Introduction
Soldering has long been a cornerstone of electronics assembly, providing a reliable method for creating permanent electrical connections. However, soldering is not always the most practical or desirable option, especially in scenarios where temporary connections, rapid prototyping, or non-permanent assemblies are required. In such cases, solderless assembly techniques come to the forefront. This article explores the various methods of assembling electronic components without solder, their advantages, applications, and the tools and materials involved.
Understanding Solderless Assembly
Solderless assembly refers to the process of connecting electronic components without the use of solder. This can be achieved through various mechanical and conductive methods that ensure reliable electrical connections. Solderless techniques are particularly useful in educational settings, prototyping, and situations where components need to be frequently reconfigured or replaced.
Advantages of Solderless Assembly
- Ease of Use: Solderless techniques are generally easier to perform, especially for beginners or those without soldering experience.
- Reusability: Components can be easily disconnected and reused, making solderless methods ideal for prototyping and experimentation.
- Safety: Eliminating the need for a soldering iron reduces the risk of burns, fumes, and other hazards associated with soldering.
- Speed: Solderless assembly can be faster, as it avoids the time-consuming process of heating and cooling solder.
- Cost-Effectiveness: Solderless methods can be more economical, as they eliminate the need for soldering equipment and consumables.
Disadvantages of Solderless Assembly
- Durability: Solderless connections may not be as durable or reliable as soldered connections, especially in high-vibration or high-temperature environments.
- Conductivity: Solderless connections can have higher resistance, which may affect the performance of high-frequency or high-current circuits.
- Size and Weight: Solderless connectors and components can be bulkier and heavier than their soldered counterparts.
Solderless Assembly Techniques
Several solderless assembly techniques are available, each with its own set of tools, materials, and applications. Below, we explore some of the most common methods.
Breadboarding
Breadboarding is one of the most popular solderless assembly techniques, widely used in prototyping and education. A breadboard is a plastic board with a grid of holes into which components and wires can be inserted to create temporary electrical connections.
How Breadboarding Works
- Structure: A typical breadboard consists of multiple rows and columns of interconnected metal clips beneath the holes. These clips hold the components and wires in place and create electrical connections.
- Power Rails: Breadboards usually have power rails running along the sides, providing easy access to power and ground connections.
- Component Placement: Components are placed into the holes, and wires are used to connect them according to the circuit diagram.
Advantages of Breadboarding
- Ease of Use: Breadboards are straightforward to use, making them ideal for beginners.
- Reusability: Components can be easily removed and reused.
- Flexibility: Circuits can be quickly modified and tested.
Disadvantages of Breadboarding
- Limited Current Handling: Breadboards are not suitable for high-current applications.
- Signal Integrity: High-frequency signals may suffer from crosstalk and noise due to the breadboard’s layout.
Wire Wrapping
Wire wrapping is a solderless technique that involves wrapping a thin wire around a terminal to create a secure electrical connection. This method is often used in prototyping and low-volume production.
How Wire Wrapping Works
- Tools: A wire wrap tool is used to wrap the wire around the terminal. The tool has a bit that grips the wire and rotates it around the terminal.
- Wire: Special wire wrap wire, typically 30 AWG, is used. The wire has a thin insulation layer that is stripped at the ends.
- Terminals: Wire wrap terminals are usually square posts that provide a secure grip for the wire.
Advantages of Wire Wrapping
- Reliability: Wire-wrapped connections are highly reliable and can withstand vibration and thermal cycling.
- Density: Wire wrapping allows for high-density connections, making it suitable for complex circuits.
- Reusability: Connections can be unwrapped and re-wrapped, allowing for modifications.
Disadvantages of Wire Wrapping
- Skill Required: Wire wrapping requires some skill and practice to achieve reliable connections.
- Time-Consuming: The process can be slower compared to other solderless methods.
Crimping
Crimping is a solderless technique that involves using a crimp tool to compress a metal connector around a wire, creating a secure electrical connection. Crimping is commonly used in wiring harnesses and connectors.
How Crimping Works
- Crimp Connectors: These are metal connectors designed to be crimped onto the ends of wires. Common types include butt connectors, ring terminals, and spade terminals.
- Crimp Tool: A crimp tool is used to compress the connector around the wire, ensuring a secure and conductive connection.
- Wire Preparation: The wire is stripped of insulation at the end, and the connector is placed over the exposed wire before crimping
Advantages of Crimping
- Durability: Crimped connections are highly durable and can withstand mechanical stress and environmental conditions.
- Consistency: Properly crimped connections provide consistent electrical performance.
- Ease of Use: Crimping is relatively easy to perform with the right tools.
Disadvantages of Crimping
- Tool Cost: High-quality crimp tools can be expensive.
- Permanent: Crimped connections are generally considered permanent and are not easily reusable.
Screw Terminals
Screw terminals are a solderless method of connecting wires by tightening screws onto the wires, securing them in place. This method is commonly used in electrical panels, terminal blocks, and some consumer electronics.
How Screw Terminals Work
- Terminal Blocks: These are blocks with multiple screw terminals, each providing a connection point for a wire.
- Screws: Screws are tightened onto the wires, pressing them against a metal plate to create an electrical connection.
- Wire Preparation: Wires are typically stripped of insulation at the ends before being inserted into the terminal.
Advantages of Screw Terminals
- Ease of Use: Screw terminals are easy to use and do not require special tools.
- Reusability: Connections can be easily undone and redone, making screw terminals suitable for applications requiring frequent changes.
- Versatility: Screw terminals can accommodate a wide range of wire sizes and types.
Disadvantages of Screw Terminals
- Mechanical Stress: Over-tightening screws can damage wires, while under-tightening can lead to loose connections.
- Size: Screw terminals can be bulkier compared to other connection methods.
Spring Clamps
Spring clamps, also known as push-in or quick-connect terminals, use a spring mechanism to hold wires in place, creating a solderless connection. This method is commonly found in consumer electronics and lighting fixtures.
How Spring Clamps Work
- Terminal Design: Spring clamp terminals have a spring-loaded mechanism that clamps down on the wire when it is inserted.
- Wire Insertion: Wires are stripped of insulation and inserted into the terminal, where the spring clamp holds them securely.
- Release Mechanism: Some spring clamp terminals have a release button or lever to remove the wire.
Advantages of Spring Clamps
- Ease of Use: Spring clamps are very easy to use, requiring no tools for insertion.
- Speed: Connections can be made quickly, making spring clamps ideal for high-volume assembly.
- Reusability: Wires can be easily removed and reinserted, allowing for modifications.
Disadvantages of Spring Clamps
- Current Handling: Spring clamps may not be suitable for high-current applications.
- Durability: The spring mechanism may wear out over time, leading to less secure connections.
Conductive Adhesives
Conductive adhesives are a solderless method that uses electrically conductive glue to create connections between components. This technique is often used in flexible circuits and applications where soldering is impractical.
How Conductive Adhesives Work
- Adhesive Application: Conductive adhesive is applied to the connection points using a syringe or dispenser.
- Curing: The adhesive is allowed to cure, forming a conductive bond between the components.
- Conductive Fillers: Conductive adhesives contain metal particles (e.g., silver) that provide electrical conductivity.
Advantages of Conductive Adhesives
- Flexibility: Conductive adhesives can be used on flexible substrates and in applications where soldering is not feasible.
- Low Temperature: The curing process occurs at lower temperatures compared to soldering, reducing thermal stress on components.
- Fine Pitch: Conductive adhesives can be used for fine-pitch connections, making them suitable for miniaturized electronics.
Disadvantages of Conductive Adhesives
- Conductivity: Conductive adhesives generally have higher resistance compared to soldered connections.
- Curing Time: The curing process can take longer than soldering, potentially slowing down assembly.
- Cost: Conductive adhesives can be more expensive than traditional soldering materials.
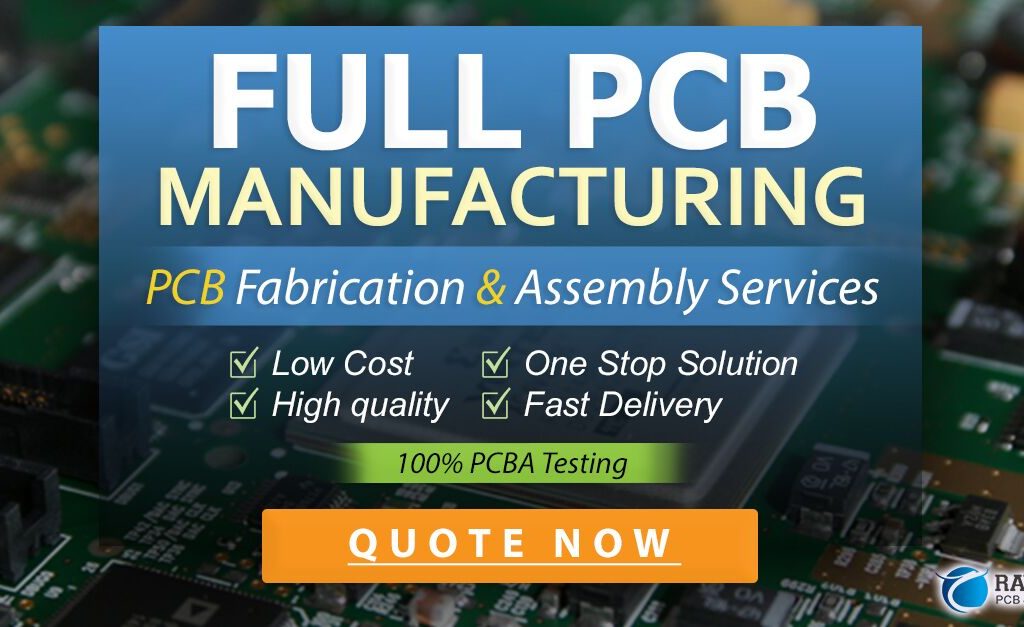
Applications of Solderless Assembly
Solderless assembly techniques are used in a wide range of applications, from education and prototyping to industrial and consumer electronics. Below are some common applications:
Education and Training
Solderless assembly is widely used in educational settings to teach students about electronics and circuit design. Breadboarding and wire wrapping are particularly popular in classrooms and workshops due to their ease of use and reusability.
Prototyping and Development
Engineers and hobbyists use solderless techniques to quickly prototype and test new circuit designs. Breadboarding and spring clamps allow for rapid iteration and modification, making them ideal for development stages.
Consumer Electronics
Solderless assembly methods like spring clamps and screw terminals are commonly used in consumer electronics for their ease of assembly and maintenance. These methods are often found in devices like lighting fixtures, audio equipment, and home appliances.
Industrial Electronics
In industrial settings, solderless techniques like crimping and wire wrapping are used for their reliability and durability. These methods are often employed in control panels, wiring harnesses, and machinery.
Flexible and Wearable Electronics
Conductive adhesives are used in flexible and wearable electronics, where traditional soldering is not feasible. These adhesives allow for the creation of circuits on flexible substrates, enabling innovative designs in wearable technology and medical devices.
Tools and Materials for Solderless Assembly
To perform solderless assembly, various tools and materials are required, depending on the chosen technique. Below is a list of common tools and materials used in solderless assembly:
Breadboarding
- Breadboard: A plastic board with a grid of holes for inserting components and wires.
- Jumper Wires: Pre-cut wires with connectors on both ends for making connections on the breadboard.
- Power Supply: A power source to provide voltage and current to the circuit.
- Components: Resistors, capacitors, ICs, and other electronic components.
Wire Wrapping
- Wire Wrap Tool: A tool with a rotating bit for wrapping wire around terminals.
- Wire Wrap Wire: Thin, insulated wire (typically 30 AWG) for making connections.
- Wire Wrap Posts: Square terminals for wire wrapping.
- Stripping Tool: A tool for stripping insulation from wire ends.
Crimping
- Crimp Tool: A tool for compressing crimp connectors onto wires.
- Crimp Connectors: Metal connectors (e.g., butt connectors, ring terminals) for crimping.
- Wire Strippers: A tool for stripping insulation from wire ends.
Screw Terminals
- Terminal Blocks: Blocks with multiple screw terminals for connecting wires.
- Screwdriver: A tool for tightening screws onto wires.
- Wire Strippers: A tool for stripping insulation from wire ends.
Spring Clamps
- Spring Clamp Terminals: Terminals with a spring-loaded mechanism for holding wires.
- Wire Strippers: A tool for stripping insulation from wire ends.
Conductive Adhesives
- Spring Clamp Terminals: Terminals with a spring-loaded mechanism for holding wires.
- Wire Strippers: A tool for stripping insulation from wire ends.
Conductive Adhesives
- Conductive Adhesive: Electrically conductive glue for creating connections.
- Dispenser: A syringe or dispenser for applying the adhesive.
- Curing Equipment: Equipment for curing the adhesive, such as an oven or UV light.
Conclusion
Solderless assembly techniques offer a versatile and practical alternative to traditional soldering, particularly in scenarios where temporary connections, rapid prototyping, or non-permanent assemblies are required. Methods like breadboarding, wire wrapping, crimping, screw terminals, spring clamps, and conductive adhesives each have their own advantages and disadvantages, making them suitable for different applications.
As technology continues to evolve, solderless assembly techniques will likely play an increasingly important role in electronics design and manufacturing. By understanding the various methods and their applications, engineers, hobbyists, and educators can choose the most appropriate technique for their needs, ensuring reliable and efficient assembly without the need for solder.
In conclusion, solderless assembly is a valuable skill set in the electronics industry, offering flexibility, ease of use, and reusability. Whether you’re a beginner learning the basics of circuit design or an experienced engineer developing the next generation of electronic devices, solderless assembly techniques provide a powerful toolkit for creating innovative and reliable electronic systems.