Printed Circuit Boards (PCBs) are the backbone of modern electronics, serving as the foundation for everything from smartphones to aerospace systems. As technology advances, the demand for faster, more reliable, and higher-density PCBs has grown exponentially. However, with increased speed and complexity comes the challenge of managing signal integrity. One of the most significant issues in high-speed PCB design is signal distortion, which can lead to data errors, reduced performance, and even system failures.
One of the most effective techniques to mitigate signal distortions in high-speed PCBs is backdrilling. This article will delve into the concept of backdrilling, its importance in PCB design, and how it can be used to reduce signal distortions. We will also explore the process of backdrilling, its benefits, and best practices for implementing it in your PCB designs.
Understanding Signal Distortions in PCBs
Before diving into backdrilling, it’s essential to understand the root causes of signal distortions in PCBs. Signal distortions occur when the integrity of an electrical signal is compromised as it travels through the PCB. These distortions can manifest as signal reflections, crosstalk, attenuation, and jitter, all of which can degrade the performance of the PCB.
1. Signal Reflections
Signal reflections occur when a signal encounters an impedance mismatch along its transmission path. This mismatch can be caused by variations in trace width, changes in dielectric material, or the presence of vias. When a signal reflects, it can interfere with the original signal, leading to data errors and reduced signal quality.
2. Crosstalk
Crosstalk is the unwanted coupling of signals between adjacent traces. As PCB designs become more compact, the distance between traces decreases, increasing the likelihood of crosstalk. This can result in signal interference, leading to data corruption and reduced performance.
3. Attenuation
Attenuation refers to the loss of signal strength as it travels through the PCB. This loss can be caused by the resistance of the traces, dielectric losses, and skin effect (where high-frequency signals tend to travel near the surface of the conductor). Attenuation can lead to weaker signals, making it difficult for the receiver to accurately interpret the data.
4. Jitter
Jitter is the variation in the timing of a signal’s transitions. It can be caused by noise, crosstalk, and reflections. Jitter can lead to timing errors, making it difficult for the receiver to correctly interpret the signal.
The Role of Vias in Signal Distortions
Vias are essential components in PCB design, providing electrical connections between different layers of the board. However, they can also be a significant source of signal distortions, particularly in high-speed designs.
1. Stub Effects
When a via is used to connect a signal from one layer to another, the portion of the via that extends beyond the target layer is known as a “stub.” Stubs can act as antennas, reflecting signals back into the transmission line and causing signal distortions. The longer the stub, the more pronounced the effect.
2. Impedance Discontinuities
Vias can also introduce impedance discontinuities, which can cause signal reflections. The transition from a trace to a via and back to a trace can create an impedance mismatch, leading to reflections and signal degradation.
3. Capacitive and Inductive Effects
Vias have inherent capacitance and inductance, which can affect the signal’s rise time and overall integrity. These effects become more pronounced at higher frequencies, making vias a critical consideration in high-speed PCB design.
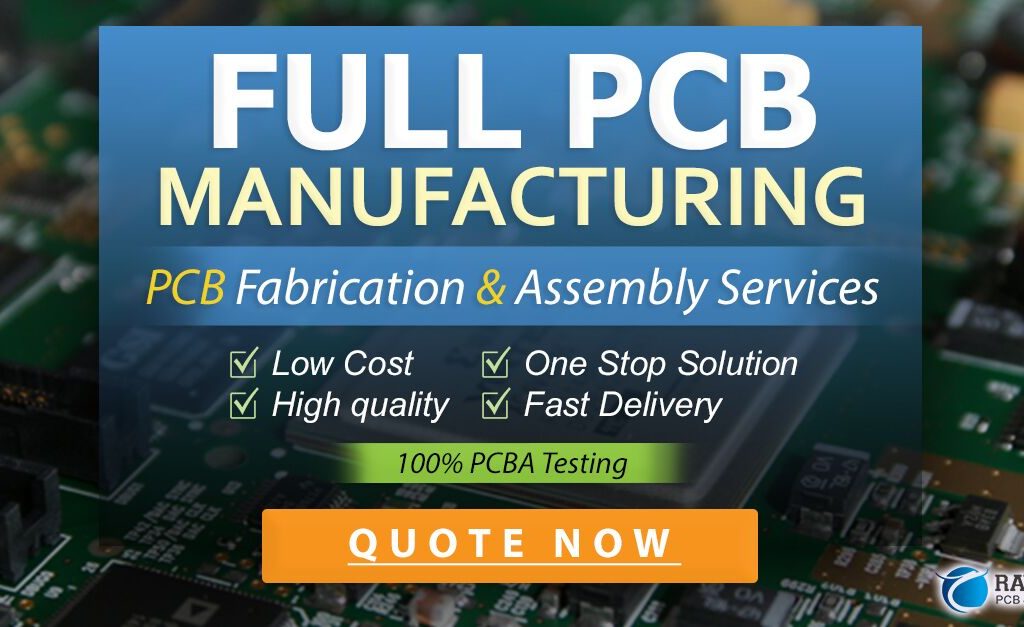
What is Backdrilling?
Backdrilling, also known as controlled-depth drilling or stub removal, is a PCB manufacturing technique used to remove the unused portion of a via stub. By eliminating the stub, backdrilling reduces signal reflections, improves signal integrity, and enhances the overall performance of the PCB.
How Backdrilling Works
- Identify the Target Layer: The first step in backdrilling is to identify the target layer where the via connects. This is the layer where the signal needs to be transmitted.
- Drill the Via: A standard via is drilled through the entire thickness of the PCB, connecting all layers.
- Backdrill the Via: A second drilling operation is performed, but this time the drill bit is carefully controlled to stop just above the target layer. This removes the portion of the via that extends beyond the target layer, effectively eliminating the stub.
- Clean the Via: After backdrilling, the via is cleaned to remove any debris or residue from the drilling process.
Benefits of Backdrilling
- Reduced Signal Reflections: By removing the via stub, backdrilling minimizes signal reflections, leading to cleaner and more reliable signals.
- Improved Signal Integrity: Backdrilling helps maintain consistent impedance along the signal path, reducing the risk of impedance discontinuities and improving overall signal integrity.
- Enhanced High-Speed Performance: Backdrilling is particularly beneficial in high-speed designs, where signal distortions can have a significant impact on performance. By reducing reflections and crosstalk, backdrilling allows for faster and more reliable data transmission.
- Reduced Jitter: By minimizing signal distortions, backdrilling can help reduce jitter, leading to more accurate timing and better overall performance.
- Cost-Effective Solution: Compared to other techniques for improving signal integrity, such as using blind or buried vias, backdrilling is a relatively cost-effective solution. It allows designers to achieve high-performance results without significantly increasing the complexity or cost of the PCB.
When to Use Backdrilling
Backdrilling is not always necessary, but it can be highly beneficial in certain scenarios. Here are some situations where backdrilling may be appropriate:
- High-Speed Designs: Backdrilling is particularly useful in high-speed PCB designs, where signal integrity is critical. It is commonly used in applications such as telecommunications, data centers, and high-performance computing.
- Long Traces: In designs with long traces, the effects of signal reflections and crosstalk can be more pronounced. Backdrilling can help mitigate these issues, ensuring reliable signal transmission over long distances.
- High-Density Designs: In high-density PCB designs, where traces are closely spaced, crosstalk and signal reflections can be significant challenges. Backdrilling can help reduce these effects, improving overall performance.
- Impedance-Sensitive Designs: In designs where maintaining consistent impedance is critical, backdrilling can help reduce impedance discontinuities caused by vias.
Best Practices for Backdrilling
To achieve the best results with backdrilling, it’s essential to follow some best practices:
- Plan Ahead: Backdrilling should be considered early in the design process. Identify the layers and vias that will require backdrilling and plan the layout accordingly.
- Use Appropriate Drill Sizes: The size of the backdrill should be carefully selected to ensure that it removes the stub without damaging the target layer. Typically, the backdrill size is slightly larger than the original via.
- Control Drill Depth: Precise control of the drill depth is critical to successful backdrilling. The drill should stop just above the target layer to avoid damaging the connection.
- Clean the Vias: After backdrilling, it’s essential to clean the vias thoroughly to remove any debris or residue. This ensures a reliable electrical connection and prevents potential issues during assembly.
- Test and Validate: After backdrilling, it’s important to test the PCB to ensure that the desired improvements in signal integrity have been achieved. This may involve signal integrity analysis, impedance testing, and other validation techniques.
- Work with Experienced Manufacturers: Backdrilling requires precision and expertise. Working with an experienced PCB manufacturer who is familiar with backdrilling techniques can help ensure a successful outcome.
Challenges and Limitations of Backdrilling
While backdrilling offers many benefits, it is not without its challenges and limitations:
- Increased Manufacturing Complexity: Backdrilling adds an additional step to the PCB manufacturing process, which can increase complexity and cost. It requires precise control of drill depth and alignment, which can be challenging.
- Limited to Certain Layers: Backdrilling is most effective for removing stubs on outer layers. For inner layers, other techniques such as blind or buried vias may be more appropriate.
- Potential for Drill Breakout: If the backdrill is not precisely controlled, there is a risk of drill breakout, where the drill extends beyond the intended depth and damages the target layer. This can lead to manufacturing defects and reduced yield.
- Not Always Necessary: In some designs, the impact of via stubs may be minimal, and backdrilling may not provide significant benefits. It’s important to carefully evaluate whether backdrilling is necessary for a particular design.
Alternatives to Backdrilling
While backdrilling is an effective technique for reducing signal distortions, it is not the only option. Here are some alternatives that may be considered:
- Blind and Buried Vias: Blind vias connect an outer layer to one or more inner layers, while buried vias connect inner layers without reaching the outer layers. These types of vias eliminate stubs entirely, providing excellent signal integrity. However, they can be more expensive and complex to manufacture.
- Microvias: Microvias are small vias typically used in high-density interconnect (HDI) PCBs. They are often used in conjunction with blind and buried vias to create complex multilayer connections. Microvias can help reduce signal distortions, but they also add to the complexity and cost of the PCB.
- Impedance Matching: Careful design of trace widths, spacing, and dielectric materials can help maintain consistent impedance and reduce signal reflections. Impedance matching is a critical aspect of high-speed PCB design and can help mitigate the need for backdrilling in some cases.
- Signal Conditioning: Techniques such as equalization, pre-emphasis, and de-emphasis can be used to compensate for signal distortions. These techniques are often used in high-speed serial interfaces to improve signal integrity.
Conclusion
In the world of high-speed PCB design, signal integrity is paramount. Signal distortions can lead to data errors, reduced performance, and system failures, making it essential to employ techniques that minimize these issues. Backdrilling is a powerful tool in the PCB designer’s arsenal, offering a cost-effective way to reduce signal reflections, improve signal integrity, and enhance overall performance.
By understanding the causes of signal distortions, the role of vias, and the benefits of backdrilling, designers can make informed decisions about when and how to use this technique. While backdrilling is not without its challenges, careful planning, precise execution, and collaboration with experienced manufacturers can help ensure successful outcomes.
As technology continues to advance, the demand for high-speed, high-performance PCBs will only grow. Backdrilling, along with other signal integrity techniques, will play a crucial role in meeting these demands, enabling the development of faster, more reliable, and more complex electronic systems. So, the next time you’re faced with the challenge of signal distortions on your PCB, remember: backdrill it, baby!