Electromagnetic Compatibility (EMC) is a critical consideration in the design and operation of electronic systems. EMC ensures that electronic devices can function correctly in their intended environment without causing or suffering from electromagnetic interference (EMI). This involves managing both on-the-board (internal) and off-the-board (external) electromagnetic phenomena. In this comprehensive guide, we will explore the fundamental principles of EMC, the challenges associated with achieving it, and best practices for managing EMC both on and off the board.
1. What is Electromagnetic Compatibility (EMC)?
Definition and Overview
Electromagnetic Compatibility (EMC) refers to the ability of an electronic device or system to operate as intended in its electromagnetic environment without introducing intolerable electromagnetic disturbances to other devices in that environment. EMC encompasses two key aspects:
- Emission: The generation of electromagnetic energy by a device, which can interfere with other devices.
- Immunity (or Susceptibility): The ability of a device to function correctly in the presence of electromagnetic disturbances from other devices.
Importance of EMC
- Regulatory Compliance: Most countries have strict EMC regulations that electronic devices must meet before they can be sold.
- Reliability: EMC ensures that devices operate reliably in their intended environment.
- Safety: In critical applications like medical devices and automotive systems, EMC is essential for ensuring safety.
2. EMC on the Board: Managing Internal Electromagnetic Phenomena
1. PCB Layout and Design
The layout and design of the Printed Circuit Board (PCB) play a crucial role in achieving EMC. Poor layout can lead to increased EMI and reduced immunity.
Best Practices for PCB Layout:
- Ground Plane: Use a solid ground plane to provide a low-impedance return path for signals and reduce EMI.
- Signal Routing: Route high-speed signals away from sensitive analog circuits and keep traces short to minimize radiation.
- Decoupling Capacitors: Place decoupling capacitors close to the power pins of ICs to filter high-frequency noise.
- Controlled Impedance: Use controlled impedance traces for high-speed signals to prevent reflections and signal integrity issues.
- Component Placement: Group related components together and separate noisy components (e.g., switching regulators) from sensitive ones.
2. Power Distribution Network (PDN)
A well-designed Power Distribution Network (PDN) is essential for minimizing noise and ensuring stable power delivery.
Best Practices for PDN Design:
- Power Planes: Use dedicated power planes to distribute power with low impedance.
- Decoupling and Bypass Capacitors: Use a combination of decoupling and bypass capacitors to filter noise at different frequencies.
- Minimize Loop Area: Keep power and ground traces close together to minimize loop area and reduce EMI.
3. Shielding and Filtering
Shielding and filtering are effective techniques for reducing EMI on the board.
Best Practices for Shielding and Filtering:
- Shielded Enclosures: Use shielded enclosures to contain EMI within the device.
- Ferrite Beads: Use ferrite beads to filter high-frequency noise on power and signal lines.
- EMI Filters: Implement EMI filters on input/output lines to reduce conducted emissions.
4. Clock and Signal Integrity
High-speed clocks and signals are major sources of EMI. Proper management of these signals is crucial for EMC.
Best Practices for Clock and Signal Integrity:
- Clock Routing: Route clock signals carefully, avoiding long traces and sharp bends.
- Termination: Use proper termination techniques (e.g., series termination) to prevent reflections and ringing.
- Spread Spectrum Clocking: Use spread spectrum clocking to reduce peak EMI emissions.
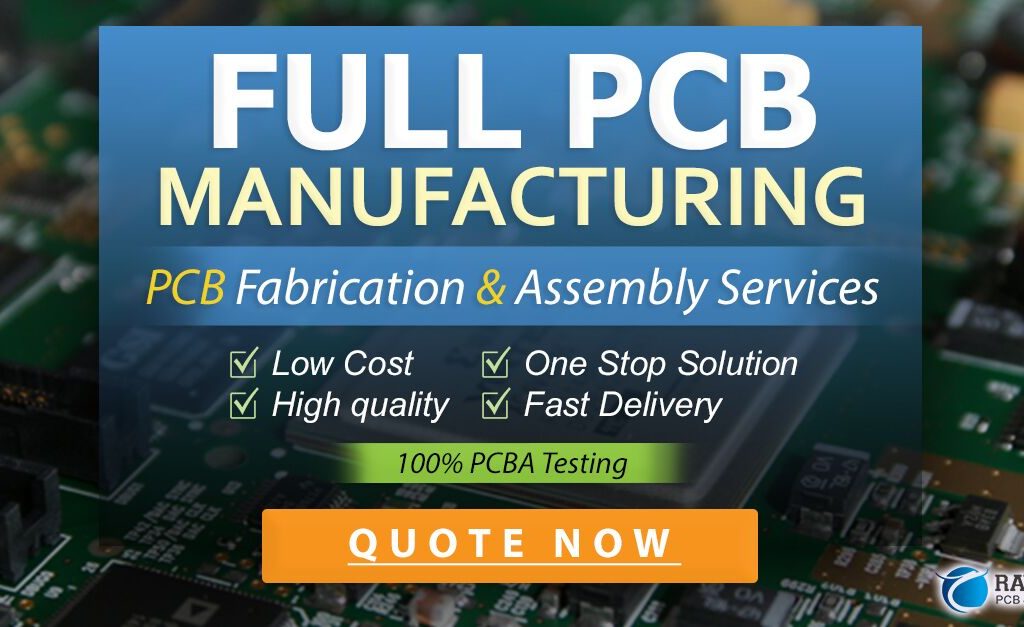
3. EMC off the Board: Managing External Electromagnetic Phenomena
1. Cable Management
Cables can act as antennas, radiating EMI or picking up external interference. Proper cable management is essential for EMC.
Best Practices for Cable Management:
- Shielded Cables: Use shielded cables to reduce radiated emissions and improve immunity.
- Cable Routing: Route cables away from noisy components and sensitive circuits.
- Ferrite Cores: Use ferrite cores on cables to suppress high-frequency noise.
2. Enclosure Design
The design of the device enclosure plays a significant role in managing EMC.
Best Practices for Enclosure Design:
- Conductive Enclosures: Use conductive materials (e.g., metal) for the enclosure to provide shielding.
- Seams and Gaps: Minimize seams and gaps in the enclosure to prevent EMI leakage. Use conductive gaskets if necessary.
- Ventilation: Use EMI shielding vents or honeycomb filters to allow ventilation while maintaining shielding effectiveness.
3. Grounding and Bonding
Proper grounding and bonding are essential for reducing EMI and ensuring EMC.
Best Practices for Grounding and Bonding:
- Single-Point Grounding: Use single-point grounding for low-frequency circuits to avoid ground loops.
- Multi-Point Grounding: Use multi-point grounding for high-frequency circuits to reduce ground impedance.
- Bonding: Ensure all metal parts of the enclosure are bonded together to create a continuous shield.
4. Environmental Considerations
The external electromagnetic environment can significantly impact EMC.
Best Practices for Environmental Considerations:
- Site Surveys: Conduct site surveys to identify potential sources of EMI in the operating environment.
- Immunity Testing: Perform immunity testing to ensure the device can withstand external electromagnetic disturbances.
- Shielding: Use additional shielding measures if the operating environment has high levels of EMI.
4. EMC Testing and Compliance
1. Emission Testing
Emission testing measures the electromagnetic energy radiated or conducted by a device.
Common Emission Tests:
- Radiated Emissions: Measures the electromagnetic energy radiated into the air.
- Conducted Emissions: Measures the electromagnetic energy conducted through power and signal lines.
2. Immunity Testing
Immunity testing evaluates the device’s ability to function correctly in the presence of electromagnetic disturbances.
Common Immunity Tests:
- Radiated Immunity: Tests the device’s resistance to radiated electromagnetic fields.
- Conducted Immunity: Tests the device’s resistance to conducted electromagnetic disturbances.
- Electrostatic Discharge (ESD): Tests the device’s resistance to static electricity discharges.
3. Compliance Standards
Various international standards define the requirements for EMC compliance.
Common EMC Standards:
- CISPR: International standards for emission limits.
- IEC: International standards for immunity testing.
- FCC: Federal Communications Commission regulations for the United States.
- EN: European Norms for EMC compliance in the European Union.
5. Best Practices for Achieving EMC
1. Design for EMC from the Start
Incorporate EMC considerations into the design process from the beginning to avoid costly redesigns later.
2. Use Simulation Tools
Use EMC simulation tools to predict and mitigate potential EMI issues during the design phase.
3. Conduct Pre-Compliance Testing
Perform pre-compliance testing to identify and address EMC issues before formal compliance testing.
4. Follow Good PCB Design Practices
Adhere to best practices for PCB layout, power distribution, and signal integrity to minimize EMI.
5. Implement Shielding and Filtering
Use shielding and filtering techniques to reduce EMI emissions and improve immunity.
6. Test in Real-World Conditions
Conduct EMC testing in conditions that simulate the real-world operating environment.
6. Conclusion
Achieving Electromagnetic Compatibility (EMC) is a complex but essential aspect of electronic design. By understanding and addressing both on-the-board and off-the-board electromagnetic phenomena, designers can create devices that operate reliably in their intended environment without causing or suffering from electromagnetic interference. Through careful PCB design, effective shielding and filtering, proper grounding and bonding, and rigorous testing, it is possible to meet EMC requirements and ensure the success of electronic products in today’s increasingly interconnected world. By following the best practices outlined in this guide, engineers can navigate the challenges of EMC and deliver high-performance, compliant, and reliable electronic systems.