Introduction
The semiconductor industry is undergoing a transformative phase, driven by the increasing demand for high-performance computing (HPC), artificial intelligence (AI), and advanced automotive systems. At the heart of this transformation lies advanced packaging technologies, particularly those involving interposers. Interposers, which act as bridges between semiconductor dies and substrates, have become critical in enabling higher performance, improved thermal management, and enhanced integration of complex systems. This article explores the cutting-edge advancements in packaging with interposers, their applications, challenges, and future trends.
The Role of Interposers in Advanced Packaging
Interposers are essential components in advanced semiconductor packaging, facilitating high-speed signal transmission and power delivery between multiple chips. They are particularly crucial in 2.5D and 3D packaging, where they enable the integration of heterogeneous components, such as CPUs, GPUs, and high-bandwidth memory (HBM).
Types of Interposers
- Silicon Interposers: Silicon interposers are widely used in high-performance applications due to their ability to support fine routing features and through-silicon vias (TSVs). They are ideal for AI and data center applications but come with high material and manufacturing costs.
- Organic Interposers: These interposers use fan-out molding compounds and offer a cost-effective alternative to silicon. However, they struggle to achieve the same level of interconnect density, limiting their use in high-performance computing.
- Glass Interposers: Glass interposers are emerging as a promising solution, offering tunable thermal expansion properties, high dimensional stability, and compatibility with panel-level packaging. They are particularly suited for automotive and AI applications.
Technological Advancements in Interposer-Based Packaging
2.5D Packaging
2.5D packaging involves placing multiple chips side by side on an interposer, which is then connected to a substrate. This approach is widely used in AI and HPC systems, where it enables the integration of processors and HBM. TSMC’s CoWoS (Chip-on-Wafer-on-Substrate) technology, for example, has been a game-changer in this space, with its latest CoWoS-L variant incorporating local silicon interconnects (LSI) to improve yield and flexibility.
3D Packaging
3D packaging takes integration a step further by stacking chips vertically. This approach is enabled by technologies like Cu-Cu hybrid bonding, which allows for ultra-fine pitch interconnects and higher bandwidth. Companies like AMD and NVIDIA are leveraging 3D packaging to stack CPU/GPU tiles and memory, achieving significant performance gains.
Hybrid Bonding and Silicon Photonics
Hybrid bonding, which combines dielectric materials with embedded metal (Cu), is revolutionizing 3D packaging by enabling pitches below 10 micrometers. This technology is critical for future HBM advancements, particularly for DRAM stacks beyond 16-Hi layers. Additionally, silicon photonics is being integrated into 3D packaging to enhance optical communication, reducing power consumption and improving bandwidth.
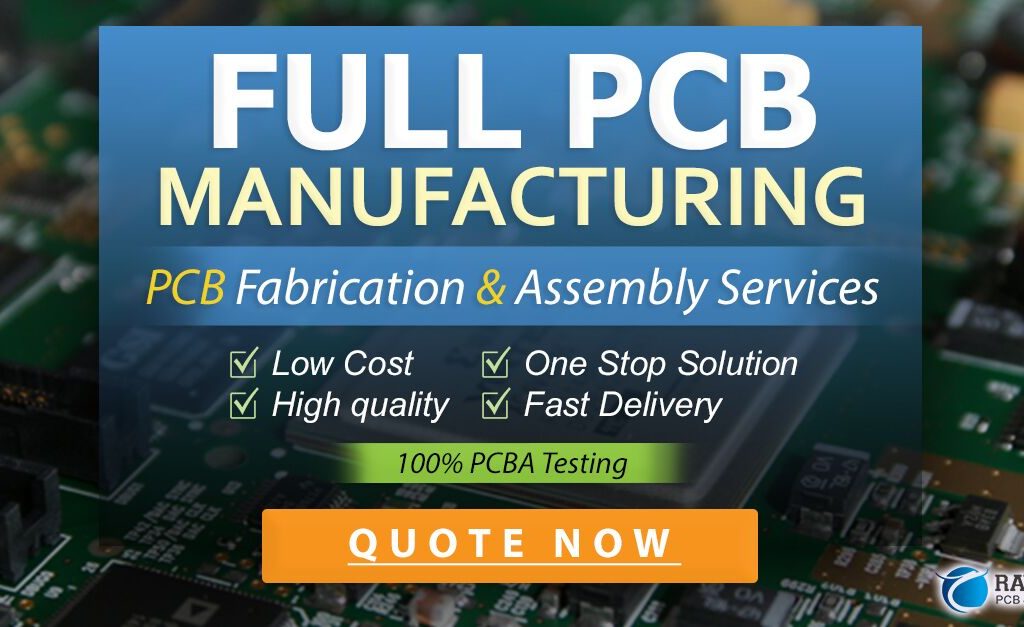
Applications of Interposer-Based Packaging
AI and Data Centers
The demand for interposer-based packaging is particularly high in AI and data center applications. NVIDIA’s Blackwell AI chips, for instance, are transitioning from CoWoS-S to CoWoS-L packaging to address yield challenges and improve performance. Similarly, SK hynix is innovating with direct stacking and advanced substrates to reduce costs and enhance HBM integration.
Automotive Systems
In the automotive sector, interposer-based packaging is enabling the development of advanced driver-assistance systems (ADAS) and autonomous driving technologies. Chiplet-based solutions are becoming pivotal, allowing for faster development cycles and improved reliability.
Consumer Electronics
Consumer electronics, including smartphones and AR/VR devices, are also benefiting from advanced packaging. While these applications are more cost-sensitive, the need for compact, high-performance solutions is driving the adoption of interposer technologies.
Challenges in Interposer-Based Packaging
Manufacturing Complexity
The production of interposers, particularly silicon and glass variants, involves complex processes such as TSV fabrication and hybrid bonding. These processes require high precision and are prone to yield issues, increasing costs.
Thermal Management
As chips become more densely packed, managing heat dissipation becomes a significant challenge. Glass interposers, with their tunable thermal expansion properties, offer a potential solution, but further research is needed to optimize their thermal performance.
Ecosystem Maturity
While glass interposers show great promise, their ecosystem is still immature. Large-scale production capabilities are limited, and technical challenges such as warpage management need to be addressed.
Future Trends in Interposer-Based Packaging
Panel-Level Packaging (PLP)
Panel-level packaging is gaining traction as a cost-effective alternative to wafer-level packaging. By enabling larger interposers and higher throughput, PLP is expected to play a key role in the future of advanced packaging.
Co-Packaged Optics (CPO)
Co-packaged optics is emerging as a critical technology for enhancing I/O bandwidth and reducing energy consumption. By integrating optical communication directly into the package, CPO addresses the growing demand for high-speed data transmission in AI and data center applications.
Collaboration and Innovation
The semiconductor industry is increasingly adopting a collaborative approach to address the challenges of advanced packaging. Initiatives like the US-JOINT consortium, which brings together companies like 3M and Resonac, are accelerating research and development in next-generation packaging technologies.
Conclusion
Interposer-based packaging is at the forefront of semiconductor innovation, enabling the integration of complex systems and driving advancements in AI, automotive, and consumer electronics. While challenges such as manufacturing complexity and thermal management remain, ongoing research and collaboration are paving the way for groundbreaking solutions. As the industry continues to evolve, interposer technologies will play a pivotal role in shaping the future of computing and connectivity.
By leveraging cutting-edge technologies like hybrid bonding, silicon photonics, and panel-level packaging, the semiconductor industry is poised to overcome the limitations of Moore’s Law and deliver unprecedented levels of performance and efficiency. The journey ahead is challenging, but the potential rewards are immense, making interposer-based packaging a cornerstone of the next generation of semiconductor innovation.