How PCB Contract Manufacturing Works
The process of contracting out PCB manufacturing typically involves the following steps:
-
Design: The client company designs the circuit board, specifying the layout, components, and materials. They provide the contract manufacturer with the PCB design files, bill of materials, and other specifications.
-
Prototyping: The contract manufacturer may first produce a prototype or small batch of boards for testing and validation. This allows the design to be checked for any issues before mass production.
-
Fabrication: Once the design is finalized, the contract manufacturer fabricates the PCBs. This involves creating the copper traces, drilling holes, applying solder mask, silkscreening, and other processes to build the bare board.
-
Component Sourcing: If the service includes PCB assembly, the contract manufacturer sources all the necessary components, such as resistors, capacitors, ICs, and connectors. They may handle the entire supply chain.
-
Assembly: The components are then soldered onto the fabricated PCB, either through automated SMT (surface mount technology) machines or manual assembly for THT (through-hole technology) components. The assembled board is cleaned and inspected.
-
Testing: The assembled PCBs undergo various electrical tests to ensure they function properly and meet the client’s specifications. This may include in-circuit testing, boundary scan, functional testing, and burn-in.
-
Packaging and Shipping: The finished and tested PCB assemblies are packaged and shipped to the client or their specified destination. The contract manufacturer may also handle logistics, such as drop shipping to end customers.
Throughout this process, the contract manufacturer and client work closely together, with regular communication to ensure the project is on track and meets requirements. Many PCB contract manufacturing services are highly automated with robotic assembly lines, automated optical inspection (AOI), and data-driven process control to ensure consistent quality and efficiency.
Benefits of Using a PCB Contract Manufacturer
There are several key advantages to outsourcing PCB fabrication and assembly to a contract manufacturing service:
Cost Savings
Establishing an in-house PCB production line requires significant upfront investment in equipment, facilities, and skilled personnel. For most companies, it is more cost-effective to leverage the economies of scale and existing infrastructure of a contract manufacturer. PCB contract manufacturing services can offer competitive pricing due to their high volumes and streamlined operations.
Focus on Core Competencies
By outsourcing PCB manufacturing, companies can focus their resources and efforts on their core competencies, such as product design, marketing, and sales. They don’t need to worry about the complexities and challenges of PCB fabrication and can instead concentrate on innovation and growing their business.
Access to Expertise and Technology
pcb contract manufacturers specialize in fabricating and assembling circuit boards. They have the expertise, experience, and advanced technology to produce high-quality PCBs efficiently and reliably. They invest in the latest equipment and continuously train their staff to stay up-to-date with industry best practices and standards.
Scalability and Flexibility
Outsourcing to a contract manufacturer provides greater scalability and flexibility compared to in-house production. The CM service can quickly ramp up or down production based on demand, without the client needing to worry about capacity constraints or idle equipment. This is especially beneficial for companies with fluctuating or unpredictable demand.
Faster Time-to-Market
Contract manufacturers often have streamlined processes and can fabricate PCBs faster than in-house production. They may also offer expedited services and can handle the entire process from design to assembly to shipping, reducing overall lead times. This allows companies to bring their products to market faster.
Quality Assurance
Reputable PCB contract manufacturing services have strict quality control measures in place to ensure consistent and reliable PCBs. They follow industry standards such as IPC and ISO, and may have certifications for specific industries such as automotive, medical, or aerospace. They use advanced inspection and testing equipment to catch any defects or issues.
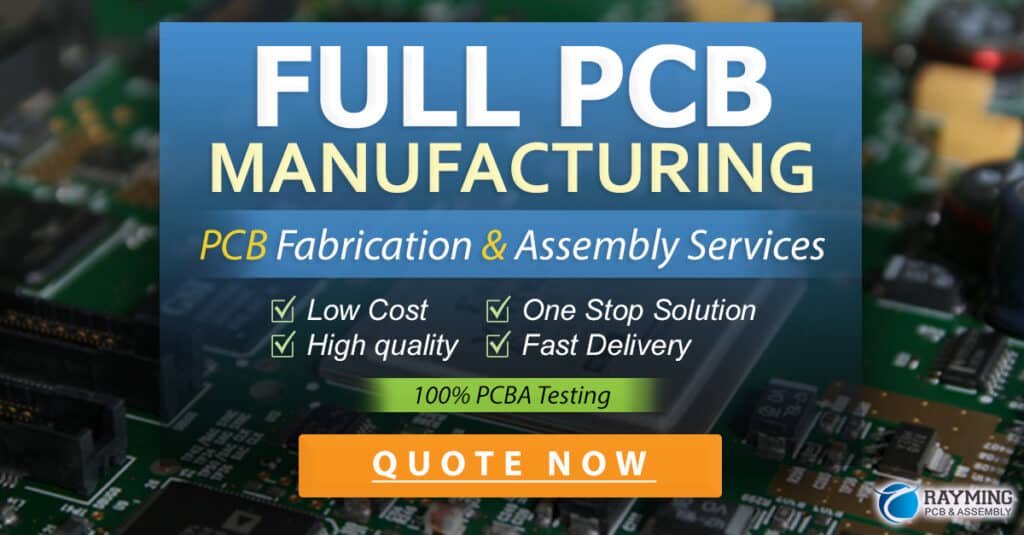
Choosing a PCB Contract Manufacturer
When selecting a PCB contract manufacturing service, there are several key factors to consider:
Factor | Description |
---|---|
Capabilities | Can they handle the complexity and volume of your PCB designs? Do they offer both prototype and mass production services? |
Quality | Do they have a robust quality management system and hold relevant certifications? What is their track record for reliability and defect rates? |
Experience | How long have they been in business? Do they have experience with PCBs similar to yours or in your industry? |
Technology | Do they have advanced equipment for fabrication, assembly, and testing? Can they handle the latest PCB technologies and components? |
Turnaround Time | What are their standard lead times for prototypes and production? Do they offer expedited services if needed? |
Cost | Are their prices competitive? Do they offer volume discounts? What is included in their pricing (e.g. testing, shipping)? |
Communication | Do they have a responsive and proactive communication style? Will you have a dedicated account manager? |
Location | Where are they located? Do they have multiple facilities for redundancy? What are the logistics and shipping options? |
It’s important to thoroughly vet potential contract manufacturers and not just choose based on the lowest price. Quality, reliability, and a good working relationship are crucial for a successful outsourcing partnership.
PCB Manufacturing Capabilities
PCB contract manufacturing services offer a wide range of capabilities to meet the needs of different industries and applications. Some key capabilities include:
PCB Fabrication
- Multilayer PCBs (up to 40+ layers)
- High-density interconnect (HDI) PCBs
- Flexible and rigid-flex PCBs
- Metal core PCBs
- RF and high-frequency PCBs
- Thick copper pcbs
- controlled impedance pcbs
PCB Assembly
- Surface mount technology (SMT)
- Through-hole technology (THT)
- Mixed technology (SMT/THT)
- Ball grid array (BGA)
- Chip on board (COB)
- Pin in paste
- Press-fit
- Conformal coating
- Potting and encapsulation
Special Materials and Finishes
- FR-4, Rogers, Teflon, polyimide, etc.
- ENIG, ENEPIG, HASL, OSP, immersion silver/tin, etc.
- Soldermask colors
- Carbon ink, peelable mask, etc.
Testing and Inspection
- In-circuit testing (ICT)
- Flying probe testing
- Boundary scan testing
- Functional circuit testing
- Burn-in testing
- X-ray inspection
- Automated optical inspection (AOI)
- 3D automated x-ray inspection (AXI)
The specific capabilities offered will vary by contract manufacturer. Some may specialize in certain types of PCBs or cater to specific industries, while others offer a broader range of general services. It’s important to choose a CM that has the right capabilities and experience for your project needs.
Industry Standards and Certifications
The PCB manufacturing industry is governed by various standards and certifications to ensure quality, reliability, and consistency. Some key standards include:
-
IPC (Association Connecting Electronics Industries): IPC is the main standards organization for the PCB and electronics assembly industries. They publish standards such as IPC-A-610 for acceptability of electronic assemblies, IPC-6012 for qualification and performance of rigid PCBs, and J-STD-001 for soldering.
-
ISO (International Organization for Standardization): Many PCB contract manufacturers are certified to ISO 9001 for quality management systems. Some may also hold industry-specific certifications like ISO 13485 for medical devices or ISO/TS 16949 for automotive.
-
UL (Underwriters Laboratories): UL is a global safety certification company that tests and certifies products, including PCBs and assemblies. They have standards for safety, flammability, and electrical performance.
-
RoHS (Restriction of Hazardous Substances): RoHS is a directive that restricts the use of certain hazardous substances in electrical and electronic products. Many PCB manufacturers offer RoHS-compliant processes and materials.
When choosing a contract manufacturer, it’s important to verify their certifications and compliance with relevant industry standards. This ensures they follow best practices and can meet the quality and reliability requirements of your project.
PCB Design Considerations for Manufacturing
To ensure a smooth and successful manufacturing process, it’s important to design your PCB with manufacturability in mind. Some key design considerations include:
-
Design for Manufacturing (DFM): Follow DFM guidelines to ensure your PCB can be efficiently and reliably manufactured. This includes considerations for minimum trace/space widths, hole sizes, annular rings, soldermask clearances, and more.
-
Component Selection: Choose components that are readily available and have standard packaging. Avoid obsolete or hard-to-find components that could cause delays or issues in manufacturing.
-
Panelization: Design your PCB to be efficiently panelized for fabrication. This involves grouping multiple copies of the board onto a larger panel with tooling holes, fiducials, and breakaway tabs.
-
Testability: Include test points and other features that allow the assembled board to be easily tested. This can include vias for bed-of-nails testing, test pads for flying probe, or boundary scan architecture.
-
Thermal Management: Consider the thermal requirements of your PCB and include features for heat dissipation, such as thermal vias, heatsinks, or metal core substrates.
-
Signal Integrity: For high-speed or RF designs, pay attention to signal integrity issues such as impedance control, crosstalk, and EMI. Use proper layout techniques and materials to ensure good signal quality.
-
Documentation: Provide clear and complete documentation to the contract manufacturer, including the bill of materials (BOM), Gerber files, assembly drawings, and any special instructions or requirements.
By designing with manufacturing in mind and communicating closely with your contract manufacturer, you can avoid potential issues and delays in the production process.
Frequently Asked Questions (FAQ)
1. What is the typical lead time for PCB manufacturing?
Lead times can vary depending on the complexity of the PCB, the volume, and the specific manufacturer. In general, prototype PCBs can be fabricated and assembled in 1-2 weeks, while production lead times are typically 3-6 weeks. However, expedited services may be available for faster turnaround.
2. How much does PCB contract manufacturing cost?
The cost of PCB contract manufacturing depends on several factors, including the size and complexity of the board, the quantity, the materials, and the specific services required (e.g. assembly, testing). In general, higher volumes will have lower per-unit costs due to economies of scale. It’s best to get quotes from multiple contract manufacturers based on your specific project requirements.
3. What files or information do I need to provide to the contract manufacturer?
To get started with PCB manufacturing, you typically need to provide:
– Bill of Materials (BOM): A list of all components used on the PCB, including part numbers, quantities, and reference designators.
– Gerber Files: The industry-standard format for PCB design data, including the copper layers, solder mask, silkscreen, and drill files.
– Assembly Drawings: Illustrations showing the component placement, orientation, and any special assembly instructions.
– Fabrication Drawings: Mechanical drawings specifying the PCB dimensions, materials, finishes, and any special requirements.
– Special Instructions: Any additional notes or requirements for the manufacturing process, such as testing, packaging, or shipping instructions.
4. Can PCB contract manufacturers handle both prototype and production quantities?
Yes, most PCB contract manufacturing services offer both prototype and mass production capabilities. Prototyping services are typically more flexible and can handle smaller quantities (e.g. 1-100 boards), while production services are geared towards higher volumes (100+ boards). Some manufacturers may have different processes or pricing structures for prototype vs. production.
5. How do I ensure the quality and reliability of my PCBs?
To ensure quality and reliability, choose a reputable PCB contract manufacturer that has a robust quality management system and holds relevant industry certifications (e.g. ISO 9001, IPC). Communicate your quality requirements clearly and work closely with the manufacturer throughout the process. You can also specify additional testing and inspection requirements, such as 100% electrical testing, X-ray inspection, or burn-in testing. Regularly audit and monitor the manufacturer’s performance and address any issues promptly.
Conclusion
PCB contract manufacturing services provide a cost-effective and efficient way for companies to outsource their PCB fabrication and assembly needs. By leveraging the expertise, technology, and scale of a specialized manufacturer, companies can focus on their core competencies while ensuring high-quality and reliable PCBs. When choosing a contract manufacturer, it’s important to consider factors such as capabilities, quality, experience, and communication. By designing for manufacturability and working closely with the manufacturer, companies can bring their electronic products to market faster and more successfully.