Understanding the Importance of Gold Thickness on PCBs
When it comes to printed circuit boards (PCBs), the thickness of the gold plating plays a crucial role in determining the overall quality, durability, and performance of the board. Gold is a popular choice for PCB surface finishes due to its excellent conductivity, corrosion resistance, and ability to provide a reliable contact surface for components. In this article, we will explore the various aspects of gold thickness on PCBs, including the benefits, standards, and factors that influence the choice of gold thickness.
The Role of Gold in PCB Manufacturing
Gold is widely used in the PCB industry as a surface finish for several reasons:
- Excellent conductivity: Gold is an exceptional conductor of electricity, ensuring efficient signal transmission and minimizing power loss.
- Corrosion resistance: Gold is highly resistant to oxidation and corrosion, protecting the underlying copper traces from environmental factors that could degrade performance.
- Solderability: Gold provides a compatible surface for soldering components, ensuring strong and reliable connections.
- Durability: Gold-plated PCBs offer enhanced durability, withstanding multiple cycles of insertion and removal of components without wearing out.
Standard Gold Thicknesses for PCBs
The thickness of gold plating on a PCB is typically measured in microinches (μin) or microns (μm). The most common gold thicknesses used in the PCB industry are:
Gold Thickness | Microinches (μin) | Microns (μm) |
---|---|---|
Flash Gold | 3 – 7 | 0.08 – 0.18 |
Soft Gold | 10 – 30 | 0.25 – 0.76 |
Hard Gold | 50 – 100 | 1.27 – 2.54 |
-
Flash Gold (3-7 μin / 0.08-0.18 μm): This is the thinnest gold plating option, primarily used for short-term storage and protection of the PCB surface. It is not suitable for high-reliability applications or multiple cycles of soldering.
-
Soft Gold (10-30 μin / 0.25-0.76 μm): Soft gold is the most common choice for PCBs, offering a balance between cost and performance. It provides good solderability, conductivity, and moderate wear resistance. Soft gold is suitable for most general-purpose applications.
-
Hard Gold (50-100 μin / 1.27-2.54 μm): Hard gold is the thickest and most durable option, ideal for high-reliability applications that require frequent insertion and removal of components, such as connectors and edge card contacts. The increased thickness offers superior wear resistance and long-term stability.
Factors Influencing Gold Thickness Selection
When choosing the appropriate gold thickness for a PCB, several factors must be considered:
-
Application requirements: The intended use of the PCB dictates the required gold thickness. High-reliability applications, such as aerospace, military, or medical devices, may demand thicker gold plating for enhanced durability and long-term performance.
-
Cost considerations: Thicker gold plating increases the overall cost of the PCB. Balancing the required performance with budget constraints is essential in selecting the appropriate gold thickness.
-
Component compatibility: The gold thickness should be compatible with the components used on the PCB. Some components may require specific gold thicknesses for optimal solderability and connection reliability.
-
Manufacturing process: The PCB manufacturing process can influence the choice of gold thickness. For example, if the PCB undergoes multiple soldering cycles or exposure to high temperatures, a thicker gold plating may be necessary to withstand the process.
The Benefits of Thick Gold PCBs
Thick gold PCBs, typically referring to those with hard gold plating (50-100 μin / 1.27-2.54 μm), offer several advantages over thinner gold options:
-
Enhanced durability: The increased thickness of hard gold plating provides superior wear resistance, making the PCB more durable and capable of withstanding frequent insertion and removal of components without damage.
-
Improved contact reliability: Thick gold ensures a stable and reliable contact surface for components, minimizing the risk of contact failures or signal integrity issues over time.
-
Corrosion resistance: The thicker gold layer offers better protection against corrosion and oxidation, prolonging the lifespan of the PCB and maintaining its performance in harsh environments.
-
High-temperature stability: Thick gold PCBs can withstand higher operating temperatures without degradation, making them suitable for applications that generate significant heat or operate in high-temperature environments.
Applications of Thick Gold PCBs
Thick gold PCBs are commonly used in industries and applications that demand high reliability, durability, and long-term performance:
-
Aerospace and defense: These sectors require PCBs that can withstand extreme conditions, frequent mating cycles, and maintain stable connections over extended periods.
-
Medical devices: Medical equipment PCBs often employ thick gold to ensure reliable performance and minimize the risk of failure, as these devices are critical to patient safety and well-being.
-
Automotive electronics: Thick gold PCBs are used in automotive applications that require robust and durable connections, such as engine control units, sensors, and safety systems.
-
Industrial automation: Industrial equipment and machinery rely on thick gold PCBs for reliable signal transmission and long-term durability in demanding environments.
Challenges and Considerations for Thick Gold PCBs
While thick gold PCBs offer numerous benefits, there are some challenges and considerations to keep in mind:
-
Cost: Thick gold plating is more expensive than thinner options, which can impact the overall cost of the PCB. Balancing the required performance with budget constraints is crucial.
-
Manufacturing complexity: Applying a thicker gold layer requires more precise control over the plating process, which can increase manufacturing complexity and lead time.
-
Solderability: Thick gold can sometimes pose challenges for solderability, as the gold layer may not fully dissolve during the soldering process, potentially leading to weak or unreliable connections. Proper process control and optimization are essential to mitigate this risk.
-
Design considerations: When designing a PCB with thick gold plating, it is important to consider the specific requirements of the components and ensure compatibility with the chosen gold thickness. Proper layout and design practices should be followed to optimize performance and reliability.
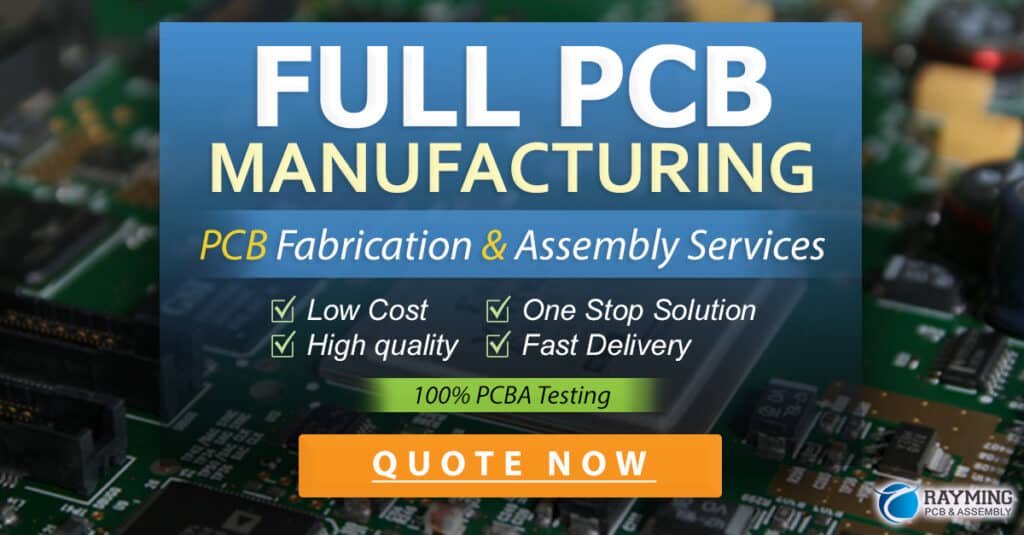
Conclusion
The thickness of gold on a PCB plays a critical role in determining its performance, durability, and reliability. Understanding the various gold thickness options, their benefits, and the factors that influence the selection process is essential for designing and manufacturing high-quality PCBs.
Thick gold PCBs, particularly those with hard gold plating, offer superior durability, contact reliability, and corrosion resistance, making them ideal for demanding applications in industries such as aerospace, medical devices, automotive electronics, and industrial automation.
While thick gold PCBs come with some challenges, such as increased cost and manufacturing complexity, the benefits they provide in terms of long-term performance and reliability often outweigh these considerations.
By carefully evaluating the application requirements, component compatibility, and manufacturing processes, PCB designers and manufacturers can select the appropriate gold thickness to ensure optimal performance and long-term success of their products.
Frequently Asked Questions (FAQ)
-
Q: What is the most common gold thickness used in PCBs?
A: The most common gold thickness used in PCBs is soft gold, which ranges from 10 to 30 microinches (0.25 to 0.76 microns). Soft gold provides a good balance between cost and performance, offering adequate solderability, conductivity, and moderate wear resistance for most general-purpose applications. -
Q: When should I choose thick gold plating for my PCB?
A: Thick gold plating, typically referring to hard gold (50-100 microinches / 1.27-2.54 microns), is recommended for high-reliability applications that require frequent insertion and removal of components, such as connectors and edge card contacts. Thick gold offers superior wear resistance, contact reliability, and long-term stability in demanding environments. -
Q: Can thick gold plating affect the solderability of a PCB?
A: Yes, thick gold plating can sometimes pose challenges for solderability. If the gold layer is too thick, it may not fully dissolve during the soldering process, potentially leading to weak or unreliable connections. Proper process control and optimization are essential to mitigate this risk and ensure good solderability. -
Q: How does the cost of thick gold PCBs compare to thinner gold options?
A: Thick gold PCBs are generally more expensive than thinner gold options due to the increased amount of gold used in the plating process. The cost difference can be significant, especially for large-scale production runs. Balancing the required performance with budget constraints is crucial when considering thick gold PCBs. -
Q: Are there any specific design considerations for thick gold PCBs?
A: Yes, when designing a PCB with thick gold plating, it is important to consider the specific requirements of the components and ensure compatibility with the chosen gold thickness. Proper layout and design practices should be followed to optimize performance and reliability. Additionally, designers should work closely with the PCB manufacturer to ensure the manufacturing process is optimized for the selected gold thickness.