Introduction
Rectifiers are essential components in electronic circuits, converting alternating current (AC) to direct current (DC). Among the various types of rectifiers, the full-wave rectifier is widely used due to its efficiency and ability to utilize both halves of the AC input cycle. The H-bridge full-wave rectifier, in particular, is a popular configuration that offers several advantages, including simplicity, high efficiency, and the ability to handle high power levels.
This guide aims to provide beginners with a comprehensive understanding of H-bridge full-wave rectifier design. We will cover the basics of rectifiers, the working principle of the H-bridge configuration, key components, design considerations, and step-by-step guidelines for designing and implementing an H-bridge full-wave rectifier.
Understanding Rectifiers
What is a Rectifier?
A rectifier is an electrical device that converts alternating current (AC), which periodically reverses direction, to direct current (DC), which flows in only one direction. Rectifiers are used in power supplies, battery chargers, and various electronic devices that require DC power.
Types of Rectifiers
- Half-Wave Rectifier: Converts only one half of the AC input cycle to DC, resulting in lower efficiency and higher ripple.
- Full-Wave Rectifier: Converts both halves of the AC input cycle to DC, offering higher efficiency and lower ripple compared to half-wave rectifiers.
- Bridge Rectifier: A type of full-wave rectifier that uses four diodes in a bridge configuration to achieve full-wave rectification.
H-Bridge Full-Wave Rectifier
The H-bridge full-wave rectifier is a specific type of bridge rectifier that uses four diodes arranged in an “H” configuration. This configuration allows for efficient full-wave rectification and is commonly used in high-power applications.
Working Principle of H-Bridge Full-Wave Rectifier
Basic Operation
The H-bridge full-wave rectifier consists of four diodes arranged in a bridge configuration. The AC input is applied across the two input terminals, and the DC output is taken from the two output terminals.
- Positive Half-Cycle: During the positive half-cycle of the AC input, diodes D1 and D3 are forward-biased and conduct current, while diodes D2 and D4 are reverse-biased and do not conduct. Current flows through D1, the load, and D3, producing a positive voltage across the load.
- Negative Half-Cycle: During the negative half-cycle of the AC input, diodes D2 and D4 are forward-biased and conduct current, while diodes D1 and D3 are reverse-biased and do not conduct. Current flows through D2, the load, and D4, producing a positive voltage across the load.
Advantages of H-Bridge Full-Wave Rectifier
- High Efficiency: Utilizes both halves of the AC input cycle, resulting in higher efficiency compared to half-wave rectifiers.
- Low Ripple: Produces a smoother DC output with lower ripple, reducing the need for extensive filtering.
- High Power Handling: Capable of handling higher power levels, making it suitable for high-power applications.
- Simplicity: Simple and robust design with only four diodes required.
Key Components of H-Bridge Full-Wave Rectifier
1. Diodes
Diodes are the core components of the H-bridge rectifier, responsible for directing the flow of current during each half-cycle of the AC input.
- Selection Criteria: When selecting diodes for an H-bridge rectifier, consider parameters such as forward voltage drop, reverse recovery time, and maximum current and voltage ratings.
- Types of Diodes: Common types of diodes used in rectifiers include silicon diodes, Schottky diodes, and fast recovery diodes.
2. Transformer
A transformer is often used to step down or step up the AC input voltage to the desired level before rectification.
- Selection Criteria: Choose a transformer with the appropriate voltage and current ratings to match the requirements of the rectifier and load.
- Turns Ratio: The turns ratio of the transformer determines the output voltage relative to the input voltage.
3. Capacitors
Capacitors are used for filtering the rectified output to reduce ripple and provide a smoother DC voltage.
- Selection Criteria: Consider capacitance value, voltage rating, and equivalent series resistance (ESR) when selecting capacitors for filtering.
- Types of Capacitors: Common types include electrolytic capacitors, ceramic capacitors, and film capacitors.
4. Load
The load is the device or circuit that consumes the DC power provided by the rectifier.
- Selection Criteria: Ensure that the load’s voltage and current requirements are within the capabilities of the rectifier.
- Types of Loads: Loads can include resistors, LEDs, motors, and other electronic devices.
Design Considerations for H-Bridge Full-Wave Rectifier
1. Voltage and Current Ratings
Ensure that all components, including diodes, transformers, and capacitors, are rated for the expected voltage and current levels in the circuit.
- Diodes: Choose diodes with a forward current rating higher than the maximum load current and a reverse voltage rating higher than the peak AC input voltage.
- Transformer: Select a transformer with a secondary voltage that matches the desired DC output voltage and a current rating that meets the load requirements.
- Capacitors: Use capacitors with a voltage rating higher than the peak rectified voltage to prevent breakdown.
2. Heat Dissipation
High-power rectifiers generate heat, which can affect the performance and lifespan of the components.
- Heat Sinks: Attach heat sinks to diodes and other heat-generating components to dissipate heat effectively.
- Thermal Management: Ensure adequate ventilation and consider using thermal vias in the PCB layout to improve heat dissipation.
3. Ripple Reduction
Ripple is the residual AC component in the rectified DC output. Minimizing ripple is essential for providing a stable DC voltage.
- Filter Capacitors: Use large filter capacitors to reduce ripple. The capacitance value should be chosen based on the load current and desired ripple voltage.
- LC Filters: In some cases, an LC filter (inductor-capacitor) can be used to further reduce ripple.
4. Efficiency
Efficiency is a critical factor in rectifier design, especially in high-power applications.
- Diode Selection: Choose diodes with low forward voltage drop and fast recovery time to minimize power loss.
- Transformer Efficiency: Use a high-efficiency transformer to reduce power loss in the conversion process.
5. Protection Circuits
Implement protection circuits to safeguard the rectifier and load from potential damage.
- Fuses: Use fuses to protect against overcurrent conditions.
- Transient Voltage Suppression (TVS) Diodes: Protect against voltage spikes and transients.
- Reverse Polarity Protection: Implement diodes or MOSFETs to prevent damage from reverse polarity connections.
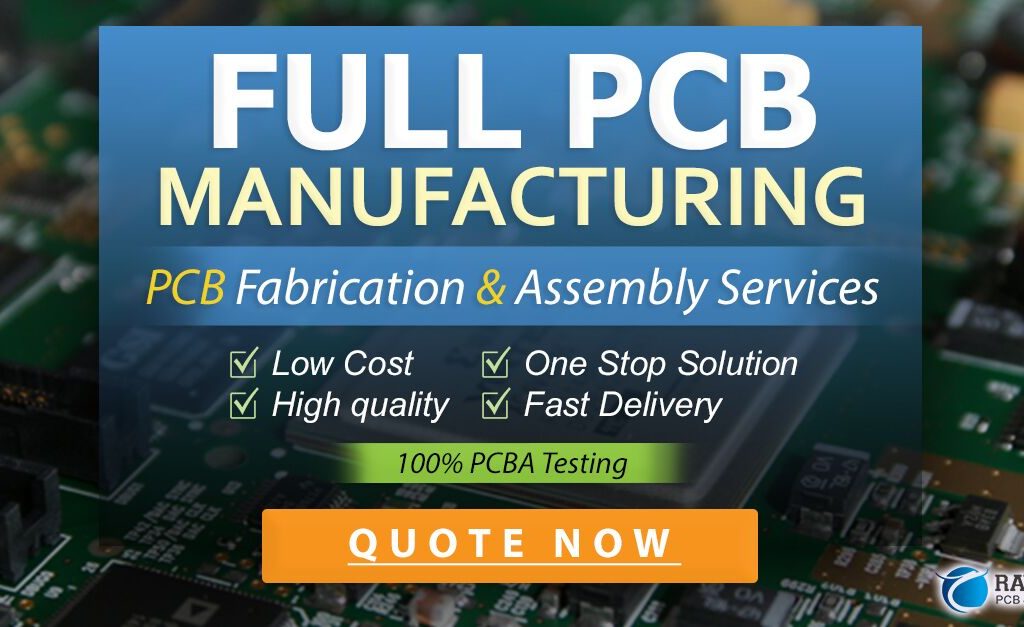
Step-by-Step Guide to Designing an H-Bridge Full-Wave Rectifier
Step 1: Define the Requirements
Start by defining the requirements for your rectifier, including:
- Input Voltage: The AC input voltage (e.g., 120V AC, 230V AC).
- Output Voltage: The desired DC output voltage.
- Load Current: The maximum current required by the load.
- Ripple Voltage: The acceptable level of ripple in the DC output.
Step 2: Select the Transformer
Choose a transformer with the appropriate turns ratio to step down or step up the AC input voltage to the desired level.
- Turns Ratio: Calculate the turns ratio based on the input and output voltage requirements.
- Current Rating: Ensure the transformer can handle the maximum load current.
Step 3: Choose the Diodes
Select diodes with the appropriate voltage and current ratings for the rectifier.
- Forward Voltage Drop: Choose diodes with a low forward voltage drop to minimize power loss.
- Reverse Recovery Time: Select diodes with a fast recovery time for high-frequency applications.
- Maximum Current and Voltage Ratings: Ensure the diodes can handle the peak current and voltage in the circuit.
Step 4: Design the Filter Circuit
Design the filter circuit to reduce ripple and provide a smooth DC output.
- Capacitor Selection: Choose filter capacitors with the appropriate capacitance and voltage rating.
- Ripple Calculation: Calculate the expected ripple voltage based on the load current and capacitor value.
Step 5: Design the PCB Layout
Design the PCB layout to ensure proper placement and routing of components.
- Component Placement: Place diodes, capacitors, and other components close to each other to minimize trace lengths.
- Trace Routing: Use wide traces for high-current paths and ensure proper grounding.
- Heat Dissipation: Include heat sinks and thermal vias for heat-generating components.
Step 6: Simulate the Circuit
Use simulation tools to model the rectifier circuit and analyze its performance.
- Voltage and Current Analysis: Verify that the circuit produces the desired output voltage and current.
- Ripple Analysis: Check the ripple voltage and ensure it meets the design requirements.
- Efficiency Calculation: Calculate the efficiency of the rectifier and identify areas for improvement.
Step 7: Build and Test the Prototype
Build a prototype of the rectifier and perform thorough testing to validate the design.
- Functional Testing: Verify that the rectifier produces the correct DC output voltage and current.
- Ripple Measurement: Measure the ripple voltage and compare it to the design specifications.
- Thermal Testing: Monitor the temperature of heat-generating components and ensure they operate within safe limits.
Step 8: Optimize and Finalize the Design
Based on the test results, optimize the design to improve performance and reliability.
- Component Selection: Replace any underperforming components with higher-rated ones.
- Layout Adjustments: Make any necessary adjustments to the PCB layout to improve heat dissipation and reduce noise.
- Final Testing: Perform final testing to ensure the rectifier meets all design requirements.
Common Mistakes to Avoid in H-Bridge Full-Wave Rectifier Design
1. Inadequate Diode Ratings
Choosing diodes with insufficient voltage or current ratings can lead to failure under load. Always select diodes with ratings that exceed the expected peak voltage and current.
2. Poor Heat Management
Neglecting heat dissipation can cause components to overheat and fail. Ensure proper heat sinking and thermal management in the design.
3. Insufficient Filtering
Inadequate filtering can result in high ripple voltage, leading to unstable DC output. Use appropriately sized filter capacitors and consider additional filtering if necessary.
4. Incorrect Transformer Selection
Using a transformer with the wrong turns ratio or current rating can result in incorrect output voltage or overload. Carefully select the transformer based on the design requirements.
5. Neglecting Protection Circuits
Failing to include protection circuits can leave the rectifier and load vulnerable to damage from overcurrent, overvoltage, or reverse polarity. Always include appropriate protection measures.
Conclusion
Designing an H-bridge full-wave rectifier is a fundamental skill for anyone involved in electronics. By understanding the working principle, selecting the right components, and following best practices in design and layout, you can create efficient and reliable rectifiers for a wide range of applications. Remember to simulate and test your designs thoroughly, and optimize them based on the results to achieve the best performance. With this beginner’s guide, you are well-equipped to embark on your journey into the world of H-bridge full-wave rectifier design.