Introduction
Printed Circuit Boards (PCBs) that are neither completely flexible nor completely rigid are known as semi flexible PCBs. These circuit boards provide a unique combination of mechanical flexibility and structural rigidity that makes them suitable for a wide range of applications where regular rigid PCBs may not be feasible.
Semi flexible PCBs provide the ability to bend and conform to shapes and spaces where a standard PCB cannot fit. At the same time, they provide enough stiffness and structure to support electronic components that flexible PCBs may struggle with. This combination of flexibility and rigidity makes semi flex PCBs highly versatile for products that require dynamic bending, folding or wrapping.
Some key highlights of semi flexible PCBs:
- Provide moderate flexibility and retain some rigidity
- Can be bent, folded or twisted to a certain extent
- Suitable for dynamic bending applications
- Support discrete electronic components
- Provide more reliability than flexible PCBs
- Used in a range of products from wearables to medical devices
In this article, we will dive deeper into semi flexible PCB materials, optimal design guidelines, and various applications that use this technology.
Materials Used in Semi Flexible PCBs
The unique mechanical properties of semi flex PCBs come from the materials used in their construction. While rigid PCBs are made of rigid laminate materials like FR-4, semi flex PCB fabrication involves more flexible dielectric materials.
Some of the common materials used are:
- Polyimide (PI)
- Polyethylene terephthalate (PET)
- Polyethylene naphthalate (PEN)
- Polyether ether ketone (PEEK)
- Liquid Crystal Polymer (LCP)
Polyimide (PI) is the most popular and widely used material for semi flex PCBs. It provides an excellent balance of flexibility, heat resistance, and mechanical strength. Polyimide laminates like DuPontTM Kapton® are commonly used.
PET and PEN offer high flexibility and are relatively low cost options. However, they have lower working temperatures.
LCP provides the highest temperature resistance but is also the most expensive material.
The choice depends on the degree of flex required vs temperature range the PCB will be exposed to during operation and storage.
Design Guidelines for Optimal Semi Flex PCBs
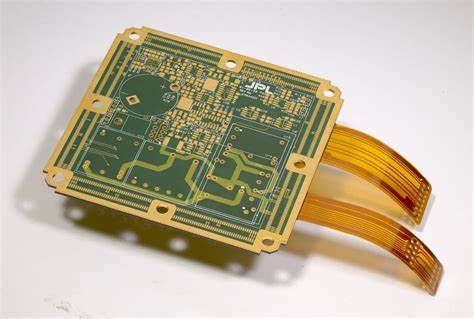
To create a reliable and durable semi flex PCB, the design has to be optimized keeping the mechanical flexibility in mind. Here are some key guidelines:
- Minimize board thickness – Keeping the PCB as thin as possible (around 0.2-0.8mm) allows greater flexibility without cracking.
- Avoid sharp corners – Rounded corners and tear-drop shapes help reduce stress concentrations.
- Use reinforced solder masks – Special flexible solder masks like LPI are needed to handle repeated bending.
- Strategic stiffening sections – Dense component areas can have additional layers to provide localized rigidity.
- Adhesives to manage layers – Adhesives fix multi-layer PCBs to prevent delamination during flexing.
- Flexible component packaging – Components must also withstand mechanical stresses. Avoid large BGAs.
- Flex-cuts in the right places – Small flex cuts strategically placed allow controlled bending motion.
- Test bend cycle life – Prototype testing ensures the PCB can last through the required bending cycles.
Adhering to these guidelines allows for reliable circuit boards that can survive mechanical stresses encountered in semi flex applications.
Applications and Examples of Semi Flexible PCBs##
The combination of moderate flexibility and structural rigidity offered by semi flex PCBs enable their use in a diverse range of applications not feasible with standard PCBs.
Wearable Electronics
Wearable devices like smart watches, fitness bands, smart glasses etc. require the PCBs to be bent and formed around the human body. Polyimide-based semi flex PCBs are commonly used to enable this flexible wearability without compromising on component support and reliability.
Medical Devices
Medical devices like hearing aids, digital pills and implantable devices require small, bendable PCBs that can fit ergonomically inside the human body. LCP and PEN based semi flex circuits provide biocompatibility and flexibility.
Robotics and Drones
For robotics and drones, PCBs must survive vibration, shock and repeated motion. Semi flex PCBs allow connections between moving parts and can withstand rigorous mechanical stresses better.
Dynamic Display and Lighting
Semi flex PCBs are used in dynamic display solutions and lighting that require bending around structures. Applications like LED strips, stage lighting, flexible displays etc benefit from this technology.
In addition, some other areas that utilize semi flex PCBs are – automotive dashboards, consumer appliances, gaming devices, aerospace and military equipment.
Frequently Asked Questions
What are some key differences between rigid, flex and semi flex PCBs?
- Rigid PCBs – Made of laminates like FR4. Provide structure but no flexibility. Best for static, rigid designs.
- Flex PCBs – Use polyimide films. Can freely bend and twist. Not suitable for heavy components.
- Semi-Flex PCBs – Balance of flexibility and rigidity. Can bend to a certain extent. Can support components. Wider range of applications.
What are some signs that a semi flex PCB needs redesign?
Some signs that a redesign may be needed:
- Board cracking or delamination on bending
- Component pads lifting or traces cracking
- Excessive localized heating
- Failure due to static fatigue after bend cycles
- Mechanical issues like warping or twisting
How many bend cycles can a well designed semi flex PCB last?
With optimal design, strategic stiffening, and robust materials, a semi flex PCB can reliably last over 10,000 bending cycles. Some applications demand over 25,000 cycles. Extensive prototyping and testing is done to ensure sufficient mechanical endurance.
Does semi flex technology significantly increase the PCB fabrication cost?
Semi flex PCBs do require more complex materials and processes compared to standard rigid PCBs. However, with modern manufacturing, the cost increase is moderate, usually 20% to 50%. The benefits of flexibility and reliability outweigh the extra fabrication costs for most applications.
Can conventional PCB assembly be used for semi flex circuits?
Yes, SMT assembly of components on semi flex PCBs can leverage the same equipment and processes as rigid PCB assembly. However, components must be selected to withstand mechanical stresses. Additional points of caution include special gluing, edge-bonding, and inspection criteria.
Conclusion
Semi flexible PCBs fill an important gap between simple flex circuits and rigid boards. With robust design and assembly, they can provide the right combination of bendability, durability and component support needed in products that require dynamic flexing in use. Their growing popularity is driven by applications in wearables, medical devices, robotics and beyond.