Introduction to Thermal Relief PCBs
In the world of printed circuit board (PCB) design, thermal management is a crucial aspect that ensures the proper functioning and longevity of electronic components. One technique used to manage heat dissipation is the incorporation of thermal relief patterns in the PCB layout. A thermal relief PCB is designed to provide a controlled path for heat to escape from components, preventing overheating and potential damage.
What is a Thermal Relief?
A thermal relief is a specialized pattern etched into the copper layer of a PCB, surrounding the pads of heat-generating components such as power transistors, voltage regulators, or high-current devices. The pattern consists of a series of thin copper traces, known as spokes, that connect the component pad to the surrounding copper pour or plane.
The primary purpose of a thermal relief is to create a thermal barrier between the component and the surrounding copper. By reducing the amount of direct copper connection, the thermal relief limits the heat transfer from the component to the PCB, allowing the heat to dissipate more gradually and evenly.
Why are Thermal Reliefs Important?
Thermal reliefs play a vital role in the overall thermal management strategy of a PCB. Here are some key reasons why thermal reliefs are important:
-
Overheating Prevention: Electronic components generate heat during operation, and if this heat is not effectively dissipated, it can lead to overheating. Overheating can cause component failure, reduced performance, and even permanent damage to the PCB. Thermal reliefs help prevent overheating by providing a controlled path for heat dissipation.
-
Solder Joint Integrity: During the soldering process, the high temperature of the molten solder can cause thermal shock to the components and the PCB. If there is a large amount of copper directly connected to the component pad, the heat from the soldering process can rapidly transfer to the surrounding area, leading to thermal stress and potential solder joint failures. Thermal reliefs reduce the amount of direct copper connection, minimizing the thermal shock and ensuring better solder joint integrity.
-
Even Heat Distribution: Thermal reliefs promote even heat distribution across the PCB. By limiting the direct copper connection, the heat from the component is spread out more gradually through the thermal relief spokes. This helps prevent hot spots and ensures a more uniform temperature distribution, reducing the risk of thermal-related issues.
-
Improved Manufacturing Process: Thermal reliefs also benefit the PCB manufacturing process. During soldering, the thermal relief pattern allows for better solder wicking and helps prevent solder bridges or shorts. The spokes of the thermal relief provide a clear path for the molten solder to flow, resulting in more reliable and consistent solder joints.
Thermal Relief Design Considerations
When designing a thermal relief PCB, several factors need to be considered to ensure optimal performance and reliability. Let’s explore some of the key design considerations:
Thermal Relief Pattern
The thermal relief pattern is typically designed as a series of thin copper traces or spokes that radiate outward from the component pad. The number, width, and spacing of these spokes can vary depending on the specific requirements of the PCB and the component.
A common thermal relief pattern consists of four spokes, arranged in a cross or star shape around the component pad. The width of the spokes is usually narrower than the surrounding copper pour to create the desired thermal barrier. The spacing between the spokes is also important, as it determines the amount of copper connection and affects the heat dissipation characteristics.
Spoke Width and Spacing
The width and spacing of the thermal relief spokes are critical parameters that impact the thermal performance of the PCB. Narrower spokes provide a greater thermal barrier, limiting the heat transfer from the component to the surrounding copper. However, if the spokes are too narrow, they may not have sufficient current-carrying capacity, leading to potential voltage drops or signal integrity issues.
On the other hand, wider spokes allow for better current flow but reduce the thermal isolation effect. The optimal spoke width depends on factors such as the component power dissipation, the desired thermal resistance, and the manufacturing capabilities.
The spacing between the spokes also plays a role in thermal management. Larger spacing reduces the amount of direct copper connection, enhancing the thermal isolation. However, if the spacing is too large, it may compromise the structural integrity of the copper pour and make the PCB more susceptible to mechanical stress.
Thermal Pad Size and Shape
The size and shape of the thermal pad, which is the area of the component pad exposed to the thermal relief pattern, are important considerations in thermal relief design. A larger thermal pad allows for better heat dissipation, as it provides more surface area for heat transfer. However, increasing the thermal pad size also increases the amount of direct copper connection, reducing the thermal isolation effect.
The shape of the thermal pad can also influence the thermal performance. Circular or oval-shaped thermal pads are commonly used, as they provide a symmetrical heat distribution. However, in some cases, rectangular or polygon-shaped thermal pads may be employed to accommodate specific component geometries or to optimize the available space on the PCB.
Copper Pour and Plane Connection
The connection between the thermal relief spokes and the surrounding copper pour or plane is another important design consideration. The copper pour acts as a heat sink, helping to dissipate the heat from the component through the thermal relief spokes.
The size and shape of the copper pour can impact the thermal performance of the PCB. A larger copper pour provides more area for heat dissipation, but it also increases the overall thermal mass of the PCB. The shape of the copper pour should be designed to ensure an even heat distribution and avoid any potential hot spots.
The connection between the thermal relief spokes and the copper pour should be designed to minimize the thermal resistance while maintaining good electrical conductivity. The spokes should be connected to the copper pour at multiple points to provide a low-resistance path for heat transfer.
Component Power Dissipation
The power dissipation of the component is a critical factor in determining the thermal relief design. Components with higher power dissipation generate more heat and require more effective thermal management techniques.
When designing a thermal relief for a high-power component, it is important to consider the maximum power dissipation specified by the manufacturer. The thermal relief design should be able to handle the expected heat generation and ensure that the component operates within its safe operating temperature range.
In some cases, additional thermal management techniques may be necessary, such as the use of heatsinks, thermal vias, or active cooling methods, in conjunction with the thermal relief pattern.
Manufacturing Considerations
The manufacturing process and capabilities also influence the thermal relief design. The PCB fabrication process, including etching, drilling, and plating, should be taken into account when designing the thermal relief pattern.
The minimum spoke width and spacing achievable by the PCB manufacturer should be considered to ensure that the thermal relief design is manufacturable. The aspect ratio of the thermal relief spokes, which is the ratio of the spoke length to its width, should also be within the acceptable range for the manufacturing process.
It is important to communicate with the PCB manufacturer and provide clear specifications for the thermal relief design to ensure that the desired thermal performance can be achieved while maintaining manufacturability.
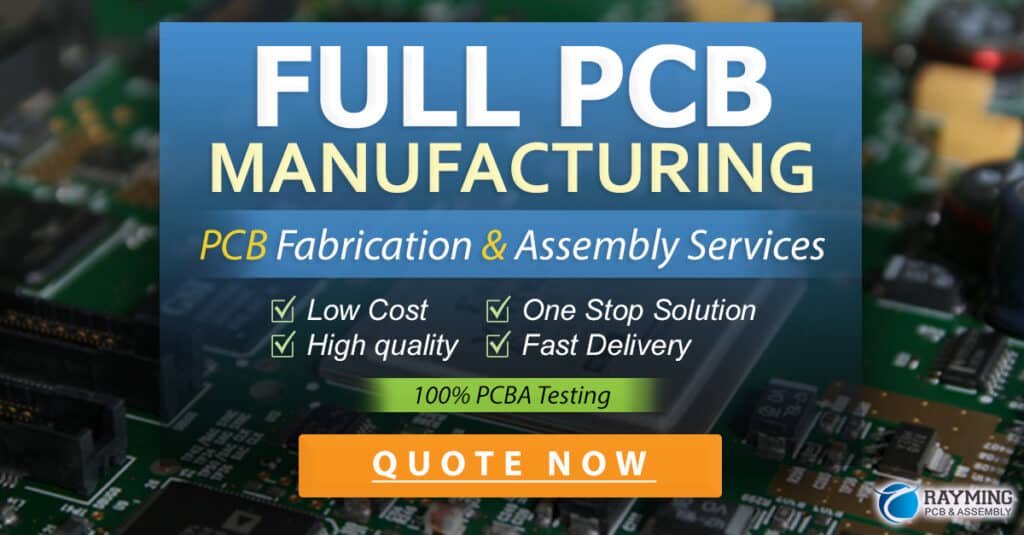
Thermal Relief Design Guidelines
To optimize the thermal performance of a PCB with thermal reliefs, here are some general design guidelines to follow:
-
Use an appropriate thermal relief pattern: Select a thermal relief pattern that provides a good balance between thermal isolation and electrical conductivity. The commonly used four-spoke pattern is a good starting point, but other patterns such as six or eight spokes can also be considered based on specific requirements.
-
Choose suitable spoke width and spacing: Determine the appropriate spoke width and spacing based on the component power dissipation, desired thermal resistance, and manufacturing capabilities. Narrower spokes provide better thermal isolation but may have limited current-carrying capacity. Wider spokes allow for better current flow but reduce the thermal isolation effect. Find the right balance that meets the thermal and electrical requirements of the PCB.
-
Optimize the thermal pad size and shape: Select the thermal pad size and shape based on the component size, power dissipation, and available space on the PCB. A larger thermal pad improves heat dissipation but reduces thermal isolation. Consider using circular or oval-shaped thermal pads for symmetrical heat distribution, or rectangular or polygon-shaped pads to accommodate specific component geometries.
-
Ensure proper copper pour and plane connection: Design the copper pour and plane connection to provide an effective heat sink for the thermal relief spokes. Ensure an even heat distribution and avoid potential hot spots. Connect the thermal relief spokes to the copper pour at multiple points to minimize thermal resistance and ensure good electrical conductivity.
-
Consider component power dissipation: Take into account the maximum power dissipation of the component when designing the thermal relief. Ensure that the thermal relief design can handle the expected heat generation and maintain the component within its safe operating temperature range. If necessary, incorporate additional thermal management techniques such as heatsinks or thermal vias.
-
Collaborate with the PCB manufacturer: Communicate with the PCB manufacturer and provide clear specifications for the thermal relief design. Consider the manufacturing capabilities, including minimum spoke width and spacing, and the aspect ratio of the thermal relief spokes. Ensure that the design is manufacturable and can achieve the desired thermal performance.
Thermal Relief Design Tools and Simulation
To aid in the design and optimization of thermal relief PCBs, various tools and simulation techniques are available. These tools help designers analyze the thermal behavior of the PCB and make informed decisions about the thermal relief design.
Thermal Simulation Software
Thermal simulation software, such as ANSYS Icepak or Mentor Graphics FloTHERM, allows designers to model and simulate the thermal performance of a PCB. These tools use finite element analysis (FEA) or computational fluid dynamics (CFD) techniques to predict the temperature distribution, heat flow, and thermal gradients on the PCB.
By importing the PCB layout and specifying the component power dissipation, material properties, and boundary conditions, designers can simulate the thermal behavior of the PCB under various operating conditions. The simulation results provide valuable insights into the effectiveness of the thermal relief design, helping to identify potential hot spots and optimize the thermal management strategy.
PCB Design Software with Thermal Analysis
Many PCB design software packages, such as Altium Designer or Cadence OrCAD, include thermal analysis capabilities. These tools allow designers to incorporate thermal relief patterns into the PCB layout and perform basic thermal analysis within the design environment.
The thermal analysis features in PCB design software typically use simplified models and algorithms to estimate the temperature distribution and thermal gradients on the PCB. While these tools may not provide the same level of accuracy as dedicated thermal simulation software, they offer a quick and convenient way to assess the thermal performance of the PCB during the design process.
Thermal Imaging and Measurement
Thermal imaging and measurement techniques are valuable for validating the thermal performance of a PCB with thermal reliefs. Thermal cameras or infrared thermography can be used to capture the temperature distribution on the PCB surface during operation.
By comparing the thermal images with the expected temperature profile from simulations or calculations, designers can assess the effectiveness of the thermal relief design and identify any discrepancies or areas for improvement. Thermal measurements using thermocouples or resistance temperature detectors (RTDs) can also provide accurate temperature data at specific points on the PCB.
Design Guidelines and Best Practices
In addition to simulation and measurement tools, designers can refer to established design guidelines and best practices for thermal relief PCBs. Industry standards, such as IPC-2221 or IPC-7351, provide recommendations for thermal relief design parameters, including spoke width, spacing, and thermal pad sizes.
Designers can also leverage the knowledge and experience of PCB design communities, forums, and application notes from component manufacturers. These resources offer valuable insights, tips, and tricks for designing effective thermal relief patterns based on real-world applications and case studies.
Thermal Relief PCB Manufacturing Process
The manufacturing process of a thermal relief PCB involves several steps to ensure the accurate and reliable creation of the thermal relief pattern. Let’s explore the key stages of the manufacturing process:
PCB Fabrication
The PCB fabrication process begins with the creation of the PCB layout and design files. The thermal relief pattern is incorporated into the copper layer artwork, specifying the spoke width, spacing, and thermal pad geometry.
The PCB fabrication process typically involves the following steps:
-
Substrate Preparation: The PCB substrate, usually made of FR-4 or other laminate materials, is cut to the required size and shape.
-
Copper Cladding: Copper foil is laminated onto the substrate using heat and pressure. The copper foil forms the conductive layer of the PCB.
-
Drilling: Holes are drilled through the PCB substrate at the locations specified in the design files. These holes accommodate component leads, vias, and mounting points.
-
Patterning: The copper layer is patterned using a photolithography process. The desired copper traces, including the thermal relief pattern, are selectively etched away, leaving the required conductive paths.
-
Plating: The drilled holes and exposed copper areas are plated with a conductive material, typically copper, to enhance the electrical conductivity and protect against oxidation.
-
Solder Mask Application: A solder mask layer is applied over the copper layer, leaving only the exposed pads and areas required for soldering. The solder mask helps prevent solder bridging and provides insulation between adjacent traces.
-
Silkscreen Printing: The component labels, annotations, and other markings are printed onto the PCB surface using silkscreen printing.
-
Surface Finish: A surface finish, such as HASL (Hot Air Solder Leveling), ENIG (Electroless Nickel Immersion Gold), or OSP (Organic Solderability Preservative), is applied to the exposed copper areas to protect against oxidation and enhance solderability.
Soldering Process
Once the PCB fabrication is complete, the components are soldered onto the board. The soldering process is critical for ensuring good thermal and electrical connections between the components and the PCB.
The soldering process can be performed using various techniques, such as wave soldering, reflow soldering, or hand soldering, depending on the type and quantity of components.
During soldering, the thermal relief pattern plays a crucial role in managing the heat transfer from the component to the PCB. The thermal relief spokes allow for controlled heat dissipation, preventing thermal shock and ensuring reliable solder joint formation.
Inspection and Quality Control
After soldering, the PCB undergoes inspection and quality control processes to verify the integrity of the solder joints and the overall functionality of the board.
Visual inspection is performed to check for any visible defects, such as solder bridges, cold solder joints, or component misalignment. Automated optical inspection (AOI) systems can be used for high-volume production to detect and identify potential issues.
Electrical testing is conducted to verify the continuity and functionality of the PCB. This may include in-circuit testing (ICT), flying probe testing, or functional testing to ensure that the PCB meets the specified electrical requirements.
Thermal imaging or thermal measurement techniques may also be employed to validate the thermal performance of the PCB and ensure that the thermal relief design is functioning as intended.
Frequently Asked Questions (FAQ)
-
What is the purpose of a thermal relief in a PCB?
A thermal relief in a PCB is designed to provide a controlled path for heat to escape from components, preventing overheating and potential damage. It creates a thermal barrier between the component and the surrounding copper, allowing heat to dissipate more gradually and evenly. -
How does a thermal relief pattern improve solder joint reliability?
A thermal relief pattern improves solder joint reliability by reducing the amount of direct copper connection between the component pad and the surrounding copper. This minimizes thermal shock during the soldering process, preventing solder joint failures caused by rapid heat transfer. -
What factors should be considered when designing a thermal relief pattern?
When designing a thermal relief pattern, several factors should be considered, including the component power dissipation, desired thermal resistance, manufacturing capabilities, thermal pad size and shape, copper pour and plane connection, and the overall thermal management strategy of the PCB. -
How can thermal simulation software assist in thermal relief PCB design?
Thermal simulation software allows designers to model and simulate the thermal performance of a PCB with thermal reliefs. By importing the PCB layout and specifying the component power dissipation, material properties, and boundary conditions, designers can predict the temperature distribution, heat flow, and thermal gradients on the PCB. This helps identify potential hot spots and optimize the thermal relief design. -
What are some common guidelines for designing effective thermal relief patterns?
Some common guidelines for designing effective thermal relief patterns include using an appropriate thermal relief pattern (e.g., four-spoke pattern), choosing suitable spoke width and spacing based on thermal and electrical requirements, optimizing the thermal pad size and shape, ensuring proper copper pour and plane connection, considering component power dissipation, and collaborating with the PCB manufacturer to ensure manufacturability and achieve the desired thermal performance.
Conclusion
Thermal relief PCBs play a vital role in ensuring the reliable operation and longevity of electronic components. By incorporating thermal relief patterns into the PCB layout, designers can effectively manage heat dissipation, prevent overheating, and improve solder joint reliability.
Designing an effective thermal relief PCB requires careful consideration of various factors, including the thermal relief pattern, spoke width and spacing, thermal pad size and shape, copper pour and plane connection, component power dissipation, and manufacturing capabilities.
Thermal simulation software, PCB design tools with thermal analysis features, and thermal imaging and measurement techniques can aid in the design and optimization of thermal relief PCBs. Established design guidelines and best practices, along with collaboration with PCB manufacturers, further contribute to achieving the desired thermal performance.
The manufacturing process of a thermal relief PCB involves precise fabrication techniques, including copper patterning, drilling, plating, and soldering. Inspection and quality control processes ensure the integrity of the solder joints and the overall functionality of the PCB.
By understanding the principles and best practices of thermal relief PCB design and manufacturing, engineers and designers can create reliable and