Introduction to Solder Mask
Solder mask, also known as solder resist or solder stop mask, is a thin lacquer-like layer of polymer usually applied to the copper traces of a printed circuit board (PCB) for protection against oxidation and to prevent solder bridges from forming between closely spaced solder pads. Solder mask is typically applied to both sides of a PCB, covering all areas except the pads and lands intended for soldering components.
The primary functions of solder mask in PCB include:
-
Preventing solder bridges: Solder mask keeps molten solder from bridging between conductors, causing short circuits.
-
Protection against oxidation: Solder mask protects the copper traces from oxidation, ensuring better solderability and a longer lifespan for the PCB.
-
Insulation: Solder mask provides electrical insulation between conductive parts, preventing unintended connections.
-
Improving aesthetics: Solder mask gives the PCB a clean, professional appearance and can be used to add labels, logos, or other markings.
Common Solder Mask Colors
Solder mask is available in various colors, with green being the most common. Other popular colors include:
- Blue
- Red
- Yellow
- Black
- White
- Purple
The choice of color is primarily a matter of preference, but it can also serve functional purposes. For example, white solder mask is often used for LED lighting applications, as it reflects light better than darker colors.
Solder Mask Application Process
The solder mask application process typically involves the following steps:
-
Cleaning: The PCB is thoroughly cleaned to remove any contaminants that may affect the adhesion of the solder mask.
-
Solder mask application: The liquid solder mask is applied to the PCB using various methods, such as screen printing, spraying, or curtain coating.
-
Pre-baking: The PCB is pre-baked to partially cure the solder mask and remove any solvents.
-
Exposure: The solder mask is exposed to UV light through a photomask, hardening the exposed areas.
-
Developing: The unexposed areas of the solder mask are removed using a developer solution.
-
Final curing: The PCB is baked at a high temperature to fully cure the solder mask and ensure optimal mechanical and chemical properties.
Solder Mask Application Methods
Several methods can be used to apply solder mask to a PCB:
-
Screen printing: A stencil is used to apply the solder mask to the PCB. This method is suitable for high-volume production and provides good thickness control.
-
Spraying: The solder mask is sprayed onto the PCB using a spray gun. This method is more flexible than screen printing but may result in a less uniform coating.
-
Curtain coating: The PCB is passed through a curtain of solder mask, coating both sides simultaneously. This method is fast and efficient but may not be suitable for boards with high component density.
-
Dry film: A dry film solder mask is laminated onto the PCB and then exposed and developed like a photoresist. This method provides excellent resolution and is suitable for fine-pitch components.
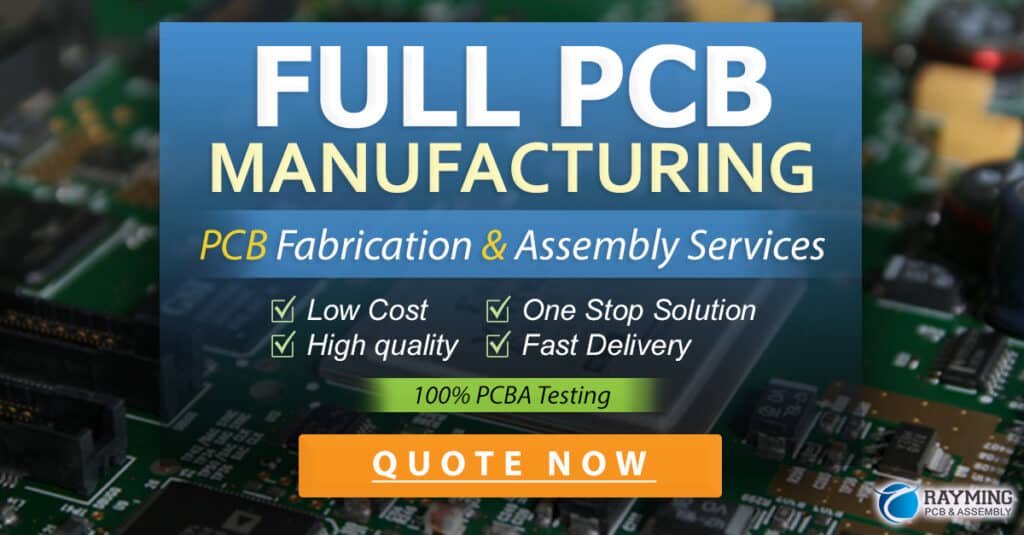
Solder Mask Properties and Specifications
When selecting a solder mask for a PCB, several properties and specifications should be considered:
-
Dielectric strength: The ability of the solder mask to withstand high voltages without breaking down.
-
Insulation resistance: The resistance of the solder mask to electrical current flow.
-
Flammability: The resistance of the solder mask to ignition and flame spread.
-
Thermal shock resistance: The ability of the solder mask to withstand rapid temperature changes without cracking or delaminating.
-
Chemical resistance: The resistance of the solder mask to chemicals commonly used in PCB manufacturing and assembly, such as flux and cleaning agents.
-
Hardness: The resistance of the solder mask to abrasion and scratching.
-
Adhesion: The ability of the solder mask to adhere to the PCB substrate and copper traces.
-
Thickness: The thickness of the solder mask layer, typically ranging from 0.5 to 2 mils (12.7 to 50.8 μm).
Solder Mask Standards and Specifications
Several industry standards and specifications provide guidelines for solder mask properties and performance:
-
IPC-SM-840E: This standard defines the requirements for solder mask performance, including adhesion, insulation resistance, and chemical resistance.
-
UL 94: This standard classifies the flammability of solder mask materials.
-
IPC-4781: This specification provides guidelines for the qualification and performance of liquid photoimageable solder masks.
-
MIL-PRF-31032: This military specification defines the requirements for solder mask performance in high-reliability applications.
Solder Mask Design Considerations
When designing a PCB with solder mask, several factors should be considered to ensure optimal performance and manufacturability:
-
Solder mask clearance: The distance between the edge of a pad or trace and the solder mask opening. Adequate clearance is necessary to prevent solder mask from encroaching on the pad and interfering with soldering.
-
Solder mask expansion: The amount by which the solder mask opening is larger than the pad or trace. Expansion is necessary to accommodate the tolerances of the solder mask application process and ensure that the entire pad is exposed for soldering.
-
Solder mask registration: The alignment of the solder mask openings with the pads and traces on the PCB. Proper registration is critical for ensuring that all pads are fully exposed and that there are no solder mask bridges between pads.
-
Solder mask sliver: A thin strip of solder mask between two closely spaced pads or traces. Slivers can be difficult to manufacture consistently and may break off during assembly, causing short circuits.
-
Solder mask dam: A ring of solder mask around a through-hole pad that prevents solder from flowing away from the hole during wave soldering.
Solder Mask Clearance and Expansion
The table below provides general guidelines for solder mask clearance and expansion based on the pad size:
Pad Size (mm) | Clearance (mm) | Expansion (mm) |
---|---|---|
< 0.5 | 0.05 | 0.025 |
0.5 – 1.0 | 0.1 | 0.05 |
1.0 – 2.0 | 0.15 | 0.075 |
> 2.0 | 0.2 | 0.1 |
Solder Mask Sliver and Dam
To prevent solder mask slivers, the minimum distance between pads or traces should be at least twice the solder mask clearance plus the minimum solder mask web width (typically 0.1 to 0.15 mm).
Solder mask dams should be at least 0.25 mm wide and extend at least 0.5 mm beyond the edge of the pad to ensure adequate solder retention during wave soldering.
Solder Mask Defects and Quality Control
Several types of defects can occur during the solder mask application process, affecting the performance and reliability of the PCB:
-
Pinholes: Small holes in the solder mask that expose the underlying copper, making it susceptible to oxidation and short circuits.
-
Bubbles: Air bubbles trapped in the solder mask, which can lead to pinholes or delamination during assembly.
-
Solder mask bridges: Solder mask that accidentally covers a portion of a pad or trace, preventing proper soldering.
-
Misregistration: Misalignment between the solder mask openings and the pads or traces, resulting in partially exposed or covered pads.
-
Insufficient cure: Solder mask that is not fully cured, leading to poor adhesion, chemical resistance, or mechanical properties.
To ensure the quality of the solder mask, several inspection and testing methods can be used:
-
Visual inspection: Checking the PCB for visible defects such as pinholes, bubbles, or misregistration.
-
Microscopic inspection: Using a microscope to examine the solder mask for smaller defects or measure the clearance and expansion.
-
Thickness measurement: Using a thickness gauge or micrometer to ensure that the solder mask meets the specified thickness requirements.
-
Adhesion testing: Performing a tape test or cross-hatch test to evaluate the adhesion of the solder mask to the PCB substrate and copper traces.
-
Insulation resistance testing: Measuring the resistance between adjacent pads or traces to ensure that the solder mask provides adequate insulation.
-
Chemical resistance testing: Exposing the PCB to various chemicals to assess the solder mask’s resistance to degradation.
FAQ
-
What is the difference between solder mask and conformal coating?
Solder mask is applied to the PCB before assembly to protect the copper traces and prevent solder bridges, while conformal coating is applied after assembly to protect the components and PCB from environmental factors like moisture, dust, and chemicals. -
Can solder mask be removed?
Yes, solder mask can be removed using abrasive methods like sanding or chemical methods like using a solder mask stripper. However, removing solder mask can damage the underlying copper traces and should only be done when necessary, such as for rework or repair. -
What is the typical thickness of solder mask?
The typical thickness of solder mask ranges from 0.5 to 2 mils (12.7 to 50.8 μm), with 1 mil (25.4 μm) being a common default thickness. The specific thickness required depends on the PCB design, application, and solder mask material. -
Can solder mask be used as a substitute for conformal coating?
While solder mask provides some protection against environmental factors, it is not a substitute for conformal coating. Conformal coating is specifically designed to protect the PCB and components from moisture, dust, chemicals, and other contaminants, and is applied after assembly. -
How does solder mask affect the impedance of a PCB?
Solder mask can affect the impedance of a PCB by altering the dielectric constant of the substrate. The thickness and dielectric properties of the solder mask material must be considered when calculating the impedance of controlled impedance traces. In some cases, a thicker or higher dielectric constant solder mask may be used to achieve the desired impedance.
Conclusion
Solder mask is a critical component of PCB manufacturing, providing protection against oxidation, solder bridges, and environmental factors while improving the aesthetics and functionality of the board. By understanding the properties, application methods, design considerations, and quality control aspects of solder mask, PCB designers and manufacturers can ensure the production of high-quality, reliable boards that meet the needs of their customers. As PCB technology continues to advance, the development of new solder mask materials and processes will play a crucial role in enabling the next generation of electronic devices.