Understanding Prepreg in PCB Manufacturing
What is Prepreg?
Prepreg, short for pre-impregnated, is a composite material used in the manufacturing of PCBs. It consists of a reinforcement fabric, typically made of glass fibers, that is pre-impregnated with a partially cured thermosetting resin, such as epoxy or polyimide. The resin is in a semi-solid state, allowing it to be pliable and easy to work with during the PCB fabrication process.
Composition of Prepreg
The composition of prepreg plays a crucial role in determining its properties and suitability for various PCB applications. The primary components of prepreg are:
- Reinforcement Fabric:
- Glass fibers (E-glass or S-glass)
- Aramid fibers (Kevlar)
-
Quartz fibers
-
Thermosetting Resin:
- Epoxy resin
- Polyimide resin
- Bismaleimide-triazine (BT) resin
The choice of reinforcement fabric and resin depends on the specific requirements of the PCB, such as thermal stability, mechanical strength, and dielectric properties.
Properties of Prepreg
Prepreg exhibits several desirable properties that make it an ideal material for PCB manufacturing:
-
Dimensional Stability: Prepreg maintains its shape and size during the lamination process, ensuring precise alignment of layers in multi-layer PCBs.
-
Mechanical Strength: The reinforcement fabric in prepreg provides excellent mechanical strength and rigidity to the PCB, enhancing its durability and resistance to physical stress.
-
Thermal Stability: Prepreg offers good thermal stability, allowing PCBs to withstand high temperatures during soldering and operation.
-
Electrical Insulation: The resin in prepreg acts as an electrical insulator, preventing short circuits and ensuring proper signal integrity.
-
Adhesion: Prepreg exhibits strong adhesion properties, enabling secure bonding between layers in multi-layer PCBs.
Role of Prepreg in PCB Fabrication
Lamination Process
Prepreg plays a vital role in the lamination process of PCB fabrication. The lamination process involves stacking multiple layers of prepreg and copper foil to create a multi-layer PCB. The steps involved in the lamination process are:
-
Layer Stacking: Alternating layers of prepreg and copper foil are stacked in a specific order, depending on the PCB design.
-
Lamination: The stacked layers are placed in a lamination press, where heat and pressure are applied. The heat causes the resin in the prepreg to flow and cure, bonding the layers together.
-
Cooling: After lamination, the PCB is cooled to room temperature, allowing the resin to fully cure and solidify.
The use of prepreg in the lamination process ensures a strong and uniform bond between the layers, resulting in a reliable and high-quality PCB.
Insulation and Dielectric Properties
Prepreg serves as an insulating material in PCBs, providing electrical isolation between conductive layers. The dielectric properties of prepreg are critical in determining the signal integrity and performance of the PCB. The dielectric constant (Dk) and dissipation factor (Df) are two key parameters that characterize the dielectric properties of prepreg.
Prepreg Type | Dielectric Constant (Dk) | Dissipation Factor (Df) |
---|---|---|
FR-4 | 4.2 – 4.5 | 0.02 – 0.03 |
High Tg FR-4 | 4.2 – 4.5 | 0.01 – 0.02 |
Polyimide | 3.5 – 3.8 | 0.002 – 0.01 |
BT | 3.8 – 4.2 | 0.01 – 0.02 |
The choice of prepreg with appropriate dielectric properties depends on the frequency, signal speed, and loss requirements of the PCB application.
Thickness Control
Prepreg plays a crucial role in controlling the thickness of PCBs. The thickness of a PCB is determined by the number of layers and the thickness of each layer, including the prepreg. Prepreg is available in various thicknesses, typically ranging from 0.05mm to 0.25mm, allowing for precise control over the final PCB thickness.
Prepreg Thickness (mm) | Typical Applications |
---|---|
0.05 – 0.08 | High-density interconnect (HDI) PCBs |
0.1 – 0.15 | Multi-layer PCBs for general applications |
0.2 – 0.25 | Thick multi-layer PCBs for power electronics |
The selection of prepreg thickness depends on the desired PCB thickness, layer count, and the specific application requirements.
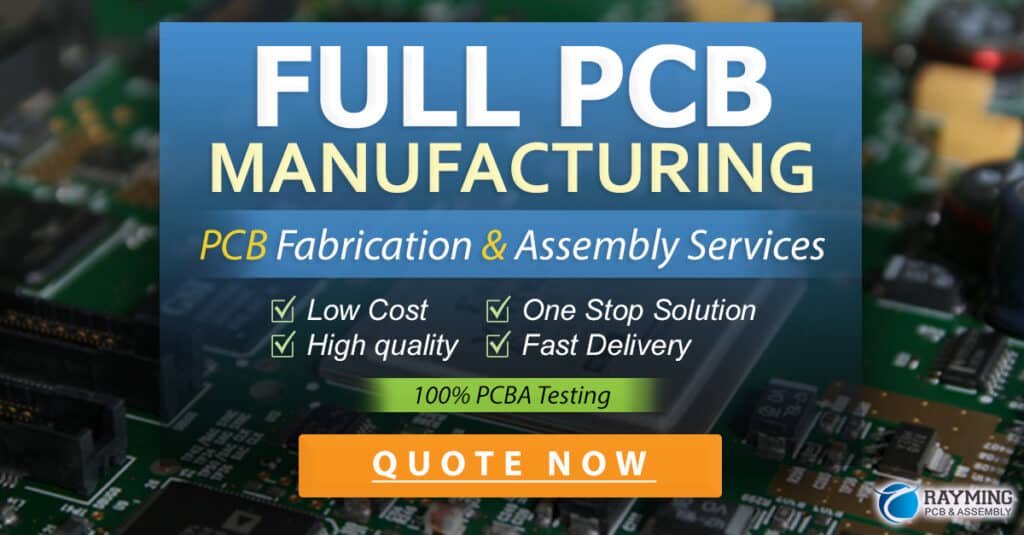
Prepreg Selection Considerations
When selecting prepreg for PCB manufacturing, several factors need to be considered to ensure optimal performance and reliability:
Glass Transition Temperature (Tg)
The glass transition temperature (Tg) is a critical parameter that determines the thermal stability of the prepreg. It is the temperature at which the prepreg transitions from a rigid, glassy state to a soft, rubbery state. PCBs exposed to high temperatures during soldering or operation require prepreg with a high Tg to maintain their structural integrity.
Prepreg Type | Glass Transition Temperature (Tg) |
---|---|
Standard FR-4 | 130°C – 140°C |
High Tg FR-4 | 170°C – 180°C |
Polyimide | 250°C – 300°C |
BT | 180°C – 220°C |
Resin Content
The resin content of prepreg refers to the percentage of resin by weight in the material. It affects the flow characteristics, adhesion strength, and dielectric properties of the prepreg. Higher resin content generally results in better flow and adhesion but may compromise the dimensional stability and dielectric properties.
Resin Content | Characteristics |
---|---|
Low (30-40%) | Better dimensional stability, lower flow |
Medium (40-50%) | Balanced properties, suitable for most applications |
High (50-60%) | Better flow and adhesion, lower dimensional stability |
The choice of resin content depends on the specific requirements of the PCB, such as layer count, copper thickness, and desired electrical properties.
Reinforcement Fabric
The reinforcement fabric in prepreg provides mechanical strength and dimensional stability to the PCB. The most common reinforcement fabrics used in prepreg are:
- E-glass: Cost-effective and widely used in general-purpose PCBs.
- S-glass: Higher strength and thermal stability compared to E-glass, used in high-performance PCBs.
- Aramid (Kevlar): Offers excellent mechanical strength and toughness, used in specialized applications.
- Quartz: Provides low dielectric constant and dissipation factor, used in high-frequency applications.
The selection of reinforcement fabric depends on the mechanical, thermal, and electrical requirements of the PCB.
Prepreg Storage and Handling
Proper storage and handling of prepreg are essential to maintain its quality and performance. Prepreg is sensitive to temperature, humidity, and light exposure, which can affect its properties and shelf life.
Storage Conditions
Prepreg should be stored in a controlled environment with the following conditions:
- Temperature: 5°C to 25°C (41°F to 77°F)
- Relative Humidity: 30% to 50%
- Light Exposure: Minimized or avoided
Prepreg should be stored in sealed, moisture-barrier bags to prevent moisture absorption and contamination.
Shelf Life
The shelf life of prepreg depends on the storage conditions and the specific resin system used. Typically, the shelf life of prepreg ranges from 6 months to 12 months when stored under recommended conditions. It is essential to use prepreg within its shelf life to ensure optimal performance and reliability.
Handling Precautions
When handling prepreg, the following precautions should be taken:
- Wear clean, lint-free gloves to prevent contamination.
- Handle prepreg in a clean, dust-free environment.
- Avoid exposing prepreg to moisture, high temperatures, or direct sunlight.
- Cut prepreg using sharp, clean tools to prevent fraying or delamination.
Proper handling of prepreg minimizes the risk of defects and ensures consistent quality in the PCB manufacturing process.
Frequently Asked Questions (FAQ)
- What is the difference between prepreg and core material in PCBs?
-
Prepreg is a composite material consisting of reinforcement fabric pre-impregnated with a partially cured resin, used for bonding layers in multi-layer PCBs. Core material, also known as copper-clad laminate (CCL), is a fully cured material with copper foil laminated on one or both sides, used as the base substrate for PCBs.
-
Can prepreg be used for single-layer PCBs?
-
Prepreg is primarily used in multi-layer PCBs to bond layers together. While it can be used in single-layer PCBs as a base substrate, it is not a common practice. Single-layer PCBs typically use copper-clad laminates (CCL) as the base material.
-
What is the purpose of the reinforcement fabric in prepreg?
-
The reinforcement fabric in prepreg provides mechanical strength, dimensional stability, and improved thermal properties to the PCB. It helps in maintaining the structural integrity of the PCB during manufacturing and operation.
-
How does the resin content of prepreg affect PCB performance?
-
The resin content of prepreg affects its flow characteristics, adhesion strength, and dielectric properties. Higher resin content improves flow and adhesion but may compromise dimensional stability and dielectric properties. The choice of resin content depends on the specific requirements of the PCB, such as layer count, copper thickness, and desired electrical properties.
-
Can prepreg be stored at room temperature?
- While prepreg can be stored at room temperature for a short period, it is recommended to store it in a controlled environment with a temperature range of 5°C to 25°C (41°F to 77°F) and a relative humidity of 30% to 50%. Storing prepreg under recommended conditions helps maintain its quality and extends its shelf life.
Conclusion
Prepreg is a vital material in the manufacturing of high-quality and reliable PCBs. Its role in the lamination process, insulation, and thickness control makes it an indispensable component in PCB fabrication. The selection of prepreg with appropriate properties, such as glass transition temperature, resin content, and reinforcement fabric, is crucial in meeting the specific requirements of PCB applications.
Proper storage and handling of prepreg are equally important to maintain its quality and performance. By understanding the characteristics and applications of prepreg, PCB manufacturers can optimize their processes and ensure the production of high-quality PCBs that meet the demands of modern electronics.
As technology advances and the complexity of electronic systems increases, the use of prepreg in PCB manufacturing will continue to evolve. Innovations in prepreg materials and processing techniques will enable the development of advanced PCBs with enhanced performance, reliability, and functionality.