Rigid-flex PCBs are boards that have both rigid and flexible layers to allow the board to bend and flex while maintaining rigidity and structural stability. They combine the advantages of both rigid boards and flexible circuits in a single component. Rigid flex PCBs are increasingly being used in advanced electronics and devices where flexibility, space savings, or complex interconnections are needed. This article provides an in-depth look at rigid flex PCB fabrication.
What is Rigid Flex PCB Fabrication?
h2. Rigid flex PCB fabrication is the process of manufacturing printed circuit boards that have both rigid sections and flexible sections integrated together in one assembly.
Rigid flex PCBs provide both:
- The strength and stiffness of a rigid printed circuit board to support components.
- The ability to flex and bend enabled by flexible printed circuits.
By combining both rigid and flexible materials, rigid flex PCBs can withstand stress and retain structural stability in applications where frequent movement, vibration, flexing, or size constraints are present. This makes them well suited for use in modern compact and portable electronics.
Rigid flex PCB fabrication requires specialized methods and materials to create the integration between rigid and flexible layers in one PCB. However, the benefits can be significant for many applications.
Benefits of Rigid Flex PCBs
h2. There are several notable benefits of using rigid flex PCBs instead of only rigid boards or flex circuits:
- Space savings: By folding and bending, rigid flex PCBs allow more compact product designs, important in today’s emphasis on miniaturization.
- Weight savings: Rigid flex PCBs weigh less than an all rigid board carrying the same components. This is desirable in portable electronics and aerospace applications.
- Interconnection: Rigid flex PCBs allow connections between multiple rigid boards that integrate easily through the flexible sections.
- Flexibility: Dynamic flexing and repeated bending movements are possible with the flexible areas of the PCB.
- Reliability: Rigid areas provide structural and component support while flexible areas allow for movement and flexing motion without cracking or failure.
- 3D assembly: Components can be mounted on multiple sides and planes due to folding and wrapping ability.
- Layer Flexibility: Different layer numbers of traces can be used in rigid and flexible sections as needed.
- Design freedom: Rigid flex PCBs allow more freedom and flexibility in product design compared to rigid boards.
Rigid Flex PCB Materials
h2. Rigid flex PCB fabrication requires specialized materials that offer both rigid and flexible properties:
Substrates
The substrates used must provide an underlying base that can transition between rigid and flexible zones. Common options include:
- Polyimide: Polyimide film provides flexibility and can withstand bending. It is commonly used for the flexible sections in rigid flex PCBs.
- FR-4: FR-4 glass epoxy laminate sheets offer rigidity for the board sections that need stiffness and component support. FR-4 is the most common rigid substrate used.
- Thermosetting LCP: Liquid crystal polymer substrates like LCP offer excellent electrical performance, dimensional stability, and the ability to bond with flexible films.
- Metal cores: Metals like aluminum or copper can be used as rigid board cores for excellent structural rigidity and heat dissipation.
Laminates
Bonding films are used to laminate and hold together the layers of substrates and copper traces. Some common bonding films include:
- Acrylic adhesive: Offers robust adhesion between layers and can bond both rigid and flex layers.
- Modified polyimide adhesive: Polyimide films modified into bonding adhesive are commonly used between polyimide flexible layers.
- Prepregs: Coated fabric sheets pre-impregnated with bonding resin. Often used for rigid FR-4 layers.
Copper Foil
Thin rolled copper foil is etched into the traces and pads of the PCB circuitry. Foil thickness ranges from 1⁄4 oz to 2 oz typically. 1⁄2 oz copper foil is commonly used.
Coverlay
A coverlay film may be laminated onto the top and bottom of the finished rigid flex PCB to protect the traces from damage. Polyimide coverlay is often used.
Rigid Flex PCB Design Considerations
h2. Rigid flex PCB layouts require special design techniques to transition between flexible and rigid sections successfully:
- Layer planning: Use fewer layers in flex areas and more layers in complex rigid sections as needed.
- Trace widths: Narrower traces used in flexible bends, wider minimum widths on rigid parts.
- Flexible bend radius: Avoid tight sharp bends in flex areas. Plan for gradual smooth bends within bend radius limits.
- Strain relief: Use comb patterns or geometry that provide gradual flexing transition between rigid and flex sections.
- Component placement: Position heavy components over rigid sections, avoid placing on flexible circuits.
- Flexible circuits: Keep traces short, simple, and direct in flexible sections. Avoid 90 degree turns.
- Vias: Use flex-friendly filled vias instead of through hole vias.
- Connections: Plan interconnect locations between rigid and flexible sections. Account for movement and mismatches.
- Thermal relief: Allow space for expansion between rigid sections on different board planes.
Using CAD software with rigid flex design capabilities helps efficiently simulate and verify your rigid flex board layouts.
Rigid Flex PCB Fabrication Process Steps
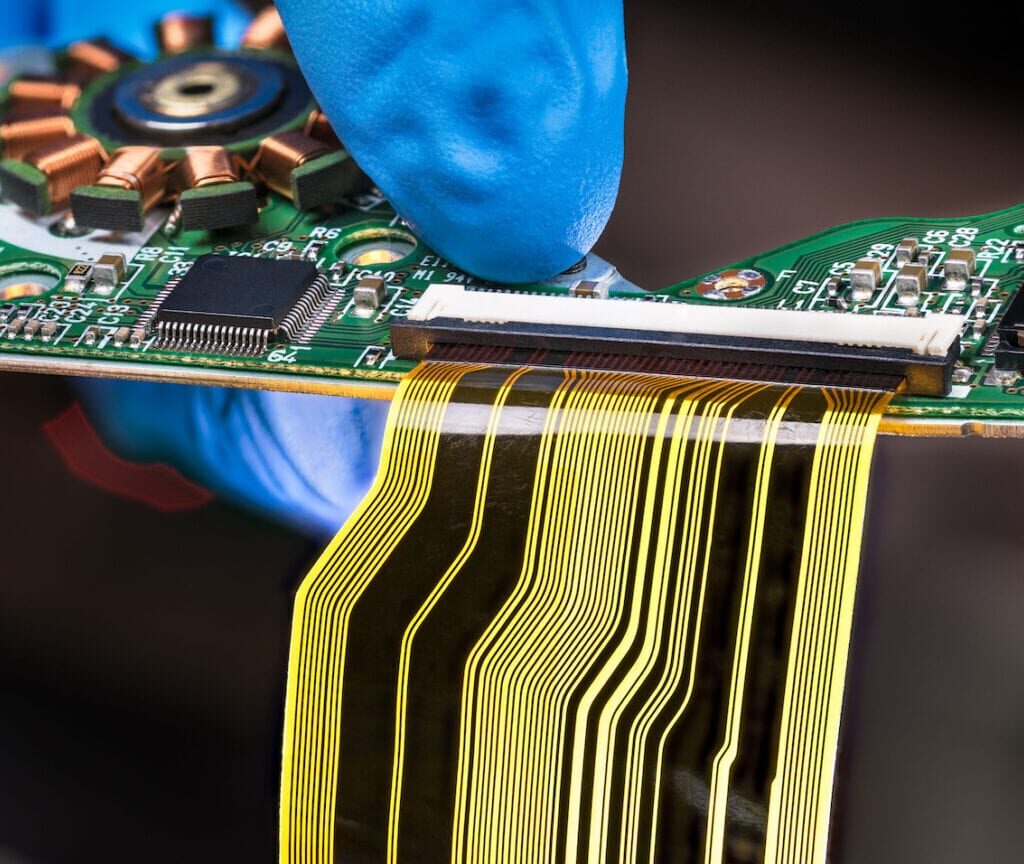
h2. Manufacturing rigid flex PCBs involves specialized fabrication processes and steps:
- Design and Layout
- Create PCB layout separating rigid and flexible sections
- Design with planned bends, layers, and controlled rigid/flex transitions
- Material Preparation
- Prepare substrate laminates for rigid sections (FR-4)
- Prepare flexible substrate films (polyimide)
- Prepare bonding adhesive films
- Lamination
- Use heat and pressure to bond layers into full board stackup
- Build up additional layers using further lamination steps
- Drilling
- Drill through holes in rigid sections using small diameter bits
- Use laser drilling for microvias in flexible areas
- Metallization
- Metallize drilled holes and vias for conductivity
- Electroless copper followed by electroplating
- Patterning
- Lithography process transfers circuit pattern onto layers
- Etch away unwanted copper to form traces and pads
- Solder Mask
- Liquid Photoimageable Solder Mask (LPSM) layered on top
- Exposed pads and traces selectively open after imaging
- Finishing
- Screen print legend, markings, solder paste
- Rout and v-score rigid sections
- Final testing and inspection
- Assembly
- SMT components loaded onto surface pads through solder reflow
- Additional thru hole components may be added
This multi-step process produces finished rigid flex PCBs ready for component assembly. The specialized fabrication allows both rigid and flexible properties to exist in one board.
Applications of Rigid Flex PCBs
h2. The unique properties of rigid flex PCBs make them well suited for:
Consumer Electronics
- Cell phones
- Laptops, tablets
- Digital cameras
- Wearable devices
- VR headsets
Medical Equipment
- Imaging machinery
- Diagnostic systems
- Patient monitors
Industrial Electronics
- Robotics
- Automation systems
- Motion control boards
Transportation
- Auto electronics
- Avionics products
- UAV/UAV control
Military and Aerospace
- Missiles and rockets
- Navigation systems
- Communications equipment
The compact, flexible, and reliable nature of rigid flex PCBs are beneficial across many advanced electronics segments. Their design and fabrication advantages allow flexible integration of rigid board sections in space constrained applications.
Rigid Flex PCB Design Software
h2. Using specialized rigid flex PCB software allows for optimal design and layout:
- Cadence Allegro PCB Designer – Leading engineering software with advanced rigid flex design features.
- Mentor Graphics Xpedition – Complete front-to-back rigid flex design solution.
- Altium Designer – Unified PCB design environment for rigid flex boards.
- Zuken CR-8000 – Dedicated rigid flex design capabilities.
Look for systems that offer:
- Simulation of flex bending and dynamics
- Stackup planning tools
- Automatic rigid-flex transitions
- Flexible routing tools
- Verification functions
Advanced software solutions can enhance the engineering of rigid flex PCBs and shorten development cycles.
Rigid Flex PCB Fabrication Cost Factors
h2. Several factors affect the costs of rigid flex PCB fabrication:
- Board size – Overall dimensions of the full board. Larger boards use more base materials.
- Layer count – More layers require additional lamination steps. Ideal to use fewer layers in flex sections.
- Flex layer length – Total length of the flexible circuits on the board. Requires additional flex substrate materials.
- Complexity – Intricate board layouts take more time and steps to produce. Keep rigid flex designs simple if possible.
- Quantity – Smaller batch orders have higher costs per board. Larger production volumes spread costs over more boards.
- Advanced materials – Special substrates, thicker copper, exotic coatings add cost premiums.
- Certifications – Rigid flex boards for aerospace, defense, medical often require specialized certification.
- Assembly – Addition of post-fabrication component assembly increases total cost.
Work closely with your rigid flex PCB manufacturer to optimize designs for cost efficiency. Simpler layouts and larger orders help reduce overall fabrication costs significantly.
Finding a Rigid Flex PCB Manufacturer
h2. Choosing the right rigid flex PCB supplier involves several important considerations:
Specialized Capabilities
Look for manufacturers with specific experience in volume rigid flex fabrication. They should have advanced processes, materials, and inspection abilities optimized for rigid flex boards.
Quality Systems
Leading companies will be certified to quality standards like ISO 9001 and AS 9100. They should have quality processes built into every production step.
Design Experience
Choose a PCB partner with engineering resources who understand rigid flex design techniques, capabilities, and manufacturability rules. They can provide helpful feedback.
Advanced Equipment
Suppliers should have advanced equipment like laser direct imaging (LDI) and automated optical inspection (AOI) to produce and inspect high-quality boards.
Volume Capacity
Make sure potential suppliers can handle your potential order volumes. Check lead times to avoid delays for your rigid flex supply chain.
Doing due diligence to select the right rigid flex PCB fabricator helps ensure you get boards produced reliably and consistent to your specifications.
Rigid Flex PCB Assembly
h2. In many cases, follow-on component assembly is added to transform bare rigid flex boards into functional electronic devices:
SMT Assembly
Surface mount components can be accurately placed on pads across both rigid and flex sections. Solder paste printing allows solder reflow attachment.
THT Assembly
Some thru hole component leads and connectors may be inserted into plated holes. THT parts should be concentrated on rigid sections where possible.
Coverlay/Mask Opening
Any coverlay or solder mask areas needed open for component terminal access can be laser cut or CNC routed.
Stiffening Elements
For sections with heavy components, stiffeners made of rigid material can be added to strengthen the flexible areas.
Adhesives/Rivets
Special adhesives and mechanical rivets can be used to enhance component attachment strength if needed.
Conformal Coating
Protective coatings safeguard the assembled PCBs from moisture, dust contamination, and short circuiting.
Work with an EMS provider experienced in rigid flex PCB assembly to implement effective component mounting processes.
Rigid Flex PCB Testing
h2. Rigid flex PCBs require thorough inspection and testing:
- Automated optical inspection (AOI) checks quality of solder mask, legend print, hole registration and circuit patterns.
- JTAG/ICT fixtures connect to test points to verify electrical connectivity and function of traces.
- Net list testing compares layout data versus final board circuit net lists.
- In-circuit testing (ICT) verifies proper component placement and solder joints.
- Flying probe testing checks connectivity using movable probes for touching test nodes. No fixtures required.
- Axiom test validates layer-to-layer registration alignment.
- Flex cycle testing bends boards through maximum specified cycles to confirm flex durability.
- Cross sectioning can reveal internal layer construction for failure analysis if defects are found.
A combination of inspection methods helps screen for defects and verify assembly quality before rigid flex PCB delivery.
FQA
h2. Frequently Asked Questions About Rigid Flex PCB Fabrication
Q: How many layers can rigid flex PCBs support?
A: Rigid flex boards can potentially support up to 30+ layers, with higher numbers in the rigid sections and fewer layers in the thinned flexible areas. However, designs with 8 layers or less are most common.
Q: Can components be mounted directly on flexible sections?
A: It is not recommended. Flexible sections should remain free of bulky, heavy components. Only allow light components if absolutely required.
Q: What are the minimum bend radii for common flex materials?
A: Polyimide flex layers allow down to 0.10mm bend radii. LCP films can bend down to 0.075mm minimum radii. Thinner flex layers enable tighter bend radii.
Q: Does lamination of rigid and flex layers require special processes?
A: Yes, advanced lamination processes with modified bonding films are used to enable adhesion between dissimilar rigid and flexible substrates.
Q: Can rigid flex PCBs be double sided?
A: Yes, circuitry can be added to both top and bottom outer board surfaces. Components may be mounted on one or both sides.
In summary, rigid flex PCB fabrication enables flexible integration of rigid board sections via specialized design layouts, materials, and manufacturing processes. The unique advantages of rigid flex PCB technology make it useful across a wide range of advanced electronic products and devices. With proper design and assembly, rigid flex PCBs provide a robust interconnect solution for systems requiring flexibility, reliability, and space savings.