch traces and small vias.
- Rapid prototyping: Laser cutting allows for rapid prototyping of PCBs, as the process is faster and more flexible than traditional manufacturing methods.
- Environmentally friendly: Laser cutting eliminates the need for chemical etching, which can be harmful to the environment and requires proper disposal of waste materials.
- Cost-effective: Laser cutting can be more cost-effective than traditional PCB manufacturing methods, particularly for low-volume production or prototyping.
- Improved reliability: Laser-cut PCBs have improved reliability due to the high precision and consistency of the cutting process, reducing the risk of defects or failures.
Limitations of laser cutting PCBs
Despite the many advantages of laser cutting PCBs, there are also some limitations to consider:
- Material constraints: Laser cutting is limited to certain PCB substrate materials, such as FR4, polyimide, and ceramic. Some materials may not be suitable for laser cutting due to their thermal properties or tendency to produce harmful fumes when vaporized.
- Thickness limitations: Laser cutting may not be suitable for very thick PCB substrates, as the laser power required to cut through the material may cause thermal damage or deformation.
- Initial investment: Laser cutting systems can be expensive, requiring a significant initial investment compared to traditional PCB manufacturing equipment.
- Operator skill: Laser cutting PCBs requires skilled operators to ensure optimal results and minimize the risk of defects or damage to the PCB.
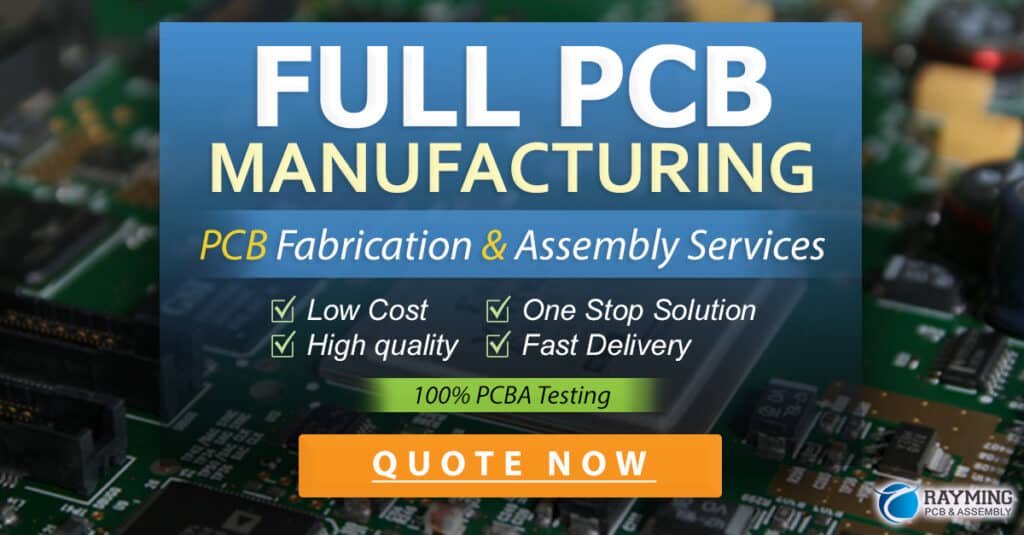
Types of lasers used for cutting PCBs
There are several types of lasers that can be used for cutting PCBs, each with its own advantages and limitations.
CO2 lasers
CO2 lasers are the most common type of laser used for cutting PCBs. They operate at a wavelength of 10.6 μm and can produce high power outputs, typically ranging from 10 to 1000 watts. CO2 lasers are well-suited for cutting a wide range of PCB substrate materials, including FR4, polyimide, and ceramic.
Advantages of CO2 lasers:
– High power output
– Versatility in cutting various PCB substrate materials
– Relatively low cost compared to other laser types
Limitations of CO2 lasers:
– Larger focus spot size compared to other laser types, which may limit the minimum feature size that can be cut
– Not suitable for cutting highly reflective materials, such as copper or aluminum
Fiber lasers
Fiber lasers are a newer type of laser that has gained popularity in recent years for cutting PCBs. They operate at a wavelength of around 1 μm and can produce high power outputs, typically ranging from 100 to 1000 watts. Fiber lasers are known for their high beam quality and small focus spot size, making them well-suited for cutting fine pitch traces and small vias.
Advantages of fiber lasers:
– High beam quality and small focus spot size, enabling the cutting of fine features
– High cutting speed and efficiency
– Low maintenance requirements and long operational lifetime
Limitations of fiber lasers:
– Higher cost compared to CO2 lasers
– Limited versatility in cutting certain PCB substrate materials, such as polyimide or ceramic
UV lasers
UV lasers operate at shorter wavelengths, typically around 355 nm, and can produce high power outputs, ranging from 1 to 20 watts. UV lasers are known for their ability to produce very fine features and high-quality edges, making them well-suited for cutting high-density PCBs and creating small vias.
Advantages of UV lasers:
– Ability to produce very fine features and high-quality edges
– Minimal thermal damage to the PCB substrate
– Suitable for cutting a wide range of PCB substrate materials
Limitations of UV lasers:
– Higher cost compared to CO2 and fiber lasers
– Lower power output and slower cutting speeds compared to other laser types
Laser Type | Wavelength | Power Output | Advantages | Limitations |
---|---|---|---|---|
CO2 | 10.6 μm | 10-1000 W | – High power output – Versatility in cutting various PCB substrate materials – Relatively low cost |
– Larger focus spot size – Not suitable for cutting highly reflective materials |
Fiber | ~1 μm | 100-1000 W | – High beam quality and small focus spot size – High cutting speed and efficiency – Low maintenance requirements |
– Higher cost – Limited versatility in cutting certain PCB substrate materials |
UV | ~355 nm | 1-20 W | – Ability to produce very fine features and high-quality edges – Minimal thermal damage – Suitable for cutting a wide range of PCB substrate materials |
– Higher cost – Lower power output and slower cutting speeds |
Laser cutting process for PCBs
The laser cutting process for PCBs involves several steps to ensure optimal results and minimize the risk of defects or damage to the PCB.
PCB design and preparation
- Create the PCB design using CAD software, ensuring that the design is optimized for laser cutting (e.g., avoiding very small features or closely spaced traces).
- Generate the necessary files for laser cutting, such as Gerber files or DXF files, which contain the information needed to guide the laser cutting system.
- Prepare the PCB substrate material by cleaning the surface and ensuring that it is free from dust, dirt, or other contaminants that could affect the laser cutting process.
Laser cutting setup
- Load the PCB substrate material into the laser cutting system, ensuring that it is properly aligned and secured.
- Set up the laser cutting parameters, such as laser power, cutting speed, and focal point, based on the PCB substrate material and the desired features to be cut.
- Upload the PCB design files to the laser cutting system and verify that the cutting path is correct and free from errors.
Laser cutting process
- Initiate the laser cutting process, which typically involves the laser beam following the cutting path defined by the PCB design files.
- Monitor the laser cutting process to ensure that it is proceeding as expected and that there are no issues, such as thermal damage or deformation of the PCB substrate.
- Once the laser cutting process is complete, remove the cut PCB from the laser cutting system and inspect it for any defects or errors.
Post-processing and inspection
- Clean the laser-cut PCB to remove any debris or residue generated during the cutting process.
- Inspect the PCB for any defects, such as incomplete cuts, thermal damage, or deformation, and address any issues as necessary.
-
Perform any additional post-processing steps, such as surface finishing or soldermask application, as required by the PCB design.
-
Test the PCB to ensure that it meets the required specifications and functions as intended.
Applications of laser-cut PCBs
Laser-cut PCBs have various applications across different industries, ranging from consumer electronics to aerospace and defense. Some of the most common applications include:
-
Rapid prototyping: Laser cutting enables rapid prototyping of PCBs, allowing designers and engineers to quickly test and iterate on new designs before moving to full-scale production.
-
High-density PCBs: Laser cutting is well-suited for creating high-density PCBs with fine pitch traces and small vias, which are essential for advanced electronic devices such as smartphones, tablets, and wearables.
-
Flexible electronics: Laser cutting can be used to create flexible PCBs using materials such as polyimide, which are increasingly used in applications such as wearable devices, medical equipment, and automotive electronics.
-
RF and microwave pcbs: Laser cutting offers high precision and consistency, making it suitable for creating PCBs for high-frequency applications, such as RF and microwave circuits used in telecommunications and radar systems.
-
Aerospace and defense: Laser-cut PCBs are used in various aerospace and defense applications, where high reliability and performance are critical, such as in satellite communication systems, avionics, and military equipment.
Future trends in laser cutting PCBs
As the demand for advanced electronic devices continues to grow, the laser cutting technology for PCBs is expected to evolve to meet the increasing requirements for performance, reliability, and cost-effectiveness. Some of the future trends in laser cutting PCBs include:
-
Increased adoption of fiber lasers: Fiber lasers are expected to gain more popularity in PCB manufacturing due to their high beam quality, small focus spot size, and high cutting speed and efficiency.
-
Emergence of ultrashort pulse lasers: Ultrashort pulse lasers, such as picosecond and femtosecond lasers, are expected to become more widely used for cutting PCBs, as they offer minimal thermal damage and high precision, enabling the creation of even finer features and higher-density PCBs.
-
Integration with other manufacturing processes: Laser cutting is likely to be increasingly integrated with other PCB manufacturing processes, such as 3D printing and surface-mount technology (SMT), to create more complex and advanced electronic devices.
-
Automation and digitalization: The laser cutting process for PCBs is expected to become more automated and digitalized, with the integration of advanced software, sensors, and control systems to optimize the cutting process and ensure consistent quality.
-
Sustainable manufacturing: As environmental concerns continue to grow, there will be an increasing focus on sustainable PCB manufacturing practices, with laser cutting playing a key role in reducing waste, energy consumption, and the use of harmful chemicals.
Frequently Asked Questions (FAQ)
-
Q: Can all types of PCB substrate materials be laser cut?
A: No, not all PCB substrate materials are suitable for laser cutting. The most common materials that can be laser cut include FR4, polyimide, and ceramic. Some materials may not be suitable due to their thermal properties or tendency to produce harmful fumes when vaporized. -
Q: How accurate is laser cutting compared to traditional PCB manufacturing methods?
A: Laser cutting offers high precision, with cutting accuracies of up to ±0.05 mm, depending on the material and laser system used. This is generally more accurate than traditional PCB manufacturing methods, such as chemical etching and mechanical drilling. -
Q: Is laser cutting more expensive than traditional PCB manufacturing methods?
A: The cost of laser cutting compared to traditional PCB manufacturing methods depends on various factors, such as the production volume, PCB complexity, and the specific laser cutting system used. While the initial investment in a laser cutting system can be high, laser cutting can be more cost-effective for low-volume production or prototyping. -
Q: What are the environmental benefits of laser cutting PCBs?
A: Laser cutting is a more environmentally friendly alternative to traditional PCB manufacturing methods, as it eliminates the need for chemical etching, which can be harmful to the environment and requires proper disposal of waste materials. Additionally, laser cutting produces minimal material waste compared to traditional cutting methods. -
Q: Can laser cutting be used for high-volume PCB production?
A: Yes, laser cutting can be used for high-volume PCB production, particularly with the adoption of automated and high-speed laser cutting systems. However, the specific production volume at which laser cutting becomes more cost-effective than traditional manufacturing methods depends on various factors, such as the PCB complexity and the specific laser cutting system used.
In conclusion, laser cutting is a promising technology for manufacturing PCBs, offering high precision, speed, and environmental benefits compared to traditional methods. As the demand for advanced electronic devices continues to grow, laser cutting is expected to play an increasingly important role in PCB manufacturing, with ongoing advancements in laser technology, automation, and sustainable manufacturing practices.