Introduction
Printed Circuit Board (PCB) design is a critical aspect of electronics engineering, influencing the performance, reliability, and manufacturability of electronic devices. Despite its importance, PCB design is often misunderstood, leading to common misconceptions that can result in suboptimal designs, increased costs, and production delays. This article aims to debunk seven prevalent misconceptions about PCB design, providing clarity and insights to help engineers and designers create better PCBs.
Misconception 1: PCB Design is Just About Connecting Components
The Reality
One of the most common misconceptions is that PCB design is merely about connecting components with traces. While routing connections is a fundamental part of the process, PCB design encompasses much more. It involves a comprehensive understanding of electrical engineering principles, signal integrity, thermal management, electromagnetic compatibility (EMC), and manufacturability.
Key Considerations
- Signal Integrity: Ensuring that signals propagate correctly without degradation or interference.
- Power Integrity: Managing power distribution to minimize noise and voltage drops.
- Thermal Management: Dissipating heat effectively to prevent overheating and ensure reliability.
- EMC/EMI: Minimizing electromagnetic interference to comply with regulatory standards.
- Manufacturability: Designing for ease of assembly, testing, and repair.
Impact
Neglecting these aspects can lead to poor performance, reliability issues, and increased production costs. A holistic approach to PCB design is essential for creating robust and efficient electronic devices.
Misconception 2: Any PCB Design Software Will Do
The Reality
Another misconception is that all PCB design software tools are essentially the same, and any tool can be used interchangeably. In reality, the choice of PCB design software can significantly impact the quality and efficiency of the design process.
Key Considerations
- Feature Set: Different tools offer varying levels of functionality, from basic routing to advanced simulation and analysis.
- Ease of Use: User-friendly interfaces and workflows can enhance productivity and reduce the learning curve.
- Integration: Compatibility with other design tools and libraries can streamline the design process.
- Support and Community: Access to technical support and a active user community can be invaluable for troubleshooting and learning.
Impact
Using inappropriate or subpar software can lead to design errors, increased development time, and higher costs. Selecting the right tool for the specific requirements of the project is crucial for achieving optimal results.
Misconception 3: High-Speed Design is Only for High-Frequency Applications
The Reality
High-speed design principles are often associated with high-frequency applications, such as RF and microwave circuits. However, these principles are also relevant for digital circuits operating at lower frequencies, especially as signal rise times decrease.
Key Considerations
- Signal Integrity: Managing reflections, crosstalk, and impedance matching to ensure signal quality.
- Power Distribution: Ensuring stable power delivery to prevent noise and voltage fluctuations.
- Routing Techniques: Using controlled impedance routing, differential pairs, and proper grounding techniques.
Impact
Ignoring high-speed design principles in digital circuits can lead to signal integrity issues, such as data corruption and timing errors, even at relatively low frequencies. Understanding and applying these principles is essential for reliable digital circuit design.
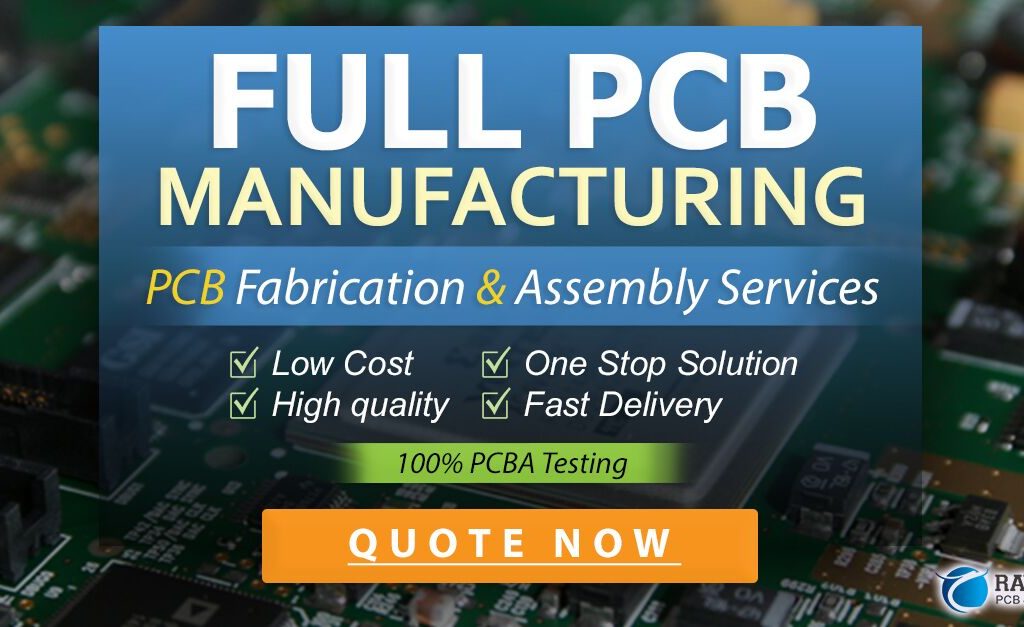
Misconception 4: More Layers Always Mean Better Performance
The Reality
While adding more layers to a PCB can provide additional routing space and improve signal integrity, it is not always necessary or beneficial. The number of layers should be determined by the specific requirements of the design.
Key Considerations
- Complexity: More layers increase the complexity and cost of the PCB.
- Signal Integrity: Proper layer stack-up and routing techniques can achieve good signal integrity with fewer layers.
- Thermal Management: Additional layers can help with heat dissipation but may not always be required.
- Cost: More layers increase manufacturing costs, which may not be justified for simpler designs.
Impact
Using more layers than necessary can lead to increased costs and complexity without corresponding performance benefits. A balanced approach, considering the specific needs of the design, is essential for optimizing performance and cost.
Misconception 5: Ground Planes Are Optional
The Reality
Some designers believe that ground planes are optional or can be omitted to simplify the design. In reality, ground planes play a crucial role in ensuring signal integrity, reducing noise, and providing a stable reference for signals.
Key Considerations
- Signal Integrity: Ground planes provide a low-impedance return path for signals, reducing noise and reflections.
- EMC/EMI: Proper grounding helps minimize electromagnetic interference and ensures compliance with regulatory standards.
- Thermal Management: Ground planes can aid in heat dissipation, improving thermal performance
Impact
Omitting ground planes can lead to increased noise, signal integrity issues, and EMC problems, compromising the performance and reliability of the PCB. Including ground planes is essential for robust and reliable designs.
Misconception 6: Design for Manufacturability (DFM) is Only for Mass Production
The Reality
Design for Manufacturability (DFM) principles are often associated with mass production, but they are equally important for low-volume and prototype designs. DFM ensures that the PCB can be manufactured efficiently and reliably, regardless of production volume.
Key Considerations
- Component Placement: Ensuring components are placed to facilitate assembly and minimize soldering issues.
- Trace Width and Spacing: Adhering to manufacturing capabilities to avoid defects and ensure reliability.
- Panelization: Designing for efficient panelization to maximize yield and reduce waste.
- Testing: Incorporating test points and features to facilitate testing and debugging.
Impact
Neglecting DFM principles can lead to manufacturing difficulties, increased costs, and delays, even for low-volume or prototype designs. Applying DFM principles from the outset ensures a smoother transition from design to production.
Misconception 7: Simulation and Testing Are Optional
The Reality
Some designers believe that simulation and testing are optional steps that can be skipped to save time and resources. In reality, simulation and testing are critical for validating the design and ensuring it meets performance and reliability requirements.
Key Considerations
- Signal Integrity Simulation: Identifying and addressing signal integrity issues before fabrication.
- Thermal Simulation: Ensuring adequate thermal management to prevent overheating.
- EMC/EMI Testing: Verifying compliance with regulatory standards and minimizing interference.
- Functional Testing: Validating the functionality and performance of the PCB.
Impact
Skipping simulation and testing can lead to undetected design flaws, resulting in performance issues, reliability problems, and costly rework. Incorporating simulation and testing into the design process is essential for achieving a successful and reliable PCB design.
Conclusion
PCB design is a complex and multifaceted process that requires a deep understanding of electrical engineering principles, signal integrity, thermal management, and manufacturability. Debunking common misconceptions about PCB design is essential for creating robust, reliable, and cost-effective electronic devices. By understanding the realities of PCB design and applying best practices, engineers and designers can avoid common pitfalls and achieve optimal results in their projects.