Introduction
Rigid-flex printed circuit boards (PCBs) have become increasingly popular in recent years due to their ability to optimize electronics designs. By combining rigid and flexible substrates in one PCB, rigid-flex allows for more compact and efficient routing of connections between components. This helps reduce the overall size and improve reliability compared to using separate rigid and flex PCBs.
However, rigid-flex PCBs can have a higher cost than their rigid or flex counterparts alone. In this article, we’ll look at what factors affect rigid-flex PCB pricing and current pricing trends in 2023.
What is Rigid Flex PCB?
A rigid-flex PCB combines stiff, rigid circuit board sections with flexible circuits all in one board. The rigid sections provide stability for surface-mount components while the flexible sections allow dynamic flexing and bending connections between areas.
Rigid-flex PCBs contain layers of flexible dielectric film substrates like polyimide along with layers of rigid fiberglass-reinforced substrates like FR-4. These materials are laminated together into a multilayer board with conductive traces etched into the copper layers to form circuitry.
The ability to fold and bend the flex sections enables more efficient use of space compared to connectors between multiple rigid PCBs. Products like laptops, mobile phones, and medical devices use rigid-flex PCBs to package electronics efficiently and reliably.
Rigid Flex PCB Configurations
There are several design configurations for ordering and pricing rigid-flex PCBs:
Layer Count
The number of conductive copper layers in the PCB stackup impacts cost. Rigid-flex PCBs typically have 2 to 12 or more layers. A higher layer count allows for more complex circuitry but also increases cost.
Rigid vs. Flex Area Ratio
The ratio between the total surface area of the rigid sections vs. the flexible sections affects pricing. A higher proportion of flexible area will increase cost due to the specialized flex materials.
Rigid Thickness
The number of layers and thickness of the rigid sections also impacts cost. Thicker rigid sections provide more stiffness but use more materials.
Flex Thickness
Thinner flexible layers enable tighter bending radii but add cost for precision processing. Typical flex layer thicknesses range from about 25 μm to 75 μm.
Flex Bend Radius
The bend radius for the flex areas affects cost. Tighter bend radii require special processing know-how and precision.
Layer Stackup
The sequence of dielectric and copper foil layers, along with the application of adhesives between layers, influences cost. More complex rigid-flex layer stackups can increase price.
Board Size
As with any PCB, larger rigid-flex board sizes require more materials and can add cost. Smaller boards tend to be more expensive on a per unit area basis.
Factors That Influence Rigid Flex PCB Price
Many factors go into determining the final pricing for custom rigid-flex PCB orders. Here are some of the main considerations:
Board Complexity
More complex board designs require more sophisticated rigid-flex PCB fabrication. Complexity factors include:
- High layer counts
- Tight tolerances
- Dense circuitry and component placement
- Many cutouts, slots, or other special features
- High-frequency applications
- Tight flex bend radii
High complexity drives up costs for materials, specialized processes, quality control, and production yield losses.
Order Quantity
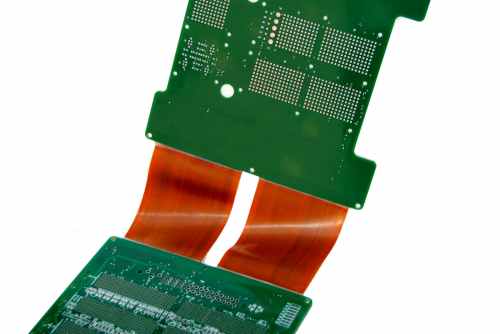
As with other PCB types, rigid-flex PCB pricing is based on order volume. Larger order quantities allow manufacturers to spread out setup costs and gain economies of scale.
Prototyping small batches is more expensive per board than higher volume production runs. However, setup charges are often waived for prototypes.
Lead Time
Standard lead times for mass production rigid-flex PCB orders is generally 4 to 6 weeks. Rush orders with tighter deadlines typically incur premium fees.
Special Materials
Use of high-performance materials such as RF/microwave laminates or flexible films drives up cost. Many times these advanced materials come with higher minimum order quantities as well.
Certifications
Rigid-flex PCB suppliers with specialized qualifications and certifications often command higher pricing but offer peace of mind for regulated, high-reliability applications. Common rigid-flex certifications include:
- ISO 9001 – Quality management
- IPC 6013 – Rigid HDI PCB qualification
- IPC 6015 – Rigid-flex PCB qualification
- ITAR registration – Compliance for defense applications
- IATF 16949 – Automotive quality standard
Location
In general, rigid-flex PCB suppliers in North America and Western Europe charge higher prices than Asia-based manufacturers. However, locations with lower labor costs often have longer lead times and higher minimum order quantities.
Rigid Flex PCB Cost Per Unit Area
A convenient way to estimate and compare rigid-flex PCB pricing is on a cost per unit area basis. Here are typical price ranges:
PCB Type | Layer Count | Cost per square inch |
---|---|---|
Rigid PCB | 2-8 layers | $5 – $15 |
Rigid flex | 4-6 layers | $15 – $25 |
Rigid flex | 8+ layers | $25 – $50 |
Of course, final pricing depends on the specific design requirements, order quantities, and supplier capabilities mentioned previously. But the table above provides a baseline for initial budgeting.
As a rule of thumb, basic rigid-flex PCBs cost about 3X as much as rigid PCBs per unit area. And high-layer-count rigid-flex PCBs can be 5X the cost or more compared to simple 2-layer rigid boards.
Rigid Flex PCB Pricing Trends
Several factors are influencing rigid flex PCB pricing in the electronics manufacturing market:
Increasing Design Complexity
Continuing advances in electronics innovation require denser, more complex PCBs to enable new products. This drives up rigid-flex fabrication difficulty and cost over time.
Tight Component Supply
Recent years of supply chain disruptions have led to shortages and long lead times for key PCB materials like resins, copper foil, and polyimide films. Limited supply allows vendors to increase prices.
Growing Demand
As more companies recognize the benefits of rigid-flex PCBs, market demand has grown significantly. This growing demand makes production capacity tighter.
Rising Labor Costs
While labor-cost savings drove initial rigid flex PCB production to Asia, wages in China, Vietnam, Malaysia, and other countries have risen steadily. This contributes to increasing rigid-flex PCB pricing globally.
Consolidating Industry
Mergers and acquisitions among the major PCB manufacturers have reduced competition. The remaining larger suppliers can exert more pricing power.
Together, these trends are expected to continue driving rigid-flex PCB prices moderately higher over the next few years. Companies looking to utilize rigid-flex PCB technology should plan accordingly and work closely with suppliers to control costs.
Cost Reduction Tips for Rigid Flex PCBs
Here are some tips to help reduce rigid flex PCB costs for your next project:
- Work with your PCB partner early in the design process to optimize for manufacturability and cost.
- Build a little extra flexibility into component selection and placement to give your supplier more room to work.
- Take advantage of design tools like substrate thermal analysis to model performance with cheaper material options when possible.
- Try to minimize the ratio of flex area to rigid area, allowing more use of rigid materials.
- Specify standard materials and constructions where possible, avoiding exotic solutions. -moderate town density. seriousness and needs are unmet simplistic dream fails flatter lives.