What are Medical PCBs?
Medical PCBs are specialized printed circuit boards that are designed and manufactured to meet the unique requirements of medical devices and equipment. These PCBs must adhere to strict regulations and standards to ensure patient safety, reliability, and accuracy. Medical PCBs are typically more complex than standard PCBs and require advanced manufacturing processes to achieve the necessary level of precision and durability.
Applications of Medical PCBs
Medical PCBs find applications in a wide range of medical devices and equipment. Some of the most common applications include:
1. Medical Imaging Equipment
Medical imaging equipment, such as X-ray machines, CT scanners, and MRI machines, rely on high-performance PCBs to process and display detailed images of the human body. These PCBs must be capable of handling high-speed data processing and signal integrity to ensure accurate diagnoses.
2. Patient Monitoring Systems
Patient monitoring systems, such as ECG monitors, pulse oximeters, and blood pressure monitors, use PCBs to collect and analyze vital signs data. These PCBs must be reliable and accurate to ensure timely detection of any abnormalities in the patient’s condition.
3. Implantable Medical Devices
Implantable medical devices, such as pacemakers, defibrillators, and neurostimulators, require highly miniaturized and reliable PCBs. These PCBs must be able to withstand the harsh environment inside the human body and function flawlessly for extended periods.
4. Surgical Equipment
Surgical equipment, such as electrosurgical units, surgical robots, and laser systems, incorporate PCBs to control and monitor various functions. These PCBs must be able to withstand the rigors of the operating room environment and provide precise control over the equipment.
5. Diagnostic Equipment
Diagnostic equipment, such as blood analyzers, DNA sequencers, and point-of-care testing devices, rely on PCBs to process and analyze biological samples. These PCBs must be capable of handling complex algorithms and delivering accurate results in a timely manner.
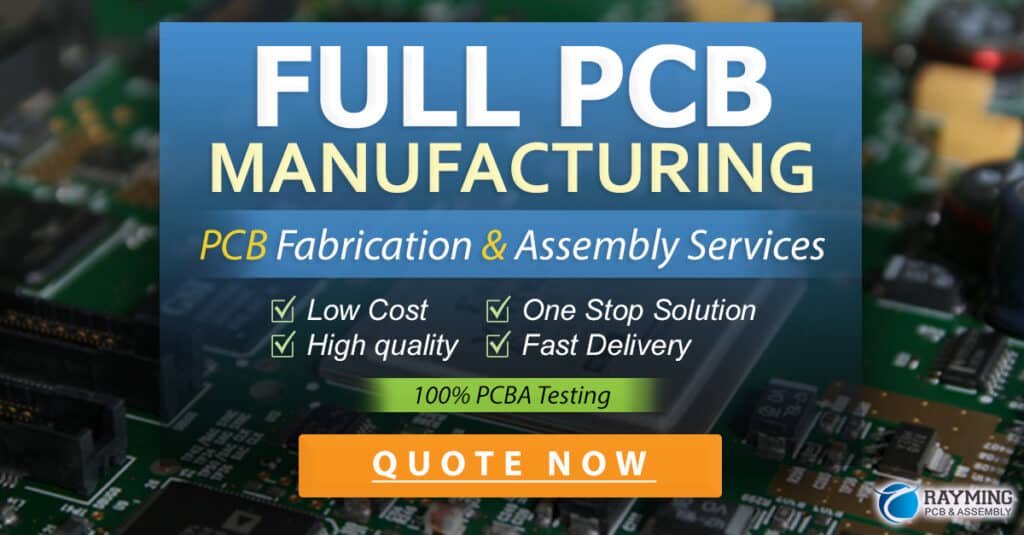
Types of Medical PCBs
Medical PCBs come in various types, each designed to meet specific requirements and applications. Some of the most common types of medical PCBs include:
1. Rigid PCBs
Rigid PCBs are the most common type of PCBs used in medical devices. They are made from a solid substrate material, such as FR-4, and offer excellent mechanical stability and durability. Rigid PCBs are suitable for a wide range of medical applications, from simple monitoring devices to complex imaging equipment.
2. Flexible PCBs
Flexible PCBs are made from a flexible substrate material, such as polyimide, and can bend and conform to various shapes. They are ideal for applications that require compact packaging or have limited space, such as implantable devices or wearable sensors. Flexible PCBs offer high reliability and resistance to vibration and shock.
3. Rigid-Flex PCBs
Rigid-flex PCBs combine the benefits of both rigid and flexible PCBs. They consist of rigid PCB sections connected by flexible PCB sections, allowing for three-dimensional packaging and improved signal integrity. Rigid-flex PCBs are commonly used in medical devices that require complex interconnections and compact packaging, such as endoscopes or surgical instruments.
4. High-Density Interconnect (HDI) PCBs
HDI PCBs feature fine pitch traces and microvias, allowing for higher component density and improved signal integrity. They are ideal for medical devices that require high-speed data processing and compact packaging, such as medical imaging equipment or diagnostic devices.
5. Multilayer PCBs
Multilayer PCBs consist of multiple layers of conductive material separated by insulating layers. They offer increased routing density and improved signal integrity compared to single-layer PCBs. Multilayer PCBs are commonly used in medical devices that require complex circuitry and high-speed data processing, such as patient monitoring systems or surgical equipment.
Medical PCB Manufacturing Process
The manufacturing process for medical PCBs is more stringent and tightly controlled compared to standard PCBs. The process typically involves the following steps:
-
Design and Layout: The PCB design is created using specialized software, taking into account the specific requirements of the medical device. The layout is optimized for signal integrity, power distribution, and component placement.
-
Material Selection: High-quality, medical-grade materials are selected for the PCB substrate, copper traces, and solder mask. These materials must meet stringent biocompatibility and durability requirements.
-
Fabrication: The PCB is fabricated using advanced manufacturing processes, such as photolithography, etching, and plating. Strict quality control measures are implemented to ensure the highest level of precision and reliability.
-
Assembly: The PCB is populated with components using automated assembly equipment. The components are carefully selected and tested to ensure they meet the required specifications.
-
Testing and Inspection: The assembled PCB undergoes rigorous testing and inspection to verify its functionality, reliability, and compliance with relevant standards. This may include electrical testing, visual inspection, and environmental stress testing.
-
Coating and Finishing: The PCB may be coated with a protective layer, such as conformal coating, to enhance its durability and resistance to environmental factors. The PCB is then cleaned and packaged for delivery.
Medical PCB Standards and Regulations
Medical PCBs must comply with various standards and regulations to ensure patient safety and device reliability. Some of the key standards and regulations include:
- IPC-6012: This standard defines the performance requirements for rigid PCBs used in medical devices.
- IPC-6013: This standard defines the performance requirements for flexible and rigid-flex PCBs used in medical devices.
- ISO 13485: This international standard specifies the quality management system requirements for medical device manufacturers.
- FDA 21 CFR Part 820: This regulation, enforced by the U.S. Food and Drug Administration (FDA), establishes the quality system requirements for medical device manufacturers.
- IEC 60601: This series of standards specifies the safety and performance requirements for medical electrical equipment.
Compliance with these standards and regulations ensures that medical PCBs meet the highest quality and safety standards, minimizing the risk of device failure or patient harm.
Challenges in Medical PCB Design and Manufacturing
Designing and manufacturing medical PCBs presents several challenges that must be addressed to ensure the highest level of quality and reliability. Some of the key challenges include:
-
Miniaturization: Many medical devices require compact packaging and miniaturized components, which can be challenging to achieve while maintaining signal integrity and reliability.
-
High-Reliability: Medical PCBs must function reliably for extended periods, often in harsh environments. Ensuring high reliability requires careful material selection, robust design, and thorough testing.
-
Electromagnetic Compatibility (EMC): Medical devices must not interfere with other electronic equipment and must be immune to electromagnetic interference. Achieving EMC compliance requires careful PCB layout and the use of shielding and filtering techniques.
-
Biocompatibility: PCBs used in implantable devices must be made from biocompatible materials that do not cause adverse reactions in the human body. Selecting appropriate materials and ensuring their long-term stability can be challenging.
-
Regulatory Compliance: Medical PCBs must comply with numerous standards and regulations, which can be complex and time-consuming. Manufacturers must have a thorough understanding of the applicable requirements and implement effective quality management systems.
Future Trends in Medical PCBs
As the medical industry continues to evolve, so do the technologies and trends in medical PCBs. Some of the future trends to watch include:
-
Wearable and Implantable Devices: The demand for wearable and implantable medical devices is expected to grow, driving the need for more compact, flexible, and biocompatible PCBs.
-
Internet of Medical Things (IoMT): The integration of medical devices with the Internet of Things (IoT) is expected to increase, enabling remote monitoring, data analytics, and personalized healthcare. This will require PCBs with advanced connectivity and data processing capabilities.
-
3D Printing: 3D printing technology is being explored for the fabrication of PCBs, offering the potential for rapid prototyping, customization, and complex geometries.
-
Advanced Materials: New materials, such as graphene and carbon nanotubes, are being investigated for their potential applications in medical PCBs, offering improved conductivity, flexibility, and biocompatibility.
-
Artificial Intelligence (AI) and Machine Learning (ML): The integration of AI and ML algorithms into medical devices is expected to increase, enabling more advanced data analysis and decision support. This will require PCBs with high-performance processing capabilities.
Frequently Asked Questions (FAQ)
-
What is the difference between medical PCBs and standard PCBs?
Medical PCBs are designed and manufactured to meet the unique requirements of medical devices and equipment, such as high reliability, biocompatibility, and compliance with strict regulations and standards. Standard PCBs, on the other hand, are designed for general-purpose applications and may not meet the same level of quality and safety requirements. -
What are the key standards and regulations for medical PCBs?
Some of the key standards and regulations for medical PCBs include IPC-6012 and IPC-6013 for performance requirements, ISO 13485 for quality management systems, FDA 21 CFR Part 820 for quality system requirements, and IEC 60601 for safety and performance requirements for medical electrical equipment. -
What are the challenges in designing and manufacturing medical PCBs?
The challenges in designing and manufacturing medical PCBs include miniaturization, high reliability, electromagnetic compatibility, biocompatibility, and regulatory compliance. Addressing these challenges requires careful design, material selection, manufacturing processes, and testing. -
What are the future trends in medical PCBs?
Future trends in medical PCBs include the growth of wearable and implantable devices, the integration of medical devices with the Internet of Things (IoMT), the use of 3D printing for PCB fabrication, the exploration of advanced materials, and the integration of artificial intelligence (AI) and machine learning (ML) algorithms. -
How can I ensure the quality and reliability of medical PCBs?
To ensure the quality and reliability of medical PCBs, it is essential to work with experienced and certified PCB manufacturers who have a thorough understanding of the applicable standards and regulations. Implementing effective quality management systems, using high-quality materials, and conducting rigorous testing and inspection are also crucial for ensuring the highest level of quality and reliability.
Conclusion
Medical PCBs play a vital role in the development and functionality of medical devices and equipment. They are designed and manufactured to meet the unique requirements of the medical industry, ensuring patient safety, device reliability, and compliance with strict regulations and standards.
From medical imaging equipment to implantable devices, medical PCBs find applications in a wide range of medical technologies. The various types of medical PCBs, such as rigid, flexible, rigid-flex, HDI, and multilayer PCBs, offer specific benefits and are selected based on the requirements of the medical device.
The manufacturing process for medical PCBs is more stringent and tightly controlled compared to standard PCBs, involving careful design, material selection, fabrication, assembly, testing, and finishing. Compliance with relevant standards and regulations, such as IPC-6012, IPC-6013, ISO 13485, FDA 21 CFR Part 820, and IEC 60601, is essential to ensure the highest level of quality and safety.
Designing and manufacturing medical PCBs presents several challenges, including miniaturization, high reliability, electromagnetic compatibility, biocompatibility, and regulatory compliance. Addressing these challenges requires expertise, advanced technologies, and a commitment to quality.
The future of medical PCBs is exciting, with trends such as wearable and implantable devices, IoMT integration, 3D printing, advanced materials, and AI/ML integration driving innovation and growth. As the medical industry continues to evolve, PCB manufacturers must stay at the forefront of technology and adapt to the changing needs of healthcare providers and patients.
By understanding the applications, types, manufacturing processes, standards, challenges, and future trends of medical PCBs, designers, manufacturers, and healthcare professionals can collaborate to develop innovative and reliable medical devices that improve patient outcomes and advance the field of medicine.