What is ENIG?
ENIG is a chemical process that deposits a thin layer of nickel and gold onto the copper pads and traces of a PCB. The process involves several steps:
- Cleaning: The PCB is thoroughly cleaned to remove any contaminants or oxidation.
- Microetching: The copper surface is slightly etched to improve adhesion.
- Electroless nickel plating: A thin layer of nickel (3-6 µm) is deposited onto the copper using an autocatalytic chemical reaction.
- Immersion gold plating: A thin layer of gold (0.05-0.2 µm) is deposited onto the nickel using a displacement reaction.
The resulting ENIG surface finish provides a flat, solderable, and corrosion-resistant surface for component assembly.
Advantages of ENIG
ENIG offers several advantages over other surface finishes:
- Excellent solderability: The gold layer provides a clean, oxide-free surface that promotes good wetting and strong solder joints.
- Flatness: The thin nickel and gold layers maintain the flatness of the copper pads, which is essential for fine-pitch components and high-density designs.
- Durability: The nickel layer acts as a barrier to prevent copper diffusion and provides good wear resistance.
- Corrosion resistance: The gold layer protects the underlying nickel and copper from oxidation and corrosion.
- Wire bonding compatibility: The gold surface is suitable for wire bonding in certain applications.
- Extended shelf life: ENIG-finished PCBs can be stored for longer periods without degradation compared to other finishes.
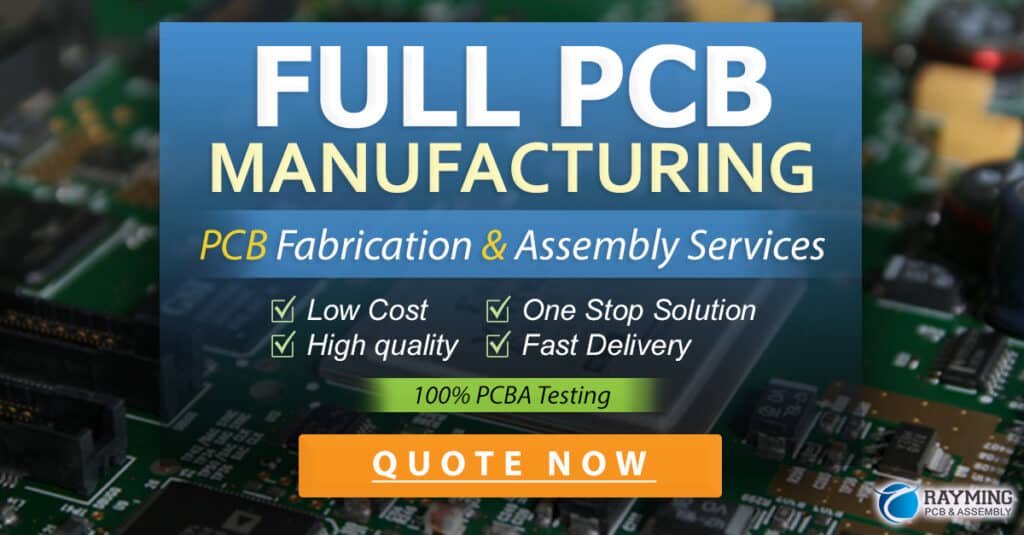
Applications of ENIG
ENIG is widely used in various industries and applications, including:
- Consumer electronics: Smartphones, tablets, laptops, and wearables.
- Automotive electronics: Engine control units, infotainment systems, and sensors.
- Medical devices: Implantable devices, diagnostic equipment, and wearable health monitors.
- Aerospace and defense: Avionics, communication systems, and military equipment.
- Industrial automation: Programmable logic controllers, sensors, and actuators.
- IoT devices: Smart home appliances, security systems, and environmental monitors.
ENIG vs. Other Surface Finishes
ENIG is one of several surface finishes used in the PCB industry. Let’s compare ENIG with some other popular finishes:
ENIG vs. HASL (Hot Air Solder Leveling)
Characteristic | ENIG | HASL |
---|---|---|
Solderability | Excellent | Good |
Flatness | Excellent | Poor |
Durability | Excellent | Good |
Cost | High | Low |
HASL is a low-cost finish that involves dipping the PCB in molten solder and leveling the excess solder with hot air. While HASL provides good solderability, it results in a less flat surface and is not suitable for fine-pitch components. ENIG, on the other hand, offers excellent flatness and solderability at a higher cost.
ENIG vs. OSP (Organic Solderability Preservative)
Characteristic | ENIG | OSP |
---|---|---|
Solderability | Excellent | Good |
Flatness | Excellent | Excellent |
Durability | Excellent | Poor |
Cost | High | Low |
OSP is a low-cost, organic coating that preserves the solderability of the copper surface. It provides excellent flatness but has limited durability and a shorter shelf life compared to ENIG. OSP is suitable for quick-turn prototypes and low-cost production, while ENIG is preferred for high-reliability applications.
ENIG vs. Immersion Tin
Characteristic | ENIG | Immersion Tin |
---|---|---|
Solderability | Excellent | Good |
Flatness | Excellent | Excellent |
Durability | Excellent | Good |
Cost | High | Moderate |
Immersion tin is a chemical process that deposits a thin layer of tin onto the copper surface. It offers good solderability, flatness, and moderate durability at a lower cost than ENIG. However, immersion tin is prone to whisker growth, which can cause short circuits in certain environmental conditions. ENIG is preferred for applications that require high reliability and long-term stability.
ENIG Process Considerations
To ensure the quality and reliability of ENIG-finished PCBs, several process considerations must be addressed:
- Surface preparation: The copper surface must be thoroughly cleaned and microetched to promote adhesion and ensure a uniform nickel deposition.
- Nickel thickness: The nickel layer should be thick enough (3-6 µm) to provide a barrier against copper diffusion and maintain flatness, but not too thick to cause brittleness or stress.
- Gold thickness: The gold layer should be thin enough (0.05-0.2 µm) to minimize cost while providing adequate protection against oxidation and corrosion.
- Contamination control: The plating solutions must be regularly monitored and maintained to prevent contamination and ensure consistent performance.
- Thermal shock resistance: ENIG-finished PCBs should be tested for thermal shock resistance to ensure the integrity of the solder joints under temperature cycling conditions.
By carefully controlling these process parameters, PCB manufacturers can produce high-quality ENIG-finished boards that meet the demanding requirements of various industries.
FAQ
-
Q: What is the typical thickness of the nickel and gold layers in ENIG?
A: The typical thickness of the nickel layer is 3-6 µm, while the gold layer is 0.05-0.2 µm. -
Q: Can ENIG be used for wire bonding?
A: Yes, the gold surface of ENIG is suitable for wire bonding in certain applications, such as semiconductor packaging. -
Q: Is ENIG suitable for high-frequency PCBs?
A: Yes, ENIG provides a smooth, flat surface that minimizes signal loss and is suitable for high-frequency applications. -
Q: How does ENIG compare to ENEPIG (Electroless Nickel Electroless Palladium Immersion Gold)?
A: ENEPIG is a similar surface finish that includes an additional palladium layer between the nickel and gold layers. ENEPIG offers better wire bonding performance and higher corrosion resistance than ENIG but at a higher cost. -
Q: Can ENIG be used for lead-free soldering?
A: Yes, ENIG is compatible with lead-free soldering processes and provides excellent solderability for lead-free solder alloys.
In conclusion, ENIG is a versatile and reliable surface finish that offers excellent solderability, flatness, and durability for a wide range of PCB applications. By understanding the characteristics, advantages, and process considerations of ENIG, PCB designers and manufacturers can make informed decisions when selecting the most appropriate surface finish for their products.