Introduction
In the realm of Printed Circuit Board (PCB) design, the Bill of Materials (BOM) is a critical document that lists all the components required to build the board. Among the various entries in a BOM, “Do Not Install” (DNI) and “Do Not Populate” (DNP) are particularly important. These entries indicate components that are included in the schematic but should not be installed or populated on the PCB during assembly. Properly managing DNI/DNP entries is essential for ensuring accurate manufacturing, reducing costs, and avoiding errors. This article explores the best practices for using schematic DNI/DNP entries in your PCB BOM, providing a comprehensive guide for engineers and designers.
Understanding DNI and DNP Entries
What are DNI and DNP Entries?
- DNI (Do Not Install): Indicates that a component should not be installed on the PCB. This could be due to various reasons such as design flexibility, future upgrades, or cost-saving measures.
- DNP (Do Not Populate): Similar to DNI, DNP indicates that a component should not be populated on the PCB. The terms are often used interchangeably, but some organizations may have specific definitions for each.
Importance of DNI/DNP Entries
- Design Flexibility: Allows for future modifications or upgrades without redesigning the entire PCB.
- Cost Savings: Reduces the number of components that need to be purchased and assembled, lowering overall costs.
- Error Prevention: Clearly communicates to the manufacturing team which components should not be installed, reducing the risk of assembly errors.
Best Practices for Using DNI/DNP Entries
1. Clearly Define DNI/DNP in Your Design Guidelines
Establishing clear definitions and guidelines for DNI/DNP entries is the first step towards effective management.
- Standardize Terminology: Decide whether to use DNI, DNP, or both, and ensure all team members understand the definitions.
- Documentation: Include detailed instructions in your design guidelines and BOM templates to ensure consistency across projects.
2. Use Consistent Naming Conventions
Consistency in naming conventions helps avoid confusion and ensures that DNI/DNP entries are easily identifiable.
- Prefix/Suffix: Use a consistent prefix or suffix (e.g., “DNI_”, “_DNP”) to label components that should not be installed or populated.
- BOM Columns: Add specific columns in the BOM for DNI/DNP status, making it clear which components are affected.
3. Annotate Schematics Clearly
Clear annotation on schematics helps both the design and manufacturing teams understand which components are DNI/DNP.
- Symbols: Use distinct symbols or labels on the schematic to indicate DNI/DNP components.
- Notes: Add notes or comments directly on the schematic to provide additional context or instructions.
4. Communicate with the Manufacturing Team
Effective communication with the manufacturing team is crucial to ensure that DNI/DNP entries are correctly interpreted and implemented.
- Pre-Production Meetings: Discuss DNI/DNP entries during pre-production meetings to clarify any ambiguities.
- Manufacturing Drawings: Include detailed manufacturing drawings that highlight DNI/DNP components and provide clear instructions.
5. Leverage BOM Management Tools
Utilizing BOM management tools can streamline the process of managing DNI/DNP entries and reduce the risk of errors.
- BOM Software: Use BOM management software that supports DNI/DNP entries and allows for easy filtering and sorting.
- Integration: Ensure that your BOM management tool integrates seamlessly with your schematic capture and PCB design tools.
6. Regularly Review and Update DNI/DNP Entries
Regular reviews and updates of DNI/DNP entries help maintain accuracy and relevance throughout the design and manufacturing process.
- Design Reviews: Include DNI/DNP entries in regular design reviews to ensure they are still applicable and correctly annotated.
- Change Management: Implement a robust change management process to track updates to DNI/DNP entries and communicate changes to all stakeholders.
7. Consider the Impact on Testing and Debugging
DNI/DNP entries can impact testing and debugging processes, so it’s important to plan accordingly.
- Test Points: Ensure that test points associated with DNI/DNP components are clearly marked and accessible if needed.
- Debugging: Consider the potential need for debugging or rework and plan for easy access to DNI/DNP components if they need to be installed later.
8. Document Rationale for DNI/DNP Entries
Documenting the rationale behind DNI/DNP entries provides valuable context for future reference and decision-making.
- Design Decisions: Record the reasons for marking components as DNI/DNP, such as cost savings, design flexibility, or future upgrades.
- Project Documentation: Include this information in project documentation and design reviews to ensure transparency and continuity.
9. Train Your Team
Ensuring that all team members are familiar with the best practices for DNI/DNP entries is essential for consistent implementation.
- Training Programs: Provide training sessions on the importance and proper use of DNI/DNP entries.
- Guidelines: Distribute clear guidelines and documentation to all team members to reinforce best practices.
10. Monitor and Improve Processes
Continuous monitoring and improvement of processes related to DNI/DNP entries can lead to better outcomes and fewer errors.
- Feedback Loops: Establish feedback loops with the manufacturing team to identify and address any issues related to DNI/DNP entries.
- Process Audits: Conduct regular audits of your DNI/DNP management processes to identify areas for improvement.
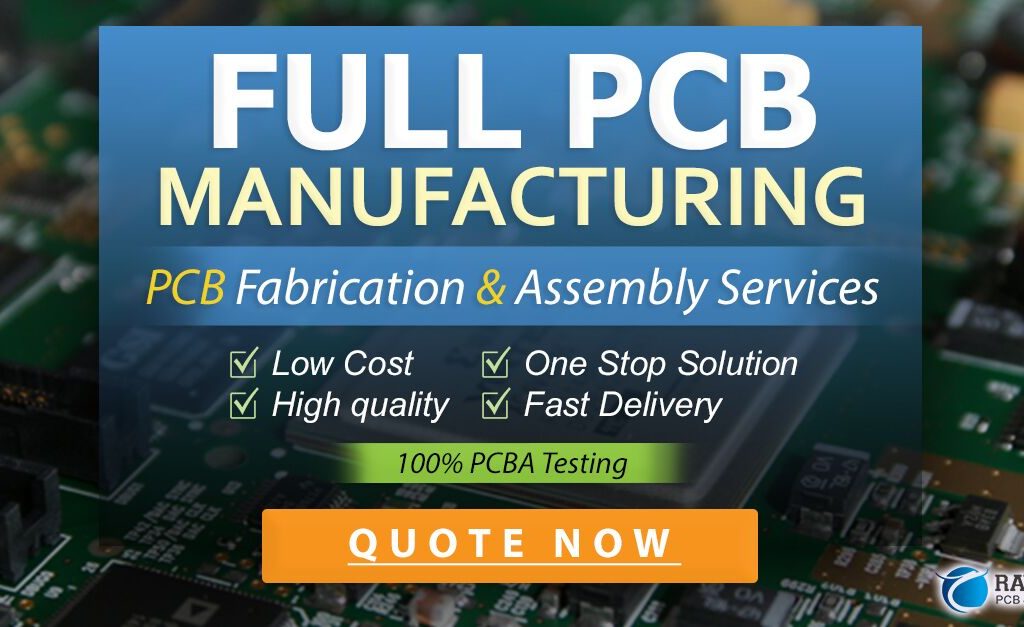
Common Challenges and Solutions
1. Miscommunication with Manufacturers
Miscommunication can lead to DNI/DNP components being incorrectly installed or omitted.
- Solution: Use clear and consistent documentation, and maintain open lines of communication with your manufacturing partners.
2. Inconsistent Naming Conventions
Inconsistent naming conventions can cause confusion and errors in the BOM.
- Solution: Standardize naming conventions and ensure all team members adhere to them.
3. Overlooking DNI/DNP in Design Reviews
Failing to review DNI/DNP entries during design reviews can result in outdated or incorrect entries.
- Solution: Include DNI/DNP entries as a standard agenda item in design reviews.
4. Impact on Testing and Debugging
DNI/DNP entries can complicate testing and debugging if not properly planned.
- Solution: Plan for potential testing and debugging needs by ensuring easy access to DNI/DNP components if required.
Case Studies
Case Study 1: Implementing DNI/DNP in a Consumer Electronics Company
A consumer electronics company faced challenges with inconsistent DNI/DNP entries, leading to manufacturing errors. By standardizing their naming conventions, clearly annotating schematics, and improving communication with their manufacturing team, they were able to reduce errors and improve efficiency.
Case Study 2: Using BOM Management Tools for DNI/DNP Entries
A small hardware startup struggled with managing DNI/DNP entries manually. By adopting BOM management software that supported DNI/DNP entries, they streamlined their process, reduced errors, and improved collaboration between design and manufacturing teams.
Case Study 3: Training and Documentation for DNI/DNP Entries
An automotive company implemented a comprehensive training program and detailed documentation for DNI/DNP entries. This ensured that all team members were familiar with best practices, leading to more accurate BOMs and fewer manufacturing issues.
Conclusion
Effectively managing DNI/DNP entries in your PCB BOM is crucial for ensuring accurate manufacturing, reducing costs, and avoiding errors. By following best practices such as clearly defining DNI/DNP, using consistent naming conventions, annotating schematics clearly, and leveraging BOM management tools, you can streamline your design and manufacturing processes. Additionally, regular reviews, clear communication, and continuous improvement of processes will help maintain the accuracy and relevance of DNI/DNP entries throughout the project lifecycle. Ultimately, these best practices contribute to the successful delivery of high-quality PCB designs and products.