Introduction
AC to DC power supply design is a fundamental aspect of electronics engineering, enabling the conversion of alternating current (AC) from the mains supply to direct current (DC) required by most electronic devices. This process involves several stages, including rectification, filtering, regulation, and protection. This article provides an in-depth exploration of AC to DC power supply design, covering the key components, design considerations, and best practices for creating efficient and reliable power supplies.
Understanding AC to DC Power Supply
What is an AC to DC Power Supply?
An AC to DC power supply is a device that converts AC voltage from the mains supply into a stable DC voltage suitable for powering electronic circuits. This conversion is essential because most electronic devices operate on DC power, while the mains supply provides AC power.
Key Components of an AC to DC Power Supply
The primary components of an AC to DC power supply include:
- Transformer: Steps down the high AC voltage from the mains to a lower AC voltage.
- Rectifier: Converts the AC voltage to pulsating DC voltage.
- Filter: Smooths the pulsating DC voltage to produce a more stable DC voltage.
- Regulator: Maintains a constant DC output voltage despite variations in input voltage and load conditions.
- Protection Circuitry: Provides protection against overvoltage, overcurrent, and short circuits.
Stages of AC to DC Power Supply Design
Step 1: Transformer
Function
The transformer is the first stage in an AC to DC power supply. It steps down the high AC voltage from the mains (typically 110V or 230V) to a lower AC voltage suitable for the subsequent stages.
Design Considerations
- Voltage Rating: The transformer’s secondary voltage should match the desired DC output voltage, considering the voltage drops in the rectifier and regulator.
- Current Rating: The transformer must be capable of supplying the maximum current required by the load.
- Efficiency: Choose a transformer with high efficiency to minimize power losses.
- Size and Weight: Consider the physical size and weight, especially for portable applications.
Step 2: Rectifier
Function
The rectifier converts the AC voltage from the transformer into pulsating DC voltage. There are two main types of rectifiers:
- Half-Wave Rectifier: Uses a single diode to allow only one half of the AC waveform to pass.
- Full-Wave Rectifier: Uses four diodes in a bridge configuration to allow both halves of the AC waveform to pass, resulting in a more efficient conversion.
Design Considerations
- Diode Selection: Choose diodes with appropriate voltage and current ratings. Schottky diodes are often preferred for their low forward voltage drop.
- Heat Dissipation: Ensure adequate heat dissipation for the diodes, especially in high-current applications.
- Efficiency: Full-wave rectifiers are more efficient than half-wave rectifiers and are generally preferred.
Step 3: Filter
Function
The filter smooths the pulsating DC voltage from the rectifier to produce a more stable DC voltage. This is typically achieved using capacitors.
Design Considerations
- Capacitor Value: The capacitance value determines the level of smoothing. Larger capacitors provide better smoothing but increase the size and cost.
- Voltage Rating: The capacitor must have a voltage rating higher than the peak rectified voltage.
- ESR (Equivalent Series Resistance): Low ESR capacitors are preferred to minimize power losses and improve performance.
- Ripple Voltage: The filter should reduce the ripple voltage to an acceptable level for the application.
Step 4: Regulator
Function
The regulator maintains a constant DC output voltage despite variations in input voltage and load conditions. There are two main types of regulators:
- Linear Regulator: Provides a stable output voltage with low noise but is less efficient due to power dissipation in the regulator.
- Switching Regulator: More efficient than linear regulators, especially for high-current applications, but can introduce more noise.
Design Considerations
- Output Voltage: Choose a regulator that provides the desired output voltage.
- Current Rating: Ensure the regulator can handle the maximum load current.
- Efficiency: Consider the efficiency of the regulator, especially for battery-powered applications.
- Heat Dissipation: Provide adequate heat dissipation for linear regulators, which can generate significant heat.
Step 5: Protection Circuitry
Function
Protection circuitry safeguards the power supply and the connected load from potential damage due to overvoltage, overcurrent, and short circuits.
Design Considerations
- Overvoltage Protection: Use components like Zener diodes or transient voltage suppressors (TVS) to protect against voltage spikes.
- Overcurrent Protection: Implement fuses or current-limiting circuits to protect against excessive current.
- Short Circuit Protection: Design the power supply to withstand short circuits without damage, using techniques like foldback current limiting.
- Thermal Protection: Include thermal shutdown features to prevent overheating.
Design Considerations for AC to DC Power Supply
Efficiency
Efficiency is a critical factor in power supply design, especially for battery-powered devices and high-power applications. Key considerations include:
- Component Selection: Choose components with low power losses, such as high-efficiency transformers, low ESR capacitors, and efficient regulators.
- Topology: Consider using switching regulators instead of linear regulators for higher efficiency.
- Heat Management: Implement effective heat dissipation techniques to minimize power losses due to heat.
Size and Weight
The physical size and weight of the power supply are important considerations, especially for portable and space-constrained applications. Key considerations include:
- Component Size: Use compact components, such as surface-mount devices (SMDs) and small transformers.
- PCB Layout: Optimize the PCB layout to minimize the footprint and ensure efficient use of space.
- Heat Dissipation: Use efficient heat dissipation techniques to reduce the need for large heat sinks.
Reliability
Reliability is crucial for ensuring the long-term performance and safety of the power supply. Key considerations include:
- Component Quality: Use high-quality components from reputable manufacturers.
- Protection Circuitry: Implement robust protection circuitry to safeguard against overvoltage, overcurrent, and short circuits.
- Thermal Management: Ensure adequate thermal management to prevent overheating and component failure.
- Testing and Validation: Perform thorough testing and validation to identify and address potential issues.
Cost
Cost is an important factor in power supply design, especially for high-volume production. Key considerations include:
- Component Cost: Choose cost-effective components without compromising on quality and performance.
- Manufacturing Cost: Optimize the design for ease of manufacturing and assembly to reduce production costs.
- Lifecycle Cost: Consider the total cost of ownership, including maintenance and replacement costs.
Compliance and Safety
Compliance with regulatory standards and safety requirements is essential for market acceptance and user safety. Key considerations include:
- Regulatory Standards: Ensure compliance with relevant standards, such as UL, CE, and FCC.
- Safety Features: Implement safety features, such as isolation, grounding, and protection circuitry.
- Certification: Obtain necessary certifications to demonstrate compliance with regulatory and safety requirements.
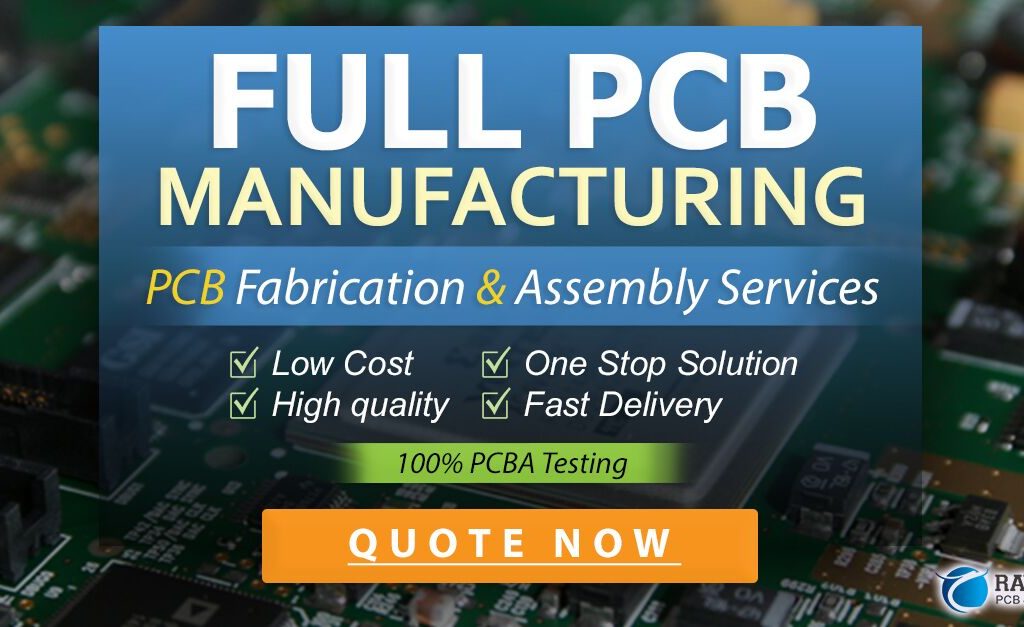
Best Practices for AC to DC Power Supply Design
Use Simulation Tools
Simulation tools can help optimize the design and identify potential issues before prototyping. Key simulation activities include:
- Circuit Simulation: Simulate the entire power supply circuit to verify performance and identify potential issues.
- Thermal Simulation: Perform thermal simulation to assess heat dissipation and identify hotspots.
- Signal Integrity Analysis: Analyze signal integrity to ensure stable and reliable operation.
Optimize PCB Layout
The PCB layout plays a critical role in the performance and reliability of the power supply. Key layout considerations include:
- Component Placement: Place components to minimize trace lengths and reduce parasitic inductance and capacitance.
- Grounding: Implement a solid ground plane to provide a low-impedance return path and reduce noise.
- Routing: Use wide traces for high-current paths and minimize the use of vias to reduce impedance.
- Heat Dissipation: Place heat-generating components, such as regulators and diodes, to facilitate effective heat dissipation.
Implement Effective Heat Management
Heat management is crucial for ensuring the reliability and longevity of the power supply. Key heat management practices include:
- Heat Sinks: Use heat sinks for components that generate significant heat, such as linear regulators and power diodes.
- Thermal Vias: Implement thermal vias to dissipate heat from components to the PCB’s ground plane.
- Airflow: Ensure adequate airflow around heat-generating components, especially in enclosed designs.
Perform Thorough Testing and Validation
Thorough testing and validation are essential for ensuring the performance and reliability of the power supply. Key testing activities include:
- Functional Testing: Verify that the power supply provides the correct output voltage and current under various load conditions.
- Thermal Testing: Assess the thermal performance to ensure that components operate within their specified temperature ranges.
- Safety Testing: Perform safety testing to verify compliance with regulatory and safety standards.
- Reliability Testing: Conduct reliability testing to identify potential failure modes and ensure long-term performance.
Collaborate with Manufacturers
Collaborating with component manufacturers and PCB fabricators can provide valuable insights and support for optimizing the design. Key collaboration activities include:
- Component Selection: Work with manufacturers to select the best components for the design.
- Design Reviews: Participate in design reviews with manufacturers to identify and address potential issues.
- Prototyping: Collaborate with manufacturers to prototype and test the design before mass production.
Case Studies
Case Study 1: Consumer Electronics
Application: AC to DC Power Supply for a Smartphone Charger
Challenges:
- High efficiency required for fast charging
- Compact size and lightweight design
- Compliance with safety and regulatory standards
Solution:
- Used a high-efficiency switching regulator
- Optimized PCB layout for compact size and effective heat dissipation
- Implemented robust protection circuitry and obtained necessary certifications
Outcome:
- High-efficiency power supply enabling fast charging
- Compact and lightweight design suitable for portable use
- Compliance with safety and regulatory standards
Case Study 2: Industrial Automation
Application: AC to DC Power Supply for an Industrial Control System
Challenges:
- High reliability and uptime requirements
- Harsh operating environment with high temperature and vibration
- Stringent safety and regulatory requirements
Solution:
- Used high-quality components with high temperature and vibration tolerance
- Implemented effective heat management and robust protection circuitry
- Performed thorough testing and validation to ensure reliability and compliance
Outcome:
- High-reliability power supply meeting stringent uptime requirements
- Robust design suitable for harsh industrial environments
- Compliance with safety and regulatory standards
Case Study 3: Automotive Electronics
Application: AC to DC Power Supply for an Automotive Infotainment System
Challenges:
- High reliability and safety requirements
- Limited PCB space and weight constraints
- Compliance with automotive standards
Solution:
- Used compact and high-efficiency components
- Optimized PCB layout for space and weight constraints
- Implemented robust protection circuitry and obtained necessary automotive certifications
Outcome:
- High-reliability power supply meeting automotive safety requirements
- Compact and lightweight design suitable for automotive applications
- Compliance with automotive standards
Conclusion
AC to DC power supply design is a critical aspect of electronics engineering, enabling the conversion of AC mains power to stable DC power required by most electronic devices. By understanding the key components, design considerations, and best practices, engineers can create efficient, reliable, and cost-effective power supplies. Whether designing for consumer electronics, industrial automation, or automotive applications, a well-designed AC to DC power supply is essential for ensuring the performance and reliability of electronic devices.