Introduction to Flex PCB Vias
A via is a plated through hole that connects different layers in a printed circuit board (PCB). Vias provide vertical interconnections and enable traces to change layers and connect components mounted on different sides of the board.
In flexible PCBs (FPCBs), vias play an especially important role in allowing signals to cross between layers in the tight spaces afforded by flex circuits. Careful via design is required to ensure reliable interconnections under repeated flexing.
This comprehensive guide covers everything you need to know about flex PCB vias, including:
- What are flex PCB vias and how do they work?
- When are vias needed in flex PCBs?
- How to design and layout vias in flex circuits
- Common problems with flex PCB vias and solutions
- Flex-specific via types and structures
- Flex PCB via reliability factors
- Flex via testing methods
- Advantages of laser-drilled flex vias
Following the design, layout, and fabrication guidelines provided in this guide will help you implement robust vias in your flex circuits for optimal performance and reliability.
What Are Flex PCB Vias and How Do They Work?
A via in a PCB provides an electrical connection between layers that routing traces alone cannot achieve. Vias are basically plated through holes that are drilled or etched through the PCB dielectric layers and plated with copper to form a continuous connection through all layers.<img src=”images/flex-pcb-via.jpg” alt=”flex pcb via” width=”400″>
A typical flex PCB via structure
In multilayer rigid boards, vias transition between the layers through straight vertical pathways. But flex circuits have dynamic layer structures that bend and flex during use.
To maintain connectivity through these dynamic flexing conditions, flex vias follow more meandering paths:
- The vertical ‘walls’ of flex vias follow a tilted angles rather than straight paths to provide stress relief during bending.
- The actual hole drilled through the dielectric is larger than the finished plated via to provide space for layer shifting.
- The via pad connections are also enlarged to compensate for layer misalignments.
These features provide the flexibility and mechanical compliance for vias to remain reliably connected through thousands or millions of flex cycles.
When Are Vias Needed in Flexible PCBs?
Vias serve several important functions in flex PCBs:
Layer Changing
The most basic purpose of a via in any PCB is allowing routing traces to change layers when required. This allows complex routing connections between components in tight spaces.
Component Connections
Vias are needed to connect component pads on different layers of the flex PCB. Components may be mounted on both sides of a double-sided flex circuit, necessitating vertical interconnections.
External Connections
Vias can connect traces to external layers, such as soldered connections to a rigid PCB or mounted component. Vias bring signals to the outer surfaces where external connections are made.
RF Signals
For high frequency RF flex circuits, vias act as short vertical transmission lines to cross signals between ground plane layers. This provides referencing for controlled impedance RF traces.
Shielding
Plated through holes around components or signals can connect ground planes above and below to provide RF shielding.
Stiffening
Selective placement of vias can provide enhanced stiffness in particular flex circuit areas for crack prevention.
Heat Dissipation
Dense via fields in flex PCB sections can improve heat dissipation from components by thermally coupling the layers.
Circuit Partitioning
Vias also support partitioning flex circuits into rigid and dynamic segments, allowing rigid sections for components and connectors while still providing dynamic flexing capability where needed.
In summary, vias should be utilized in flexible PCB designs wherever vertical layer interconnectivity is required, which is in most multilayer flex circuits.
Flex PCB Via Design and Layout Guidelines
Careful design and layout of vias is essential in flex PCBs to avoid reliability issues under dynamic bending. Follow these guidelines when implementing vias in flex circuits:
Via Size
- Size vias proportionally to the specified layer thickness, larger for thicker dielectric layers. As a rule of thumb, minimum finished via diameter should be no less than 4 times the copper thickness for reliable plating coverage.
- Default flex via diameters range from 0.15mm to 0.5mm. Choose the largest size possible for greater reliability.
- The drill diameter for a flex via is generally 0.1-0.15mm larger than the finished plated size to allow for flex layer shifting and prevent cracking.
Via Pads
- Use tear-drop shaped pads or rounded rectangles rather than standard round O-shaped pads. Rounded pad edges reduce stress concentrations.
- Make pads significantly larger than the via barrel, with at least 0.3mm annular ring width. This compensates for layer misalignment during bending.
- Utilize thermal relief cutouts around via pads whenever possible to reduce cracking from thermomechanical stresses.
Spacing and Density
- Provide maximum spacing between vias and traces/pads. Use at least 2x the via diameter spacing as a minimum.
- For dense via fields, use staggered grid patterns with triangular rather than square spacing for optimal mechanical performance.
- Limit via field density to 60-80% max pad coverage for layer sections that will experience significant bending stresses.
Layout Symmetry
- Strive for symmetry in via layouts on opposite sides of the dielectric at layer transitions. This balances stresses during flexing.
- Route associated traces to vias orthogonally (90 degree angles) whenever possible for reduced joint stresses.
Layer Transitions
- Avoid placing vias at exact flexible-to-rigid boundaries which are high stress areas. Shift vias slightly into rigid regions if possible.
- For exiting buried traces to an external layer, terminate the trace and then bridge up to the outer layer. Avoid routing traces diagonally through multiple layers.
By following these guidelines, you can design reliable vias tailored for the mechanical rigors of dynamic flex circuit environments.
Common Problems with Flex PCB Vias
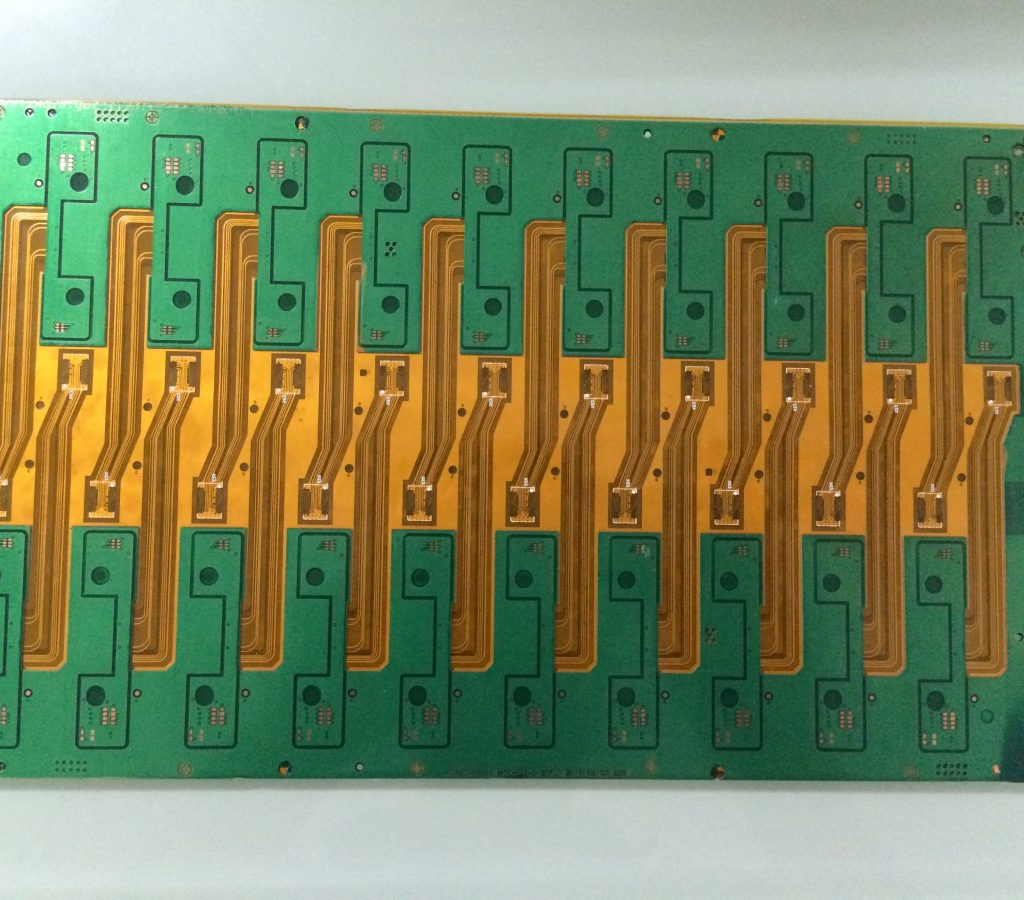
Failures of vias can cause serious reliability issues in flex circuits. Here are some of the most common flex via problems and potential solutions:
Cracked Vias
Repeated stresses can propagate micro-cracks in via barrels and pads, causing evential failure. This can be prevented by:
- Increasing via size and annular ring width
- Reducing via density at flex zones
- Improving laminate copper coverage in plating
- Optimizing adjacent trace routing
Plating Voids
Incomplete plating of via holes during fabrication can create voids inside the via structure leading to intermittent connections. Solutions include:
- Specifying and inspecting plating thickness
- Optimizing drill size for aspect ratio
- Improving drilling precision
- Using sloped via sidewalls for better plating coverage
Overfilled Vias
Excessive plating material can clog and close up via holes, blocking trace connections. This can be avoided by:
- Controlling plating process accuracy
- Validating minimum hole size versus aspect ratio
- Cleaning drilled holes properly before plating
Via Cracking Under Bending
Repeated dynamic stresses can propagate cracks initiating partial or total via fractures. Mitigation approaches:
- Widen annular pad rings to absorb flexing
- Utilize tear-drop pads for reduced stress points
- Limit via densities in high-flex zones
- Optimize routing trace angles
Layer Misregistration
Shifting between flexible layers can cause via pads to partially or fully detach from barrel surfaces. This is prevented by:
- Increasing annular ring clearance around barrels
- Reducing routing trace angles at vias
- Improving drill precision and capture pad registration
By understanding the potential failure modes and associated best practices, flex circuit designers can implement vias for maximized reliability under bending.
Specialized Flexible PCB Via Types and Structures
In addition to conventional plated through hole vias, some specialized via constructions and geometries are used to achieve improved performance and reliability in certain flex PCB applications:
Blind/Buried Vias
These vias connect an internal layer to an adjacent outer layer only, without passing fully through the entire PCB thickness. Reduces unnecessary connections.
Filled Vias
The through hole is filled with an epoxy or polymer plug after plating. Provides enhanced structural stability.
Tented Vias
A soldermask layer covers or ‘tents’ the via pad, leaving only a small opening. Limits solder wicking down vias.
Stub/Stitch Vias
Shallow vias connect adjacent layers without passing fully through dielectric. Reduces layer stresses.
Skip Vias
The connection skips over one layer to another further within the layer stack. Reduces shorting risks.
Microvias
Smaller diameter vias down to 0.15mm provide connections in ultra-dense flex circuits. Require laser drilling.
Offset Vias
The holes are offset between adjacent layers to create diagonal ‘skewed’ paths. Balances bending stresses.
Dogbone Vias
The via has enlarged circular pads joined by a narrower neck. Reduces bending stress concentrations.
By selecting the most appropriate via types for each flex circuit application, electrical connections and mechanical reliability can be optimized.
Key Reliability Factors for Flex PCB Vias
Several design, material, and manufacturing factors are key to ensuring robust, reliable via performance in dynamic flexing environments:
- Annular Ring – Adequate pad clearance around barrel avoids separation during bending
- Pad Shapes – Rounded pad edges reduce stress points that could crack
- Surface Finishes – Immersion tin or gold prevents pads oxidizing and losing solderability
- Plating Thickness – Heavier copper plating withstands thermal stresses and cracking
- Aspect Ratios – Maintaining drill diameter to thickness ratios under 10:1 ensures uniform plating
- Drilling Accuracy – Tight tolerances and perpendicularity prevents cracks developing during holes drilling
- Laminate Materials – Robust dielectric materials like polyimide are needed to survive repeated bending without cracking
- Prepreg Control – Uniform prepreg materials enhance platability and minimize thickness variations
- Etching Accuracy – Precise etching prevents undercutting via pad interfaces and edges
By controlling these factors, flex PCB fabricators can produce robust vias providing years of reliable performance in dynamic operating environments.
Testing and Inspection Methods for Flexible PCB Vias
To ensure the reliability of flex vias for bending applications, various design analysis, fabrication process, and testing methods should be utilized:
Simulation and Modeling
- Finite element analysis predicts mechanical stress and failure points in proposed flex via designs.
- Thermal modeling analyzes heat dissipation capabilities.
- Electromagnetic analysis models electrical performance.
Process Validation
- Cross-section micrographs validate plating uniformity and hole filling.
- Microscope inspection of hole walls checks for smear or cracks.
- Automated optical inspection ensures minimum annular ring dimensions are maintained.
Plating Tests
- Bond strength tests check plating adhesion to base copper.
- Micro hardness measurements confirm plating hardness.
- Plating thickness measurements verify desired copper thickness is achieved.
Reliability Testing
- HAST, temperature cycling, and shock/vibration tests verify via survivability under stresses.
- Air-to-air flexing tests check for cracks or openings developing.
- Cross-section analysis after testing reveals areas for process improvement.
Implementing the appropriate combination of analysis, inspection, and testing provides full validation of flex PCB via reliability for the application.
Benefits of Laser Drilled Vias in Flexible Circuits
Traditionally, mechanical punching and drilling methods have created via holes in flex PCBs. But laser drilling offers numerous benefits, especially as flex circuits become denser with smaller features:
Improved Precision and Accuracy
- Laser systems drill vias with tight tolerances down to ±0.025mm for more consistent sizing.
- Laser holes exhibit near-perfect circularity with precise positioning.
- Via-in-pad drilling achieves excellent pad-to-hole registration.
Smaller Via Capabilities
- Lasers can ablate holes down to 0.1mm or less, enabling ultra-dense via arrangements.
- Microvias with ±0.05mm tolerance facilitate complex HDI circuit architectures.
Higher Aspect Ratio Vias
- Laser via holes maintain consistent parallel sidewalls at aspect ratios up to 10:1.
- This allows smaller vias to be reliably plated through thicker flex substrates.
Faster Processing
- Lasers drill through shots in nanoseconds, avoiding the mechanical stresses of punching.
- Panel-scale laser via drilling achieves high throughput.
Reduced Damage and Absence of Smear
- The laser ablates material cleanly without distortion or debris.
- No desmear processing is required prior to metallization.
Improved Plating Coverage and Bond Strength
- The pristine, unmarred hole walls provide optimal surfaces for copper plating adhesion.
Blind and Buried Via Capability
- Lasers can selectively ablate vias partially through a PCB layer stack.
- This allows high-density build-up circuit architectures.
As flex PCBs continue trending toward finer features, higher densities, and advanced HDI architectures, laser drilling will become indispensable for achieving the precision small via structures necessary in an economical, reliable manner. The collateral benefits in process simplification, plating quality, and improved reliability are also driving adoption of laser systems.
Conclusion
Vias play a critical role in flexible PCBs by enabling vertical transitions between layers to route traces and connect components. But the demanding mechanical stresses of dynamic flexing environments make via design, layout, and fabrication vital for reliable products. Utilizing the guidelines in this article will allow you to implement robust vias tailored for flex circuit needs.
Key highlights include:
- Size vias appropriately for the substrate thickness and provide adequate annular clearance.
- Use tear-drop pads and thermal reliefs to reduce stress concentrations.
- Stagger vias in grid patterns with maximum spacing in bend areas.
- Balance layouts symmetrically and route traces orthogonally.
- Avoid vias at layer transitions and use blind/buried vias where possible.
- Address potential failure modes like cracking, voids, and misregistration.
- Take advantage of laser drilling capabilities for cost-effective precision and high densities.
Correctly designed and manufactured vias are essential for realizing the full benefits of flexible circuits. By following the recommendations here, you can achieve the mix of electrical connectivity, mechanical integrity, and reliability needed for successful flex PCB products.
FQA
What determines the minimum size and spacing for flex PCB vias?
The minimum via size is primarily determined by the layer copper thickness, in order to achieve a reliable plated connection. Minimum spacing is driven by voltage requirements, manufacturing capabilities, and providing space to route escape traces between vias or pads. Annular ring clearance must also be maintained around drilled holes to prevent cracking.
How many vias should be used for a robust layer-to-layer connection?
As a general guideline, at least 2-3 vias should be used in parallel for each layer transition to provide redundancy in the connection. 4-6 vias are preferable for transitions carrying critical signals or higher currents. The vias are often arranged in staggered or triangular patterns for optimal mechanical performance.
Can flex PCBs use microvias like rigid boards?
Yes, the latest high density interconnect (HDI) flex designs are utilizing laser-drilled microvias with sizes below 0.15mm and pitches down to 0.2mm. This supports complex build-up circuit architectures but requires precise laser drilling and plating processes.
Is it always necessary to match drill sizes when stacking flex layers?
Matching drill sizes per layer ensures vias stack concentrically for most reliable connections. But slightly offsetting select layers with larger holes can help equalize stresses and reduce cracking tendencies during dynamic bending.
Are filled vias better than conventional hollow plated through vias for flex circuits?
Filled vias do provide enhanced mechanical stability and cross-section solder joints due to the solidified plug material. However, filled vias require additional fabrication processing and can increase material costs. Either via type can work well for flex PCBs depending on the specific design needs.