Introduction to Green PCBs
Green PCBs, also known as solder mask green PCBs, have become increasingly popular in the electronics industry due to their distinctive appearance and potential cost-saving benefits. In this comprehensive article, we will explore the concept of green PCBs, their manufacturing process, and whether they offer a more cost-effective solution compared to other PCB colors.
What are Green PCBs?
Green PCBs are printed circuit boards that feature a green solder mask layer. The solder mask is a protective coating applied to the copper traces on the PCB, leaving only the exposed areas where components will be soldered. The green color is achieved by adding pigments to the solder mask material during the manufacturing process.
Why Choose Green PCBs?
There are several reasons why manufacturers and designers opt for green PCBs:
- Aesthetics: Green PCBs have a distinct and professional appearance that appeals to many users.
- Contrast: The green color provides excellent contrast against the white silkscreen, making it easier to read component labels and track routing.
- Durability: Green solder mask is known for its durability and resistance to scratches and abrasions.
- Cost: Some manufacturers claim that green PCBs are more cost-effective compared to other colors.
The Manufacturing Process of Green PCBs
To understand the potential cost implications of green PCBs, let’s dive into the manufacturing process.
PCB Fabrication Steps
The basic steps involved in PCB fabrication are as follows:
- Design: The PCB design is created using CAD software, specifying the layout, components, and connections.
- Printing: The design is printed onto a copper-clad laminate using a photoresist process.
- Etching: The unwanted copper is removed through an etching process, leaving only the desired traces.
- Drilling: Holes are drilled into the PCB for component placement and vias.
- Solder Mask Application: The solder mask layer is applied to the PCB, covering the copper traces while leaving the pads exposed.
- Silkscreen Printing: The white silkscreen layer is printed onto the PCB, adding labels, logos, and other markings.
- Surface Finish: A surface finish, such as HASL or ENIG, is applied to the exposed pads to prevent oxidation and enhance solderability.
- Cutting and Routing: The PCB panel is cut and routed to the desired shape and size.
- Quality Control: The finished PCBs undergo rigorous quality control tests to ensure they meet the required specifications.
Solder Mask Application in Green PCBs
The solder mask application step is where the green color comes into play. The solder mask is typically applied using a silkscreen printing process or a liquid photo imageable (LPI) process.
In the silkscreen printing process, the green solder mask ink is applied through a fine mesh screen onto the PCB. The screen has a stencil of the desired solder mask pattern, allowing the ink to pass through only in the required areas.
In the LPI process, a photosensitive polymer is applied to the PCB and then exposed to UV light through a photomask. The exposed areas harden, while the unexposed areas are washed away, leaving the desired solder mask pattern.
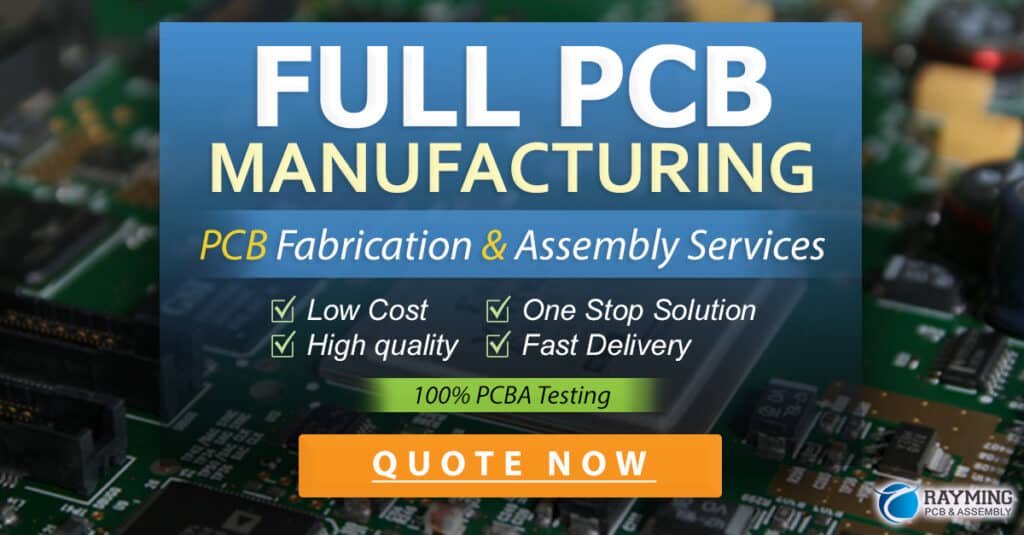
Cost Comparison of Green PCBs
Now, let’s address the main question: are green PCBs cheaper compared to other colors? The answer is not straightforward, as several factors influence the cost of PCB manufacturing.
Factors Affecting PCB Cost
- PCB Size: Larger PCBs generally cost more due to the increased material and processing requirements.
- Layer Count: Multi-layer PCBs are more expensive than single-layer or double-layer boards due to the additional manufacturing steps involved.
- Quantity: Higher quantities of PCBs often result in lower unit costs due to economies of scale.
- Design Complexity: Complex designs with fine pitch components, high-density layouts, or strict tolerances may incur higher manufacturing costs.
- Surface Finish: The choice of surface finish, such as HASL, ENIG, or OSP, can impact the overall cost of the PCB.
- Turnaround Time: Faster turnaround times may come with a price premium, while standard lead times are generally more cost-effective.
Green PCB Cost Comparison
When it comes to the cost of green PCBs specifically, there are a few considerations:
- Solder Mask Material: The cost of green solder mask material is similar to that of other standard colors like red, blue, or black. There is no significant price difference based on color alone.
- Pigment Additives: The green pigments used in the solder mask may have a slight impact on the material cost, but this is generally negligible in the overall PCB manufacturing process.
- Manufacturer Pricing: Some PCB manufacturers may offer competitive pricing for green PCBs as a marketing strategy to attract customers who prefer this color.
To provide a clearer picture, let’s compare the prices of green PCBs with other colors from a few popular PCB manufacturers:
Manufacturer | PCB Specifications | Green PCB Price | Other Color Price |
---|---|---|---|
PCBWay | 2 layers, 100x100mm, 10 pcs | $5 | $5 |
JLCPCB | 2 layers, 100x100mm, 10 pcs | $2 | $2 |
OSHPark | 2 layers, 100x100mm, 3 pcs | $10 | $10 |
As evident from the table, the prices for green PCBs are identical to those of other colors for the same specifications. This suggests that the color of the solder mask does not have a significant impact on the overall cost of the PCB.
Benefits and Drawbacks of Green PCBs
While green PCBs offer several advantages, there are also some potential drawbacks to consider.
Benefits of Green PCBs
- Visual Appeal: Green PCBs have a professional and attractive appearance that can enhance the overall look of the final product.
- Improved Contrast: The green solder mask provides excellent contrast against the white silkscreen, making it easier to read component labels and track routing.
- Durability: Green solder mask is known for its durability and resistance to scratches and abrasions, ensuring the longevity of the PCB.
- Widespread Availability: Green is a standard color option offered by most PCB manufacturers, making it easy to source green PCBs from various suppliers.
Drawbacks of Green PCBs
- Limited Design Flexibility: While green is a popular color choice, it may not always align with the desired aesthetic of the final product. Some designs may require specific color schemes that are not compatible with green PCBs.
- Potential for Color Variations: The shade of green used by different PCB manufacturers may vary slightly, which could lead to inconsistencies in the appearance of the final product if sourcing from multiple suppliers.
- Optical Inspection Challenges: In some cases, the green solder mask may make it more difficult to visually inspect the PCB for defects or issues, especially when compared to lighter colors like white or yellow.
Frequently Asked Questions (FAQ)
-
Q: Are green PCBs more expensive than other colors?
A: No, green PCBs are generally not more expensive than other standard colors like red, blue, or black. The color of the solder mask does not significantly impact the overall cost of the PCB. -
Q: Can I order green PCBs in small quantities?
A: Yes, most PCB manufacturers offer green PCBs in small quantities, even for prototype or low-volume production runs. The minimum order quantity (MOQ) varies depending on the manufacturer but can be as low as 5 or 10 pieces. -
Q: Are there any technical advantages to using green PCBs?
A: Green PCBs offer good contrast against the white silkscreen, making it easier to read component labels and track routing. However, there are no significant technical advantages compared to other standard PCB colors. -
Q: Can I customize the shade of green used for my PCBs?
A: Most PCB manufacturers have a standard shade of green used for their solder mask. Customizing the shade of green may be possible but could incur additional costs and minimum order quantities. It’s best to consult with your chosen PCB manufacturer for specific options. -
Q: Are green PCBs suitable for all applications?
A: Green PCBs are suitable for a wide range of applications, including consumer electronics, industrial equipment, and automotive systems. However, some specific applications may have color requirements that are not compatible with green PCBs, such as medical devices or aerospace systems.
Conclusion
In conclusion, green PCBs have gained popularity in the electronics industry due to their distinct appearance, good contrast, and durability. While there is a perception that green PCBs may be cheaper, the reality is that the color of the solder mask does not significantly impact the overall cost of the PCB.
The cost of PCB manufacturing is influenced by various factors such as size, layer count, quantity, design complexity, surface finish, and turnaround time. When comparing prices from different manufacturers, green PCBs are typically priced similarly to other standard colors for the same specifications.
Green PCBs offer several benefits, including visual appeal, improved contrast, and widespread availability. However, they may have limited design flexibility, potential for color variations, and optical inspection challenges in some cases.
Ultimately, the choice of green PCBs depends on the specific requirements and preferences of the project. If green aligns with the desired aesthetic and meets the technical requirements, it can be an excellent option for PCB fabrication.
When sourcing green PCBs, it’s essential to work with reputable PCB manufacturers who have experience in producing high-quality boards in various colors. By considering the factors that influence PCB cost and weighing the benefits and drawbacks of green PCBs, designers and manufacturers can make informed decisions that balance cost, appearance, and functionality.