Understanding Impedance in PCBs
Impedance is a measure of the opposition that a circuit presents to the flow of alternating current (AC) at a given frequency. In the context of PCBs, impedance refers to the characteristic impedance of the transmission lines, which are the conductive traces that carry signals between components. The characteristic impedance of a transmission line depends on several factors, including the geometry of the trace, the dielectric properties of the substrate material, and the proximity of other conductive elements.
Factors Affecting Impedance in PCBs
-
Trace Geometry: The width, thickness, and spacing of the conductive traces on a PCB play a significant role in determining the characteristic impedance. Wider traces have lower impedance, while narrower traces have higher impedance. The thickness of the trace also affects impedance, with thicker traces having lower impedance than thinner ones.
-
Substrate Material: The dielectric constant (Dk) and dissipation factor (Df) of the substrate material influence the impedance of the transmission lines. Materials with higher Dk values, such as FR-4, result in lower impedance compared to materials with lower Dk values, like Rogers laminates. The Df of the substrate material determines the loss tangent, which affects the signal attenuation and quality.
-
Proximity Effects: The presence of other conductive elements, such as adjacent traces, power planes, or ground planes, can impact the impedance of a transmission line. The closer the proximity of these elements, the greater the influence on the impedance. Proper spacing and shielding techniques are employed to minimize the effects of proximity on impedance.
Common Impedance Values in PCBs
The choice of impedance value depends on the specific application, the signaling standard being used, and the desired performance characteristics. Here are some common impedance values found in PCB designs:
Impedance Value | Application |
---|---|
50 ohms | RF circuits, high-speed digital interfaces |
75 ohms | Video applications, coaxial cables |
90 ohms | USB 3.0 differential pairs |
100 ohms | Ethernet, LVDS differential pairs |
120 ohms | CAN bus, RS-485 differential pairs |
50 Ohms Impedance
50 ohms is one of the most commonly used impedance values in PCB design, particularly for RF circuits and high-speed digital interfaces. This value provides a good balance between power handling capability and signal integrity. Many RF connectors, such as SMA and BNC, are designed for 50-ohm systems. High-speed digital interfaces, like HDMI and PCIe, also utilize 50-ohm impedance for single-ended traces.
Differential Impedance
Differential signaling is widely used in high-speed digital communication to improve noise immunity and reduce electromagnetic interference (EMI). Differential pairs, consisting of two interconnected traces with equal and opposite signals, are designed to have a specific differential impedance. Common differential impedance values include 90 ohms for USB 3.0 and 100 ohms for Ethernet and LVDS interfaces.
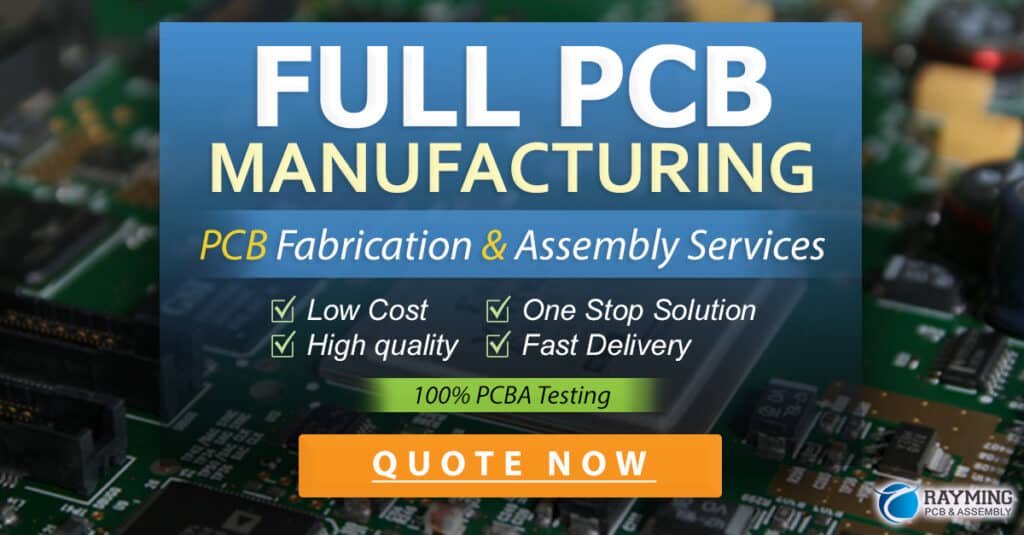
Impedance Control Techniques in PCB Design
To achieve the desired impedance in a PCB design, various techniques are employed during the layout and manufacturing process. These techniques ensure that the characteristic impedance of the transmission lines matches the target value, minimizing signal reflections and distortions.
Trace Geometry Control
One of the primary methods of controlling impedance is by adjusting the geometry of the conductive traces. The width and thickness of the traces are carefully selected based on the desired impedance value and the properties of the substrate material. Impedance calculators and simulation tools are used to determine the appropriate trace dimensions for a given impedance target.
Dielectric Material Selection
The choice of substrate material plays a crucial role in achieving the desired impedance. Materials with consistent dielectric properties, such as FR-4 or high-performance laminates like Rogers, are commonly used for impedance-controlled designs. The dielectric constant and dissipation factor of the material are considered when calculating the impedance of the transmission lines.
Shielding and Grounding Techniques
Proper shielding and grounding techniques are essential for maintaining the integrity of impedance-controlled traces. Ground planes are often used to provide a stable reference for the signals and to minimize the impact of external noise. Shielding techniques, such as the use of coplanar waveguides or shielded traces, help to reduce crosstalk and interference between adjacent signals.
Manufacturing Process Control
The manufacturing process of the PCB must be tightly controlled to ensure that the impedance targets are met consistently. Factors such as copper plating thickness, etching accuracy, and laminate thickness variations can affect the impedance of the transmission lines. Stringent process controls and regular impedance testing are implemented to maintain the desired impedance values throughout the manufacturing process.
Benefits of Impedance Control in PCB Design
Implementing impedance control in PCB design offers several benefits for high-speed digital and RF applications:
-
Signal Integrity: Matched impedance ensures that signals propagate through the transmission lines with minimal reflections and distortions. This improves signal quality, reduces bit error rates, and enables faster data transmission speeds.
-
Reduced EMI: Proper impedance control helps to minimize electromagnetic interference (EMI) by reducing the amount of radiated emissions from the PCB. This is particularly important for meeting regulatory compliance standards and preventing interference with nearby electronic devices.
-
Improved Timing Margins: Impedance-controlled traces exhibit consistent propagation delays, which is crucial for maintaining tight timing margins in high-speed digital systems. Matched impedance helps to prevent signal skew and ensures that signals arrive at their destinations within the specified timing windows.
-
Enhanced Reliability: By minimizing signal reflections and reducing stress on the components, impedance control contributes to the overall reliability of the PCB. It helps to prevent signal integrity issues that can lead to system failures or intermittent behavior.
Challenges and Considerations
While impedance control is essential for high-speed PCB designs, it also presents some challenges and considerations:
-
Increased Design Complexity: Implementing impedance control requires careful planning and analysis during the PCB design process. Trace geometry, spacing, and routing must be optimized to achieve the desired impedance, which can add complexity to the layout.
-
Higher Manufacturing Costs: Impedance-controlled PCBs typically require tighter manufacturing tolerances and additional process steps, such as impedance testing and verification. This can increase the overall manufacturing costs compared to non-impedance-controlled designs.
-
Material Selection: Choosing the appropriate substrate material is critical for achieving the desired impedance. High-performance materials with consistent dielectric properties may be more expensive than standard FR-4 laminates.
-
Signal Integrity Simulation: To ensure the integrity of impedance-controlled traces, signal integrity simulations are often performed during the design phase. These simulations help to identify potential issues and optimize the design before fabrication, but they require specialized tools and expertise.
FAQ
-
Q: What is the purpose of impedance control in PCB design?
A: Impedance control in PCB design ensures that the characteristic impedance of transmission lines matches the impedance of the source and load, minimizing signal reflections and distortions. It is essential for maintaining signal integrity in high-speed digital and RF circuits. -
Q: How does trace geometry affect impedance in PCBs?
A: Trace geometry, including the width, thickness, and spacing of the conductive traces, directly influences the characteristic impedance of the transmission lines. Wider traces have lower impedance, while narrower traces have higher impedance. The thickness of the trace also affects impedance, with thicker traces having lower impedance than thinner ones. -
Q: What are some common impedance values used in PCB design?
A: Common impedance values in PCB design include 50 ohms for RF circuits and high-speed digital interfaces, 75 ohms for video applications and coaxial cables, 90 ohms for USB 3.0 differential pairs, 100 ohms for Ethernet and LVDS differential pairs, and 120 ohms for CAN bus and RS-485 differential pairs. -
Q: How does the choice of substrate material affect impedance in PCBs?
A: The dielectric constant (Dk) and dissipation factor (Df) of the substrate material influence the impedance of the transmission lines. Materials with higher Dk values, such as FR-4, result in lower impedance compared to materials with lower Dk values, like Rogers laminates. The Df of the substrate material determines the loss tangent, which affects signal attenuation and quality. -
Q: What are the benefits of implementing impedance control in PCB design?
A: Implementing impedance control in PCB design offers several benefits, including improved signal integrity, reduced electromagnetic interference (EMI), improved timing margins, and enhanced reliability. It ensures that signals propagate through the transmission lines with minimal reflections and distortions, enabling faster data transmission speeds and reducing the risk of system failures.
Conclusion
Impedance control is a critical aspect of PCB design, particularly for high-speed digital and RF applications. Understanding the concept of common impedance values and the factors that influence impedance, such as trace geometry, substrate material, and proximity effects, is essential for designing reliable and high-performance PCBs. By employing impedance control techniques, such as trace geometry control, dielectric material selection, shielding, and grounding, designers can ensure the integrity of signals and minimize signal reflections and distortions.
While implementing impedance control presents challenges, such as increased design complexity and higher manufacturing costs, the benefits of improved signal integrity, reduced EMI, and enhanced reliability make it a necessary consideration for modern PCB designs. As electronic systems continue to push the boundaries of speed and performance, impedance control will remain a crucial factor in ensuring the success and reliability of these systems.