Introduction to rf pcb Design
Designing a radio frequency (RF) printed circuit board (PCB) requires careful consideration of various factors to ensure optimal performance and minimize signal interference. RF PCB design involves dealing with high-frequency signals, which are more sensitive to noise, impedance mismatches, and signal integrity issues compared to low-frequency designs. In this article, we will delve into the key aspects of RF PCB design, providing guidelines and best practices to help you create a successful RF PCB.
Understanding the Basics of RF PCB Design
What is an RF PCB?
An RF PCB is a specialized printed circuit board designed to handle high-frequency signals, typically in the range of megahertz (MHz) to gigahertz (GHz). These PCBs are used in various applications, such as wireless communication devices, radar systems, and high-speed digital circuits.
Key Characteristics of RF PCBs
RF PCBs have distinct characteristics that set them apart from standard PCBs:
- Higher operating frequencies
- Stringent impedance control requirements
- Increased sensitivity to noise and interference
- Need for specialized materials and manufacturing techniques
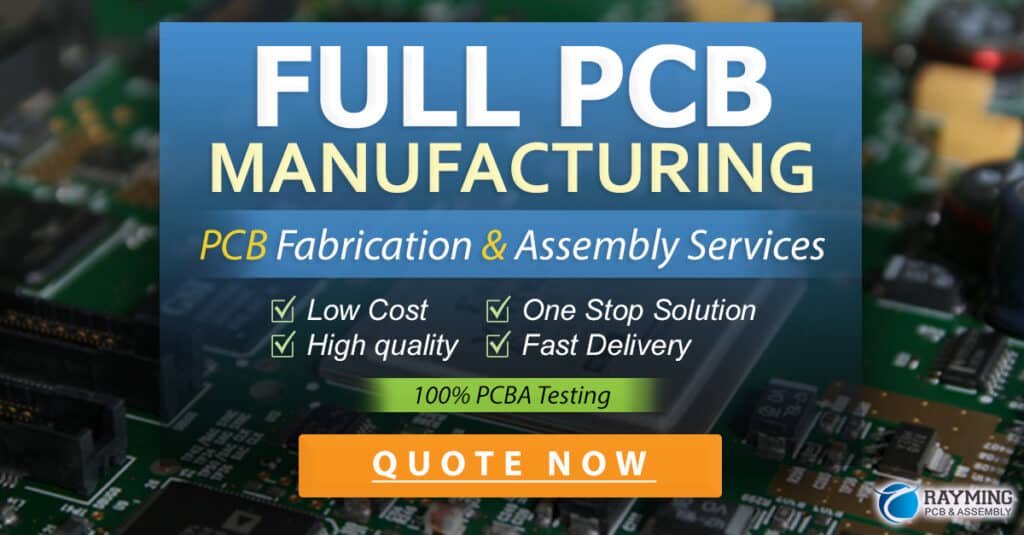
Planning Your RF PCB Design
Define Your Application Requirements
Before starting your RF PCB design, clearly define your application requirements, including:
- Operating frequency range
- Signal power levels
- Bandwidth
- Noise and interference tolerance
- Size and form factor constraints
Choose the Right PCB Material
The choice of PCB material is crucial in RF design. The material’s dielectric constant (Dk) and dissipation factor (Df) significantly impact signal propagation and loss. Common RF PCB materials include:
- FR-4: Suitable for low-cost, low-frequency applications
- Rogers: High-performance material with low Dk and Df, ideal for high-frequency designs
- PTFE (Teflon): Excellent electrical properties but more expensive and challenging to manufacture
Consider the Layer Stack-up
The layer stack-up of your RF PCB plays a vital role in signal integrity and impedance control. A typical RF PCB stack-up may include:
- Signal layers: For routing RF traces and components
- Ground planes: To provide a low-impedance return path and shielding
- Power planes: To distribute power to components
- Dielectric layers: To separate and insulate the conductive layers
RF PCB Layout Techniques
Impedance Matching
Impedance matching is critical in RF PCB design to minimize signal reflections and ensure maximum power transfer. The characteristic impedance of transmission lines should match the impedance of the source and load. Common impedance values in RF design are 50Ω and 75Ω.
To achieve the desired impedance, consider the following factors:
- Trace width and thickness
- Dielectric thickness and permittivity
- Proximity to ground planes
Use impedance calculators or simulation tools to determine the appropriate trace dimensions for your desired impedance.
Ground Planes and Shielding
Proper grounding and shielding are essential in RF PCB design to minimize noise, crosstalk, and electromagnetic interference (EMI). Follow these guidelines:
- Use solid ground planes to provide a low-impedance return path for high-frequency signals
- Avoid splitting ground planes, as it can create impedance discontinuities
- Use via stitching to connect ground planes on different layers
- Implement shielding techniques, such as grounded coplanar waveguides or microstrip with ground planes, to isolate sensitive traces
Component Placement and Routing
Careful component placement and routing are crucial for optimal RF performance. Consider the following best practices:
- Place components close to their associated traces to minimize parasitic inductance and capacitance
- Avoid long trace runs and minimize trace lengths to reduce signal loss and phase delay
- Use a symmetrical layout for differential signals to maintain signal integrity
- Keep sensitive traces away from potential noise sources, such as digital circuits or power supply lines
- Use a straightforward routing strategy, avoiding sharp bends or unnecessary vias
Decoupling and Filtering
Decoupling and filtering techniques help mitigate noise and ensure a clean power supply for RF components. Implement the following:
- Place decoupling capacitors close to the power pins of active components
- Use a combination of bulk and high-frequency decoupling capacitors to cover a wide frequency range
- Implement power supply filtering, such as ferrite beads or pi-filters, to suppress high-frequency noise
- Use LC filters or impedance matching networks to filter unwanted frequencies and improve signal quality
Simulation and Verification
EM Simulation
Electromagnetic (EM) simulation tools, such as Ansys HFSS or CST Studio Suite, allow you to analyze the electromagnetic behavior of your RF PCB design. EM simulation helps you:
- Evaluate the impedance and propagation characteristics of transmission lines
- Identify potential signal integrity issues, such as reflections or crosstalk
- Optimize component placement and routing for better performance
- Verify compliance with electromagnetic compatibility (EMC) standards
Circuit Simulation
Circuit simulation tools, such as Keysight ADS or Cadence Spectre, enable you to simulate the electrical behavior of your RF circuit. Use circuit simulation to:
- Validate the performance of your RF components and circuits
- Analyze the frequency response, gain, and noise characteristics
- Optimize component values and bias conditions
- Verify the overall system-level performance
Manufacturing Considerations
PCB Fabrication Tolerances
RF PCBs require tighter fabrication tolerances compared to standard PCBs. Work closely with your PCB manufacturer and communicate your requirements clearly, including:
- Trace width and spacing tolerances
- Dielectric thickness and permittivity tolerances
- Via hole size and positioning accuracy
- Copper thickness and surface finish specifications
Assembly and Testing
Pay attention to the assembly and testing process of your RF PCB:
- Use high-quality components with tight tolerances to ensure consistent performance
- Follow proper soldering techniques, such as controlled impedance soldering or reflow soldering, to minimize signal degradation
- Perform thorough testing and measurements, including S-parameter measurements, to validate the RF performance of your PCB
Best Practices and Guidelines
Keep it Simple
Strive for simplicity in your RF PCB design. Avoid unnecessary complexity and keep your layout as clean and straightforward as possible. A simple design is easier to analyze, troubleshoot, and manufacture.
Modularize Your Design
Break down your RF system into modular subsystems, such as the RF front-end, baseband processing, and power management sections. Modularization allows for easier design, testing, and integration of individual components.
Use Appropriate Connectors
Choose RF connectors that are suitable for your frequency range and power requirements. Common RF connectors include:
- SMA (Sub-Miniature A): Suitable for frequencies up to 18 GHz
- SMB (Sub-Miniature B): Suitable for frequencies up to 4 GHz
- MMCX (Micro-Miniature Coaxial): Compact connector for frequencies up to 6 GHz
- BNC (Bayonet Neill-Concelman): Rugged connector for frequencies up to 4 GHz
Ensure proper connector mounting and grounding to minimize signal loss and reflections.
Document Your Design
Maintain clear and comprehensive documentation of your RF PCB design, including:
- Schematic diagrams
- Bill of Materials (BOM)
- Layout files
- Assembly drawings
- Test specifications
Proper documentation facilitates collaboration, troubleshooting, and future revisions of your design.
Frequently Asked Questions (FAQ)
1. What is the difference between RF PCB and standard PCB design?
RF PCB design focuses on high-frequency signals and requires careful consideration of impedance matching, signal integrity, and noise reduction. Standard PCB design typically deals with lower-frequency signals and has less stringent requirements for impedance control and shielding.
2. How do I choose the right PCB material for my RF design?
The choice of PCB material depends on your application requirements, such as operating frequency, dielectric constant, and dissipation factor. FR-4 is suitable for low-cost, low-frequency applications, while Rogers and PTFE materials are preferred for high-frequency designs that demand low loss and stable dielectric properties.
3. What is the importance of impedance matching in RF PCB design?
Impedance matching is crucial in RF PCB design to minimize signal reflections and ensure maximum power transfer. Mismatched impedances can lead to signal distortion, reduced efficiency, and increased noise. By matching the impedance of transmission lines to the source and load impedances, you can optimize signal integrity and overall system performance.
4. How can I reduce noise and interference in my RF PCB design?
To reduce noise and interference in your RF PCB design, consider the following techniques:
- Use solid ground planes and proper grounding strategies
- Implement shielding techniques, such as grounded coplanar waveguides or shielded traces
- Place decoupling capacitors close to active components
- Use power supply filtering, such as ferrite beads or pi-filters
- Minimize trace lengths and keep sensitive traces away from noise sources
- Use differential signaling for noise cancellation
5. What are some common mistakes to avoid in RF PCB design?
Some common mistakes to avoid in RF PCB design include:
- Neglecting impedance matching and control
- Splitting ground planes or creating discontinuities in the ground path
- Routing RF traces near noise sources or over split planes
- Using excessively long or meandering traces
- Overlooking decoupling and filtering requirements
- Failing to simulate and verify the design before fabrication
By being aware of these pitfalls and following best practices, you can minimize design errors and improve the overall performance of your RF PCB.
Conclusion
Designing an RF PCB requires a thorough understanding of high-frequency signal behavior, impedance matching, and noise reduction techniques. By following the guidelines and best practices outlined in this article, you can create a robust and reliable RF PCB design that meets your application requirements.
Remember to carefully plan your design, choose the right materials, and pay attention to layout techniques, such as impedance matching, grounding, and shielding. Utilize simulation tools to validate your design and work closely with your PCB manufacturer to ensure proper fabrication and assembly.
With a well-designed RF PCB, you can achieve optimal signal integrity, minimize noise and interference, and ensure the reliable performance of your RF system.